Introduction to Rigid-Flex PCB Design
Rigid-flex PCB design is a unique combination of rigid and flexible printed circuit boards that offers numerous advantages over traditional PCB designs. This innovative technology allows for the creation of compact, lightweight, and highly reliable electronic devices that can withstand harsh environments and repeated flexing. Rigid-flex PCBs are widely used in various industries, including aerospace, medical, military, and consumer electronics.
In this article, we will discuss the best practices for designing rigid-flex PCBs, covering various aspects such as material selection, layer stackup, design considerations, and manufacturing guidelines. By following these best practices, designers can create robust and reliable rigid-flex PCBs that meet the specific requirements of their applications.
Understanding Rigid-Flex PCB Technology
What is a Rigid-Flex PCB?
A rigid-flex PCB is a hybrid printed circuit board that combines both rigid and flexible substrates. The rigid portions of the board provide structural support and accommodate components, while the flexible sections allow for bending and folding, enabling 3D packaging and improved connectivity between different parts of the device.
Advantages of Rigid-Flex PCBs
Rigid-flex PCBs offer several advantages over traditional PCB designs:
- Reduced size and weight: By eliminating the need for connectors and cables, rigid-flex PCBs enable more compact and lightweight designs.
- Improved reliability: Rigid-flex PCBs minimize the number of interconnects, reducing the risk of failure due to vibration, shock, or thermal stress.
- Enhanced flexibility: The flexible sections of the board allow for bending and folding, enabling 3D packaging and improved connectivity between components.
- Cost-effective: Although the initial cost of rigid-flex PCBs may be higher, they can reduce overall system costs by eliminating connectors and cables and simplifying the assembly process.
Material Selection for Rigid-Flex PCBs
Flexible Substrates
The most common flexible substrates used in rigid-flex PCBs are:
- Polyimide (PI): Known for its excellent thermal stability, chemical resistance, and mechanical properties, PI is the most widely used flexible substrate in rigid-flex PCBs.
- Polyester (PET): PET offers good electrical properties and is more cost-effective than PI, but it has lower temperature resistance and mechanical strength.
Rigid Substrates
The rigid portions of the PCB are typically made of:
- FR-4: A glass-reinforced epoxy laminate, FR-4 is the most common rigid substrate used in PCBs due to its good mechanical and electrical properties and cost-effectiveness.
- High-Tg FR-4: This variant of FR-4 offers improved thermal stability and is suitable for applications with higher operating temperatures.
Adhesives
Adhesives are used to bond the flexible and rigid substrates together. The most common adhesives used in rigid-flex PCBs are:
- Acrylic: Acrylic adhesives offer good bonding strength and flexibility but have lower temperature resistance compared to epoxy adhesives.
- Epoxy: Epoxy adhesives provide excellent thermal stability and chemical resistance, making them suitable for high-reliability applications.
