Introduction
In the world of printed circuit board (PCB) manufacturing, the choice between copper defined and soldermask defined pads can significantly impact the overall quality, reliability, and manufacturability of the final product. This article will delve into the advantages and disadvantages of each approach, helping designers and manufacturers make informed decisions based on their specific requirements.
What are Copper Defined and Soldermask Defined Pads?
Before exploring the pros and cons of each approach, it’s essential to understand the fundamental differences between copper defined and soldermask defined pads.
Copper Defined Pads
Copper defined pads, also known as non-solder mask defined (NSMD) pads, are characterized by the copper pad size being smaller than the opening in the soldermask layer. In this configuration, the copper pad’s edges define the solderable area, while the soldermask serves as a protective layer around the pad.
Soldermask Defined Pads
Soldermask defined pads, also referred to as solder mask defined (SMD) pads, feature a soldermask opening that is smaller than the underlying copper pad. The soldermask layer effectively defines the solderable area, while the copper pad extends slightly beyond the soldermask opening.
Advantages of Copper Defined Pads
1. Improved Solder Joint Reliability
One of the primary advantages of copper defined pads is enhanced solder joint reliability. The exposed copper edges of the pad provide a larger surface area for the solder to adhere to, resulting in a stronger mechanical bond between the component and the PCB. This increased bond strength helps to minimize the risk of solder joint failures, particularly in applications subject to vibration, thermal cycling, or mechanical stress.
2. Better Copper Etching Accuracy
Copper defined pads offer better accuracy during the copper etching process. Since the soldermask layer does not define the pad size, any variations or inconsistencies in the soldermask alignment will not affect the final pad dimensions. This improved etching accuracy is particularly beneficial for designs with fine-pitch components or high-density layouts, where precise pad sizes and spacings are critical.
3. Reduced Soldermask Misalignment Issues
With copper defined pads, soldermask misalignment is less likely to cause problems during assembly. Since the soldermask opening is larger than the copper pad, minor misalignments will not impact the solderable area or the solder joint quality. This tolerance to misalignment can lead to higher yields and fewer assembly-related defects, ultimately reducing manufacturing costs.
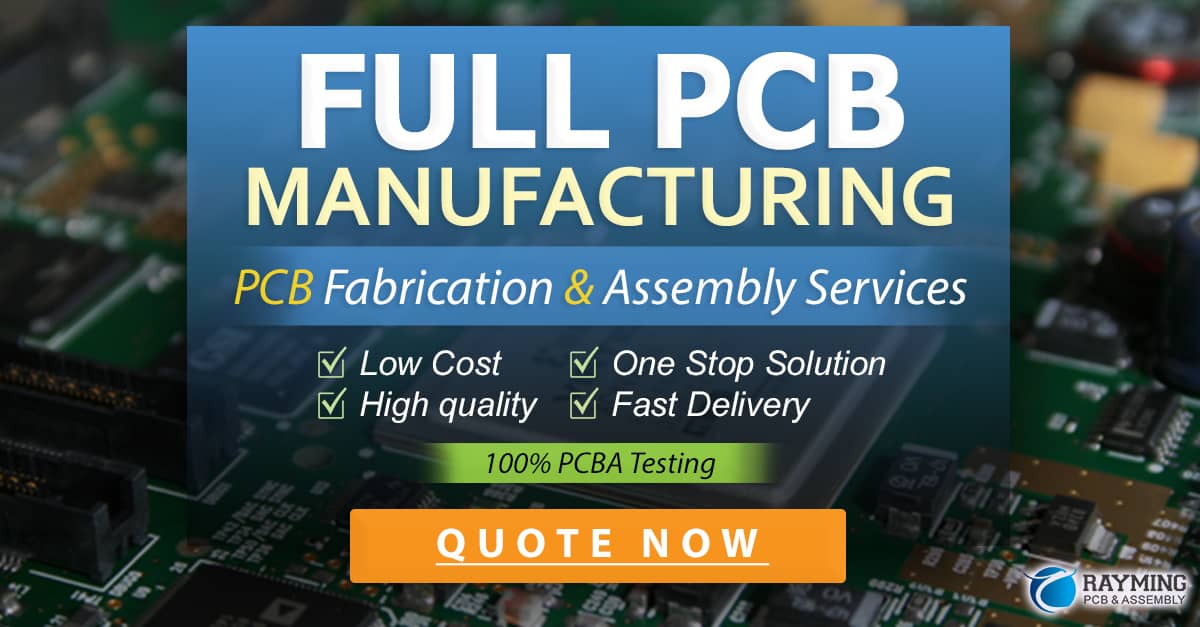
Disadvantages of Copper Defined Pads
1. Increased Risk of Solder Bridging
One potential drawback of copper defined pads is the increased risk of solder bridging, especially in designs with closely spaced pads. The exposed copper between pads can allow solder to flow and create unintended connections, leading to short circuits and other assembly defects. To mitigate this risk, designers must carefully consider pad spacing and solder mask clearances when using copper defined pads.
