Introduction to Heat Sink PCBs
In the world of electronics, heat management is a crucial aspect of ensuring the proper functioning and longevity of devices. As electronic components become more compact and powerful, the need for efficient heat dissipation becomes increasingly important. This is where Heat Sink Printed Circuit Boards (PCBs) come into play. Heat Sink PCBs are specially designed to efficiently transfer heat away from electronic components, preventing overheating and ensuring optimal performance.
What is a Heat Sink PCB?
A Heat Sink PCB is a type of printed circuit board that incorporates a heat sink directly onto the board itself. A heat sink is a passive heat exchanger that absorbs and dissipates heat from electronic components. By integrating the heat sink into the PCB design, Heat Sink PCBs provide a compact and efficient solution for heat management in electronic devices.
Key features of Heat Sink PCBs
- Integrated heat sink: The heat sink is directly attached to the PCB, eliminating the need for separate heat sink components.
- Thermal vias: Heat Sink PCBs often feature thermal vias, which are small holes filled with conductive material that help transfer heat from the components to the heat sink.
- High thermal conductivity: The materials used in Heat Sink PCBs, such as copper and aluminum, have high thermal conductivity, allowing for efficient heat transfer.
- Customizable design: Heat Sink PCBs can be customized to fit the specific requirements of different electronic devices, ensuring optimal heat dissipation.
Importance of Heat Sink PCBs in the Electrical Industry
The electrical industry relies heavily on the proper functioning and reliability of electronic devices. Heat Sink PCBs play a vital role in ensuring the performance and longevity of these devices by effectively managing heat dissipation. Here are some key reasons why Heat Sink PCBs are essential in the electrical industry:
1. Preventing overheating
One of the primary functions of Heat Sink PCBs is to prevent electronic components from overheating. Overheating can lead to a range of issues, including:
- Reduced performance: As electronic components heat up, their performance may degrade, leading to slower processing speeds and potential errors.
- Shortened lifespan: Prolonged exposure to high temperatures can cause electronic components to deteriorate faster, reducing their overall lifespan.
- Safety hazards: In extreme cases, overheating can cause electronic devices to malfunction or even catch fire, posing safety risks to users.
By efficiently dissipating heat away from electronic components, Heat Sink PCBs help prevent these issues and ensure the stable operation of electronic devices.
2. Enabling compact designs
The electrical industry is constantly pushing for smaller and more compact electronic devices. However, as devices become smaller, the heat generated by electronic components becomes more concentrated, making heat dissipation a significant challenge. Heat Sink PCBs offer a solution to this problem by integrating the heat sink directly onto the PCB, eliminating the need for separate heat sink components and allowing for more compact device designs.
3. Improving reliability and longevity
Effective heat management is crucial for the reliability and longevity of electronic devices. By preventing overheating and ensuring that electronic components operate within their optimal temperature range, Heat Sink PCBs contribute to the overall reliability of electronic devices. This is particularly important in applications where device failure can have severe consequences, such as in medical equipment, aerospace systems, and industrial control devices.
4. Cost-effective solution
Heat Sink PCBs provide a cost-effective solution for heat management in electronic devices. By integrating the heat sink directly onto the PCB, the need for separate heat sink components is eliminated, reducing the overall cost of the device. Additionally, the improved reliability and longevity offered by Heat Sink PCBs can lead to reduced maintenance and replacement costs over the life of the device.
Applications of Heat Sink PCBs
Heat Sink PCBs find applications in a wide range of industries and devices. Some common applications include:
1. Power electronics
Power electronic devices, such as power converters, inverters, and motor drives, generate significant amounts of heat due to the high currents and voltages involved. Heat Sink PCBs are commonly used in these devices to ensure efficient heat dissipation and prevent overheating.
2. LED lighting
LED lighting systems, particularly high-power LED arrays, generate a considerable amount of heat. Heat Sink PCBs are used in LED lighting applications to prevent overheating and ensure the longevity and performance of the LEDs.
3. Automotive electronics
The automotive industry relies heavily on electronic systems for various functions, such as engine control, infotainment, and safety features. Heat Sink PCBs are used in automotive electronic devices to ensure reliable operation in the harsh environment of a vehicle, where temperatures can fluctuate significantly.
4. Industrial control systems
Industrial control systems, such as programmable logic controllers (PLCs) and human-machine interfaces (HMIs), often operate in challenging environments with high temperatures and vibrations. Heat Sink PCBs are used in these systems to ensure reliable operation and prevent overheating.
5. Aerospace and defense
Electronic devices used in aerospace and defense applications must meet stringent reliability and performance requirements. Heat Sink PCBs are used in these applications to ensure effective heat management and reliable operation in demanding environments.
