What is Conformal Coating?
Conformal coating is a protective layer applied to printed circuit boards (PCBs) to shield them from environmental factors such as moisture, dust, chemicals, and extreme temperatures. This coating is a thin polymeric film that “conforms” to the contours of the PCB, including the components and solder joints. Conformal coating is essential for ensuring the reliability and longevity of electronic devices, particularly those exposed to harsh conditions.
Types of Conformal Coating
There are several types of Conformal Coatings, each with its own unique properties and advantages. The most common types include:
- Acrylic Resin (AR)
- Silicone Resin (SR)
- Polyurethane (UR)
- Epoxy Resin (ER)
- Parylene (XY)
Type | Advantages | Disadvantages |
---|---|---|
Acrylic Resin (AR) | Easy to apply and remove, cost-effective, fast-drying | Limited chemical and abrasion resistance |
Silicone Resin (SR) | High flexibility, wide temperature range, good moisture resistance | Difficult to apply and remove, expensive |
Polyurethane (UR) | Excellent abrasion and chemical resistance, good dielectric properties | Requires a thicker coating, can be difficult to remove |
Epoxy Resin (ER) | High chemical and abrasion resistance, good adhesion | Brittle, difficult to remove, requires high cure temperatures |
Parylene (XY) | Uniform coating, excellent dielectric properties, thin coating | Expensive, requires specialized equipment for application |
Why is Conformal Coating Important?
Conformal coating is crucial for protecting PCBs from various environmental factors that can lead to device failure. Some of the key benefits of conformal coating include:
- Protection against moisture and humidity
- Resistance to chemicals and solvents
- Insulation against high voltages
- Prevention of dendrite growth and leakage currents
- Mechanical protection against vibration and shock
Industries that Require Conformal Coating
Many industries rely on conformal coating to ensure the reliability and longevity of their electronic devices. Some of these industries include:
- Aerospace and Defense
- Automotive
- Medical Devices
- Consumer Electronics
- Industrial Equipment
- Marine and Offshore
How to Apply Conformal Coating
There are several methods for applying conformal coating to PCBs. The choice of method depends on factors such as the type of coating, the size and complexity of the PCB, and the production volume. The most common application methods include:
Spraying
Spraying is a popular method for applying conformal coating, as it offers good coverage and can be automated for high-volume production. This method involves using a spray gun to atomize the coating material and apply it evenly to the PCB surface.
Dipping
Dipping involves immersing the PCB in a tank of conformal coating material. This method ensures complete coverage of the PCB, including hard-to-reach areas. However, it can be difficult to control the coating thickness and may require masking of certain components.
Brush Coating
Brush coating is a manual method that involves applying the conformal coating with a brush. This method is suitable for small-scale production or for coating specific areas of the PCB. Brush coating allows for precise control of the coating application but can be time-consuming and may result in inconsistent coverage.
Selective Coating
Selective coating involves applying the conformal coating only to specific areas of the PCB, such as sensitive components or connectors. This method can be automated using specialized equipment, such as needle dispensers or robotic systems, to ensure precise and repeatable coating application.
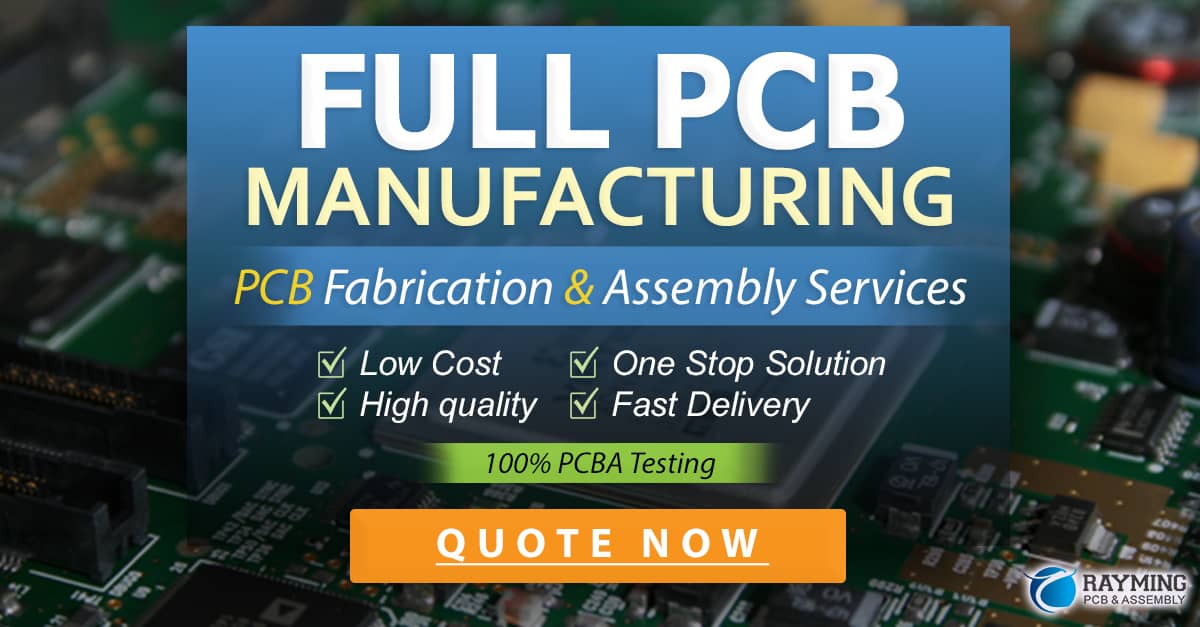
Inspection and Testing of Conformal Coating
After applying the conformal coating, it is essential to inspect and test the PCB to ensure proper coverage and performance. Some common inspection and testing methods include:
-
Visual Inspection: This involves examining the coated PCB under magnification to check for defects such as bubbles, voids, or inadequate coverage.
