Introduction to Box Build Assembly
Box build assembly is a crucial process in the manufacturing of electronic devices. It involves the integration of various components, such as printed circuit boards (PCBs), wiring, connectors, and enclosures, into a complete functional unit. The success of a box build assembly project depends on several factors, including design, component selection, assembly techniques, testing, and quality control.
In this article, we will discuss the top 5 things to consider when planning and executing a box build assembly process. By understanding these key considerations, manufacturers can optimize their assembly processes, reduce costs, and improve product quality.
1. Design for Manufacturing (DFM)
What is Design for Manufacturing?
Design for Manufacturing (DFM) is an approach that focuses on creating product designs that are optimized for the manufacturing process. By considering the limitations and capabilities of the manufacturing process during the design phase, engineers can create designs that are easier, faster, and more cost-effective to produce.
Benefits of Implementing DFM
- Reduced manufacturing costs
- Improved product quality
- Faster time-to-market
- Enhanced reliability and durability
Key Elements of DFM in Box Build Assembly
- Component Selection: Choose components that are readily available, cost-effective, and compatible with the manufacturing process.
- PCB Design: Design PCBs with appropriate trace widths, spacing, and component placement to facilitate easy assembly and minimize the risk of defects.
- Enclosure Design: Create enclosure designs that are easy to assemble, provide adequate protection for the components, and allow for efficient cable management.
- Assembly Techniques: Consider the assembly techniques that will be used, such as through-hole or surface-mount technology, and design the product accordingly.
2. Component Selection and Procurement
Importance of Component Selection
Selecting the right components is critical to the success of a box build assembly project. The choice of components can impact the functionality, reliability, and cost of the final product. Here are some factors to consider when selecting components:
- Functionality: Ensure that the selected components meet the functional requirements of the product.
- Quality: Choose components from reputable suppliers that meet industry standards and have a proven track record of quality.
- Cost: Consider the cost of the components and their impact on the overall project budget.
- Availability: Select components that are readily available and have stable supply chains to avoid delays in production.
Procurement Strategies
Once the components have been selected, it is essential to establish an effective procurement strategy. Here are some best practices for component procurement:
- Vendor Selection: Choose vendors that are reliable, offer competitive pricing, and provide good customer support.
- Inventory Management: Implement an inventory management system to ensure that components are available when needed and to minimize the risk of stockouts or excess inventory.
- Lead Time Management: Monitor lead times for critical components and adjust procurement schedules accordingly to avoid delays in production.
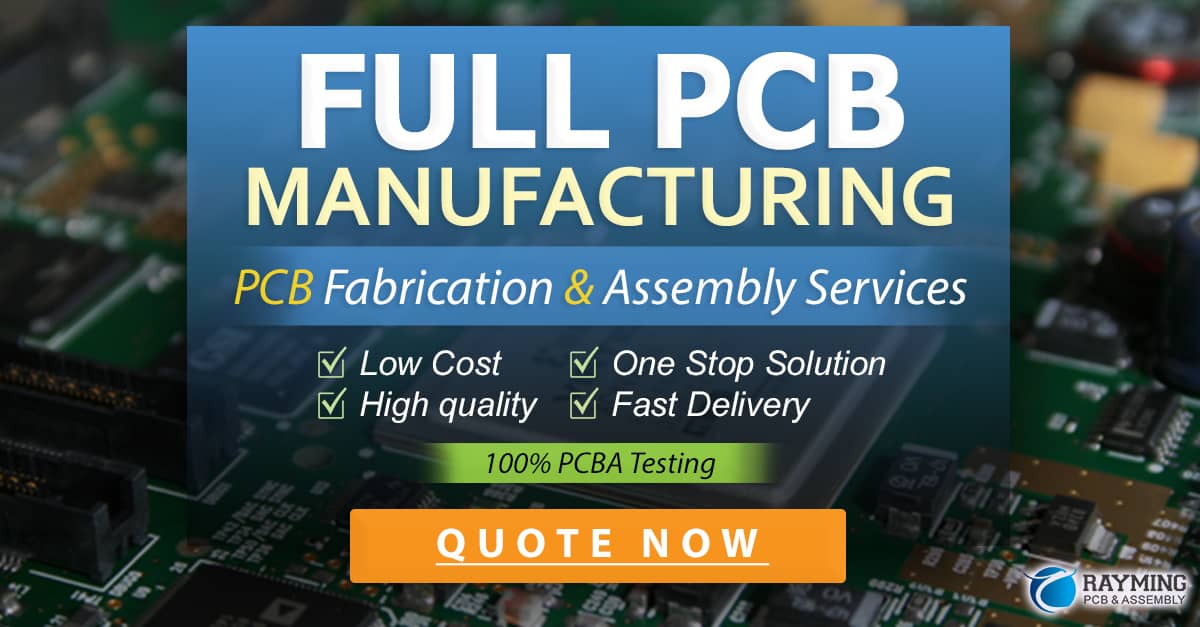
3. Assembly Techniques and Processes
Through-Hole vs. Surface-Mount Technology
There are two primary techniques used in box build assembly: through-hole and surface-mount technology (SMT).
Technique | Description | Advantages | Disadvantages |
---|---|---|---|
Through-hole | Components are inserted through holes in the PCB and soldered on the opposite side. | – Easy to assemble manually – Suitable for high-power applications – More durable connections |
– Larger PCB size – Slower assembly process – Higher cost compared to SMT |
Surface-mount | Components are placed directly on the surface of the PCB and soldered using reflow or wave soldering. | – Smaller PCB size – Faster assembly process – Lower cost compared to through-hole |
– Requires specialized equipment for assembly – More sensitive to thermal stress – Difficult to replace or repair components |
Manual vs. Automated Assembly
Box build assembly can be performed manually or using automated equipment. The choice between manual and automated assembly depends on several factors, such as production volume, product complexity, and available resources.
