Understanding the Basics of PCB Manufacturing
Before diving into the tips, let’s briefly review the fundamental steps involved in PCB manufacturing:
- Design: Creating the PCB layout using specialized software
- Fabrication: Manufacturing the bare PCB
- Assembly: Populating the PCB with electronic components
- Testing and Inspection: Ensuring the PCB meets quality standards and functions as intended
Key Considerations for PCB Design
Choosing the Right PCB Material
Selecting the appropriate PCB material is crucial for the performance and reliability of your final product. The most common PCB materials include:
Material | Characteristics |
---|---|
FR-4 | Cost-effective, suitable for most applications |
High Tg FR-4 | Higher heat resistance, ideal for high-temperature environments |
Polyimide | Flexible, high-temperature resistance, used in aerospace industry |
Aluminum | Excellent thermal conductivity, used for heat dissipation |
Consider the specific requirements of your application, such as temperature range, flexibility, and thermal management, when choosing the PCB material.
Optimizing PCB Layer Stack-up
Proper layer stack-up design is essential for signal integrity, power distribution, and manufacturability. Here are some tips for optimizing your PCB layer stack-up:
- Use dedicated power and ground planes to minimize noise and improve power distribution
- Alternate signal layers with ground planes to reduce crosstalk and improve signal integrity
- Use symmetrical stack-ups to minimize warping and improve manufacturability
- Consider the dielectric constant and thickness of the insulating layers to control impedance
Implementing DFM Guidelines
Design for Manufacturability (DFM) is a set of guidelines that help ensure your PCB design is manufacturable, reliable, and cost-effective. Some key DFM considerations include:
- Maintaining minimum trace width and spacing based on the PCB fabrication capabilities
- Avoiding acute angles in traces to prevent acid traps during etching
- Using vias strategically to minimize drilling costs and improve reliability
- Providing sufficient clearance between components for assembly and soldering
Fabrication and Assembly Best Practices
Choosing the Right PCB Fabrication Partner
Selecting a reliable and experienced PCB fabrication partner is crucial for ensuring high-quality PCBs. When evaluating potential partners, consider the following factors:
- Manufacturing capabilities, such as minimum feature sizes and layer count
- Quality control processes and certifications (e.g., ISO 9001, UL, RoHS)
- Lead times and pricing
- Customer support and communication
Implementing Lean Manufacturing Principles
Lean manufacturing is a methodology that focuses on minimizing waste and maximizing efficiency in the production process. Some key lean manufacturing principles that can be applied to PCB manufacturing include:
- Value Stream Mapping: Identifying and eliminating non-value-added activities in the manufacturing process
- 5S: Organizing the workspace for efficiency and reducing clutter
- Kaizen: Continuously improving processes through small, incremental changes
- Just-in-Time (JIT) Production: Producing goods only as they are needed to reduce inventory and minimize waste
Utilizing Automated Assembly Techniques
Automated assembly techniques, such as Surface Mount Technology (SMT) and Through-Hole Technology (THT), can significantly improve the speed, accuracy, and consistency of PCB assembly. Here’s a comparison of SMT and THT:
Aspect | SMT | THT |
---|---|---|
Component Placement | Components placed on the surface of the PCB | Components inserted through holes in the PCB |
Soldering Method | Reflow soldering | Wave soldering or hand soldering |
Component Density | Higher component density possible | Lower component density |
Assembly Speed | Faster assembly | Slower assembly |
Cost | Generally more cost-effective for high volume | More cost-effective for low volume |
Consider the specific requirements of your product, such as component types, production volume, and cost constraints, when choosing between SMT and THT assembly techniques.
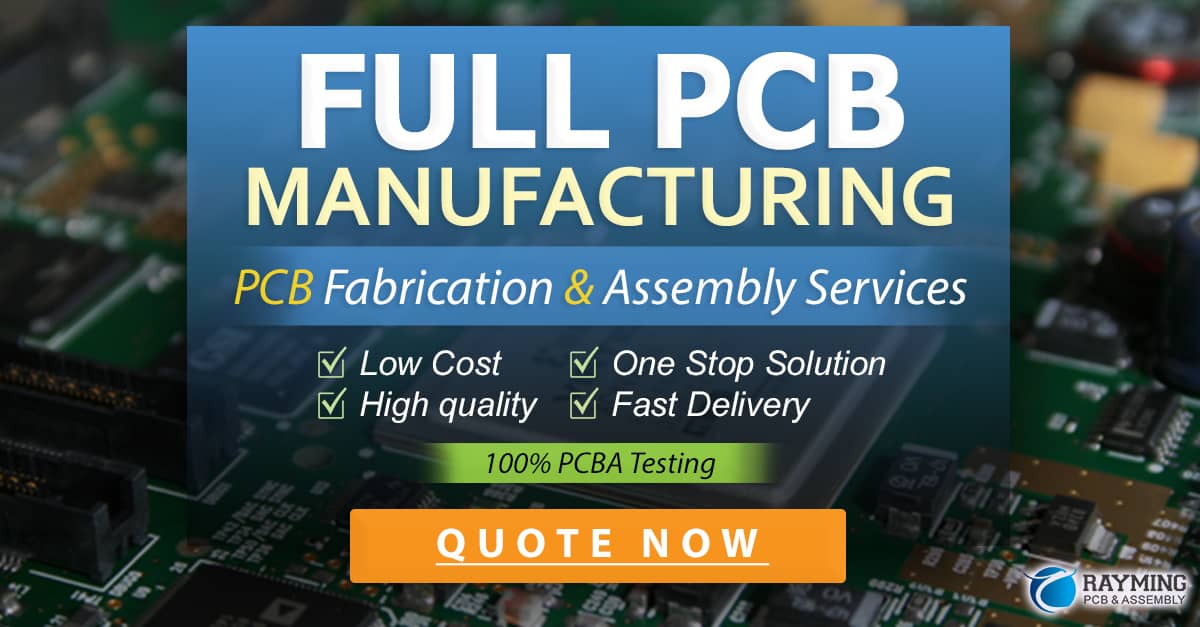
Testing and Quality Control
Implementing In-Circuit Testing (ICT)
In-Circuit Testing (ICT) is a technique used to verify the functionality of individual components on an assembled PCB. ICT involves using a bed-of-nails fixture to make electrical contact with test points on the PCB, allowing for the testing of:
- Component presence and orientation
- Component value and tolerance
- Short circuits and open circuits
- Basic functionality of analog and digital components
Implementing ICT can help identify defects early in the manufacturing process, reducing rework costs and improving overall quality.
