Understanding the Fundamentals of Wave Soldering
Before delving into the best long-term practices for wave soldering, it is crucial to understand the fundamentals of this process. Wave soldering involves the following key steps:
-
PCB Preparation: The PCB is designed, fabricated, and populated with components on the top side, leaving the bottom side exposed for soldering.
-
Flux Application: A thin layer of flux is applied to the bottom side of the PCB to remove oxides, prevent re-oxidation, and enhance solder wettability.
-
Preheating: The PCB is preheated to activate the flux and reduce thermal shock when it comes into contact with the molten solder.
-
Solder Wave Contact: The PCB is brought into contact with the molten solder wave, which is pumped up from a solder pot and flows over a weir, creating a standing wave.
-
Cooling: After passing through the solder wave, the PCB is cooled to allow the solder joints to solidify.
Advantages of Wave Soldering
Wave soldering offers several advantages over other soldering techniques, such as manual soldering or reflow soldering:
- High throughput: Wave soldering can process a large number of PCBs quickly, making it suitable for high-volume production.
- Consistency: The automated nature of wave soldering ensures consistent solder joint quality across multiple PCBs.
- Cost-effectiveness: Wave soldering is generally more cost-effective than other soldering methods, particularly for high-volume production.
Challenges in Wave Soldering
Despite its advantages, wave soldering also presents some challenges that must be addressed to ensure long-term success:
- Thermal shock: Exposing components to the high temperature of the molten solder can cause thermal shock, leading to component damage or failure.
- Bridging: Excessive solder can cause bridging between adjacent pins or pads, resulting in short circuits.
- Insufficient wetting: Poor wetting can occur due to inadequate flux application, incorrect preheating, or contaminated solder, leading to weak or incomplete solder joints.
Best Practices for Long-Term Success in Wave Soldering
To overcome the challenges associated with wave soldering and ensure long-term success in electronic assembly manufacturing, consider implementing the following best practices:
1. PCB Design Optimization
Proper PCB design is crucial for successful wave soldering. Follow these guidelines to optimize your PCB design:
- Avoid using fine-pitch components or leadless packages near the edge of the board, as they are more susceptible to bridging.
- Maintain adequate spacing between components and traces to minimize the risk of bridging.
- Use thermal relief pads for components with large thermal masses to prevent thermal shock.
- Incorporate solderable finishes, such as Hot Air Solder Leveling (HASL) or Electroless Nickel Immersion Gold (ENIG), to enhance solder wettability.
2. Flux Selection and Application
Selecting the appropriate flux and applying it correctly is essential for achieving high-quality solder joints. Consider the following:
- Choose a flux that is compatible with your solder alloy and PCB surface finish.
- Use a flux with the appropriate activity level for your application (e.g., no-clean, water-soluble, or rosin-based).
- Apply a thin, uniform layer of flux to the bottom side of the PCB using a foam, spray, or wave fluxing system.
- Regularly monitor and maintain the flux concentration and application system to ensure consistent performance.
3. Preheat Optimization
Proper preheating is critical for activating the flux, reducing thermal shock, and promoting solder wettability. Optimize your preheating process by:
- Setting the preheat temperature based on the thermal requirements of your components and PCB material.
- Using a multi-stage preheat system to gradually increase the PCB temperature and minimize thermal stress.
- Monitoring the preheat temperature using thermocouples or infrared sensors to ensure consistency.
- Adjusting the conveyor speed and preheat settings to achieve the desired preheat profile.
4. Solder Wave Optimization
The solder wave is the heart of the wave soldering process, and its optimization is crucial for achieving high-quality solder joints. Consider the following:
- Maintain the solder pot temperature within the recommended range for your solder alloy (typically 240-260°C for Sn63/Pb37 and 260-280°C for lead-free alloys).
- Control the solder wave height and flow rate to ensure adequate contact with the PCB without causing turbulence or excessive solder consumption.
- Use a nitrogen atmosphere to minimize solder oxidation and improve solder joint quality.
- Regularly analyze and maintain the solder composition to ensure it remains within specification.
5. Process Monitoring and Control
Implementing process monitoring and control systems is essential for maintaining consistent wave soldering performance and identifying potential issues before they impact product quality. Consider the following:
- Use sensors and data acquisition systems to monitor key process parameters, such as preheat temperature, solder pot temperature, and conveyor speed.
- Establish statistical process control (SPC) charts to track process performance and identify trends or anomalies.
- Implement automated optical inspection (AOI) systems to detect solder defects, such as bridging, insufficient wetting, or cold solder joints.
- Regularly review process data and perform root cause analysis to identify and address any issues.
6. Maintenance and Calibration
Regular maintenance and calibration of wave soldering equipment are essential for ensuring long-term performance and reliability. Develop a comprehensive maintenance and calibration plan that includes:
- Daily, weekly, and monthly cleaning and inspection of the solder pot, wave nozzle, and conveyor system.
- Regular calibration of temperature sensors, flow meters, and other critical instruments.
- Scheduled preventive maintenance to replace worn or damaged components, such as solder pot liners, pump seals, or conveyor belts.
- Documenting all maintenance and calibration activities to ensure traceability and compliance with quality standards.
7. Training and Skill Development
Investing in the training and skill development of your wave soldering operators and technicians is crucial for long-term success. Consider the following:
- Provide comprehensive training on wave soldering fundamentals, best practices, and troubleshooting techniques.
- Encourage cross-functional collaboration between operators, engineers, and quality personnel to foster continuous improvement.
- Develop standard operating procedures (SOPs) and work instructions to ensure consistent performance across all shifts and personnel.
