Introduction to PCB Plating
Printed Circuit Board (PCB) plating is an essential process in the manufacturing of electronic devices. It involves the deposition of a thin layer of metal onto the surface of the PCB to improve its electrical conductivity, durability, and solderability. PCB plating is crucial for ensuring the proper functioning and reliability of electronic components and circuits.
Types of PCB Plating
There are several types of PCB plating, each with its own unique characteristics and applications. The most common types of PCB plating include:
- Copper Plating
- Tin Plating
- Nickel Plating
- Gold Plating
- Silver Plating
Plating Type | Characteristics | Applications |
---|---|---|
Copper | High conductivity, low cost | General-purpose PCBs, inner layers |
Tin | Good solderability, corrosion resistance | Surface finish, lead-free soldering |
Nickel | Hardness, wear resistance, diffusion barrier | Underlayer for gold or silver plating |
Gold | Excellent conductivity, corrosion resistance | High-reliability connectors, RF/microwave PCBs |
Silver | High conductivity, low contact resistance | RF/microwave PCBs, switch contacts |
Importance of Hole Plating in PCBs
Hole plating, also known as through-hole plating, is a critical process in PCB manufacturing that involves the deposition of a conductive layer inside the drilled holes of a PCB. This process ensures electrical connectivity between the different layers of the board and allows for the installation of through-hole components.
Benefits of Hole Plating
-
Electrical Connectivity: Hole plating creates a conductive path between the layers of the PCB, allowing signals and power to pass through the board.
-
Mechanical Strength: Plated holes provide additional mechanical support for through-hole components, enhancing the overall durability of the PCB.
-
Solderability: Hole plating improves the solderability of through-hole components, ensuring a strong and reliable solder joint.
-
Thermal Management: Plated holes can help dissipate heat from power-intensive components, improving the thermal performance of the PCB.
PCB Plating Process
The PCB plating process typically involves several steps, including:
-
Cleaning: The PCB surface is cleaned to remove any contaminants or debris that may interfere with the plating process.
-
Activation: The surface is activated to ensure proper adhesion of the plating material.
-
Electroless Plating: A thin layer of metal, usually copper, is deposited onto the PCB surface through an electroless chemical process.
-
Electrolytic Plating: The desired metal (e.g., copper, tin, nickel, or gold) is electroplated onto the PCB surface using an electric current.
-
Inspection: The plated PCB is inspected for quality and adherence to specifications.
Factors Affecting PCB Plating Quality
Several factors can influence the quality of PCB plating, including:
-
Surface Preparation: Proper cleaning and activation of the PCB surface are essential for achieving uniform and adherent plating.
-
Plating Bath Composition: The composition of the plating bath, including the concentration of metal ions, pH, and temperature, must be carefully controlled to ensure optimal plating results.
-
Current Density: The current density used during electrolytic plating can affect the thickness, uniformity, and grain structure of the plated layer.
-
Plating Time: The duration of the plating process determines the thickness of the plated layer and must be carefully monitored to achieve the desired results.
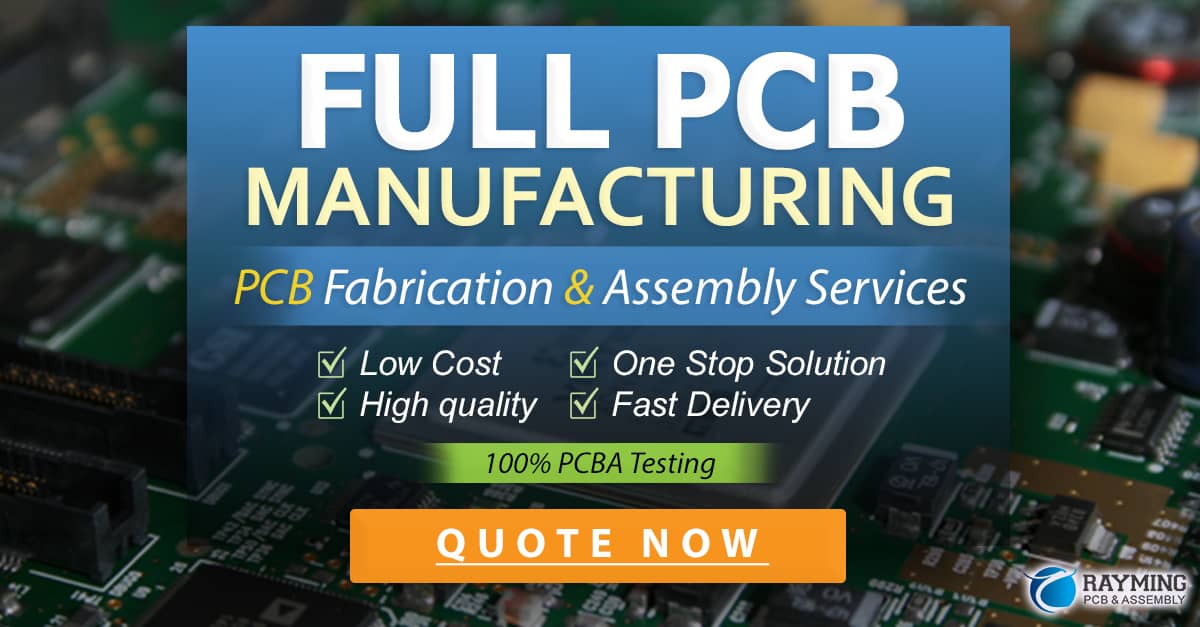
Hole Plating Techniques
There are two primary techniques used for hole plating in PCB manufacturing:
-
Panel Plating: In this method, the entire PCB panel is plated, including the holes and the surface. Panel plating is a simpler and more cost-effective process but may result in uneven plating thickness.
