Introduction: The Vital Role of PCBs in Modern Industry
Printed Circuit Boards, or PCBs, are the unsung heroes powering the technological revolution across industries worldwide. These unassuming green boards packed with intricate copper pathways and electronic components form the backbone of countless electronic devices and systems. In the realm of industrial applications, PCBs have emerged as a catalyst for innovation, enabling the development of more efficient, compact, and intelligent solutions.
This article delves into the world of PCB Innovation, exploring how advancements in PCB design and manufacturing are transforming industrial applications. From enhancing reliability and performance to enabling the Internet of Things (IoT) and Industry 4.0, PCBs are at the forefront of driving industrial progress.
The Evolution of PCB Technology
Early Days: From Point-to-Point Wiring to Printed Circuits
The journey of PCBs began in the early 20th century when electronic devices relied on point-to-point wiring. This manual process involved connecting components using individual wires, resulting in bulky, unreliable, and difficult-to-manufacture devices. The advent of printed circuits in the 1940s revolutionized electronics manufacturing by allowing the etching of conductive pathways onto an insulating substrate.
The Rise of Multilayer PCBs
As electronic devices became more complex, the need for higher component density and improved signal integrity grew. Multilayer PCBs emerged as a solution, allowing designers to stack multiple layers of conductive pathways separated by insulating materials. This breakthrough enabled the creation of more compact and sophisticated devices while reducing electromagnetic interference (EMI) and improving signal quality.
Surface Mount Technology (SMT) and Miniaturization
The introduction of Surface Mount Technology (SMT) in the 1980s marked another significant milestone in PCB innovation. SMT allowed components to be mounted directly onto the surface of the PCB, eliminating the need for through-hole mounting. This advancement facilitated the miniaturization of electronic devices, as smaller components could be used, and the overall footprint of the PCB could be reduced.
PCB Innovations Driving Industrial Applications
High-Density Interconnect (HDI) PCBs
High-Density Interconnect (HDI) PCBs have become increasingly popular in industrial applications due to their ability to accommodate a large number of components in a small form factor. HDI PCBs feature finer trace widths, smaller vias, and higher layer counts compared to traditional PCBs. This allows for the development of more compact and powerful industrial devices, such as sensors, controllers, and communication modules.
Feature | Traditional PCB | HDI PCB |
---|---|---|
Trace Width | >100 μm | <100 μm |
Via Diameter | >200 μm | <150 μm |
Layer Count | <8 layers | >8 layers |
Flexible and Rigid-Flex PCBs
Flexible and Rigid-Flex PCBs have gained traction in industrial applications where space constraints, mobility, and reliability are critical factors. Flexible PCBs consist of a thin, flexible substrate that can bend and conform to various shapes, making them ideal for wearable devices, robotics, and applications requiring movement or flexibility.
Rigid-Flex PCBs combine the benefits of both rigid and flexible PCBs by integrating rigid and flexible sections into a single board. This hybrid approach allows for the creation of three-dimensional structures, enabling more compact and reliable designs in industrial applications such as automotive electronics, aerospace systems, and medical devices.
Thermal Management and High-Temperature PCBs
Industrial applications often involve harsh environments with extreme temperatures, making thermal management a crucial aspect of PCB design. Innovations in PCB materials and construction techniques have led to the development of high-temperature PCBs that can withstand temperatures up to 200°C or more. These PCBs utilize specialized substrates, such as polyimide or ceramic, and employ advanced thermal management techniques, including thermal vias, heat spreaders, and active cooling solutions.
Temperature Range | PCB Material |
---|---|
-55°C to 105°C | FR-4 |
-55°C to 125°C | High Tg FR-4 |
-55°C to 170°C | Polyimide |
-55°C to 200°C | Ceramic |
Embedded Components and 3D PCBs
Embedded component technology is revolutionizing PCB design by allowing components to be embedded within the layers of the PCB itself. This approach offers several advantages, including reduced board size, improved signal integrity, and enhanced reliability. By embedding components such as resistors, capacitors, and even active devices like ICs, designers can create highly integrated and compact industrial solutions.
