Introduction to Aluminum PCB Heat Dissipation
Aluminum PCBs have gained significant popularity in recent years due to their excellent heat dissipation properties. Unlike traditional FR-4 PCBs, aluminum PCBs utilize an aluminum substrate that effectively transfers heat away from critical components, ensuring optimal performance and reliability. In this article, we will delve into the heat dissipation capabilities of aluminum PCBs and explore the design methods employed to maximize their thermal management potential.
Understanding the Importance of Heat Dissipation
Heat dissipation is a crucial aspect of electronic device design. As electronic components operate, they generate heat, which, if not properly managed, can lead to performance degradation, reduced lifespan, and even device failure. Efficient heat dissipation is particularly important in high-power applications, such as LED lighting, power electronics, and automotive systems, where excessive heat can have severe consequences.
Advantages of Aluminum PCBs for Heat Dissipation
Aluminum PCBs offer several advantages over traditional FR-4 PCBs when it comes to heat dissipation:
-
High Thermal Conductivity: Aluminum has a thermal conductivity of approximately 237 W/mK, which is significantly higher than the thermal conductivity of FR-4 (0.3 W/mK). This means that aluminum PCBs can efficiently transfer heat away from hot spots, preventing localized temperature buildup.
-
Excellent Heat Spreading: The aluminum substrate acts as a heat spreader, distributing heat evenly across the PCB surface. This helps to minimize temperature gradients and reduces the risk of thermal stress on components.
-
Improved Reliability: By effectively dissipating heat, aluminum PCBs enhance the overall reliability of electronic devices. Lower operating temperatures reduce the likelihood of component failure and extend the device’s lifespan.
-
Lightweight and Durable: Aluminum PCBs are lighter than their copper counterparts, making them suitable for weight-sensitive applications. Additionally, aluminum’s inherent strength and durability provide enhanced mechanical stability to the PCB assembly.
Design Methods for Optimizing Heat Dissipation in Aluminum PCBs
To fully leverage the heat dissipation capabilities of aluminum PCBs, careful design considerations must be made. Here are some key design methods and techniques used to optimize heat dissipation in aluminum PCBs:
1. Thermal Vias
Thermal vias are small, plated holes drilled through the PCB to facilitate heat transfer from one layer to another. By strategically placing thermal vias near heat-generating components, designers can create a low-resistance thermal path that allows heat to be efficiently conducted to the aluminum substrate. The number, size, and placement of thermal vias depend on factors such as the component’s power dissipation, the desired thermal resistance, and the available board space.
Component Power Dissipation (W) | Recommended Thermal Via Diameter (mm) | Recommended Number of Thermal Vias |
---|---|---|
0.5 – 1.0 | 0.3 – 0.5 | 4 – 8 |
1.0 – 2.0 | 0.5 – 0.8 | 8 – 16 |
2.0 – 5.0 | 0.8 – 1.0 | 16 – 32 |
2. Thermal Planes
Thermal planes are large copper areas on the PCB that are connected to the aluminum substrate through a high density of thermal vias. These planes serve as heat spreaders, efficiently distributing heat across the PCB surface. Designers often place thermal planes directly beneath high-power components to provide a low-resistance thermal path to the aluminum substrate. The size and shape of thermal planes can be optimized based on the component’s power dissipation and the available board space.
3. Component Placement and Spacing
Proper component placement and spacing are crucial for effective heat dissipation. Heat-generating components should be strategically placed to minimize thermal interaction and ensure adequate airflow. Designers should consider the following guidelines:
- Place high-power components near the edge of the PCB to facilitate heat transfer to the surrounding environment.
- Provide sufficient spacing between components to prevent thermal coupling and allow for adequate airflow.
- Arrange components in a staggered pattern to promote better heat distribution and avoid localized hot spots.
4. Thermal Interface Materials (TIMs)
Thermal interface materials (TIMs) are used to enhance heat transfer between components and the aluminum substrate. TIMs fill the microscopic air gaps between mating surfaces, reducing thermal resistance and improving heat conduction. Common TIMs include thermal greases, thermal pads, and phase change materials. The selection of TIMs depends on factors such as the component’s power dissipation, the required thermal conductivity, and the ease of application.
TIM Type | Thermal Conductivity (W/mK) | Advantages | Disadvantages |
---|---|---|---|
Thermal Grease | 1 – 10 | High thermal conductivity | Messy application, pump-out |
Thermal Pad | 0.5 – 5 | Easy to apply, no mess | Lower thermal conductivity |
Phase Change | 1 – 5 | Conforms to surface irregularities | Limited temperature range |
5. Heatsinks and Cooling Solutions
In high-power applications, additional cooling solutions may be necessary to supplement the heat dissipation provided by the aluminum PCB. Heatsinks are commonly used to increase the surface area for heat dissipation and enhance convective cooling. Designers should consider the following factors when selecting and designing heatsinks:
- Heatsink material: Aluminum and copper are common heatsink materials due to their high thermal conductivity.
- Fin design: The number, size, and shape of fins affect the heatsink’s surface area and heat transfer efficiency.
- Airflow: Adequate airflow is necessary to effectively remove heat from the heatsink. Fans or other active cooling solutions may be required in some cases.
Case Studies and Real-World Applications
To illustrate the effectiveness of aluminum PCBs for heat dissipation, let’s explore a few real-world applications:
1. LED Lighting
Aluminum PCBs are widely used in LED lighting applications due to their excellent thermal management properties. LEDs generate a significant amount of heat, and proper heat dissipation is crucial to maintain their performance and longevity. By using aluminum PCBs with thermal vias, thermal planes, and heatsinks, designers can effectively remove heat from the LEDs, ensuring stable light output and prolonging the lifespan of the lighting system.
