What are RF PCBs?
RF printed circuit boards (PCBs) are specialized circuit boards designed to carry high-frequency signals with minimal loss and distortion. Unlike standard PCBs that operate at lower frequencies, RF PCBs require careful design considerations to maintain signal integrity and minimize electromagnetic interference (EMI) at radio frequencies, typically above 100 MHz.
RF PCBs find applications in various wireless communication devices, such as:
– Cell phones
– Wi-Fi routers
– Bluetooth devices
– GPS receivers
– Radar systems
– Satellite communication equipment
The key challenges in designing RF PCBs include impedance matching, signal isolation, and minimizing losses due to the skin effect and dielectric absorption at high frequencies.
RF PCB Materials
Substrates
The choice of substrate material is crucial for RF PCBs, as it directly impacts the board’s electrical properties and performance. The most common substrates used in RF PCBs are:
Substrate | Dielectric Constant (Dk) | Dissipation Factor (Df) | Applications |
---|---|---|---|
FR-4 | 4.3 – 4.6 | 0.02 – 0.03 | Low-cost, general-purpose RF PCBs |
Rogers RO4003C | 3.38 | 0.0027 | High-performance, low-loss RF PCBs |
Rogers RO4350B | 3.48 | 0.0037 | High-frequency, low-loss RF PCBs |
PTFE (Teflon) | 2.1 – 2.5 | 0.0002 – 0.0008 | Ultra-low-loss, high-frequency PCBs |
FR-4 is a cost-effective option for low-frequency RF applications, while Rogers and PTFE materials offer superior performance at higher frequencies due to their lower dielectric constant and dissipation factor.
Conductors
Copper is the most widely used conductor material in RF PCBs. The copper thickness and surface finish are essential factors in RF design.
Copper Thickness (oz) | Thickness (μm) | Applications |
---|---|---|
0.5 oz | 17.5 | Low-power, high-frequency RF circuits |
1 oz | 35 | General-purpose RF PCBs |
2 oz | 70 | High-power RF amplifiers and transmitters |
The skin effect causes high-frequency currents to flow primarily on the surface of conductors, making the surface finish important for RF performance. Common surface finishes include:
– Hot Air Solder Leveling (HASL)
– Immersion Silver (IAg)
– Electroless Nickel Immersion Gold (ENIG)
– Electroless Nickel Electroless Palladium Immersion Gold (ENEPIG)
RF PCB Design Considerations
Impedance Matching
Impedance matching is critical in RF PCB design to ensure maximum power transfer and minimize signal reflections. The characteristic impedance of transmission lines on the PCB must match the impedance of the connected devices, typically 50Ω or 75Ω.
To achieve the desired characteristic impedance, designers must consider factors such as:
– Substrate dielectric constant
– Substrate thickness
– Copper trace width and thickness
– Ground plane proximity
Online calculators and RF PCB design software can help determine the appropriate trace dimensions for a given substrate and target impedance.
Signal Integrity
Maintaining signal integrity is crucial in RF PCB design to minimize distortion, crosstalk, and EMI. Key techniques for improving signal integrity include:
-
Ground planes: Use uninterrupted ground planes to provide a low-impedance return path for high-frequency currents and shield signals from interference.
-
Via stitching: Place vias along the edges of ground planes to reduce fringing fields and improve shielding effectiveness.
-
Trace routing: Route RF traces as far away from each other as possible to minimize crosstalk. Use curved traces instead of 90-degree corners to reduce reflections.
-
Decoupling capacitors: Place decoupling capacitors close to active components to minimize power supply noise and improve high-frequency performance.
-
Shielding: Use shielding techniques, such as grounded copper pours or metal cans, to isolate sensitive RF circuits from external interference.
Component Placement
Proper component placement is essential for optimizing RF PCB performance. Guidelines for component placement include:
- Place RF components close to the board edge to minimize trace lengths and reduce losses.
- Orient components to minimize coupling and crosstalk.
