Introduction
In the world of electronics, the demand for high-performance, compact, and reliable devices is constantly increasing. To meet these challenges, manufacturers are turning to Embedded PCB Assemblies as a solution. Embedded PCB assemblies offer numerous advantages over traditional PCB designs, including improved performance, reduced size, and enhanced reliability.
This article will explore the potential of embedded PCB assemblies and how they can be used to improve the performance of electronics devices. We will discuss the benefits of embedded PCB assemblies, the different types of embedded PCB assemblies, and the design considerations for implementing them in electronics devices.
What are Embedded PCB Assemblies?
Embedded PCB assemblies are a type of printed circuit board (PCB) where electronic components are embedded within the layers of the board itself. This is in contrast to traditional PCB designs, where components are mounted on the surface of the board.
In an embedded PCB assembly, the components are placed in cavities or pockets within the layers of the board. These cavities are typically filled with a dielectric material, such as epoxy or polyimide, to provide insulation and protection for the components.
Benefits of Embedded PCB Assemblies
Embedded PCB assemblies offer several key benefits over traditional PCB designs:
-
Improved Performance: By embedding components within the layers of the board, the distance between components is reduced, leading to improved signal integrity and reduced noise and interference.
-
Reduced Size: Embedded PCB assemblies allow for a more compact design, as components can be placed closer together and within the layers of the board itself.
-
Enhanced Reliability: The embedded components are protected from external factors such as moisture, dust, and physical damage, leading to improved reliability and longer product life.
-
Increased Functionality: Embedded PCB assemblies can accommodate a higher density of components, allowing for more complex and feature-rich designs.
Types of Embedded PCB Assemblies
There are several different types of embedded PCB assemblies, each with its own unique characteristics and applications.
Cavity Embedding
In cavity embedding, components are placed in cavities within the layers of the board. These cavities are typically filled with a dielectric material to provide insulation and protection for the components.
Cavity embedding is well-suited for applications that require a high degree of protection for sensitive components, such as medical devices or aerospace electronics.
Copper Coin Embedding
Copper coin embedding involves placing copper coins or discs within the layers of the board. These coins serve as thermal and electrical conductors, helping to dissipate heat and provide a low-impedance path for electrical signals.
Copper coin embedding is commonly used in power electronics applications, where efficient heat dissipation and low-impedance electrical connections are critical.
Chip Embedding
Chip embedding involves placing bare die or packaged chips directly within the layers of the board. This allows for a highly compact design and improved electrical performance, as the distance between the chip and other components is minimized.
Chip embedding is often used in high-performance computing and telecommunications applications, where space is at a premium and signal integrity is critical.
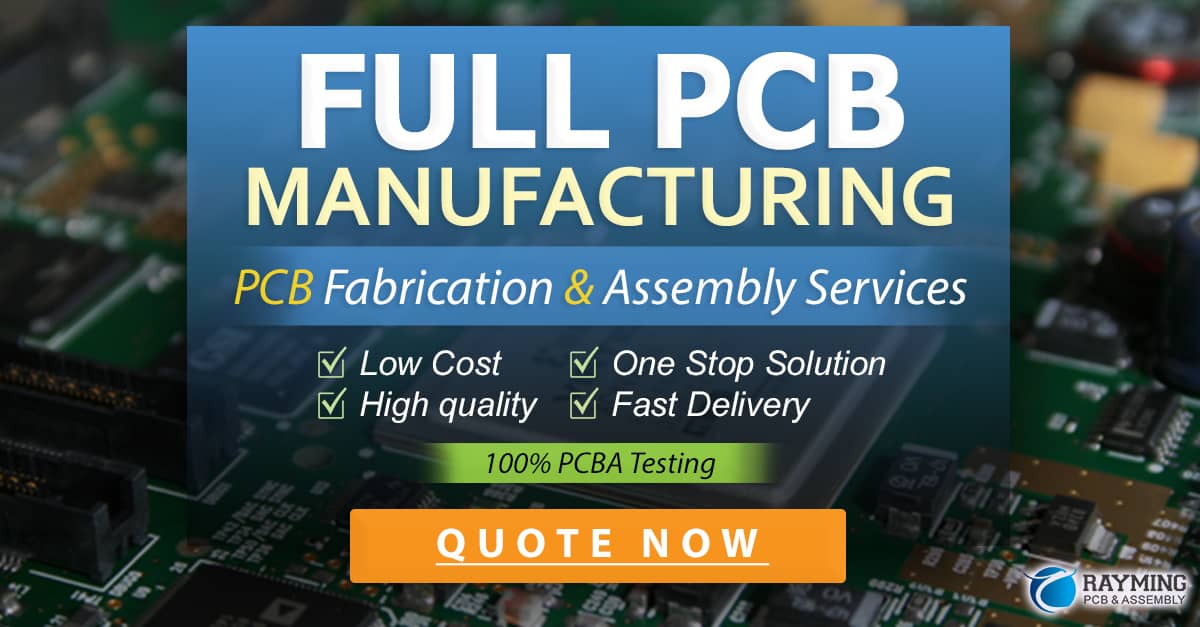
Design Considerations for Embedded PCB Assemblies
When designing embedded PCB assemblies, there are several key considerations that must be taken into account to ensure optimal performance and reliability.
