Why PCB certifications Matter
PCB certifications are vital for several reasons:
- Quality assurance: Certifications ensure that the manufacturer follows strict quality control processes, resulting in consistently high-quality PCBs.
- Reliability: Certified manufacturers are more likely to produce reliable PCBs that function as intended, reducing the risk of failures and delays.
- Compliance: Certifications demonstrate compliance with industry regulations and standards, which is especially important for PCBs used in sensitive applications such as medical devices or aerospace.
- Customer confidence: Partnering with a certified manufacturer instills confidence in customers, knowing that their PCBs are produced by a reputable and qualified company.
Essential PCB Certifications
1. ISO 9001
ISO 9001 is a globally recognized quality management system (QMS) standard. It ensures that the manufacturer has a well-documented and implemented QMS that focuses on continuous improvement, customer satisfaction, and consistent product quality.
ISO 9001 Key Requirements | Description |
---|---|
Customer focus | Understanding and meeting customer requirements |
Leadership | Establishing a clear direction and engaging employees |
Process approach | Managing activities and resources as processes |
Improvement | Continuously improving processes and performance |
Evidence-based decisions | Making decisions based on data and analysis |
Relationship management | Managing relationships with suppliers and other stakeholders |
2. IPC Standards
IPC (Association Connecting Electronics Industries) is a global trade association that develops standards for the electronics industry. Some essential IPC standards for PCBs include:
IPC-A-600
IPC-A-600 is a standard that defines the acceptability criteria for PCBs. It covers various aspects such as:
- Visual and dimensional requirements
- Material and construction requirements
- Solderability and surface finish requirements
- Electrical performance requirements
IPC-6012
IPC-6012 is a standard that defines the qualification and performance specifications for rigid PCBs. It covers requirements for:
- Material selection and compatibility
- Conductor definition and spacing
- Hole size and placement
- Solder mask and marking
- Electrical testing
IPC-A-610
IPC-A-610 is a standard that provides acceptance criteria for electronic assemblies. It covers requirements for:
- Soldering and assembly processes
- Component placement and alignment
- Cleanliness and contamination control
- Mechanical and electrical integrity
3. UL Certification
Underwriters Laboratories (UL) is a global safety certification company that tests and certifies products for safety and performance. UL certification is essential for PCBs used in products that require safety certification, such as consumer electronics or industrial equipment.
UL Standard | Description |
---|---|
UL 94 | Tests for flammability of plastic materials |
UL 796 | Standard for printed wiring boards |
UL 746 | Standard for polymeric materials |
UL 60950 | Standard for information technology equipment safety |
4. IATF 16949
IATF 16949 is a quality management system standard specifically for the automotive industry. If your PCBs are intended for use in automotive applications, your manufacturing partner must be IATF 16949 certified. This standard builds upon ISO 9001 and includes additional requirements specific to the automotive sector, such as:
- Product safety and reliability
- Defect prevention and reduction
- Continuous improvement
- Supply chain management
5. AS9100
AS9100 is a quality management system standard for the aerospace industry. If your PCBs are intended for use in aerospace applications, your manufacturing partner should be AS9100 certified. This standard includes requirements specific to the aerospace sector, such as:
- Configuration management
- Risk management
- Counterfeit parts prevention
- Product realization
Additional Considerations
In addition to the certifications mentioned above, there are other factors to consider when selecting a PCB manufacturing partner:
- Experience: Choose a manufacturer with a proven track record of producing high-quality PCBs for your specific industry or application.
- Capabilities: Ensure that the manufacturer has the necessary equipment, facilities, and expertise to produce your PCBs according to your specifications.
- Customer service: Look for a manufacturer that provides excellent customer support, communication, and responsiveness throughout the manufacturing process.
- Pricing: While cost is an important factor, avoid compromising on quality and reliability for the sake of lower prices.
