Introduction to Hole Production
Hole production is a critical aspect of manufacturing processes across various industries, including aerospace, automotive, and medical devices. Two common types of holes encountered in these applications are blind holes and buried holes. Understanding the techniques and challenges associated with producing these holes is essential for engineers and manufacturers to ensure the quality and functionality of their products.
What are Blind Holes?
Blind holes are holes that are drilled, milled, or otherwise machined to a specific depth without penetrating through the entire workpiece. These holes have a bottom surface and are often used for threading, tapping, or accommodating components such as bearings, pins, or fasteners.
What are Buried Holes?
Buried holes, also known as embedded holes, are holes that are completely enclosed within a solid material. These holes are not accessible from the surface of the workpiece and are typically created during the manufacturing process, such as casting, 3D printing, or multi-layer assembly.
Techniques for Producing Blind Holes
Drilling
Drilling is the most common method for creating blind holes. The process involves using a drill bit to remove material and create a cylindrical hole to a desired depth. When drilling blind holes, it is essential to control the depth accurately to ensure the hole does not penetrate through the workpiece.
Types of Drill Bits for Blind Holes
- Standard twist drills
- Spot drills
- Flat bottom drills
- Parabolic drills
Factors Affecting Drilling Performance
- Spindle speed
- Feed rate
- Coolant application
- Drill bit geometry
- Workpiece material properties
Milling
Milling is another technique used for producing blind holes, particularly when the hole requires a non-circular cross-section or a flat bottom. End mills, slot drills, and face mills can be used to create blind holes with various geometries.
Types of Milling Cutters for Blind Holes
- End mills
- Slot drills
- Face mills
- Plunge milling cutters
Factors Affecting Milling Performance
- Cutting speed
- Feed rate
- Depth of cut
- Cutter geometry
- Workpiece material properties
Electrical Discharge Machining (EDM)
EDM is a non-traditional machining process that uses electrical discharges to remove material from the workpiece. This technique is particularly useful for creating blind holes in hard, conductive materials or for producing holes with complex geometries.
Types of EDM for Blind Holes
- Sinker EDM
- Wire EDM
- Hole drilling EDM
Factors Affecting EDM Performance
- Electrode material and geometry
- Discharge current and voltage
- Pulse duration and frequency
- Dielectric fluid properties
- Workpiece material properties
Techniques for Producing Buried Holes
Casting
Casting is a manufacturing process that involves pouring molten material into a mold cavity and allowing it to solidify. Buried holes can be created by placing cores or inserts within the mold to form the desired hole geometry.
Types of Casting for Buried Holes
- Sand casting
- Investment casting
- Die casting
- Permanent mold casting
Factors Affecting Casting Performance
- Mold design and material
- Pouring temperature and rate
- Solidification rate
- Casting material properties
- Post-casting machining and finishing
3D Printing
3D printing, also known as additive manufacturing, is a process that builds objects layer by layer using materials such as plastics, metals, or ceramics. Buried holes can be designed into the 3D model and printed directly, eliminating the need for additional machining steps.
Types of 3D Printing for Buried Holes
- Fused Deposition Modeling (FDM)
- Selective Laser Sintering (SLS)
- Stereolithography (SLA)
- Direct Metal Laser Sintering (DMLS)
Factors Affecting 3D Printing Performance
- Print resolution and layer thickness
- Material properties and compatibility
- Support structure design
- Post-processing and finishing
- Dimensional accuracy and repeatability
Multi-Layer Assembly
Multi-layer assembly involves stacking and bonding multiple layers of material to create a single, unified structure. Buried holes can be formed by designing the holes into the individual layers before assembly.
Types of Multi-Layer Assembly for Buried Holes
- Laminated Object Manufacturing (LOM)
- Sheet metal stacking
- Polymer film stacking
- Ceramic tape stacking
Factors Affecting Multi-Layer Assembly Performance
- Layer alignment and registration
- Bonding method and strength
- Material compatibility and properties
- Post-assembly machining and finishing
- Dimensional accuracy and repeatability
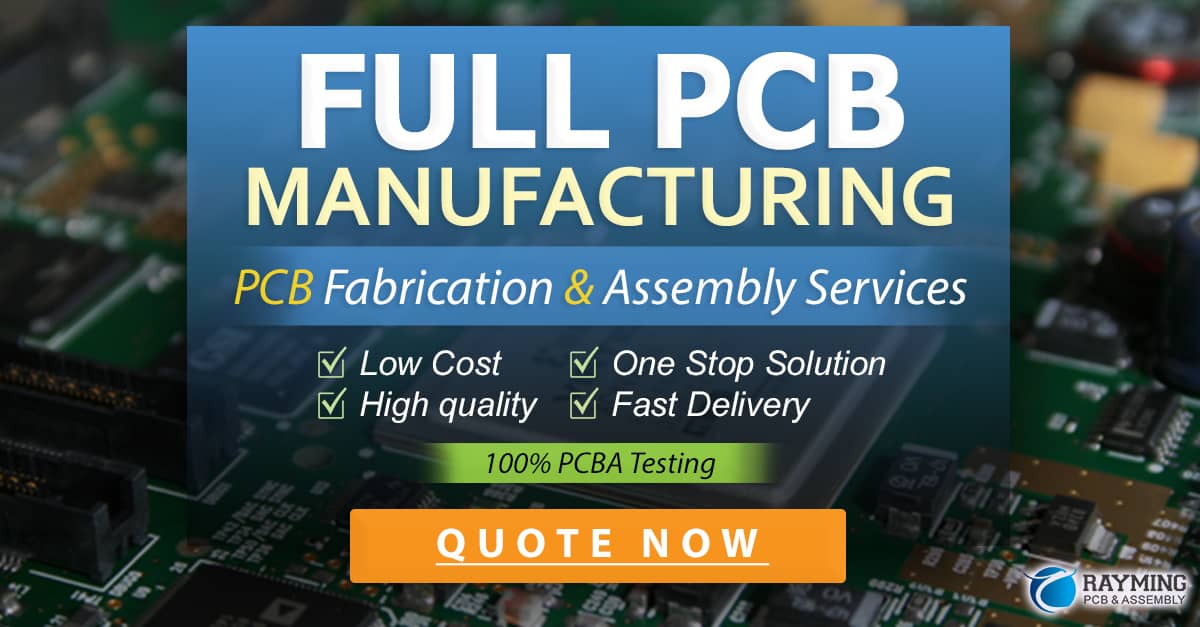
Challenges in Blind Hole and Buried Hole Production
Depth Control
Controlling the depth of blind holes is critical to ensure the hole does not penetrate through the workpiece. Techniques such as depth stops, precision feed control, and in-process monitoring can help maintain accurate depth control.
