Introduction to Finite Element Analysis (FEA) in PCB Design
Finite Element Analysis (FEA) is a powerful computational method used to analyze and optimize the design of various structures, including Printed Circuit Boards (PCBs). In the context of PCB manufacturing, FEA helps engineers and designers to predict the behavior of PCBs under different environmental conditions, such as temperature changes, mechanical stress, and vibrations. By using FEA, PCB designers can identify potential issues early in the design process, reducing the risk of costly redesigns and product failures.
What is Finite Element Analysis?
Finite Element Analysis is a numerical method that divides a complex structure into smaller, simpler parts called finite elements. These elements are connected at points called nodes, forming a mesh-like structure. The behavior of each element is described using mathematical equations, which are then solved simultaneously to determine the overall behavior of the structure under specific loading conditions.
Benefits of using FEA in PCB design
- Improved reliability: FEA helps identify potential weaknesses in the PCB design, allowing designers to make necessary changes before manufacturing.
- Cost reduction: By catching design issues early, FEA reduces the need for physical prototyping and redesigns, saving time and money.
- Enhanced performance: FEA enables designers to optimize PCB layouts for better thermal management, signal integrity, and mechanical stability.
- Faster time-to-market: With fewer design iterations and prototypes required, FEA accelerates the PCB development process, allowing faster product launches.
Common Types of FEA PCB Analysis
1. Thermal Analysis
Thermal analysis is one of the most critical aspects of PCB design, as it helps ensure that the board can dissipate heat effectively and maintain stable operation under various temperature conditions. FEA thermal analysis calculates the temperature distribution across the PCB, identifying hot spots and areas with poor heat dissipation.
Importance of thermal management in PCBs
- Prevents component overheating and failure
- Ensures reliable operation in different environmental conditions
- Prolongs the lifespan of the PCB and its components
- Maintains optimal performance and signal integrity
Factors affecting PCB thermal performance
- Component placement and density
- PCB material properties (thermal conductivity, specific heat, etc.)
- Copper trace width and thickness
- Presence of thermal vias and heat sinks
- Ambient temperature and airflow conditions
Example: Thermal FEA of a power amplifier PCB
In this example, a power amplifier PCB is analyzed using FEA to identify potential thermal issues. The analysis considers factors such as component power dissipation, PCB material properties, and ambient temperature.
Component | Power Dissipation (W) |
---|---|
Transistor Q1 | 5 |
Transistor Q2 | 3 |
Resistor R1 | 1 |
Resistor R2 | 0.5 |
The FEA results show the temperature distribution across the PCB, highlighting areas with high temperatures that may require additional cooling or design modifications.
2. Mechanical Stress Analysis
Mechanical stress analysis evaluates the PCB’s ability to withstand various mechanical loads, such as vibrations, shocks, and bending. This type of analysis is particularly important for PCBs used in harsh environments or applications with high reliability requirements, such as automotive, aerospace, and military electronics.
Common mechanical loads on PCBs
- Vibrations from motors, fans, or transportation
- Shocks from drops or impacts
- Bending and twisting during handling or installation
- Thermal expansion and contraction due to temperature changes
Factors affecting PCB mechanical performance
- PCB material properties (Young’s modulus, Poisson’s ratio, etc.)
- Thickness and number of PCB layers
- Copper trace and via layout
- Component placement and mounting methods
- Presence of mechanical reinforcements or stiffeners
Example: Mechanical stress FEA of an automotive ECU PCB
In this example, an automotive Engine Control Unit (ECU) PCB is analyzed using FEA to determine its ability to withstand vibrations and thermal cycling. The analysis considers factors such as PCB material properties, component mass, and vibration frequency.
Parameter | Value |
---|---|
PCB material | FR-4 |
PCB thickness | 1.6 mm |
Number of layers | 6 |
Vibration frequency | 50 Hz |
Vibration amplitude | 2 g |
The FEA results show the stress distribution across the PCB, identifying areas with high stress concentrations that may require design modifications or additional mechanical support.
3. Signal Integrity Analysis
Signal integrity analysis examines the quality of electrical signals transmitted through the PCB, ensuring that they maintain their intended characteristics and timing. This type of analysis is crucial for high-speed digital designs, where signal distortion, crosstalk, and electromagnetic interference (EMI) can lead to system malfunctions and failures.
Factors affecting PCB signal integrity
- Trace geometry (width, thickness, spacing)
- Dielectric material properties
- Impedance matching and termination
- Via and connector placement
- Clock and data rates
- Presence of ground and power planes
Common signal integrity issues
- Reflections due to impedance mismatches
- Crosstalk between adjacent traces
- EMI from high-frequency signals
- Signal attenuation and distortion
- Timing skew and jitter
Example: Signal integrity FEA of a high-speed DDR4 memory interface
In this example, a DDR4 memory interface on a PCB is analyzed using FEA to ensure proper signal integrity. The analysis considers factors such as trace geometry, dielectric properties, and termination schemes.
Parameter | Value |
---|---|
DDR4 data rate | 3200 MT/s |
Trace width | 0.1 mm |
Trace spacing | 0.15 mm |
Dielectric material | Rogers RO4350B |
Dielectric constant (Dk) | 3.48 |
Termination scheme | On-die termination (ODT) |
The FEA results show the signal waveforms and eye diagrams at the receiver, allowing designers to assess the signal quality and make necessary adjustments to the PCB layout or termination settings.