2. Reduced Soldermask Coverage
Copper defined pads have larger soldermask openings, which can result in reduced soldermask coverage on the PCB surface. This reduced coverage may compromise the board’s overall protection against environmental factors, such as moisture, contamination, and electrostatic discharge (ESD). In applications where robust soldermask protection is essential, copper defined pads may not be the optimal choice.
3. Potential for Copper Pad Damage
During the soldermask application process, copper defined pads are exposed and vulnerable to damage from handling or contact with the soldermask material. Any scratches, dings, or contamination on the copper surface can negatively impact the solderability and reliability of the pad. To minimize the risk of damage, extra care must be taken during the soldermask application and subsequent handling of the PCB.
Advantages of Soldermask Defined Pads
1. Reduced Solder Bridging Risk
Soldermask defined pads offer a significant advantage in reducing the risk of solder bridging between adjacent pads. The soldermask layer acts as a barrier, preventing solder from flowing beyond the defined solderable area. This containment is particularly beneficial in designs with fine-pitch components or high-density layouts, where the likelihood of solder bridging is higher.
2. Improved Soldermask Coverage
With soldermask defined pads, the soldermask layer extends over a larger portion of the copper pad, providing better overall coverage and protection. This increased coverage helps to safeguard the PCB against environmental factors, such as moisture, dust, and chemical contamination. Enhanced soldermask coverage also improves the board’s resistance to electrostatic discharge (ESD) events, which can damage sensitive components.
3. Better Aesthetics
Soldermask defined pads can contribute to improved PCB aesthetics, particularly in applications where visual appearance is important. The smaller soldermask openings create a cleaner, more uniform look, with less exposed copper on the board surface. This aesthetic enhancement can be especially relevant for consumer electronics or products where a premium appearance is desired.
Disadvantages of Soldermask Defined Pads
1. Reduced Solder Joint Strength
One potential drawback of soldermask defined pads is the reduced solder joint strength compared to copper defined pads. The smaller solderable area, defined by the soldermask opening, provides less surface area for the solder to bond with the copper pad. This reduced bonding area can result in weaker solder joints, which may be more susceptible to failure under mechanical stress or thermal cycling.
2. Soldermask Alignment Criticality
Soldermask defined pads rely heavily on the accurate alignment of the soldermask layer to the copper pads. Any misalignment or variations in the soldermask opening can directly impact the solderable area and, consequently, the solder joint quality. Ensuring precise soldermask alignment requires tight process control and may lead to increased manufacturing costs and potential yield issues.
3. Limited Pad Size Flexibility
With soldermask defined pads, the solderable area is constrained by the soldermask opening size. This limitation can restrict the designer’s flexibility in terms of pad dimensions, particularly when working with larger components or connectors. In some cases, the soldermask opening may not provide sufficient space for the desired pad size, necessitating a switch to copper defined pads or a redesign of the component layout.
