Introduction to PCB Copper Cladding
Printed Circuit Boards (PCBs) are the backbone of modern electronics. They provide a platform for electronic components to be mounted and interconnected, forming a complete circuit. One of the most critical aspects of PCB manufacturing is the copper cladding process. PCB copper cladding refers to the layer of copper foil that is bonded to the surface of the PCB substrate, which is typically made of fiberglass or other insulating materials. The copper cladding serves as the conductive pathway for electrical signals to travel between components on the PCB.
The Importance of PCB Copper Cladding
PCB copper cladding plays a vital role in the performance and reliability of electronic devices. The quality of the copper cladding can significantly impact the signal integrity, power distribution, and heat dissipation of the PCB. Poor copper cladding can lead to signal loss, crosstalk, and other issues that can compromise the functionality of the electronic device.
Factors Affecting PCB Copper Cladding Quality
Several factors can affect the quality of PCB copper cladding, including:
- Copper foil thickness
- Copper foil purity
- Copper foil surface roughness
- Adhesion between the copper foil and the substrate
- Etching process used to create the circuit pattern
Copper Foil Thickness
The thickness of the copper foil used in PCB cladding is typically measured in ounces per square foot (oz/ft²). The most common copper foil thicknesses used in PCB manufacturing are:
Copper Foil Thickness (oz/ft²) | Thickness (μm) |
---|---|
0.5 | 17.5 |
1 | 35 |
2 | 70 |
3 | 105 |
Choosing the Right Copper Foil Thickness
The choice of copper foil thickness depends on the specific requirements of the PCB design. Thinner copper foils are typically used for high-density designs with fine pitch traces, while thicker copper foils are used for power electronics and high-current applications. It is important to choose the right copper foil thickness to ensure optimal performance and reliability of the PCB.
Copper Foil Purity
The purity of the copper foil used in PCB cladding is another critical factor that can affect the quality of the finished product. High-purity copper foils have better electrical conductivity and are less prone to oxidation and other forms of degradation.
Copper Foil Purity Grades
Copper foil purity is typically expressed in grades, with higher grades indicating higher purity. The most common copper foil purity grades used in PCB manufacturing are:
Copper Foil Purity Grade | Purity (%) |
---|---|
Grade 1 | 99.5 |
Grade 2 | 99.8 |
Grade 3 | 99.9 |
The Benefits of High-Purity Copper Foils
Using high-purity copper foils in PCB cladding can provide several benefits, including:
- Better electrical conductivity
- Reduced signal loss and crosstalk
- Improved heat dissipation
- Longer product lifespan
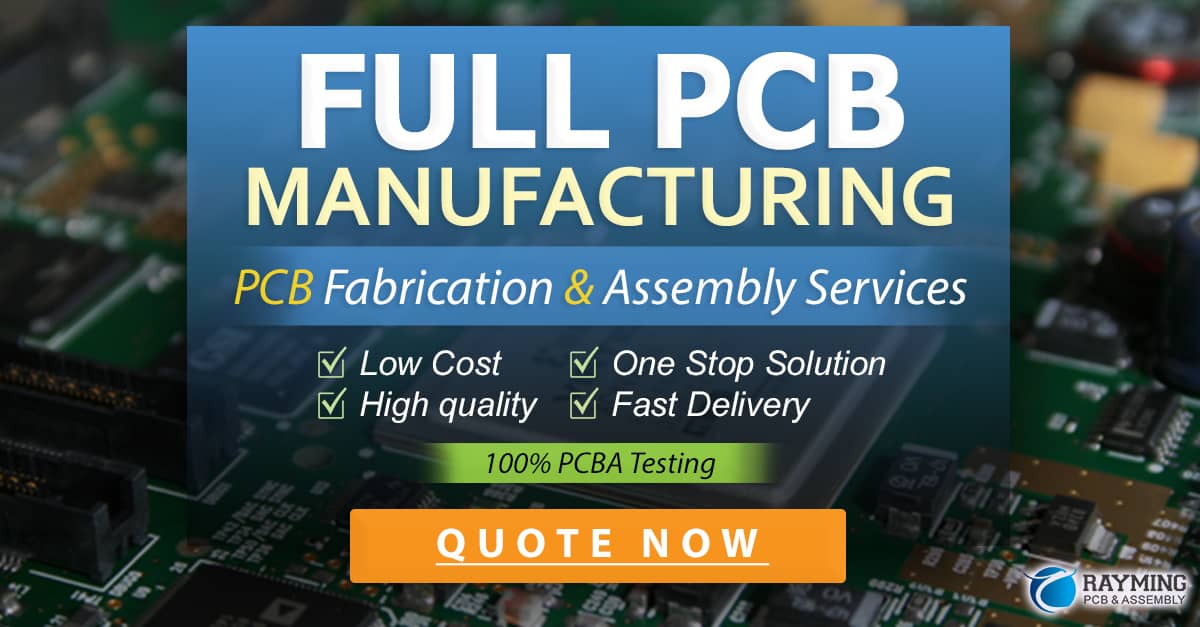
Copper Foil Surface Roughness
The surface roughness of the copper foil used in PCB cladding can also impact the quality of the finished product. Rougher copper foil surfaces provide better adhesion to the substrate, but can also lead to signal loss and other issues.
