What is PCB Burn-in?
PCB burn-in, also known as board conditioning or heat soaking, is a process that involves subjecting printed circuit boards (PCBs) to elevated temperatures for an extended period. This procedure aims to identify and eliminate early-life failures, ensuring that only reliable and stable PCBs are deployed in the final product.
Burn-in testing is crucial for PCBs destined for use in critical applications, such as aerospace, military, and medical devices, where reliability and longevity are paramount. By exposing the boards to high temperatures, latent defects and weaknesses that may not be apparent during normal operation can be detected and addressed before the PCBs are integrated into the end product.
The Importance of PCB Burn-In
PCB burn-in is an essential step in the manufacturing process for several reasons:
-
Early Failure Detection: Burn-in testing helps identify PCBs that are prone to early failure due to manufacturing defects, component issues, or design flaws. By subjecting the boards to elevated temperatures, these defects can be exposed and the faulty PCBs can be removed from the production line.
-
Improved Reliability: By eliminating early failures, burn-in testing ensures that only reliable and stable PCBs are used in the final product. This leads to improved overall reliability and reduces the likelihood of field failures, which can be costly and damaging to a company’s reputation.
-
Cost Savings: Identifying and addressing PCB issues early in the manufacturing process can result in significant cost savings. It is far more expensive to repair or replace a faulty product after it has been shipped to the customer than it is to detect and resolve issues during production.
-
Compliance with Industry Standards: Many industries, such as aerospace and defense, have strict reliability requirements for electronic components. PCB burn-in testing helps manufacturers meet these standards and ensure that their products are suitable for use in demanding applications.
The PCB Burn-In Process
The PCB burn-in process typically involves the following steps:
-
Preparation: Before the burn-in process begins, the PCBs are visually inspected for any obvious defects or issues. They are then cleaned to remove any contaminants that could affect the testing results.
-
Mounting: The PCBs are mounted on specialized burn-in racks or fixtures that are designed to hold the boards securely during the testing process. These fixtures often include interconnects that allow the boards to be powered and monitored during the burn-in cycle.
-
Temperature Elevation: The PCBs are placed in a burn-in chamber, which is a temperature-controlled environment that can maintain elevated temperatures for extended periods. The temperature is typically set to a level that is higher than the maximum expected operating temperature of the PCB, but not so high as to cause damage to the components.
-
Duration: The burn-in process can last anywhere from a few hours to several days, depending on the specific requirements of the application and the industry standards being followed. During this time, the PCBs are subjected to the elevated temperature continuously.
-
Monitoring: Throughout the burn-in process, the PCBs are monitored for any signs of failure or instability. This can include monitoring electrical parameters, such as voltage and current, as well as visual inspections for any physical damage or changes.
-
Failure Analysis: If a PCB fails during the burn-in process, it is removed from the production line and subjected to further analysis to determine the root cause of the failure. This information is used to improve the design and manufacturing processes to prevent similar issues in the future.
-
Final Inspection: After the burn-in process is complete, the PCBs undergo a final visual inspection and electrical test to ensure that they are functioning properly and meet all required specifications.
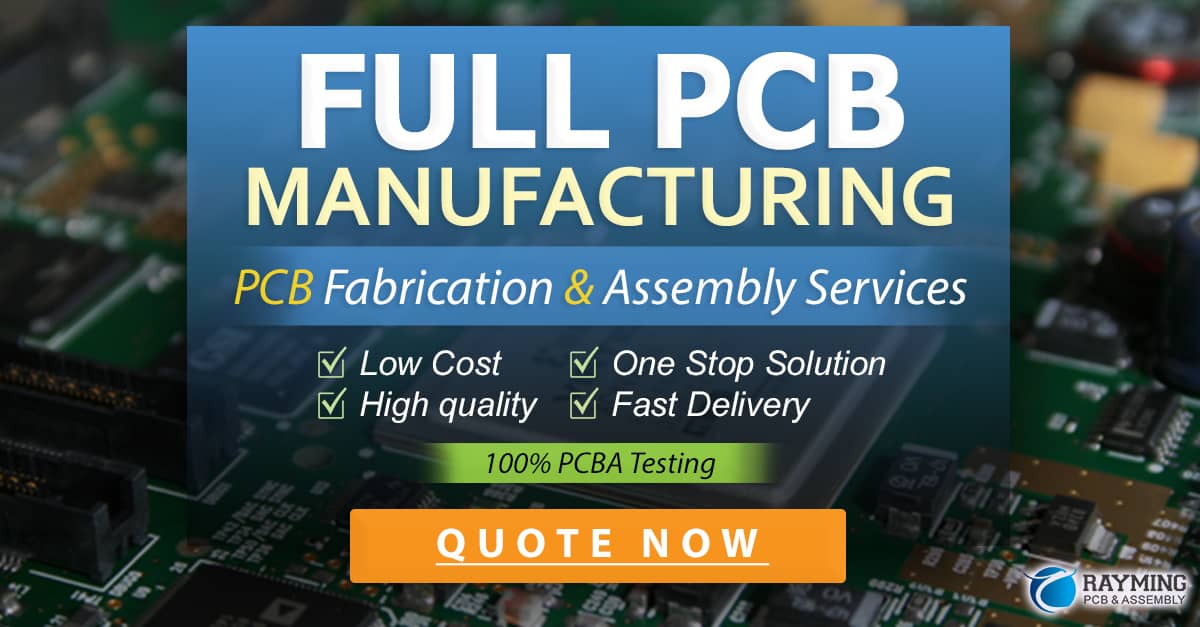
Burn-In PCB Manufacturers and Fabricators
When selecting a PCB manufacturer or fabricator for burn-in testing, it is essential to choose a company with experience and expertise in this specialized process. Some factors to consider include:
-
Experience: Look for a manufacturer with a proven track record of successfully conducting burn-in testing for PCBs in your specific industry or application.