- Regularly assess operator skills and provide ongoing training to address any knowledge gaps or performance issues.
Frequently Asked Questions (FAQ)
1. What is the difference between lead-based and lead-free solder alloys in wave soldering?
Lead-based solder alloys, such as Sn63/Pb37, have been widely used in wave soldering for decades due to their low melting point, excellent wettability, and reliability. However, due to environmental and health concerns, lead-free solder alloys, such as Sn96.5/Ag3.0/Cu0.5 (SAC305), have become increasingly popular. Lead-free alloys have higher melting points and require tighter process control to achieve comparable solder joint quality.
2. How can I prevent bridging in wave soldering?
To prevent bridging in wave soldering, consider the following:
- Optimize PCB design with adequate spacing between components and traces.
- Use a nitrogen atmosphere to reduce solder oxidation and improve wettability.
- Control the solder wave height and flow rate to minimize turbulence and excessive solder deposition.
- Adjust the conveyor speed and preheat settings to achieve the desired solder contact time and thermal profile.
3. What are the most common defects in wave soldering, and how can they be addressed?
The most common defects in wave soldering include:
- Bridging: Addressed through PCB design optimization, nitrogen atmosphere, and solder wave control.
- Insufficient wetting: Addressed through proper flux selection and application, preheat optimization, and solder wave control.
- Cold solder joints: Addressed through preheat optimization, solder pot temperature control, and conveyor speed adjustment.
- Solder balls: Addressed through flux selection, preheat optimization, and solder wave control.
4. How often should I perform maintenance on my wave soldering equipment?
The frequency of maintenance on wave soldering equipment depends on factors such as production volume, solder alloy type, and environmental conditions. As a general guideline:
- Perform daily cleaning and inspection of the solder pot, wave nozzle, and conveyor system.
- Conduct weekly or monthly preventive maintenance, such as replacing solder pot liners or pump seals.
- Calibrate critical instruments, such as temperature sensors and flow meters, according to the manufacturer’s recommendations or at least annually.
5. What are the key considerations when selecting a flux for wave soldering?
When selecting a flux for wave soldering, consider the following:
- Compatibility with your solder alloy and PCB surface finish.
- Activity level (no-clean, water-soluble, or rosin-based) based on your cleaning requirements and environmental regulations.
- Thermal stability and residue characteristics to ensure compatibility with your preheat and cleaning processes.
- Shelf life and storage requirements to maintain flux performance over time.
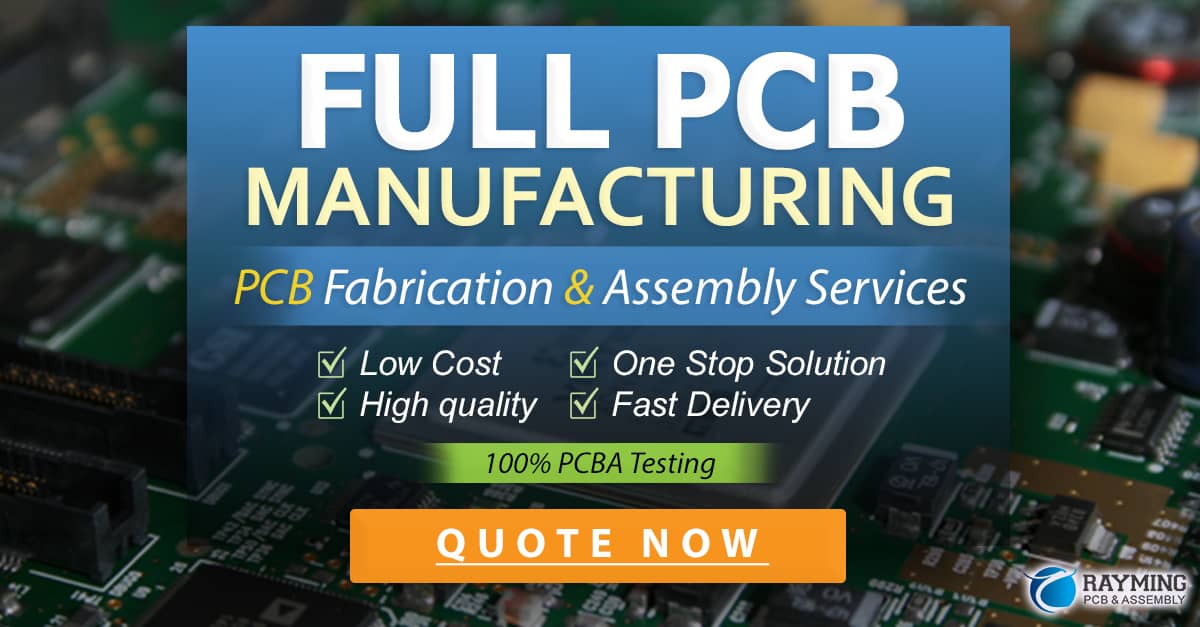
Conclusion
Wave soldering is a critical process in electronic assembly manufacturing that requires careful control and optimization to ensure long-term success. By implementing best practices in PCB design, flux selection and application, preheat optimization, solder wave control, process monitoring, maintenance, and training, you can consistently produce high-quality solder joints and minimize defects.
As the electronics industry continues to evolve, with increasing demands for miniaturization, higher reliability, and environmental sustainability, it is essential to continuously review and adapt your wave soldering processes to meet these challenges. By staying informed about the latest technologies, materials, and best practices, and fostering a culture of continuous improvement, you can ensure the long-term success of your electronic assembly manufacturing operations.
0 Comments