What is Electrostatic Powder Coating?
Electrostatic powder coating is a popular method used for applying a protective and decorative finish to various metal surfaces. This process involves the use of a dry powder that is electrically charged and sprayed onto the surface of the metal object. The charged powder particles adhere to the grounded metal surface, creating an even coating. The coated object is then placed in an oven, where the powder melts and cures, forming a durable and smooth finish.
The Process of Electrostatic Powder Coating
- Preparation: The metal surface is cleaned, degreased, and pretreated to ensure proper adhesion of the powder coating.
- Powder Application: The powder is loaded into a hopper and then sprayed using an electrostatic gun. The gun applies a high-voltage electrostatic charge to the powder particles, which causes them to be attracted to the grounded metal surface.
- Curing: The coated object is placed in an oven, where it is heated to a specific temperature (usually between 350°F and 400°F) for a certain duration. This process allows the powder to melt, flow, and form a smooth, durable finish.
Types of Powder Coatings
There are two main types of powder coatings used in the electrostatic powder spray process:
-
Thermoplastic Powder Coatings: These coatings do not undergo a chemical change during the curing process. They can be remelted and reshaped after application. Examples include nylon, polyester, and vinyl.
-
Thermoset Powder Coatings: These coatings undergo a chemical change during the curing process, forming a hard, irreversible finish. They offer superior durability and resistance to chemicals, heat, and abrasion. Examples include epoxy, polyester, and polyurethane.
Advantages of Electrostatic Powder Coating
1. Durability and Longevity
One of the most significant advantages of electrostatic powder coating is its exceptional durability. The curing process creates a strong, cross-linked finish that is resistant to chipping, scratching, fading, and peeling. This makes powder-coated surfaces ideal for applications that require a long-lasting, protective finish, such as:
- Outdoor furniture and equipment
- Automotive parts
- Architectural components
- Appliances and machinery
Compared to traditional liquid paints, powder coatings offer superior resistance to the following:
Factor | Powder Coating | Liquid Paint |
---|---|---|
Chemicals | High | Moderate |
UV Exposure | High | Low to Moderate |
Abrasion | High | Moderate |
Impact | High | Moderate |
Corrosion | High | Moderate |
2. Environmental Friendliness
Electrostatic powder coating is an eco-friendly alternative to traditional liquid painting methods. Powder coatings contain no solvents or volatile organic compounds (VOCs), which are harmful to the environment and human health. This means that the process emits minimal pollutants into the atmosphere, making it a more sustainable choice for finishing metal surfaces.
Additionally, powder coating overspray can be collected, recycled, and reused, reducing waste and minimizing the environmental impact of the coating process.
3. Cost-Effectiveness
While the initial investment in equipment for electrostatic powder coating may be higher than traditional liquid painting, the long-term cost benefits are substantial. Some of the factors that contribute to the cost-effectiveness of powder coating include:
- Reduced Material Waste: Powder coating has a higher transfer efficiency (up to 95%) compared to liquid paint (30-50%), meaning less material is wasted during application.
- Faster Application: The electrostatic charge ensures even coverage and minimizes the need for multiple coats, reducing application time.
- Lower Energy Consumption: Powder coating cures at lower temperatures than liquid paint, resulting in lower energy costs.
- Longer Lifespan: The durability of powder-coated surfaces reduces the need for frequent repainting or touch-ups, saving money on maintenance costs.
4. Versatility and Customization
Electrostatic powder coating offers a wide range of colors, textures, and finishes, allowing for extensive customization options. From matte and gloss finishes to metallic and textured effects, powder coatings can be tailored to suit various aesthetic and functional requirements.
Some common finishes and effects include:
- Matte
- Gloss
- Semi-gloss
- Metallic
- Textured
- Wrinkle
- Hammer tone
- Transparent
This versatility makes powder coating suitable for a diverse range of applications, from decorative to industrial.
5. Improved Corrosion Resistance
Powder-coated surfaces offer excellent corrosion resistance, making them ideal for use in harsh environments or outdoor applications. The seamless, even coverage provided by the electrostatic application process minimizes the risk of gaps or thin spots that could be prone to corrosion.
Additionally, powder coatings can be formulated with specific properties to enhance corrosion resistance, such as:
- Epoxy-based coatings for chemical resistance
- Zinc-rich primers for cathodic protection
- UV-resistant additives for outdoor exposure
Disadvantages of Electrostatic Powder Coating
1. Limited Substrate Compatibility
Electrostatic powder coating is primarily suitable for metal surfaces, as the process relies on the electrical conductivity of the substrate. This limits its application to non-conductive materials such as wood, plastic, or glass. However, some advancements have been made in the development of special conductive primers that allow powder coating to be applied to non-conductive surfaces.