-
Equipment: Ensure that the manufacturer has the necessary burn-in chambers, fixtures, and monitoring equipment to properly conduct the testing process.
-
Standards Compliance: Verify that the manufacturer follows relevant industry standards and guidelines for PCB burn-in testing, such as IPC-9701 or MIL-STD-883.
-
Quality Control: Inquire about the manufacturer’s quality control processes and procedures to ensure that they have a robust system in place for identifying and addressing PCB issues.
-
Turnaround Time: Consider the manufacturer’s lead times for burn-in testing and ensure that they can meet your project’s timeline requirements.
Some notable burn-in PCB manufacturers and fabricators include:
Company | Location | Industries Served |
---|---|---|
Acme PCB Inc. | USA | Aerospace, Defense, Medical |
Elite Electronics Ltd. | UK | Automotive, Industrial, Telecommunications |
PCB Solutions GmbH | Germany | Consumer Electronics, IoT, Renewable Energy |
Advanced Circuits Inc. | Canada | Military, Space, High-Performance Computing |
Sunstone Circuits | USA | Prototyping, Low-Volume Production |
Common PCB Burn-In Testing Standards
There are several industry standards and guidelines that govern PCB burn-in testing, depending on the specific application and industry. Some of the most common standards include:
-
IPC-9701: This standard, developed by the Association Connecting Electronics Industries (IPC), provides guidelines for the qualification and performance testing of printed boards. It includes provisions for burn-in testing and is widely used in the electronics industry.
-
MIL-STD-883: This military standard outlines the test methods and procedures for microelectronics, including PCBs. Method 1015 specifically addresses burn-in testing and is often required for PCBs used in defense applications.
-
JEDEC JESD22-A103: Developed by the Joint Electron Device Engineering Council (JEDEC), this standard provides guidelines for high-temperature storage life testing of semiconductor devices, which can be adapted for PCB burn-in testing.
-
ISO 9001: While not specifically focused on burn-in testing, this quality management system standard requires manufacturers to have processes in place for identifying and addressing product defects, which can include burn-in testing.
Frequently Asked Questions (FAQ)
-
Q: What is the purpose of PCB burn-in testing?
A: The purpose of PCB burn-in testing is to identify and eliminate early-life failures in printed circuit boards by subjecting them to elevated temperatures for an extended period. This process helps ensure that only reliable and stable PCBs are used in the final product. -
Q: How long does a typical PCB burn-in test last?
A: The duration of a PCB burn-in test can vary depending on the specific requirements of the application and the industry standards being followed. It can range from a few hours to several days of continuous exposure to elevated temperatures. -
Q: What temperature is used for PCB burn-in testing?
A: The temperature used for PCB burn-in testing is typically higher than the maximum expected operating temperature of the PCB, but not so high as to cause damage to the components. The exact temperature can vary depending on the specific standard being followed and the PCB’s intended application. -
Q: How do I choose a PCB manufacturer for burn-in testing?
A: When choosing a PCB manufacturer for burn-in testing, consider factors such as their experience in your specific industry, the equipment they use, their compliance with relevant industry standards, their quality control processes, and their ability to meet your project’s timeline requirements. -
Q: Is PCB burn-in testing required for all applications?
A: While PCB burn-in testing is not required for all applications, it is highly recommended for PCBs used in critical applications where reliability and longevity are essential, such as in aerospace, military, and medical devices. Many industry standards and customer requirements may mandate burn-in testing for certain applications.
Conclusion
PCB burn-in testing is a crucial process for ensuring the reliability and longevity of printed circuit boards, particularly those used in critical applications. By subjecting PCBs to elevated temperatures for extended periods, manufacturers can identify and eliminate early-life failures, resulting in improved product quality, cost savings, and compliance with industry standards.
When selecting a burn-in PCB manufacturer or fabricator, it is essential to consider their experience, equipment, standards compliance, quality control processes, and ability to meet project timelines. By partnering with a reputable and experienced manufacturer, you can ensure that your PCBs undergo thorough burn-in testing and are suitable for use in demanding applications.
As technology continues to advance and the demand for reliable electronics grows, the importance of PCB burn-in testing will only increase. By understanding the burn-in process and working with trusted manufacturers, you can ensure that your PCBs meet the highest standards of quality and reliability.
0 Comments