Implementing FEA in the PCB Design Workflow
To effectively incorporate FEA into the PCB design process, consider the following steps:
- Define the analysis goals and requirements based on the specific application and operating conditions.
- Create an accurate 3D model of the PCB, including components, traces, and vias.
- Assign material properties and boundary conditions to the model, such as thermal conductivity, mechanical constraints, and electrical characteristics.
- Generate a suitable mesh for the model, balancing accuracy and computational efficiency.
- Run the FEA simulation and analyze the results, identifying potential issues and areas for improvement.
- Iterate on the PCB design based on the FEA results, making necessary changes to optimize performance and reliability.
- Validate the final design through physical prototyping and testing.
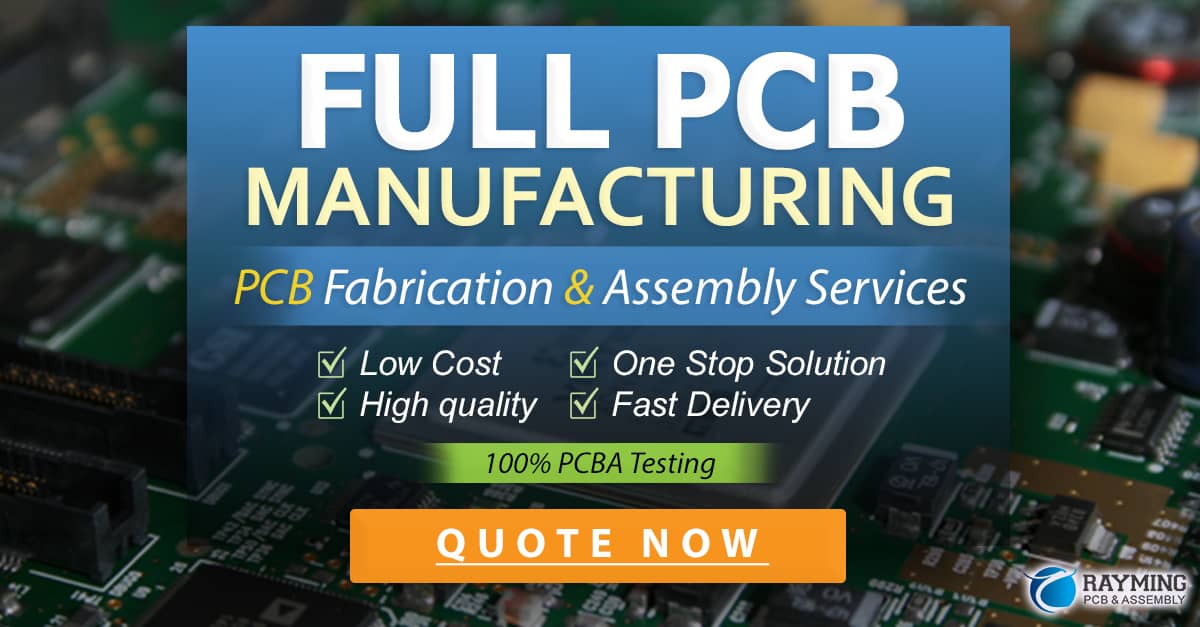
Frequently Asked Questions (FAQ)
1. What software tools are commonly used for FEA in PCB design?
Some popular FEA software tools for PCB design include:
– Ansys Mechanical
– Siemens Simcenter
– Altium Designer
– Autodesk Fusion 360
– SolidWorks Simulation
2. How accurate are FEA results compared to real-world PCB performance?
FEA results can be highly accurate when the model is properly set up with accurate material properties, boundary conditions, and mesh settings. However, it’s essential to validate FEA results through physical testing to account for factors that may not be fully captured in the simulation, such as manufacturing tolerances and environmental variations.
3. Can FEA completely replace physical prototyping and testing?
While FEA can significantly reduce the need for physical prototyping and testing, it cannot completely replace them. Physical testing is still necessary to validate the final design and ensure that it meets all performance and reliability requirements under real-world conditions.
4. How long does a typical FEA PCB simulation take to run?
The duration of an FEA PCB simulation depends on various factors, such as the complexity of the model, mesh density, and computational resources available. Simple analyses may take a few minutes, while more complex simulations can take several hours or even days.
5. Can FEA be used for both rigid and flexible PCBs?
Yes, FEA can be applied to both rigid and flexible PCBs. However, flexible PCBs may require additional considerations, such as modeling the bending behavior and using appropriate material models to capture the non-linear stress-strain relationships of the flexible substrate and components.
Conclusion
Finite Element Analysis is a valuable tool for PCB designers and manufacturers, enabling them to analyze and optimize the thermal, mechanical, and electrical performance of PCBs before physical prototyping and production. By leveraging FEA, engineers can identify and address potential issues early in the design process, reducing the risk of costly redesigns and product failures.
The three most common types of FEA PCB analysis are thermal analysis, mechanical stress analysis, and signal integrity analysis. Each type focuses on specific aspects of PCB performance and reliability, providing designers with valuable insights to make informed design decisions.
To successfully implement FEA in the PCB design workflow, it’s essential to define clear analysis goals, create accurate models, assign appropriate material properties and boundary conditions, and validate the results through physical testing. By incorporating FEA into the design process, PCB manufacturers can develop more reliable, high-performance products while reducing development time and costs.
0 Comments