3D PCBs take this concept further by stacking multiple PCBs vertically and interconnecting them using through-silicon vias (TSVs) or other vertical interconnect technologies. This three-dimensional approach enables the creation of highly dense and complex systems in a small form factor, making them ideal for space-constrained industrial applications.
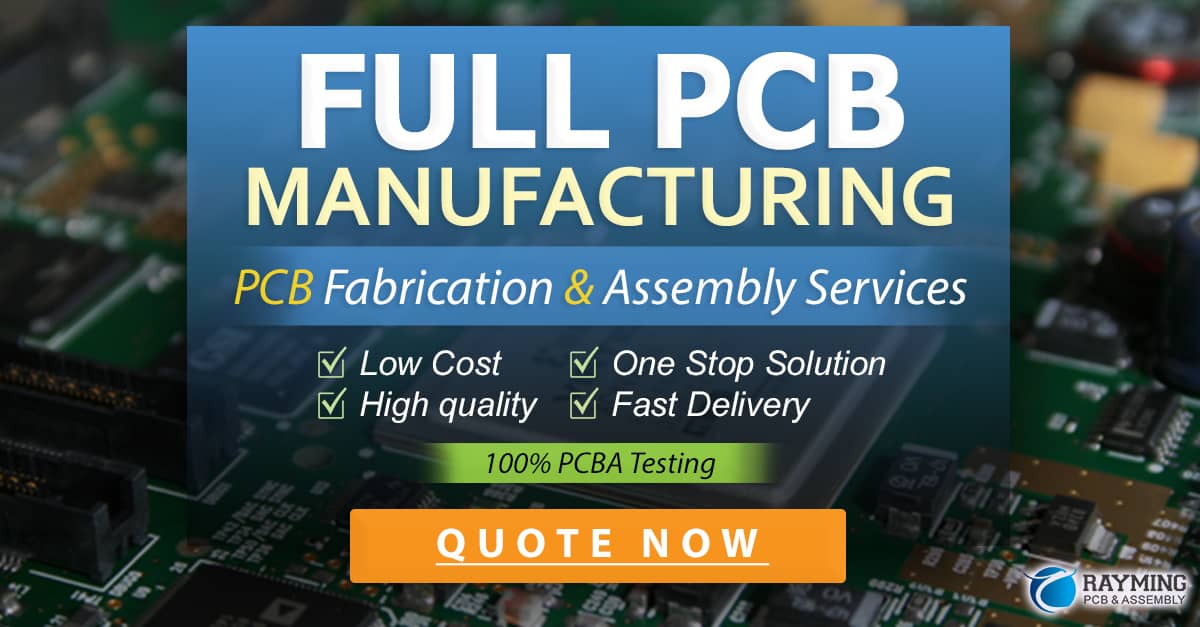
PCBs Enabling Industry 4.0 and the Internet of Things (IoT)
Smart Sensors and Edge Computing
PCBs play a crucial role in enabling the deployment of smart sensors and edge computing devices in industrial settings. These devices collect, process, and analyze data at the source, reducing latency and enabling real-time decision-making. PCB innovations, such as miniaturization, low-power design, and wireless connectivity, have made it possible to develop compact and energy-efficient sensors and edge computing modules that can be easily integrated into industrial systems.
Industrial IoT (IIoT) and Machine-to-Machine (M2M) Communication
The Industrial Internet of Things (IIoT) relies heavily on PCBs to enable seamless communication between machines, sensors, and control systems. PCBs equipped with wireless communication technologies, such as Wi-Fi, Bluetooth, LoRaWAN, and cellular (e.g., 5G), allow industrial devices to exchange data and interact with each other, facilitating machine-to-machine (M2M) communication. These connected systems enable remote monitoring, predictive maintenance, and optimization of industrial processes, leading to increased efficiency and productivity.