- Group components by function and separate sensitive analog circuits from noisy digital circuits.
- Use surface-mount devices (SMDs) whenever possible to reduce parasitics and improve high-frequency performance.
Multilayer PCBs
Multilayer PCBs offer several advantages for RF designs, such as:
– Improved shielding and isolation between layers
– Reduced board size and component count
– Easier impedance control and trace routing
When designing multilayer RF PCBs, consider the following:
– Use dedicated signal and ground layers to minimize crosstalk and improve shielding.
– Ensure proper layer stacking to maintain signal integrity and minimize warpage.
– Use blind and buried vias to reduce board size and improve high-frequency performance.
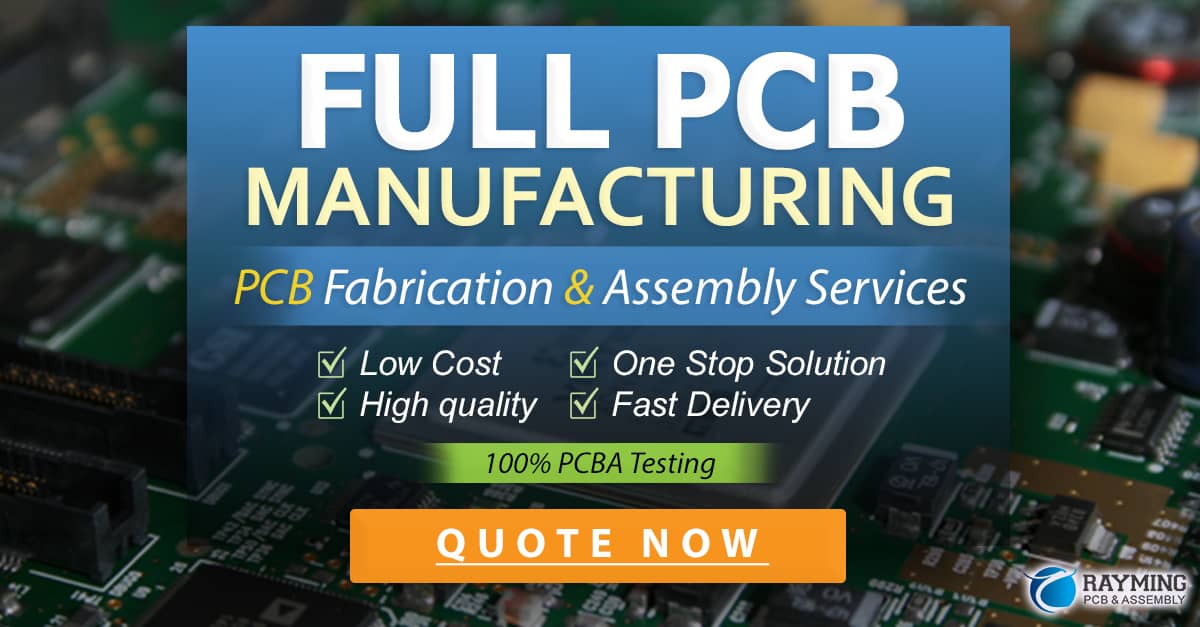
RF PCB Manufacturing and Assembly
Fabrication Process
RF PCBs require specialized fabrication processes to ensure high-quality and consistent performance. Key steps in the fabrication process include:
-
Material selection: Choose appropriate substrate and conductor materials based on the design requirements and target frequency range.
-
Lamination: Stack and laminate the substrate layers under high temperature and pressure to form a solid board.
-
Drilling: Drill through-holes and vias using high-precision CNC machines.
-
Plating: Apply copper plating to the drilled holes and vias to create electrical connections between layers.
-
Etching: Remove unwanted copper from the board surface using photolithography and chemical etching processes.
-
Solder mask and silkscreen: Apply solder mask and silkscreen layers to protect the board and improve assembly accuracy.
-
Surface finish: Apply the desired surface finish (e.g., HASL, ENIG) to protect the copper traces and improve solderability.