Choosing Between Copper Defined and Soldermask Defined Pads
The decision to use copper defined or soldermask defined pads depends on various factors, including the specific application, design requirements, manufacturing capabilities, and cost considerations. The following table summarizes the key factors to consider when making this choice:
Factor | Copper Defined Pads | Soldermask Defined Pads |
---|---|---|
Solder Joint Strength | Higher | Lower |
Solder Bridging Risk | Higher | Lower |
Soldermask Coverage | Lower | Higher |
Copper Etching Accuracy | Higher | Lower |
Soldermask Alignment | Less Critical | More Critical |
Pad Size Flexibility | Higher | Lower |
Aesthetics | Less Uniform | More Uniform |
Designers should carefully evaluate these factors and consult with their manufacturing partners to determine the most suitable approach for their specific project.
Frequently Asked Questions (FAQ)
1. Can I mix copper defined and soldermask defined pads on the same PCB?
Yes, it is possible to use both copper defined and soldermask defined pads on the same PCB. However, it’s essential to clearly communicate this requirement to the manufacturer and ensure that the design files accurately reflect the desired pad definitions. Mixing pad types can be useful in situations where different components have specific requirements or when balancing the advantages and disadvantages of each approach.
2. Are there any specific industries or applications that prefer one pad definition over the other?
Some industries, such as aerospace and defense, may prefer copper defined pads due to their increased solder joint reliability and resistance to mechanical stress. In contrast, consumer electronics and applications with high-density layouts may favor soldermask defined pads for their reduced solder bridging risk and improved aesthetics. However, the choice ultimately depends on the specific requirements and constraints of each project.
3. How do copper defined and soldermask defined pads impact the assembly process?
The choice of pad definition can influence the assembly process in several ways. Copper defined pads may require more precise solder paste application to avoid bridging, while soldermask defined pads can be more forgiving in this regard. Additionally, the pad definition can affect the solder joint profile and the amount of solder wicking onto the pad. Assembly process parameters, such as stencil design, solder paste selection, and reflow profile, may need to be adjusted based on the chosen pad definition to ensure optimal results.
4. Are there any cost implications when choosing between copper defined and soldermask defined pads?
In most cases, the cost difference between copper defined and soldermask defined pads is minimal. However, soldermask defined pads may require tighter tolerances and more precise alignment during manufacturing, which can slightly increase production costs. On the other hand, copper defined pads may necessitate additional design considerations to mitigate solder bridging risk, which can also impact overall costs. It’s essential to discuss cost implications with the manufacturing partner and make decisions based on the project’s specific budget and requirements.
5. Can the choice of pad definition affect the PCB’s long-term reliability?
Yes, the choice of pad definition can have an impact on the PCB’s long-term reliability. Copper defined pads typically offer stronger solder joints, which can enhance the board’s resistance to mechanical stress and thermal cycling. However, soldermask defined pads provide better protection against environmental factors, such as moisture and contamination, which can contribute to improved long-term reliability in certain applications. Designers should carefully consider the specific reliability requirements of their project and select the pad definition that best meets those needs.
Conclusion
Understanding the advantages and disadvantages of copper defined and soldermask defined pads is crucial for designing and manufacturing high-quality, reliable PCBs. By carefully evaluating the specific requirements of each project, designers can make informed decisions that balance factors such as solder joint strength, solder bridging risk, soldermask coverage, and manufacturing considerations.
Effective communication between the design team and the manufacturing partner is essential to ensure that the chosen pad definition is properly implemented and optimized for the specific application. By taking a holistic approach and considering the various trade-offs associated with each pad definition, designers can create PCBs that meet the desired performance, reliability, and cost targets.
As technology continues to advance and PCB designs become increasingly complex, staying informed about the latest techniques and best practices in pad definition will be crucial for success in the ever-evolving world of electronics manufacturing.
0 Comments