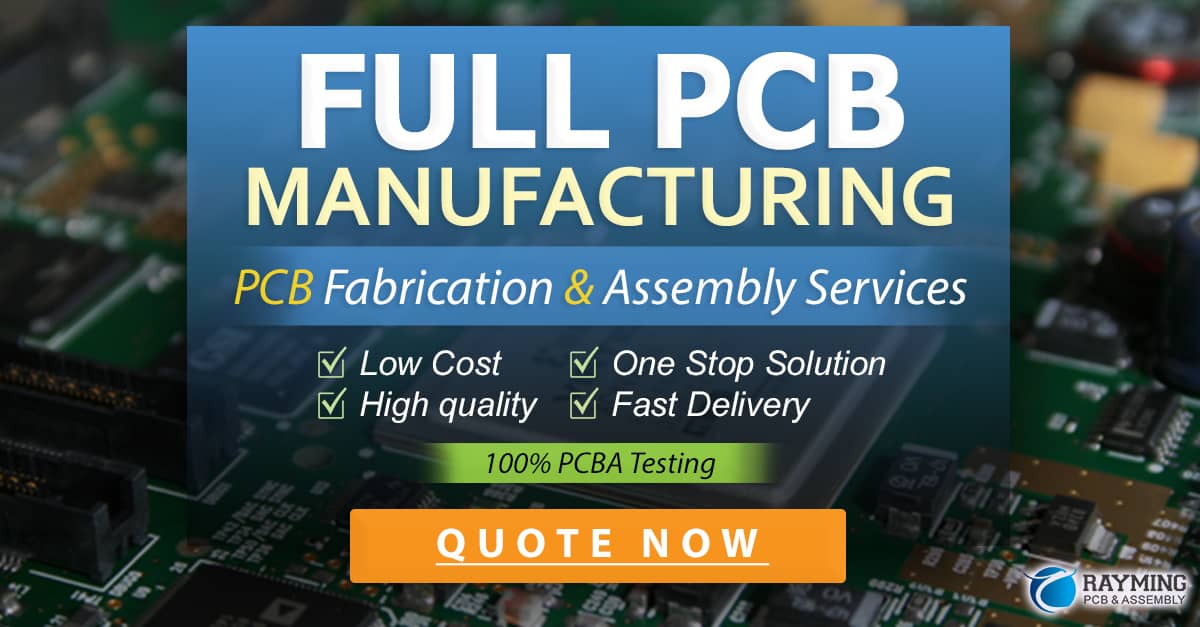
Rigid-Flex PCB Layer Stackup Design
Basic Layer Stackup
A typical rigid-flex PCB layer stackup consists of:
- Rigid layers: The rigid portions of the board, usually made of FR-4 or high-Tg FR-4.
- Flexible layers: The flexible portions of the board, typically made of polyimide or polyester.
- Adhesive layers: Used to bond the rigid and flexible layers together.
- Copper layers: The conductive layers that form the circuit patterns on both rigid and flexible sections.
Symmetrical Stackup
To minimize warpage and ensure the mechanical stability of the rigid-flex PCB, it is essential to design a symmetrical layer stackup. This means that the number and thickness of layers should be balanced on either side of the neutral axis of the board.
Controlled Impedance
When designing high-speed or RF circuits, it is crucial to maintain controlled impedance throughout the rigid-flex PCB. This can be achieved by carefully selecting the dielectric materials, adjusting the trace widths and spacing, and using reference planes to control the impedance of the transmission lines.
Rigid-Flex PCB Design Considerations
Bend Radius
The minimum bend radius is a critical factor in rigid-flex PCB design, as it determines the flexibility and reliability of the board. The bend radius should be at least six times the thickness of the flexible substrate to prevent damage to the copper traces and ensure long-term reliability.
Transition Zones
Transition zones are the areas where the rigid and flexible sections of the board meet. These zones are subject to high stress during bending and require special design considerations:
- Staggered copper layers: The copper layers should be staggered at the transition zones to distribute the stress and prevent cracking.
- Teardrop pads: Using teardrop-shaped pads at the transition zones can help to reinforce the copper traces and improve reliability.
Strain Relief
Incorporating strain relief features in the rigid-flex PCB design can help to minimize stress on the flexible sections and improve the overall reliability of the board. Some common strain relief techniques include:
- Anchoring: Anchoring the flexible sections to the rigid portions of the board using adhesives or mechanical fasteners can help to distribute the stress and prevent damage.
- Stress cut: Adding stress cuts, or small slots, at the transition zones can help to relieve stress and prevent cracking.
Component Placement
When placing components on a rigid-flex PCB, it is important to consider the following:
- Flexible sections: Avoid placing components on the flexible sections of the board, as they can be subjected to stress during bending and may cause reliability issues.
- Rigid sections: Place components on the rigid portions of the board, ensuring that they are properly supported and do not interfere with the bending of the flexible sections.
Manufacturing Guidelines for Rigid-Flex PCBs
Coverlay Application
Coverlay is a protective layer applied over the flexible portions of the board to insulate and protect the copper traces. When applying coverlay, consider the following:
- Adhesion: Ensure proper adhesion between the coverlay and the flexible substrate to prevent delamination and reliability issues.