Copper Foil Surface Roughness Classifications
Copper foil surface roughness is typically classified into three categories:
- Low Profile (LP)
- Standard Profile (SP)
- Very Low Profile (VLP)
The choice of copper foil surface roughness depends on the specific requirements of the PCB design. LP and VLP copper foils are typically used for high-frequency applications, while SP copper foils are used for general-purpose applications.
Adhesion between the Copper Foil and the Substrate
The adhesion between the copper foil and the substrate is another critical factor that can affect the quality of the finished PCB. Poor adhesion can lead to delamination, which can cause signal loss and other issues.
Factors Affecting Copper Foil Adhesion
Several factors can affect the adhesion between the copper foil and the substrate, including:
- Surface roughness of the copper foil
- Surface treatment of the substrate
- Lamination process parameters (temperature, pressure, time)
- Moisture content of the substrate
Improving Copper Foil Adhesion
There are several ways to improve the adhesion between the copper foil and the substrate, including:
- Using copper foils with appropriate surface roughness
- Proper surface treatment of the substrate
- Optimizing the lamination process parameters
- Controlling the moisture content of the substrate
Etching Process Used to Create the Circuit Pattern
The etching process used to create the circuit pattern on the PCB can also impact the quality of the finished product. There are two main types of etching processes used in PCB manufacturing:
- Subtractive etching
- Additive etching
Subtractive Etching
In subtractive etching, the circuit pattern is created by selectively removing the unwanted copper from the PCB surface. This is typically done using a photoresist and chemical etchants.
Additive Etching
In additive etching, the circuit pattern is created by selectively adding copper to the PCB surface. This is typically done using a process called electroplating.
Choosing the Right Etching Process
The choice of etching process depends on the specific requirements of the PCB design. Subtractive etching is typically used for high-volume production, while additive etching is used for high-density designs with fine pitch traces.
FAQ
-
What is PCB copper cladding?
PCB copper cladding refers to the layer of copper foil that is bonded to the surface of the PCB substrate, which serves as the conductive pathway for electrical signals. -
What factors can affect the quality of PCB copper cladding?
Several factors can affect the quality of PCB copper cladding, including copper foil thickness, purity, surface roughness, adhesion to the substrate, and the etching process used to create the circuit pattern. -
What are the most common copper foil thicknesses used in PCB manufacturing?
The most common copper foil thicknesses used in PCB manufacturing are 0.5 oz/ft², 1 oz/ft², 2 oz/ft², and 3 oz/ft². -
What are the benefits of using high-purity copper foils in PCB cladding?
Using high-purity copper foils in PCB cladding can provide several benefits, including better electrical conductivity, reduced signal loss and crosstalk, improved heat dissipation, and longer product lifespan. -
What are the two main types of etching processes used in PCB manufacturing?
The two main types of etching processes used in PCB manufacturing are subtractive etching and additive etching.
Conclusion
PCB copper cladding is a critical aspect of PCB manufacturing that can significantly impact the performance and reliability of electronic devices. Choosing the right copper foil thickness, purity, surface roughness, and etching process can help ensure optimal signal integrity, power distribution, and heat dissipation in the finished PCB. By paying attention to these factors and following best practices in PCB design and manufacturing, engineers and manufacturers can create high-quality PCBs that meet the demands of today’s complex electronic systems.
0 Comments