Assembly Method | Advantages | Disadvantages |
---|---|---|
Manual | – Lower initial investment – Flexibility to handle complex or custom assemblies – Suitable for low-volume production |
– Slower production rate – Higher labor costs – Potential for human error |
Automated | – Faster production rate – Consistent quality – Lower labor costs – Suitable for high-volume production |
– Higher initial investment – Limited flexibility for custom assemblies – Requires specialized programming and maintenance |
Process Optimization
To ensure efficient and cost-effective box build assembly, it is essential to optimize the assembly process. Here are some strategies for process optimization:
- Work Instructions: Develop clear and detailed work instructions to guide operators through the assembly process.
- Jigs and Fixtures: Use jigs and fixtures to ensure consistent and accurate assembly of components.
- Lean Manufacturing: Implement lean manufacturing principles, such as 5S and Kaizen, to eliminate waste and continuously improve the assembly process.
- Quality Control: Establish quality control measures, such as in-process inspections and functional testing, to identify and correct defects early in the assembly process.
4. Testing and Quality Control
Importance of Testing and Quality Control
Testing and quality control are critical aspects of the box build assembly process. They ensure that the final product meets the required specifications, functions as intended, and is free from defects. Effective testing and quality control can help to:
- Identify and correct defects early in the assembly process
- Improve product reliability and durability
- Reduce warranty claims and customer returns
- Enhance customer satisfaction and brand reputation
Types of Testing
There are several types of testing that can be performed during the box build assembly process, including:
- In-Circuit Testing (ICT): Verifies the functionality of individual components and connections on the PCB.
- Functional Testing: Verifies that the assembled product meets the specified functional requirements.
- Burn-In Testing: Subjects the product to elevated temperatures and operating conditions to identify early-life failures.
- Environmental Testing: Verifies that the product can withstand the expected environmental conditions, such as temperature, humidity, and vibration.
Quality Control Measures
In addition to testing, there are several quality control measures that can be implemented to ensure the consistency and quality of the box build assembly process:
- Incoming Inspection: Verify the quality and conformance of incoming components and materials.
- In-Process Inspection: Monitor the assembly process at critical points to identify and correct defects.
- Final Inspection: Perform a comprehensive inspection of the finished product to ensure that it meets all specifications and requirements.
- Traceability: Maintain records of components, processes, and test results to enable traceability and root cause analysis in case of defects or failures.
5. Supply Chain Management
Importance of Supply Chain Management
Effective supply chain management is crucial for the success of a box build assembly project. It ensures that the right components and materials are available when needed, at the right price, and in the right quantities. Good supply chain management can help to:
- Reduce lead times and minimize the risk of stockouts
- Optimize inventory levels and reduce carrying costs
- Improve supplier relationships and negotiate better prices
- Enhance flexibility and responsiveness to changes in demand or product requirements
Key Elements of Supply Chain Management
- Demand Planning: Forecast the demand for the final product and translate it into component and material requirements.
- Supplier Selection: Choose suppliers that can provide the required components and materials at the right price, quality, and delivery terms.
- Inventory Management: Establish optimal inventory levels for components and materials based on lead times, demand variability, and production schedules.
- Logistics and Transportation: Coordinate the movement of components and materials from suppliers to the assembly facility, and the finished products to customers.
- Risk Management: Identify and mitigate potential risks in the supply chain, such as supplier failures, natural disasters, or geopolitical events.
Frequently Asked Questions (FAQ)
-
What is box build assembly?
Box build assembly is the process of integrating various components, such as PCBs, wiring, connectors, and enclosures, into a complete functional unit. -
What are the benefits of implementing Design for Manufacturing (DFM) in box build assembly?
The benefits of implementing DFM in box build assembly include reduced manufacturing costs, improved product quality, faster time-to-market, and enhanced reliability and durability. -
What are the primary techniques used in box build assembly?
The two primary techniques used in box build assembly are through-hole and surface-mount technology (SMT). -
Why are testing and quality control important in box build assembly?
Testing and quality control are important in box build assembly because they ensure that the final product meets the required specifications, functions as intended, and is free from defects. They help to identify and correct defects early in the assembly process, improve product reliability and durability, reduce warranty claims and customer returns, and enhance customer satisfaction and brand reputation. -
What are the key elements of supply chain management in box build assembly?
The key elements of supply chain management in box build assembly include demand planning, supplier selection, inventory management, logistics and transportation, and risk management. Effective supply chain management ensures that the right components and materials are available when needed, at the right price, and in the right quantities, while minimizing risks and optimizing costs.
Conclusion
Box build assembly is a complex process that requires careful consideration of several factors, including design, component selection, assembly techniques, testing, and supply chain management. By understanding and addressing these key considerations, manufacturers can optimize their assembly processes, reduce costs, and improve product quality.
Implementing Design for Manufacturing (DFM) principles, selecting the right components and suppliers, choosing appropriate assembly techniques, establishing effective testing and quality control measures, and managing the supply chain effectively are all critical to the success of a box build assembly project.
By following the guidelines and best practices outlined in this article, manufacturers can streamline their box build assembly processes, enhance product reliability and durability, and ultimately deliver high-quality products to their customers.
0 Comments