What is BGA Assembly?
Ball Grid Array (BGA) assembly is a high-density packaging technology used in the manufacturing of electronic devices. BGA assemblies consist of a substrate with a grid of solder balls on the bottom surface, which are used to connect the package to a printed circuit board (PCB). This packaging method allows for a high number of interconnections in a small area, making it ideal for complex, high-performance electronic devices.
Advantages of BGA Assembly
- Space-saving: BGA packages have a smaller footprint compared to other packaging technologies, allowing for more compact and efficient PCB designs.
- High interconnection density: The grid of solder balls enables a high number of interconnections between the package and the PCB, facilitating the design of complex, high-performance devices.
- Improved thermal performance: BGA packages have better thermal dissipation properties compared to other packaging methods, as the solder balls provide a direct thermal path from the package to the PCB.
- Enhanced electrical performance: The shorter interconnections in BGA packages result in reduced signal delay and improved signal integrity, making them suitable for high-speed applications.
Challenges in BGA Assembly
Despite the numerous benefits of BGA assembly, there are some challenges associated with this technology:
- Inspection difficulties: The solder joints in BGA assemblies are hidden beneath the package, making visual inspection challenging. Specialized inspection techniques, such as X-ray inspection, are often required to ensure the quality of the solder joints.
- Rework and repair: Reworking or repairing BGA assemblies can be difficult due to the hidden nature of the solder joints. Specialized equipment and expertise are necessary to perform successful rework and repair operations.
- Thermal stress: The coefficient of thermal expansion (CTE) mismatch between the BGA package and the PCB can lead to thermal stress during temperature cycling, potentially causing solder joint failures.
BGA Assembly Process
The BGA assembly process involves several key steps to ensure the proper attachment of the BGA package to the PCB. These steps include:
1. PCB Preparation
Before the BGA package can be attached, the PCB must be properly prepared. This involves:
- Cleaning the PCB surface to remove any contaminants
- Applying solder paste to the BGA landing pads using a stencil or solder paste printer
- Inspecting the solder paste deposit to ensure proper volume and placement
2. BGA Package Placement
Once the PCB is prepared, the BGA package is placed onto the PCB using a pick-and-place machine. The machine precisely aligns the package with the landing pads on the PCB, ensuring accurate placement.
3. Reflow Soldering
After the BGA package is placed, the assembly undergoes reflow soldering. This process involves:
- Preheating the assembly to activate the flux in the solder paste and remove any moisture
- Ramping up the temperature to melt the solder balls and form a strong bond between the package and the PCB
- Cooling the assembly to allow the solder joints to solidify
4. Inspection and Testing
After the reflow soldering process, the BGA assembly undergoes inspection and testing to ensure the quality and reliability of the solder joints. Common inspection and testing methods include:
- Visual inspection using microscopes or cameras
- X-ray inspection to examine the hidden solder joints
- Electrical testing to verify the functionality and performance of the assembly
BGA Rework and Repair
Despite the challenges associated with reworking and repairing BGA assemblies, there are established procedures and specialized equipment available to address these issues.
BGA Rework Process
The BGA rework process typically involves the following steps:
- Removing the defective BGA package using a hot air rework station or infrared heating system
- Cleaning the PCB landing pads to remove any residual solder or contaminants
- Applying new solder paste or flux to the landing pads
- Placing a new BGA package onto the PCB using a pick-and-place machine or manual placement
- Reflowing the assembly to form new solder joints
- Inspecting and testing the reworked assembly to ensure proper functionality
BGA Repair Techniques
In some cases, minor defects in BGA solder joints can be repaired without completely removing the package. Some common BGA repair techniques include:
- Solder ball replacement: Replacing individual damaged or missing solder balls using a solder ball placement tool
- Solder joint reflow: Reflowing specific solder joints using a focused heat source, such as a soldering iron or hot air pencil
- Epoxy underfill repair: Applying epoxy underfill material to reinforce and stabilize damaged solder joints
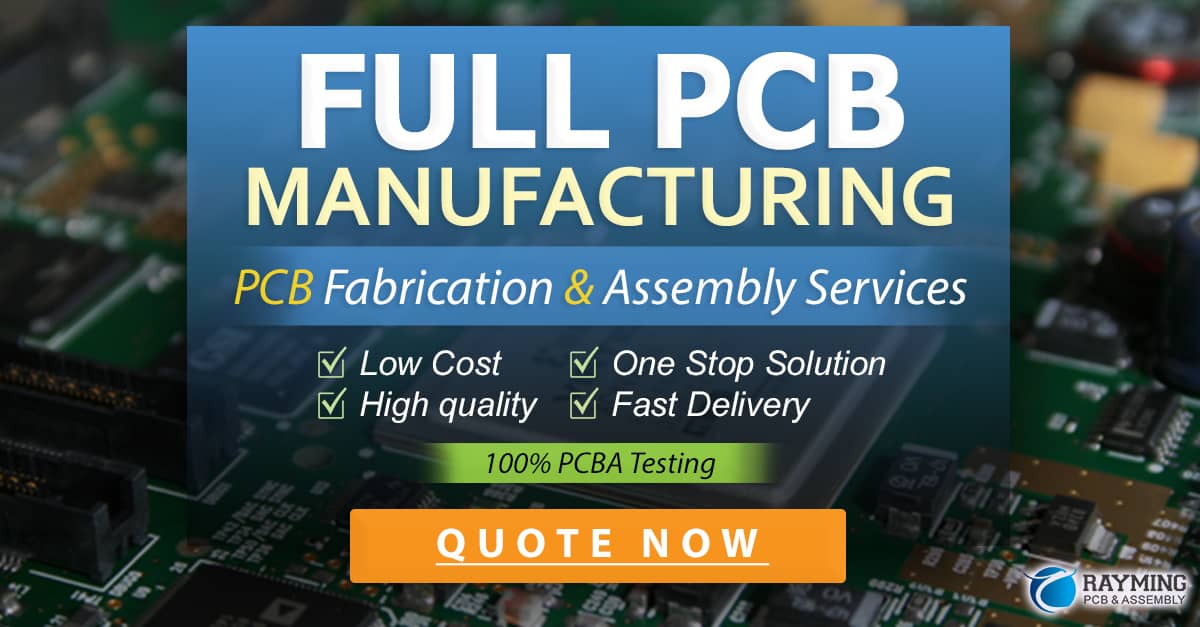
Advanced BGA Assembly Techniques
As electronic devices continue to become more complex and miniaturized, advanced BGA assembly techniques have been developed to meet these challenges.