2. Power Electronics
Power electronics, such as motor drives, inverters, and power supplies, often deal with high currents and voltages, resulting in substantial heat generation. Aluminum PCBs are well-suited for these applications, as they can efficiently dissipate heat away from power components like MOSFETs, IGBTs, and rectifiers. By employing thermal vias, thermal planes, and appropriate TIMs, designers can maintain safe operating temperatures and prevent thermal runaway in power electronic systems.
3. Automotive Electronics
Automotive electronics operate in harsh environments with wide temperature ranges and vibrations. Aluminum PCBs provide the necessary heat dissipation and mechanical stability to withstand these challenging conditions. In applications like engine control units (ECUs), infotainment systems, and LED headlights, aluminum PCBs ensure reliable performance by effectively managing thermal loads and minimizing thermal stress on components.
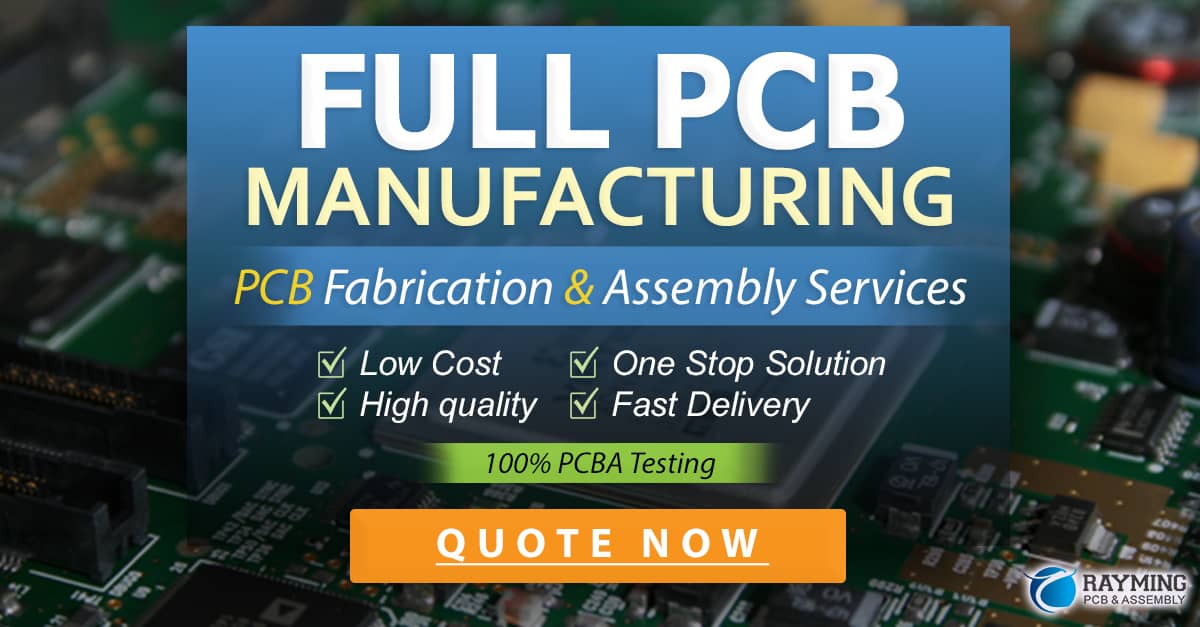
Frequently Asked Questions (FAQ)
-
Q: What are the advantages of using aluminum PCBs for heat dissipation compared to traditional FR-4 PCBs?
A: Aluminum PCBs offer several advantages over FR-4 PCBs for heat dissipation, including high thermal conductivity, excellent heat spreading, improved reliability, and lightweight and durable construction. -
Q: How do thermal vias help in dissipating heat in aluminum PCBs?
A: Thermal vias are small, plated holes drilled through the PCB that create a low-resistance thermal path from heat-generating components to the aluminum substrate. They facilitate efficient heat transfer and help to minimize localized hot spots. -
Q: What factors should be considered when selecting thermal interface materials (TIMs) for aluminum PCBs?
A: When selecting TIMs for aluminum PCBs, designers should consider factors such as the component’s power dissipation, the required thermal conductivity, and the ease of application. Common TIMs include thermal greases, thermal pads, and phase change materials, each with its own advantages and disadvantages. -
Q: How does proper component placement and spacing contribute to effective heat dissipation in aluminum PCBs?
A: Proper component placement and spacing are crucial for effective heat dissipation in aluminum PCBs. Heat-generating components should be placed near the edge of the PCB, with sufficient spacing between components to minimize thermal interaction and allow for adequate airflow. A staggered component arrangement can also promote better heat distribution and avoid localized hot spots. -
Q: In what real-world applications are aluminum PCBs commonly used for their heat dissipation capabilities?
A: Aluminum PCBs are commonly used in various real-world applications that require efficient heat dissipation, such as LED lighting, power electronics, and automotive electronics. These applications often involve high-power components and demanding operating conditions, making aluminum PCBs an ideal choice for thermal management.
Conclusion
Aluminum PCBs have revolutionized the way we approach heat dissipation in electronic devices. With their excellent thermal conductivity, heat spreading capabilities, and mechanical stability, aluminum PCBs offer a reliable solution for managing thermal challenges in a wide range of applications. By employing design techniques such as thermal vias, thermal planes, strategic component placement, and appropriate TIMs, designers can optimize the heat dissipation performance of aluminum PCBs and ensure the long-term reliability of electronic systems.
As technology continues to advance and power densities increase, the importance of effective heat dissipation will only grow. Aluminum PCBs, with their superior thermal management properties, are well-positioned to meet the evolving needs of the electronics industry. By understanding the principles of heat dissipation and applying the appropriate design methods, engineers and designers can harness the full potential of aluminum PCBs to create innovative, reliable, and thermally efficient electronic solutions.
0 Comments