Assembly Techniques
Assembling RF PCBs requires special care to maintain signal integrity and minimize parasitics. Common assembly techniques for RF PCBs include:
-
Surface-mount technology (SMT): SMT is the preferred assembly method for RF PCBs due to its lower parasitics and higher component density compared to through-hole technology.
-
Reflow soldering: Reflow soldering is the most common method for attaching SMDs to RF PCBs. It involves applying solder paste to the pads, placing components, and passing the board through a reflow oven to melt the solder and form electrical connections.
-
Wave soldering: Wave soldering is used for through-hole components and involves passing the board over a molten solder wave to form electrical connections.
-
Selective soldering: Selective soldering is used for mixed-technology boards with both SMDs and through-hole components. It involves using a localized soldering iron or laser to solder specific components without affecting nearby SMDs.
Quality Control
Ensuring the quality of RF PCBs is critical for reliable performance in the final application. Quality control measures for RF PCBs include:
-
Visual inspection: Inspect the board for defects such as shorts, opens, and solder bridges using automated optical inspection (AOI) systems or manual inspection under magnification.
-
Electrical testing: Perform electrical tests, such as continuity, insulation resistance, and high-potential (hipot) tests, to verify the board’s electrical integrity.
-
RF testing: Conduct RF performance tests, such as S-parameter measurements and signal power measurements, to ensure the board meets the design specifications.
-
Environmental testing: Perform environmental tests, such as temperature cycling and humidity exposure, to validate the board’s reliability under various operating conditions.
Frequently Asked Questions (FAQ)
1. What is the difference between RF PCBs and standard PCBs?
RF PCBs are designed to handle high-frequency signals (typically above 100 MHz) with minimal loss and distortion, while standard PCBs are designed for lower-frequency applications. RF PCBs require special design considerations, such as impedance matching, signal integrity, and EMI reduction, to maintain signal quality at high frequencies.
2. What are the most common materials used for RF PCBs?
The most common substrate materials for RF PCBs are FR-4, Rogers RO4003C, Rogers RO4350B, and PTFE (Teflon). Copper is the most widely used conductor material, with various thicknesses and surface finishes available to suit different RF applications.
3. Why is impedance matching important in RF PCB design?
Impedance matching is critical in RF PCB design to ensure maximum power transfer and minimize signal reflections. Mismatched impedances can lead to signal degradation, reduced efficiency, and increased EMI. By matching the characteristic impedance of transmission lines on the PCB to the impedance of connected devices (typically 50Ω or 75Ω), designers can optimize RF performance.
4. How can I improve signal integrity in RF PCB designs?
To improve signal integrity in RF PCB designs, consider using uninterrupted ground planes, via stitching, proper trace routing, decoupling capacitors, and shielding techniques. These methods help minimize distortion, crosstalk, and EMI, ensuring high-quality signal transmission at high frequencies.
5. What are the advantages of using multilayer PCBs for RF designs?
Multilayer PCBs offer several advantages for RF designs, including improved shielding and isolation between layers, reduced board size and component count, and easier impedance control and trace routing. By using dedicated signal and ground layers, designers can minimize crosstalk and improve overall RF performance.
Conclusion
RF printed circuit boards are essential components in modern wireless communication devices, enabling high-frequency signal transmission with minimal loss and distortion. Designing and manufacturing RF PCBs requires careful consideration of materials, impedance matching, signal integrity, component placement, and assembly techniques.
By understanding the unique challenges and best practices associated with RF PCB design and fabrication, engineers can create high-performance, reliable RF circuits for a wide range of applications, from consumer electronics to advanced radar systems.
As wireless technologies continue to evolve and demand for high-speed, low-latency communication grows, the importance of RF PCBs will only increase. Staying up-to-date with the latest advancements in RF PCB materials, design tools, and manufacturing processes will be crucial for engineers and companies looking to stay competitive in the rapidly evolving world of wireless communications.
0 Comments