-
Pattern Plating: This technique involves plating only the desired areas of the PCB, including the holes, using a photoresist mask. Pattern plating offers better control over plating thickness and distribution but is more complex and expensive than panel plating.
Challenges in Hole Plating
Hole plating can present several challenges, particularly as PCB designs become more complex and feature smaller hole sizes. Some of these challenges include:
-
Aspect Ratio: High aspect ratio holes (i.e., holes with a large depth-to-diameter ratio) can be difficult to plate uniformly, leading to poor electrical connectivity and reliability.
-
Voids and Nodules: Improper plating conditions can result in the formation of voids or nodules inside the plated holes, which can compromise the electrical and mechanical integrity of the PCB.
-
Thickness Variation: Achieving a consistent plating thickness throughout the hole, particularly at the center, can be challenging due to the “dog-boning” effect, where the plating is thicker at the ends of the hole.
Quality Control and Testing
To ensure the quality and reliability of plated PCBs, manufacturers employ various quality control and testing methods, such as:
-
Cross-Sectional Analysis: A plated PCB is cut and examined under a microscope to assess the plating thickness, uniformity, and adherence to the substrate.
-
Electrical Testing: Continuity and resistance tests are performed to verify the electrical connectivity and integrity of the plated holes and surfaces.
-
Solderability Testing: The solderability of the plated surfaces is evaluated using wetting balance tests or dip-and-look methods.
-
Environmental Testing: Plated PCBs are subjected to various environmental stresses, such as thermal cycling, humidity, and salt spray, to assess their durability and reliability.
Advanced PCB Plating Technologies
As the electronics industry continues to evolve, new PCB plating technologies are being developed to meet the growing demands for higher performance, reliability, and sustainability. Some of these advanced technologies include:
-
Electroless Nickel Immersion Gold (ENIG): ENIG is a surface finish that offers excellent solderability, corrosion resistance, and wire bonding capabilities. It consists of an electroless nickel layer followed by a thin immersion gold layer.
-
Electroless Nickel Electroless Palladium Immersion Gold (ENEPIG): ENEPIG is an advanced surface finish that combines the benefits of ENIG with the added advantages of an electroless palladium layer, which provides improved wear resistance and contact reliability.
-
Immersion Silver: Immersion silver is a cost-effective and eco-friendly alternative to ENIG, offering good solderability and electrical performance.
-
Direct Metallization: Direct metallization is an innovative process that enables the plating of non-conductive surfaces without the need for electroless copper deposition, reducing the environmental impact and process complexity of PCB plating.
Environmental Considerations
PCB plating processes can have a significant environmental impact due to the use of hazardous chemicals and the generation of waste. To mitigate these effects, PCB manufacturers are adopting more eco-friendly practices, such as:
- Implementing closed-loop systems to recycle and reuse plating chemicals.
- Utilizing alternative, less toxic chemistries, such as cyanide-free copper plating baths.
- Investing in waste treatment and disposal facilities to properly handle and dispose of plating wastes.
- Adhering to international environmental standards, such as the Restriction of Hazardous Substances (RoHS) directive and the Registration, Evaluation, Authorization, and Restriction of Chemicals (REACH) regulation.
Future Trends in PCB Plating
As the demand for advanced electronic devices continues to grow, PCB plating technologies are expected to evolve to meet new challenges and requirements. Some of the future trends in PCB plating include:
- Miniaturization: The development of new plating techniques to enable the fabrication of ultra-fine pitch and high-density interconnects.
- 3D Plating: The integration of plating processes with 3D printing technologies to create complex, three-dimensional PCB structures.
- Flexible and Stretchable Electronics: The adaptation of plating methods to accommodate the unique requirements of flexible and stretchable PCBs.
- Sustainable Materials: The exploration of eco-friendly and sustainable plating materials, such as bio-based polymers and recycled metals.
Frequently Asked Questions (FAQ)
-
What is the difference between electroless and electrolytic plating?
Electroless plating is a chemical process that deposits a thin layer of metal onto a surface without the use of an external electric current. In contrast, electrolytic plating uses an electric current to deposit the metal layer, allowing for greater control over the plating thickness and distribution. -
Why is hole plating important in PCB manufacturing?
Hole plating is crucial for establishing electrical connectivity between the different layers of a PCB and providing mechanical support for through-hole components. It ensures the proper functioning and reliability of the electronic device. -
What are the most common metals used in PCB plating?
The most common metals used in PCB plating are copper, tin, nickel, and gold. Each metal has its own unique properties and applications, such as copper for high conductivity, tin for solderability, nickel for hardness and corrosion resistance, and gold for excellent conductivity and corrosion resistance. -
How can I improve the quality of hole plating in my PCBs?
To improve hole plating quality, ensure proper surface preparation, optimize the plating bath composition and operating conditions, use appropriate current density and plating time, and consider advanced plating techniques like pattern plating for better control over plating thickness and distribution. -
What environmental concerns are associated with PCB plating, and how can they be addressed?
PCB plating processes can generate hazardous waste and involve the use of toxic chemicals. To mitigate these environmental concerns, manufacturers can implement closed-loop systems, utilize eco-friendly chemistries, invest in proper waste treatment and disposal, and adhere to international environmental standards like RoHS and REACH.
Conclusion
PCB plating and hole plating are critical processes in the manufacturing of electronic devices, ensuring the proper functioning, reliability, and durability of PCBs. As the electronics industry continues to advance, new plating technologies and environmentally friendly practices are being developed to meet the growing demands for high-performance, sustainable, and cost-effective PCB solutions. By understanding the fundamentals of PCB plating, designers and manufacturers can make informed decisions to optimize their PCB designs and production processes, ultimately leading to better electronic products for consumers.
0 Comments