2. Higher Initial Investment
Setting up an electrostatic powder coating system requires a significant initial investment in equipment and facilities. The necessary equipment includes:
- Powder coating booth
- Electrostatic spray guns
- Powder recovery system
- Curing oven
- Pretreatment equipment
This higher upfront cost may be a barrier for smaller businesses or those with limited budgets.
3. Difficulty in Achieving Thin Coats
Powder coatings typically produce thicker films compared to liquid paints, with an average thickness ranging from 2 to 6 mils (50 to 150 microns). This can be a disadvantage when a thin, smooth finish is required, such as in the case of intricate or delicate components.
4. Color Matching Challenges
Achieving an exact color match can be more challenging with powder coatings compared to liquid paints. This is due to the limited ability to make on-site adjustments to the powder formulation. Color matching requires careful planning and communication with the powder coating manufacturer to ensure the desired shade is achieved.
5. Touchup and Repair Limitations
Repairing damaged or worn powder-coated surfaces can be more difficult than touching up liquid-painted surfaces. In most cases, the entire component must be stripped and recoated to achieve a uniform finish. This can be time-consuming and costly, especially for large or complex parts.
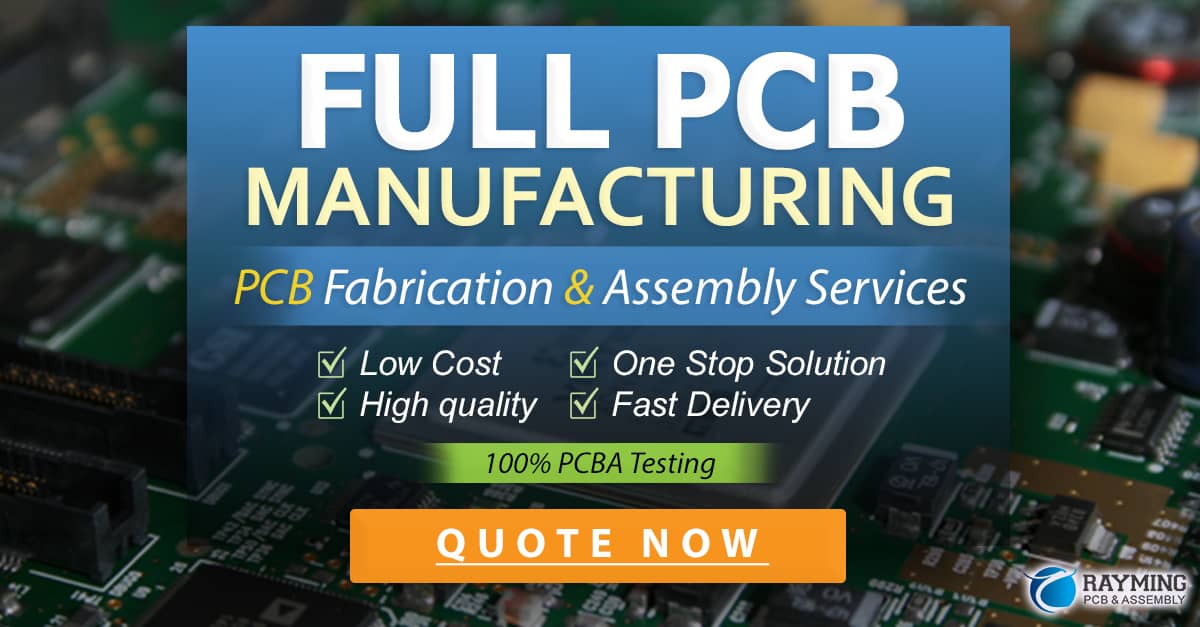
FAQ
- Can powder coating be applied to all metal surfaces?
-
Powder coating can be applied to most metal surfaces, including steel, aluminum, and galvanized metals. However, some metals may require special pretreatment or priming to ensure proper adhesion.
-
How long does powder coating last?
-
The lifespan of a powder-coated surface depends on various factors, such as the quality of the coating, the environment it is exposed to, and the level of maintenance. In general, powder coatings can last up to 20 years or more with proper care.
-
Is powder coating more expensive than liquid painting?
-
The initial cost of powder coating may be higher due to the equipment and setup required. However, in the long run, powder coating can be more cost-effective due to its durability, lower material waste, and reduced maintenance requirements.
-
Can powder coating be removed?
-
Yes, powder coating can be removed using various methods, such as chemical stripping, abrasive blasting, or burn-off ovens. However, the removal process can be time-consuming and may require special equipment and safety precautions.
-
Are there any health risks associated with powder coating?
- Powder coatings are generally considered safe and non-toxic once cured. However, during the application process, proper safety measures should be taken to avoid inhalation of powder particles. Adequate ventilation, personal protective equipment, and proper handling procedures are essential to minimize health risks.
0 Comments