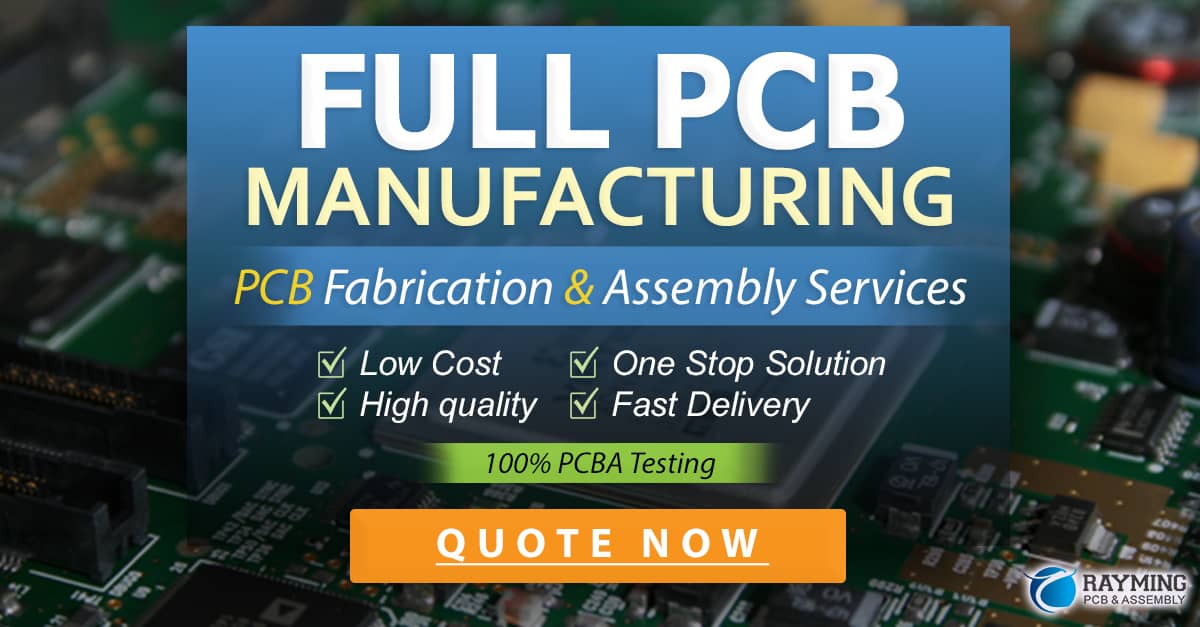
Design Considerations for Heat Sink PCBs
When designing Heat Sink PCBs, several key factors must be considered to ensure optimal heat dissipation and overall performance. These include:
1. Material selection
The choice of materials for Heat Sink PCBs is critical for effective heat dissipation. Some commonly used materials include:
Material | Thermal Conductivity (W/mK) | Advantages | Disadvantages |
---|---|---|---|
Copper | 385-401 | High thermal conductivity, excellent electrical conductivity | Expensive, heavy |
Aluminum | 205-237 | Lightweight, good thermal conductivity, cost-effective | Lower electrical conductivity than copper |
Copper-clad aluminum | 173-220 | Combines advantages of copper and aluminum | Limited thickness options |
2. Thermal via design
Thermal vias play a crucial role in transferring heat from the electronic components to the heat sink. When designing thermal vias, consider the following:
- Size and number of vias: Larger and more numerous vias provide better heat transfer but may impact the available space for routing.
- Via placement: Thermal vias should be placed as close to the heat-generating components as possible for optimal heat transfer.
- Via filling: Filling thermal vias with conductive material, such as copper or silver epoxy, improves heat transfer.
3. Heat sink design
The design of the heat sink itself is critical for effective heat dissipation. Consider the following factors:
- Surface area: A larger surface area allows for better heat dissipation. Consider using fins or other features to increase the surface area of the heat sink.
- Orientation: The orientation of the heat sink should be optimized for natural convection, allowing hot air to rise and cool air to flow in.
- Attachment method: The heat sink must be securely attached to the PCB to ensure efficient heat transfer. Common attachment methods include soldering, mechanical fasteners, and thermal adhesives.
4. Thermal interface materials
Thermal interface materials (TIMs) are used to improve the thermal contact between the electronic components and the heat sink. TIMs fill in any air gaps and irregularities, allowing for better heat transfer. Common TIMs include thermal greases, thermal pads, and phase change materials.
Manufacturing Process for Heat Sink PCBs
The manufacturing process for Heat Sink PCBs involves several key steps:
- PCB design: The PCB is designed using computer-aided design (CAD) software, incorporating the heat sink and thermal vias.