Chip Evacuation
Removing chips and debris from blind holes can be challenging, as the chips tend to accumulate at the bottom of the hole. Proper coolant application, peck drilling cycles, and specialized drill bit geometries can aid in chip evacuation.
Surface Finish
Achieving a smooth surface finish in blind holes can be difficult, particularly at the bottom of the hole where tool access is limited. Specialized cutting tools, optimized machining parameters, and post-process finishing techniques can help improve surface finish.
Dimensional Accuracy
Maintaining dimensional accuracy in blind and buried holes is essential for proper fit and function of mating components. Factors such as tool deflection, thermal expansion, and material inconsistencies can affect dimensional accuracy. In-process monitoring, tool compensation, and post-process measurement can help ensure dimensional accuracy.
Inspection and Quality Control
Inspecting blind and buried holes can be challenging due to limited accessibility. Non-destructive testing methods such as borescopes, ultrasonic testing, and X-ray computed tomography (CT) can be used to assess hole quality and detect defects.
Table: Comparison of Blind Hole Production Techniques
Technique | Advantages | Disadvantages | Typical Applications |
---|---|---|---|
Drilling | – Versatile – Cost-effective – High production rates |
– Limited to circular cross-sections – Depth control challenges – Chip evacuation issues |
– Threaded holes – Bearing bores – Fastener holes |
Milling | – Non-circular cross-sections – Flat bottom holes – Good surface finish |
– Slower than drilling – Tool deflection – Chip evacuation issues |
– Keyways – Pockets – Complex hole geometries |
EDM | – Hard, conductive materials – Complex geometries – No tool wear |
– Slow process – High energy consumption – Limited to conductive materials |
– Mold and die making – Aerospace components – Medical devices |
Table: Comparison of Buried Hole Production Techniques
Technique | Advantages | Disadvantages | Typical Applications |
---|---|---|---|
Casting | – Complex geometries – Mass production – Wide range of materials |
– Porosity and inclusions – Dimensional variations – Post-casting machining |
– Engine blocks – Pump housings – Valve bodies |
3D Printing | – Complex geometries – Rapid prototyping – No tooling required |
– Limited materials – Anisotropic properties – Post-processing required |
– Aerospace components – Medical implants – Customized products |
Multi-Layer Assembly | – Large, complex structures – Combination of materials – Embedded features |
– Layer alignment – Bonding strength – Post-assembly machining |
– Electronic packaging – Microfluidic devices – Composite structures |
Frequently Asked Questions (FAQ)
- What is the difference between a blind hole and a through hole?
-
A blind hole is a hole that is drilled to a specific depth without penetrating through the entire workpiece, while a through hole is a hole that extends completely through the workpiece.
-
How can I ensure accurate depth control when drilling blind holes?
-
Accurate depth control can be achieved by using depth stops, precision feed control, and in-process monitoring techniques such as laser sensors or touch probes.
-
What are some common challenges in producing blind holes?
-
Common challenges in blind hole production include depth control, chip evacuation, surface finish, and dimensional accuracy. Proper tool selection, machining parameters, and in-process monitoring can help mitigate these challenges.
-
Can 3D printing be used to create buried holes?
-
Yes, 3D printing can be used to create buried holes by designing the holes into the 3D model before printing. The holes are formed during the layer-by-layer building process, eliminating the need for additional machining steps.
-
How can I inspect the quality of blind and buried holes?
- Non-destructive testing methods such as borescopes, ultrasonic testing, and X-ray computed tomography (CT) can be used to assess the quality of blind and buried holes without damaging the workpiece. These methods can detect defects, measure dimensions, and evaluate surface finish.
Conclusion
Blind holes and buried holes are essential features in various manufacturing applications, and producing them requires specialized techniques and considerations. Drilling, milling, and EDM are common methods for creating blind holes, while casting, 3D printing, and multi-layer assembly are used for producing buried holes.
Each technique presents unique challenges, such as depth control, chip evacuation, surface finish, and dimensional accuracy. Manufacturers must select the appropriate method based on factors such as workpiece material, hole geometry, production volume, and quality requirements.
By understanding the principles, advantages, and limitations of each technique, engineers and manufacturers can optimize their hole production processes to ensure the quality, functionality, and reliability of their products.
0 Comments