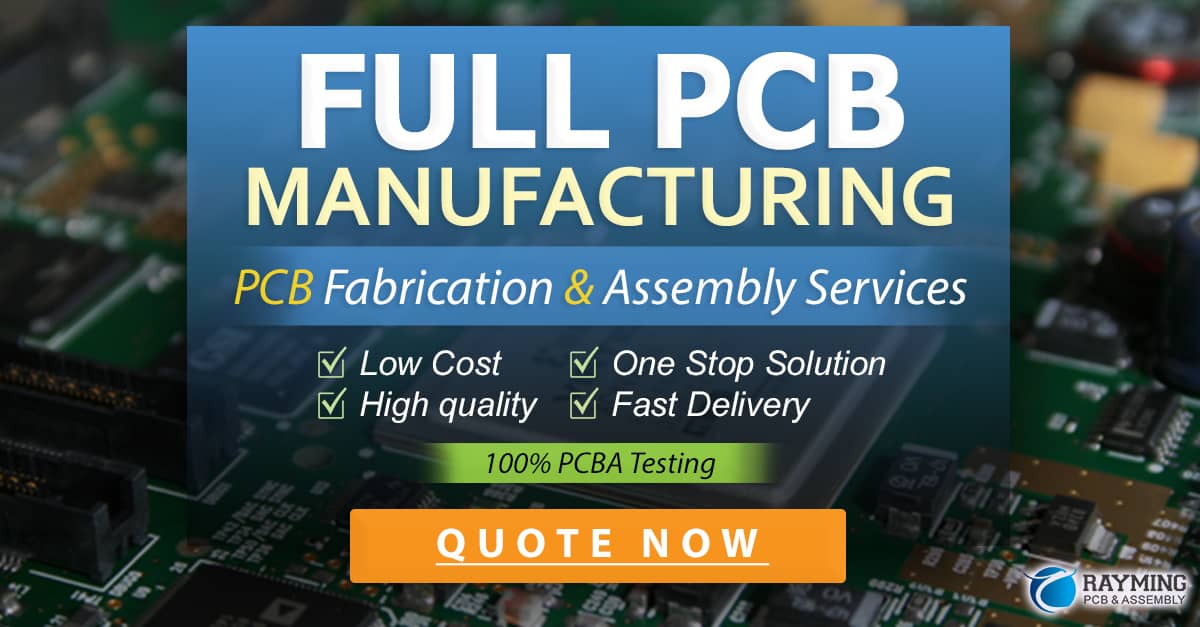
FAQ
-
Q: What happens if a PCB manufacturer loses their certification?
A: If a manufacturer loses their certification, it means they no longer meet the requirements of that particular standard. This could be due to changes in their processes, equipment, or personnel. It’s essential to verify that your manufacturing partner maintains their certifications regularly. -
Q: Can a manufacturer have multiple certifications?
A: Yes, a manufacturer can hold multiple certifications, such as ISO 9001, IPC standards, and industry-specific certifications like IATF 16949 or AS9100. Having multiple certifications demonstrates a commitment to quality and compliance across various sectors. -
Q: How often do manufacturers need to renew their certifications?
A: The frequency of certification renewal depends on the specific standard and the certifying body. Most certifications require annual surveillance audits and a full recertification audit every three years. However, some certifications may have different renewal cycles. -
Q: Can I request copies of a manufacturer’s certifications?
A: Yes, you can and should request copies of a manufacturer’s certifications. Most reputable manufacturers will readily provide their certification documents upon request. Reviewing these documents helps verify the manufacturer’s compliance and ensures their certifications are up to date. -
Q: What if my PCB application doesn’t require specific certifications?
A: Even if your PCB application doesn’t require specific certifications, working with a certified manufacturer ensures a higher level of quality, reliability, and consistency. Certifications demonstrate a manufacturer’s commitment to best practices and continuous improvement, which benefits all customers regardless of their specific requirements.
Conclusion
Choosing a PCB manufacturing partner with the right certifications is crucial for ensuring the quality, reliability, and compliance of your PCBs. ISO 9001, IPC standards, UL certification, IATF 16949, and AS9100 are among the essential certifications to look for, depending on your industry and application.
By partnering with a certified manufacturer, you can have confidence in their processes, products, and services, ultimately leading to the successful production of your PCBs and the satisfaction of your end-users.
0 Comments