Utilizing Automated Optical Inspection (AOI)
Automated Optical Inspection (AOI) is a technique that uses high-resolution cameras and image processing algorithms to inspect assembled PCBs for defects. AOI can detect:
- Missing or misaligned components
- Solder joint defects (e.g., bridging, insufficient solder)
- Damaged or incorrect components
- Incorrect component polarity
AOI is a fast and reliable method for identifying defects that may be difficult to detect through manual inspection, ensuring higher quality PCBs.
Conducting Functional Testing
Functional testing involves verifying that the assembled PCB performs as intended in its final application. This can include:
- Power-on testing to ensure proper power supply and distribution
- Signal integrity testing to verify proper communication between components
- Environmental testing to ensure the PCB can withstand the intended operating conditions (e.g., temperature, humidity, vibration)
- Boundary scan testing (JTAG) to test the interconnections between components
Conducting thorough functional testing helps ensure that the PCB will perform reliably in its end-use application.
Continuous Improvement and Industry 4.0
Implementing Statistical Process Control (SPC)
Statistical Process Control (SPC) is a method for monitoring and controlling the manufacturing process using statistical methods. SPC involves:
- Collecting data on key process parameters (e.g., solder paste thickness, component placement accuracy)
- Analyzing the data to identify trends and variations
- Implementing corrective actions to keep the process within acceptable limits
By implementing SPC, you can reduce process variation, improve product quality, and minimize waste.
Leveraging Industry 4.0 Technologies
Industry 4.0 refers to the ongoing automation and data exchange trend in manufacturing technologies. Some key Industry 4.0 technologies that can be leveraged in PCB manufacturing include:
- Internet of Things (IoT): Using sensors and connected devices to monitor and control the manufacturing process in real-time
- Big Data Analytics: Analyzing large volumes of data generated by the manufacturing process to identify trends, optimize processes, and predict maintenance needs
- Artificial Intelligence (AI) and Machine Learning (ML): Using AI and ML algorithms to automate decision-making, improve process efficiency, and detect defects
- Robotics and Automation: Implementing robots and automated systems to improve accuracy, speed, and consistency in PCB assembly
By embracing Industry 4.0 technologies, you can future-proof your PCB manufacturing process and stay competitive in an increasingly digital landscape.
FAQ
1. What is the difference between PCB fabrication and PCB assembly?
PCB fabrication refers to the process of manufacturing the bare PCB, while PCB assembly involves populating the fabricated PCB with electronic components.
2. What are the most common PCB materials, and how do I choose the right one for my application?
The most common PCB materials are FR-4, High Tg FR-4, Polyimide, and Aluminum. The choice of material depends on factors such as the intended operating temperature range, flexibility requirements, and thermal management needs of your application.
3. What is Design for Manufacturability (DFM), and why is it important?
Design for Manufacturability (DFM) is a set of guidelines that help ensure your PCB design is manufacturable, reliable, and cost-effective. Implementing DFM principles can minimize production issues, reduce costs, and improve the overall quality of your PCBs.
4. What are the key differences between Surface Mount Technology (SMT) and Through-Hole Technology (THT) in PCB assembly?
SMT involves placing components on the surface of the PCB and soldering them using reflow soldering, while THT involves inserting components through holes in the PCB and soldering them using wave soldering or hand soldering. SMT allows for higher component density and faster assembly, while THT is more cost-effective for low-volume production.
5. How can Industry 4.0 technologies benefit PCB manufacturing?
Industry 4.0 technologies, such as IoT, Big Data Analytics, AI, and Robotics, can help PCB manufacturers monitor and control their processes in real-time, optimize efficiency, predict maintenance needs, and improve overall product quality. By embracing these technologies, PCB manufacturers can stay competitive in an increasingly digital landscape.
By implementing the tips and best practices outlined in this article, OEM PCB manufacturers can optimize their production processes, ensure high-quality products, and stay ahead of the competition in an ever-evolving industry.
0 Comments