Introduction to BGA PCB Assembly
Ball Grid Array (BGA) is a surface-mount packaging used for integrated circuits. BGA packages are used to permanently mount devices such as microprocessors. A BGA can provide more interconnection pins than can be put on a dual in-line or flat package. The whole bottom surface of the device can be used, instead of just the perimeter.
BGA PCB assembly is a complex process that requires specialized equipment and expertise. This article will provide an in-depth look at BGA PCB assembly, including the process, benefits, and challenges. We will also discuss how to choose the right BGA PCB assembly company for your project.
What is BGA PCB?
BGA (Ball Grid Array) is a type of surface-mount packaging used for integrated circuits. The BGA package is used to permanently mount devices such as microprocessors. In a BGA, the integrated circuit is mounted on the top surface of the package substrate, and the bottom surface has an array of solder balls that are used to attach the package to a printed circuit board (PCB).
Feature | Description |
---|---|
Package Type | Surface-mount |
Mounting | Permanently mounted |
Device Types | Microprocessors, ASICs, FPGAs |
Connection Type | Array of solder balls |
Advantages | High density, Small footprint, Good thermal and electrical performance |
Disadvantages | Difficult to inspect and rework, Requires specialized equipment |
BGA packages offer several advantages over other package types, such as dual in-line packages (DIP) and quad flat packages (QFP). The main advantages of BGA packages are:
-
High density: BGA packages can provide more interconnection pins than other package types. This is because the entire bottom surface of the package can be used for connections, instead of just the perimeter.
-
Small footprint: BGA packages have a smaller footprint than other package types with the same number of pins. This is because the solder balls are arranged in an array instead of along the perimeter.
-
Good thermal and electrical performance: BGA packages offer good thermal and electrical performance due to the short distance between the chip and the PCB.
However, BGA packages also have some disadvantages, such as:
-
Difficult to inspect and rework: BGA packages are difficult to inspect and rework due to the small size and high density of the solder balls.
-
Requires specialized equipment: BGA Assembly requires specialized equipment, such as pick-and-place machines, reflow ovens, and X-ray inspection systems.
The BGA PCB Assembly Process
The BGA PCB assembly process involves several steps, including:
-
Solder paste printing: Solder paste is applied to the PCB pads using a stencil printer. The stencil ensures that the correct amount of solder paste is applied to each pad.
-
Component placement: The BGA package is placed on the PCB using a pick-and-place machine. The machine uses vision systems to ensure that the package is placed accurately.
-
Reflow soldering: The PCB is heated in a reflow oven to melt the solder paste and form a permanent connection between the BGA package and the PCB.
-
Inspection: The assembled PCB is inspected using automated optical inspection (AOI) and X-ray inspection to ensure that the solder joints are properly formed and that there are no defects.
Step | Description |
---|---|
Solder Paste Printing | Solder paste applied to PCB pads using stencil printer |
Component Placement | BGA package placed on PCB using pick-and-place machine |
Reflow Soldering | PCB heated in reflow oven to melt solder paste and form permanent connection |
Inspection | Assembled PCB inspected using AOI and X-ray to ensure proper solder joint formation and no defects |
Solder Paste Printing
Solder paste printing is the first step in the BGA PCB assembly process. Solder paste is a mixture of tiny solder balls suspended in flux. The flux helps to clean the metal surfaces and prevent oxidation during the soldering process.
The solder paste is applied to the PCB pads using a stencil printer. The stencil is a thin sheet of metal or plastic with holes cut out in the shape of the PCB pads. The stencil is placed over the PCB, and the solder paste is spread over the top of the stencil using a squeegee. The solder paste is forced through the holes in the stencil and onto the PCB pads.
The thickness of the stencil and the size of the holes determine the amount of solder paste that is applied to each pad. It is important to apply the correct amount of solder paste to ensure a good connection between the BGA package and the PCB.
Component Placement
After the solder paste has been applied to the PCB pads, the BGA package is placed on the PCB using a pick-and-place machine. The pick-and-place machine uses a vacuum nozzle to pick up the BGA package and place it on the PCB.
The pick-and-place machine uses vision systems to ensure that the BGA package is placed accurately on the PCB. The vision systems use cameras to locate the fiducial marks on the PCB and the BGA package. Fiducial marks are small, round marks that are used as reference points for aligning the package to the PCB.
Once the BGA package is aligned with the PCB, the pick-and-place machine places the package onto the solder paste. The package is held in place by the tackiness of the solder paste.
Reflow Soldering
After the BGA package has been placed on the PCB, the PCB is heated in a reflow oven to melt the solder paste and form a permanent connection between the package and the PCB.