- PCB fabrication: The PCB is fabricated using standard PCB manufacturing processes, such as etching, drilling, and plating.
- Heat sink attachment: The heat sink is attached to the PCB using the chosen attachment method, such as soldering or mechanical fasteners.
- Component assembly: The electronic components are assembled onto the PCB using standard assembly processes, such as surface-mount technology (SMT) or through-hole technology.
- Testing and inspection: The assembled Heat Sink PCB undergoes testing and inspection to ensure proper functionality and heat dissipation performance.
Advantages of Heat Sink PCBs
Heat Sink PCBs offer several advantages over traditional heat management solutions:
- Compact design: By integrating the heat sink directly onto the PCB, Heat Sink PCBs allow for more compact device designs.
- Improved heat dissipation: Heat Sink PCBs provide efficient heat dissipation, preventing overheating and ensuring optimal performance of electronic components.
- Enhanced reliability: Effective heat management provided by Heat Sink PCBs contributes to the overall reliability and longevity of electronic devices.
- Cost-effective: Heat Sink PCBs eliminate the need for separate heat sink components, reducing the overall cost of the device.
Challenges and Limitations of Heat Sink PCBs
While Heat Sink PCBs offer many benefits, there are also some challenges and limitations to consider:
- Design complexity: Incorporating a heat sink into the PCB design can increase the complexity of the design process, requiring careful consideration of thermal management aspects.
- Manufacturing challenges: The manufacturing process for Heat Sink PCBs can be more complex than traditional PCBs, requiring specialized equipment and expertise.
- Cost: While Heat Sink PCBs can be cost-effective in the long run, the initial design and manufacturing costs may be higher than traditional PCB solutions.
- Weight: Depending on the materials used, Heat Sink PCBs may be heavier than traditional PCBs, which can be a concern in weight-sensitive applications.
Future Trends in Heat Sink PCB Technology
As electronic devices continue to become more compact and powerful, the demand for advanced heat management solutions will continue to grow. Some future trends in Heat Sink PCB technology include:
- Advanced materials: The development of new materials with higher thermal conductivity and lower weight, such as graphene and carbon nanotubes, may lead to more efficient and lightweight Heat Sink PCBs.
- 3D printing: The use of 3D printing technology for the fabrication of Heat Sink PCBs may allow for more complex and optimized heat sink designs.
- Active cooling: The integration of active cooling solutions, such as miniature fans or liquid cooling systems, onto Heat Sink PCBs may provide even better heat dissipation performance.
- Embedded sensors: The incorporation of temperature sensors directly onto Heat Sink PCBs may enable real-time monitoring and control of heat dissipation, ensuring optimal performance and safety.
Frequently Asked Questions (FAQ)
-
What is the difference between a Heat Sink PCB and a traditional PCB?
A Heat Sink PCB integrates a heat sink directly onto the PCB itself, while a traditional PCB relies on separate heat sink components for heat dissipation. -
What materials are commonly used in Heat Sink PCBs?
Common materials used in Heat Sink PCBs include copper, aluminum, and copper-clad aluminum. These materials are chosen for their high thermal conductivity and ability to efficiently transfer heat. -
How do thermal vias work in Heat Sink PCBs?
Thermal vias are small holes drilled through the PCB and filled with conductive material, such as copper or silver epoxy. They provide a path for heat to transfer from the electronic components to the heat sink, improving overall heat dissipation. -
Can Heat Sink PCBs be customized for specific applications?
Yes, Heat Sink PCBs can be customized to meet the specific requirements of different applications. The design of the heat sink, thermal vias, and other features can be optimized based on the heat dissipation needs and space constraints of the device. -
Are Heat Sink PCBs more expensive than traditional PCBs?
The initial design and manufacturing costs for Heat Sink PCBs may be higher than traditional PCBs due to the added complexity of incorporating a heat sink. However, the long-term cost benefits, such as improved reliability and reduced need for separate heat sink components, can make Heat Sink PCBs a cost-effective solution in many applications.
Conclusion
Heat Sink PCBs are a crucial component in the electrical industry, providing efficient and reliable heat management solutions for a wide range of electronic devices. By integrating heat sinks directly onto the PCB, Heat Sink PCBs offer compact, cost-effective, and high-performance heat dissipation, ensuring the optimal functioning and longevity of electronic components.
As the demand for more advanced and compact electronic devices continues to grow, the importance of Heat Sink PCBs will only increase. With ongoing advancements in materials, manufacturing processes, and design techniques, Heat Sink PCBs are poised to play a vital role in shaping the future of the electrical industry.
0 Comments