Introduction to PCB Anti-interference
Printed Circuit Boards (PCBs) are essential components in modern electronic devices. They provide a platform for interconnecting electronic components and enable the efficient functioning of the device. However, PCBs are susceptible to various types of interference, which can affect the performance and reliability of the device. In this article, we will discuss the various anti-interference methods that can be employed in PCB circuits to minimize the impact of interference and ensure optimal performance.
What is PCB Interference?
PCB interference refers to the unwanted signals or noise that can affect the operation of a PCB circuit. This interference can be caused by various factors, such as:
- Electromagnetic Interference (EMI)
- Radio Frequency Interference (RFI)
- Crosstalk
- Power Supply Noise
- Ground Bounce
Interference can lead to various issues, such as signal distortion, data corruption, and even complete system failure. Therefore, it is crucial to employ effective anti-interference methods in PCB circuits to minimize the impact of interference.
Types of PCB Interference
Electromagnetic Interference (EMI)
EMI is a type of interference caused by electromagnetic fields generated by electronic devices. It can be further classified into two types:
- Conducted EMI: This type of EMI is caused by the flow of unwanted currents through the conductors of the PCB.
- Radiated EMI: This type of EMI is caused by the electromagnetic fields generated by the electronic components on the PCB.
EMI can cause various issues, such as signal distortion, data corruption, and even complete system failure.
Radio Frequency Interference (RFI)
RFI is a type of interference caused by radio frequency signals generated by electronic devices. It can be caused by various factors, such as:
- Wireless communication devices
- Mobile phones
- Microwave ovens
- Radar systems
RFI can cause various issues, such as signal distortion, data corruption, and even complete system failure.
Crosstalk
Crosstalk is a type of interference caused by the coupling of signals between adjacent traces on a PCB. It can be further classified into two types:
- Near-end Crosstalk (NEXT): This type of crosstalk occurs when the coupled signal travels in the opposite direction to the original signal.
- Far-end Crosstalk (FEXT): This type of crosstalk occurs when the coupled signal travels in the same direction as the original signal.
Crosstalk can cause various issues, such as signal distortion and data corruption.
Power Supply Noise
Power supply noise is a type of interference caused by fluctuations in the power supply voltage. It can be caused by various factors, such as:
- Switching power supplies
- Motor drives
- Lighting systems
Power supply noise can cause various issues, such as signal distortion and data corruption.
Ground Bounce
Ground bounce is a type of interference caused by the sudden flow of current through the ground plane of a PCB. It can be caused by various factors, such as:
- Simultaneous switching of multiple outputs
- Insufficient ground plane
- Improper decoupling
Ground bounce can cause various issues, such as signal distortion and data corruption.
Anti-interference Methods in PCB Circuit
Proper PCB Layout
One of the most effective ways to minimize PCB interference is to design a proper PCB layout. A well-designed PCB layout can help to reduce the coupling of signals between adjacent traces, minimize the impact of EMI and RFI, and ensure proper grounding. Some of the key considerations for a proper PCB layout include:
- Minimizing the length of high-speed signal traces
- Avoiding sharp bends and corners in signal traces
- Providing adequate spacing between signal traces
- Using ground planes and power planes to provide shielding
- Placing decoupling capacitors close to the power pins of ICs
PCB Layout Consideration | Description |
---|---|
Trace Length | Minimize the length of high-speed signal traces to reduce the impact of EMI and RFI |
Trace Routing | Avoid sharp bends and corners in signal traces to minimize reflections and signal distortion |
Trace Spacing | Provide adequate spacing between signal traces to minimize crosstalk |
Ground and Power Planes | Use ground planes and power planes to provide shielding and minimize EMI and RFI |
Decoupling Capacitors | Place decoupling capacitors close to the power pins of ICs to minimize power supply noise |
Shielding
Shielding is another effective method for minimizing PCB interference. Shielding involves enclosing the PCB or specific components in a conductive material, such as metal or conductive foam, to block electromagnetic fields and minimize the impact of EMI and RFI. Some of the key considerations for effective shielding include:
- Choosing the appropriate shielding material based on the frequency range of the interference
- Ensuring proper grounding of the shield
- Minimizing gaps and openings in the shield
- Using gaskets and conductive adhesives to ensure proper contact between the shield and the PCB
Shielding Material | Frequency Range |
---|---|
Aluminum | 10 kHz – 1 GHz |
Copper | 10 kHz – 10 GHz |
Steel | 10 kHz – 100 MHz |