The reflow oven heats the PCB to a specific temperature profile that is designed to melt the solder paste and form a good connection without damaging the components. The temperature profile typically includes several stages, such as:
-
Preheat: The PCB is heated to a temperature below the melting point of the solder paste to activate the flux and remove any moisture.
-
Soak: The PCB is held at a constant temperature to allow the components to reach a uniform temperature.
-
Reflow: The PCB is heated to a temperature above the melting point of the solder paste to melt the solder and form a connection between the BGA package and the PCB.
-
Cooling: The PCB is cooled to room temperature to allow the solder to solidify and form a permanent connection.
Stage | Description |
---|---|
Preheat | PCB heated to temperature below solder paste melting point to activate flux and remove moisture |
Soak | PCB held at constant temperature to allow components to reach uniform temperature |
Reflow | PCB heated to temperature above solder paste melting point to melt solder and form connection |
Cooling | PCB cooled to room temperature to allow solder to solidify and form permanent connection |
Inspection
After the BGA PCB has been assembled, it is important to inspect the solder joints to ensure that they are properly formed and that there are no defects. There are two main types of inspection that are used for BGA PCBs:
-
Automated Optical Inspection (AOI): AOI uses cameras and image processing software to inspect the solder joints for defects such as bridging, insufficient solder, and misaligned components.
-
X-Ray Inspection: X-ray inspection uses X-rays to create an image of the solder joints inside the BGA package. This allows the inspection of solder joints that are hidden from view, such as those under the BGA package.
Inspection Type | Description |
---|---|
Automated Optical Inspection (AOI) | Uses cameras and image processing software to inspect solder joints for defects |
X-Ray Inspection | Uses X-rays to create image of solder joints inside BGA package to inspect hidden joints |
If any defects are found during the inspection process, the PCB may need to be reworked or scrapped. Rework involves removing the defective component and replacing it with a new one. Scrapping involves discarding the entire PCB and starting over.
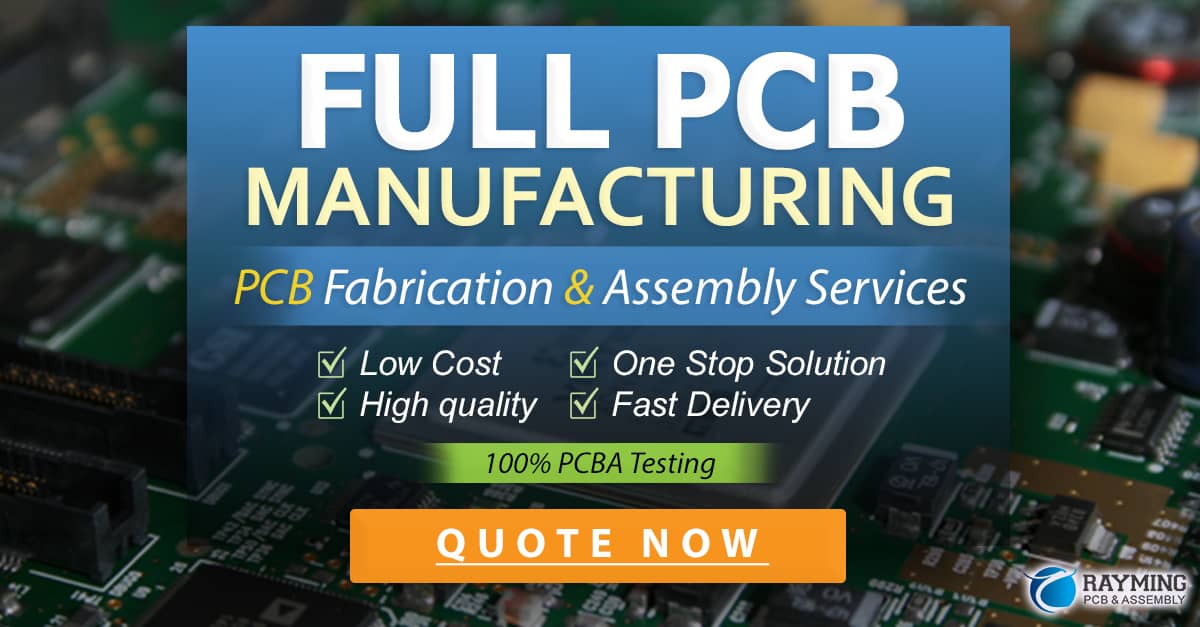
Benefits of BGA PCB Assembly
BGA PCB assembly offers several benefits over other types of PCB assembly, such as through-hole and surface-mount assembly. Some of the main benefits of BGA PCB assembly include:
-
High density: BGA packages can provide more interconnection pins than other package types, allowing for higher density PCBs.
-
Small footprint: BGA packages have a smaller footprint than other package types with the same number of pins, allowing for smaller PCBs.