-
Thickness Measurement: Using a thickness gauge or microscope, the coating thickness can be measured to ensure it meets the specified requirements.
-
Adhesion Testing: This test involves applying a tape to the coated surface and then pulling it off to check the coating’s adhesion to the PCB.
-
Insulation Resistance (IR) Testing: IR testing measures the coating’s ability to resist electrical current flow and maintain insulation properties.
-
Salt Spray Testing: This test exposes the coated PCB to a salt spray environment to evaluate its corrosion resistance.
Removing Conformal Coating
In some cases, it may be necessary to remove the conformal coating for rework, repair, or inspection purposes. The removal method depends on the type of coating and the specific requirements of the PCB. Some common removal methods include:
-
Solvent Removal: This involves using a chemical solvent to dissolve the coating material. The solvent is applied to the coated surface and then wiped or brushed away, taking the coating with it.
-
Mechanical Removal: This method uses abrasive tools, such as scrapers or sandpaper, to physically remove the coating from the PCB surface. Care must be taken not to damage the underlying components or circuitry.
-
Thermal Removal: Some conformal coatings, such as parylene, can be removed using heat. The coated PCB is heated to a specific temperature, causing the coating to decompose and evaporate.
-
Plasma Removal: This advanced method uses a plasma etching process to remove the conformal coating selectively. The coated PCB is exposed to a plasma gas, which reacts with the coating material and removes it from the surface.
Frequently Asked Questions (FAQ)
1. How do I choose the right conformal coating for my PCB?
Choosing the right conformal coating depends on several factors, including the environmental conditions the PCB will be exposed to, the required performance characteristics, and the compatibility with the PCB materials and components. Consider consulting with a coating specialist or reviewing the manufacturer’s guidelines to select the most suitable coating for your application.
2. Can conformal coating be applied to populated PCBs?
Yes, conformal coating can be applied to populated PCBs. However, care must be taken to mask or protect sensitive components, such as connectors or switches, that should not be coated. Selective coating methods, such as brush coating or needle dispensing, can be used to apply the coating only to specific areas of the populated PCB.
3. How does conformal coating affect PCB Repair and rework?
Conformal coating can make PCB repair and rework more challenging, as the coating must be removed to access the underlying components or circuitry. The coating removal process can be time-consuming and may require specialized equipment or solvents. However, many conformal coatings are designed to be removable, and following the manufacturer’s guidelines for removal can help minimize any potential issues.
4. What is the typical thickness of a conformal coating?
The typical thickness of a conformal coating varies depending on the type of coating and the application method. In general, conformal coatings range from 25 to 250 microns (0.001 to 0.010 inches) in thickness. Thinner coatings may be sufficient for general-purpose protection, while thicker coatings may be required for more demanding environments or high-voltage applications.
5. How long does conformal coating last?
The longevity of a conformal coating depends on various factors, such as the type of coating, the environmental conditions, and the quality of the application process. In general, conformal coatings can last for several years or even decades, provided they are applied correctly and the PCB is not subjected to extreme conditions or mechanical damage. Regular inspection and maintenance can help extend the life of the conformal coating and ensure optimal performance of the PCB.
Conclusion
Conformal coating is a critical process for protecting PCBs from environmental factors and ensuring the reliability and longevity of electronic devices. By understanding the different types of conformal coatings, their application methods, and the inspection and testing procedures, engineers and manufacturers can make informed decisions about the best coating solution for their specific requirements. As the electronics industry continues to evolve and push the boundaries of performance and reliability, conformal coating will remain an essential tool for protecting and enhancing the functionality of PCBs in a wide range of applications.
0 Comments