- Openings: Accurately align the openings in the coverlay with the pads and vias on the flexible substrate to ensure proper connections.
Stiffener Placement
Stiffeners are used to reinforce the rigid portions of the board and provide support for components. When placing stiffeners, consider the following:
- Material selection: Choose a stiffener material that is compatible with the rigid substrate and has a similar coefficient of thermal expansion (CTE) to minimize stress.
- Placement: Ensure that the stiffeners are placed accurately and do not interfere with the bending of the flexible sections.
Panelization
Panelization is the process of arranging multiple rigid-flex PCBs on a single panel for efficient manufacturing. When panelizing rigid-flex PCBs, consider the following:
- Placement: Arrange the boards on the panel in a way that minimizes waste and allows for easy depanelization.
- Tooling holes: Include tooling holes in the panel to ensure accurate registration during the manufacturing process.
Testing and Validation of Rigid-Flex PCBs
Mechanical Testing
Mechanical testing is essential to ensure the reliability and durability of rigid-flex PCBs. Some common mechanical tests include:
- Bend testing: Subjecting the board to repeated bending cycles to verify its flexibility and resistance to fatigue.
- Shock and vibration testing: Exposing the board to simulated shock and vibration conditions to ensure it can withstand the intended operating environment.
Electrical Testing
Electrical testing is necessary to verify the functionality and performance of the rigid-flex PCB. Some common electrical tests include:
- Continuity testing: Verifying that all the connections on the board are intact and there are no open circuits.
- Insulation resistance testing: Measuring the resistance between different conductors on the board to ensure adequate insulation.
- High-voltage testing: Applying a high voltage to the board to detect any potential breakdown or leakage currents.
Frequently Asked Questions (FAQ)
-
Q: What are the main advantages of using rigid-flex PCBs over traditional PCBs?
A: Rigid-flex PCBs offer several advantages, including reduced size and weight, improved reliability, enhanced flexibility, and cost-effectiveness by eliminating the need for connectors and cables. -
Q: What are the most common flexible substrates used in rigid-flex PCBs?
A: The most common flexible substrates used in rigid-flex PCBs are polyimide (PI) and polyester (PET). PI is known for its excellent thermal stability, chemical resistance, and mechanical properties, while PET offers good electrical properties and is more cost-effective. -
Q: Why is it important to design a symmetrical layer stackup for rigid-flex PCBs?
A: Designing a symmetrical layer stackup is crucial to minimize warpage and ensure the mechanical stability of the rigid-flex PCB. By balancing the number and thickness of layers on either side of the neutral axis, the board can maintain its structural integrity during manufacturing and operation. -
Q: What is the minimum bend radius for a rigid-flex PCB, and why is it important?
A: The minimum bend radius for a rigid-flex PCB is typically six times the thickness of the flexible substrate. Adhering to this guideline prevents damage to the copper traces and ensures long-term reliability of the board. -
Q: What are some common mechanical and electrical tests performed on rigid-flex PCBs?
A: Common mechanical tests for rigid-flex PCBs include bend testing, shock and vibration testing, while common electrical tests include continuity testing, insulation resistance testing, and high-voltage testing. These tests help to verify the reliability, durability, and functionality of the board.
Conclusion
Designing rigid-flex PCBs requires careful consideration of various factors, including material selection, layer stackup, design rules, and manufacturing guidelines. By following the best practices outlined in this article, designers can create reliable and high-performance rigid-flex PCBs that meet the specific requirements of their applications.
As the demand for compact, lightweight, and flexible electronic devices continues to grow, rigid-flex PCB technology will play an increasingly important role in enabling innovative product designs across various industries. By staying up-to-date with the latest advancements and best practices in rigid-flex PCB design, engineers and designers can unlock new possibilities and drive the future of electronIC Packaging.
0 Comments