-
Good thermal and electrical performance: BGA packages offer good thermal and electrical performance due to the short distance between the chip and the PCB.
-
Reliability: BGA packages provide a more reliable connection than other package types due to the larger number of solder balls and the shorter distance between the chip and the PCB.
-
Cost-effective: BGA PCB assembly can be more cost-effective than other types of PCB assembly for high-volume production runs.
Benefit | Description |
---|---|
High Density | BGA packages provide more interconnection pins than other package types |
Small Footprint | BGA packages have smaller footprint than other package types with same number of pins |
Good Thermal and Electrical Performance | Short distance between chip and PCB offers good thermal and electrical performance |
Reliability | Larger number of solder balls and shorter distance between chip and PCB provides more reliable connection |
Cost-Effective | Can be more cost-effective than other PCB assembly types for high-volume production runs |
Challenges of BGA PCB Assembly
While BGA PCB assembly offers many benefits, it also presents some challenges that must be overcome to ensure a successful assembly process. Some of the main challenges of BGA PCB assembly include:
-
Thermal management: BGA packages generate a lot of heat, which must be dissipated to prevent damage to the components. This requires careful thermal management, including the use of heatsinks and fans.
-
Inspection and rework: BGA packages are difficult to inspect and rework due to the small size and high density of the solder balls. This requires specialized equipment and expertise.
-
Warpage: BGA packages can warp during the reflow process due to the high temperatures and the different thermal expansion coefficients of the materials used. This can cause open or short circuits and other defects.
-
Solder joint reliability: The reliability of the solder joints is critical to the performance and longevity of the BGA PCB. Factors such as solder paste quality, reflow profile, and PCB design can affect the reliability of the solder joints.
Challenge | Description |
---|---|
Thermal Management | BGA packages generate a lot of heat that must be dissipated to prevent damage |
Inspection and Rework | Small size and high density of solder balls makes inspection and rework difficult |
Warpage | High temperatures and different thermal expansion coefficients can cause warpage |
Solder Joint Reliability | Factors such as solder paste quality, reflow profile, and PCB design can affect reliability |
To overcome these challenges, it is important to work with an experienced BGA PCB assembly company that has the expertise and equipment necessary to ensure a successful assembly process.
Choosing a BGA PCB Assembly Company
When choosing a BGA PCB assembly company, there are several factors to consider to ensure that you get the best possible service and quality. Some of the main factors to consider include:
-
Experience: Look for a company that has extensive experience in BGA PCB assembly and a track record of successful projects.
-
Equipment: Make sure that the company has the specialized equipment necessary for BGA PCB assembly, such as pick-and-place machines, reflow ovens, and X-ray inspection systems.
-
Quality control: Check that the company has a robust quality control process in place to ensure that the assembled PCBs meet your specifications and are free of defects.
-
Communication: Choose a company that communicates clearly and promptly and is responsive to your needs and concerns.
-
Cost: While cost is always a factor, it should not be the only consideration. Look for a company that offers a good balance of quality and value.
Factor | Description |
---|---|
Experience | Look for company with extensive experience and track record of successful projects |
Equipment | Ensure company has specialized equipment necessary for BGA PCB assembly |
Quality Control | Check that company has robust quality control process to ensure PCBs meet specifications |
Communication | Choose company that communicates clearly and promptly and is responsive to needs |
Cost | Look for company that offers good balance of quality and value |
Frequently Asked Questions (FAQ)
-
What is BGA PCB assembly?
BGA PCB assembly is the process of attaching a Ball Grid Array (BGA) package to a printed circuit board (PCB) using solder balls. -
What are the advantages of BGA PCB assembly?
The advantages of BGA PCB assembly include high density, small footprint, good thermal and electrical performance, reliability, and cost-effectiveness for high-volume production runs. -
What are the challenges of BGA PCB assembly?
The challenges of BGA PCB assembly include thermal management, inspection and rework, warpage, and solder joint reliability. -
What equipment is needed for BGA PCB assembly?
The equipment needed for BGA PCB assembly includes pick-and-place machines, reflow ovens, and X-ray inspection systems. -
How do I choose a BGA PCB assembly company?
When choosing a BGA PCB assembly company, consider factors such as experience, equipment, quality control, communication, and cost.
Conclusion
BGA PCB assembly is a complex process that requires specialized equipment and expertise. By understanding the process, benefits, and challenges of BGA PCB assembly, you can make informed decisions about your PCB assembly needs.
When choosing a BGA PCB assembly company, it is important to consider factors such as experience, equipment, quality control, communication, and cost. By working with an experienced and reputable company, you can ensure that your BGA PCBs are assembled to the highest standards of quality and reliability.
0 Comments