Conductive Foam | 10 MHz – 10 GHz |
Filtering
Filtering is another effective method for minimizing PCB interference. Filtering involves the use of passive components, such as capacitors and inductors, to attenuate unwanted signals and minimize the impact of EMI and RFI. Some of the key considerations for effective filtering include:
- Choosing the appropriate filter topology based on the frequency range of the interference
- Selecting the appropriate filter components based on the desired attenuation and cutoff frequency
- Placing the filter components close to the source of the interference
- Providing adequate grounding for the filter components
Filter Topology | Frequency Range |
---|---|
Low-pass Filter | DC – Cutoff Frequency |
High-pass Filter | Cutoff Frequency – Infinity |
Band-pass Filter | Lower Cutoff Frequency – Upper Cutoff Frequency |
Band-stop Filter | DC – Lower Cutoff Frequency, Upper Cutoff Frequency – Infinity |
Grounding
Proper grounding is essential for minimizing PCB interference. A well-designed grounding scheme can help to minimize ground bounce, reduce the impact of EMI and RFI, and ensure proper operation of the PCB circuit. Some of the key considerations for effective grounding include:
- Using a solid ground plane to provide a low-impedance return path for signals
- Minimizing the length of ground traces
- Providing adequate grounding for shielding and filtering components
- Using a star grounding scheme for sensitive circuits
- Avoiding ground loops and providing a single-point ground reference
Grounding Scheme | Description |
---|---|
Solid Ground Plane | Provides a low-impedance return path for signals and minimizes ground bounce |
Star Grounding | Provides a single-point ground reference for sensitive circuits and minimizes ground loops |
Hybrid Grounding | Combines the benefits of solid ground plane and star grounding for optimal performance |
Decoupling
Decoupling is another effective method for minimizing PCB interference. Decoupling involves the use of capacitors to provide a local energy storage and minimize the impact of power supply noise. Some of the key considerations for effective decoupling include:
- Placing decoupling capacitors close to the power pins of ICs
- Using a combination of bulk and ceramic capacitors for optimal performance
- Providing adequate grounding for the decoupling capacitors
- Using a power plane to distribute power to the decoupling capacitors
Decoupling Capacitor Type | Description |
---|---|
Bulk Capacitor | Provides a low-frequency energy storage and minimizes power supply noise |
Ceramic Capacitor | Provides a high-frequency energy storage and minimizes power supply noise |
Tantalum Capacitor | Provides a high-capacitance energy storage and minimizes power supply noise |
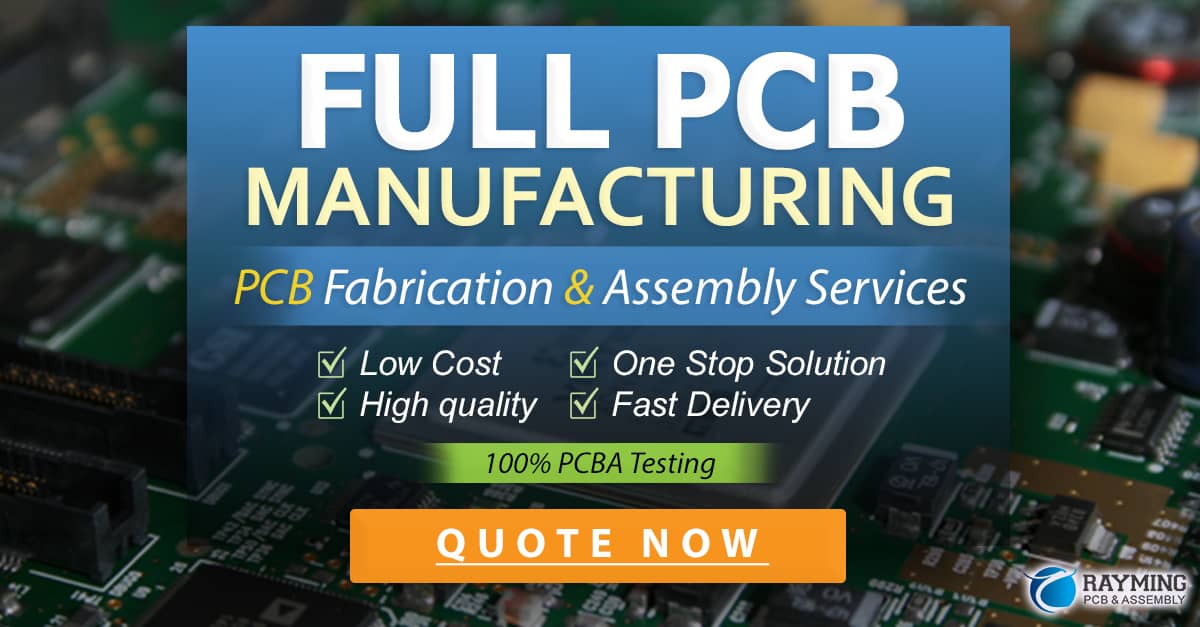
Frequently Asked Questions (FAQ)
What is the difference between EMI and RFI?
EMI and RFI are both types of electromagnetic interference, but they differ in their frequency range. EMI typically refers to interference in the frequency range of 10 kHz to 1 GHz, while RFI refers to interference in the frequency range of 1 GHz and above.
What is the purpose of a ground plane in a PCB?
A ground plane in a PCB serves several purposes, including:
- Providing a low-impedance return path for signals
- Minimizing ground bounce and voltage differences across the PCB
- Providing shielding against EMI and RFI
- Improving the thermal performance of the PCB
What is the difference between a low-pass filter and a high-pass filter?
A low-pass filter attenuates signals above a certain cutoff frequency, while allowing signals below the cutoff frequency to pass through. A high-pass filter, on the other hand, attenuates signals below a certain cutoff frequency, while allowing signals above the cutoff frequency to pass through.
What is the purpose of decoupling capacitors in a PCB?
Decoupling capacitors are used in a PCB to provide a local energy storage and minimize the impact of power supply noise. They are typically placed close to the power pins of ICs and provide a low-impedance path for high-frequency noise to flow back to the power supply.
What is the difference between a solid ground plane and a star grounding scheme?
A solid ground plane provides a low-impedance return path for signals and minimizes ground bounce across the entire PCB. A star grounding scheme, on the other hand, provides a single-point ground reference for sensitive circuits and minimizes ground loops. A hybrid grounding scheme combines the benefits of both solid ground plane and star grounding for optimal performance.
Conclusion
PCB interference is a common problem that can affect the performance and reliability of electronic devices. However, by employing effective anti-interference methods, such as proper PCB layout, shielding, filtering, grounding, and decoupling, the impact of interference can be minimized. By considering the key factors for each anti-interference method and selecting the appropriate techniques based on the specific requirements of the PCB circuit, designers can ensure optimal performance and reliability of their electronic devices.
0 Comments