3D Packaging
3D packaging involves stacking multiple BGA packages vertically to create a high-density, 3D structure. This technique enables the integration of more functionality into a smaller space, improving device performance and reducing overall package size.
Package-on-Package (PoP)
Package-on-Package (PoP) is a 3D packaging technique where one BGA package is stacked on top of another. This method is commonly used in mobile devices, where memory packages are stacked on top of processor packages to save space and improve performance.
Embedded Die Packaging
Embedded die packaging involves placing bare semiconductor dies directly into the PCB substrate, eliminating the need for a separate package. This technique reduces the overall package size and improves electrical performance by shortening the interconnections between the die and the PCB.
Choosing a BGA Assembly Service Provider
When selecting a BGA assembly service provider, it is essential to consider several factors to ensure high-quality results and reliable service.
Experience and Expertise
Look for a service provider with extensive experience in BGA assembly and a proven track record of successfully completing projects similar to yours. The provider should have a deep understanding of BGA assembly processes, challenges, and best practices.
Equipment and Facilities
Ensure that the service provider has state-of-the-art equipment and facilities capable of handling your specific BGA assembly requirements. This includes:
- Advanced pick-and-place machines for accurate package placement
- Reflow soldering ovens with precise temperature control
- Inspection equipment, such as X-ray machines and microscopes
- ESD-protected work areas to prevent damage to sensitive components
Quality Control and Certifications
Choose a service provider that adheres to strict quality control procedures and holds relevant industry certifications, such as ISO 9001, IPC-A-610, and J-STD-001. These certifications demonstrate the provider’s commitment to quality and adherence to industry standards.
Customer Support and Communication
Effective communication and responsive customer support are crucial when working with a BGA assembly service provider. Look for a provider that offers clear and timely communication, responds promptly to your inquiries, and provides regular project updates.
Flexibility and Scalability
Select a service provider that can accommodate your specific needs and scale their services to meet your future requirements. This includes the ability to handle both small and large production volumes, as well as the flexibility to adapt to changes in your project scope or timeline.
Frequently Asked Questions (FAQ)
1. What is the difference between BGA and other packaging technologies?
BGA packages differ from other packaging technologies, such as Quad Flat Packages (QFP) and Dual Inline Packages (DIP), in several ways:
- BGA packages have a higher interconnection density, allowing for more connections in a smaller area
- BGA packages have a smaller footprint, enabling more compact PCB designs
- BGA packages offer better thermal and electrical performance due to the shorter interconnections
2. Can BGA assemblies be reworked or repaired?
Yes, BGA assemblies can be reworked or repaired, although it is more challenging compared to other packaging technologies. Specialized equipment, such as hot air rework stations and X-ray inspection machines, along with skilled technicians, are required to perform successful BGA rework and repair operations.
3. What are the common causes of BGA assembly failures?
Common causes of BGA assembly failures include:
- Improper solder paste application or stencil design
- Inaccurate BGA package placement
- Incorrect reflow soldering profile
- Coefficient of thermal expansion (CTE) mismatch between the package and the PCB
- Mechanical stress or shock during handling or operation
4. How can I ensure the quality of my BGA assemblies?
To ensure the quality of your BGA assemblies, consider the following:
- Work with an experienced and reputable BGA assembly service provider
- Use high-quality materials, such as PCBs, BGA packages, and solder paste
- Implement strict quality control procedures, including inspection and testing
- Follow industry standards and best practices for BGA assembly processes
- Conduct thorough design reviews to identify and address potential issues early in the development process
5. What should I look for when selecting a BGA assembly service provider?
When choosing a BGA assembly service provider, consider the following factors:
- Experience and expertise in BGA assembly
- State-of-the-art equipment and facilities
- Adherence to quality control procedures and industry certifications
- Responsive customer support and clear communication
- Flexibility and scalability to meet your specific needs
Conclusion
BGA assembly is a critical technology in the manufacturing of high-density, high-performance electronic devices. By understanding the advantages, challenges, and processes involved in BGA assembly, designers and manufacturers can make informed decisions and ensure the success of their projects.
When selecting a BGA assembly service provider, it is essential to choose a partner with the experience, expertise, and resources necessary to deliver high-quality results. By working with a reputable provider and following industry best practices, you can overcome the challenges associated with BGA assembly and bring your innovative electronic devices to market efficiently and reliably.
Packaging Technology | Advantages | Challenges |
---|---|---|
BGA | High interconnection density, compact size | Inspection difficulties, rework challenges |
QFP | Lower cost, easier inspection | Lower interconnection density, larger size |
DIP | Simple assembly, easy rework | Large size, limited interconnection density |
In summary, BGA assembly services play a vital role in the production of advanced electronic devices. By partnering with an experienced and capable service provider, designers and manufacturers can leverage the benefits of BGA technology while mitigating the associated challenges, ultimately delivering high-quality, reliable products to their customers.
0 Comments