Material Selection
The choice of materials for the PCB substrate, dielectric, and conductive layers is critical in embedded PCB assemblies. The materials must be compatible with the embedding process and provide the necessary electrical, thermal, and mechanical properties for the application.
Some common materials used in embedded PCB assemblies include:
Material | Properties |
---|---|
FR-4 | Low cost, good mechanical strength, suitable for general-purpose applications |
Polyimide | High temperature resistance, good electrical properties, suitable for high-reliability applications |
PTFE | Low dielectric constant, low loss, suitable for high-frequency applications |
Ceramic | High thermal conductivity, low CTE, suitable for high-power applications |
Thermal Management
Embedded PCB assemblies can present unique thermal management challenges, as the embedded components may generate significant heat that must be dissipated to prevent damage or performance degradation.
Some strategies for thermal management in embedded PCB assemblies include:
- Using thermally conductive materials, such as copper or aluminum, for the PCB substrate or thermal vias
- Incorporating heat spreaders or heat sinks to dissipate heat from high-power components
- Optimizing the placement and orientation of components to minimize thermal coupling and promote efficient heat dissipation
Signal Integrity
Maintaining signal integrity is critical in embedded PCB assemblies, as the close proximity of components can lead to increased noise, crosstalk, and other signal integrity issues.
Some techniques for improving signal integrity in embedded PCB assemblies include:
- Using controlled impedance design techniques to match the impedance of the signal traces to the source and load impedances
- Implementing ground planes and power planes to provide low-impedance return paths and minimize noise and interference
- Using differential signaling for high-speed signals to cancel out common-mode noise and improve signal-to-noise ratio
Manufacturing Process
The manufacturing process for embedded PCB assemblies is more complex than traditional PCB manufacturing, as it involves additional steps such as cavity formation, component placement, and dielectric filling.
Some key considerations for the manufacturing process include:
- Selecting a manufacturing partner with experience and expertise in embedded PCB assembly
- Ensuring that the design is compatible with the chosen manufacturing process and materials
- Implementing appropriate quality control measures to ensure consistent and reliable performance of the finished product
Applications of Embedded PCB Assemblies
Embedded PCB assemblies are used in a wide range of electronics applications, from consumer devices to industrial and aerospace systems. Some examples of applications that can benefit from embedded PCB assemblies include:
Wearable Electronics
Wearable devices, such as smartwatches and fitness trackers, require highly compact and lightweight designs. Embedded PCB assemblies can help to minimize the size and weight of these devices while providing the necessary functionality and performance.
Automotive Electronics
The harsh operating environment and high reliability requirements of automotive electronics make embedded PCB assemblies an attractive option. Embedded assemblies can provide improved protection against vibration, temperature extremes, and moisture, while also enabling more compact and lightweight designs.
Medical Devices
Medical devices, such as implantable sensors and drug delivery systems, require a high degree of reliability and biocompatibility. Embedded PCB assemblies can provide the necessary protection and performance for these critical applications.
Aerospace and Defense
Aerospace and defense applications demand the highest levels of performance and reliability. Embedded PCB assemblies can help to meet these requirements while also providing the necessary ruggedness and environmental resistance for operation in extreme conditions.
Frequently Asked Questions (FAQ)
-
Q: What are the main benefits of using embedded PCB assemblies?
A: The main benefits of embedded PCB assemblies include improved performance, reduced size, enhanced reliability, and increased functionality compared to traditional PCB designs. -
Q: What types of materials are commonly used in embedded PCB assemblies?
A: Common materials used in embedded PCB assemblies include FR-4, polyimide, PTFE, and ceramic, each offering different properties suitable for various applications. -
Q: How can thermal management be addressed in embedded PCB assemblies?
A: Thermal management in embedded PCB assemblies can be addressed through the use of thermally conductive materials, heat spreaders or heat sinks, and optimized component placement and orientation. -
Q: What techniques can be used to improve signal integrity in embedded PCB assemblies?
A: Techniques for improving signal integrity in embedded PCB assemblies include controlled impedance design, implementing ground and power planes, and using differential signaling for high-speed signals. -
Q: What industries can benefit from the use of embedded PCB assemblies?
A: Industries that can benefit from embedded PCB assemblies include wearable electronics, automotive electronics, medical devices, and aerospace and defense.
Conclusion
Embedded PCB assemblies offer a powerful solution for improving the performance, reliability, and functionality of electronics devices. By embedding components within the layers of the board, designers can achieve more compact, high-performance designs that are well-suited for a wide range of applications.
However, implementing embedded PCB assemblies requires careful consideration of material selection, thermal management, signal integrity, and manufacturing processes. By working with experienced manufacturing partners and following best practices for embedded PCB design, electronics manufacturers can unlock the full potential of this innovative technology and deliver cutting-edge products to their customers.
As the demand for high-performance, compact, and reliable electronics continues to grow, embedded PCB assemblies will play an increasingly important role in shaping the future of the industry. By embracing this technology and its many benefits, manufacturers can position themselves at the forefront of innovation and deliver the next generation of electronics devices.
0 Comments