Cybersecurity and Secure PCB Design
As industrial systems become increasingly connected, cybersecurity becomes a paramount concern. PCB innovations are addressing this challenge by incorporating secure design practices and features. Secure PCBs may include tamper-evident coatings, embedded security chips, and hardware-based encryption to protect against unauthorized access, tampering, and data breaches. By prioritizing security at the PCB level, industrial organizations can enhance the overall security posture of their connected systems.
The Future of PCB Innovation in Industrial Applications
Advanced Materials and Nanotechnology
The future of PCB innovation lies in the exploration of advanced materials and nanotechnology. Researchers are investigating the use of graphene, carbon nanotubes, and other nanomaterials to develop PCBs with superior electrical, thermal, and mechanical properties. These materials have the potential to enable even smaller, faster, and more efficient industrial electronics.
Additive Manufacturing and 3D Printing
Additive manufacturing and 3D printing technologies are poised to disrupt traditional PCB manufacturing processes. These methods allow for the rapid prototyping and production of complex PCB structures, including those with embedded components and three-dimensional features. As these technologies mature, they will enable faster time-to-market, reduced waste, and greater design flexibility for industrial PCBs.
Artificial Intelligence (AI) and Machine Learning (ML) in PCB Design
The integration of Artificial Intelligence (AI) and Machine Learning (ML) in PCB design tools is expected to revolutionize the way industrial PCBs are developed. AI-powered design software can automatically optimize PCB layouts, component placement, and routing based on specified constraints and objectives. This will lead to more efficient and reliable designs, reduced development time, and lower costs for industrial PCB projects.
Frequently Asked Questions (FAQ)
-
Q: What are the key benefits of using HDI PCBs in industrial applications?
A: HDI PCBs offer several benefits for industrial applications, including higher component density, smaller form factors, improved signal integrity, and reduced electromagnetic interference (EMI). These advantages enable the development of more compact, reliable, and high-performance industrial devices. -
Q: How do flexible and rigid-flex PCBs differ from traditional rigid PCBs?
A: Flexible PCBs are made of a thin, flexible substrate that can bend and conform to various shapes, making them suitable for applications requiring movement or flexibility. Rigid-flex PCBs combine rigid and flexible sections into a single board, allowing for three-dimensional structures and more compact designs. Traditional rigid PCBs, on the other hand, are made of a rigid substrate and are best suited for applications where flexibility is not required. -
Q: What role do PCBs play in enabling the Industrial Internet of Things (IIoT)?
A: PCBs are essential for enabling the IIoT by providing the necessary connectivity, processing power, and sensor integration. PCBs equipped with wireless communication technologies allow industrial devices to exchange data and interact with each other, facilitating machine-to-machine (M2M) communication. Additionally, PCB innovations in miniaturization and low-power design enable the development of compact and energy-efficient sensors and edge computing devices that are crucial for IIoT deployments. -
Q: How can PCB design address cybersecurity concerns in connected industrial systems?
A: PCB design can address cybersecurity concerns by incorporating secure design practices and features. These may include tamper-evident coatings, embedded security chips, and hardware-based encryption to protect against unauthorized access, tampering, and data breaches. By prioritizing security at the PCB level, industrial organizations can enhance the overall security posture of their connected systems. -
Q: What are some emerging technologies that will shape the future of PCB innovation in industrial applications?
A: Several emerging technologies are expected to shape the future of PCB innovation in industrial applications. These include advanced materials and nanotechnology, which can enable the development of PCBs with superior electrical, thermal, and mechanical properties. Additive manufacturing and 3D printing technologies will allow for rapid prototyping and production of complex PCB structures. Additionally, the integration of Artificial Intelligence (AI) and Machine Learning (ML) in PCB design tools will lead to more efficient, reliable, and optimized industrial PCB designs.
Conclusion: Embracing PCB Innovation for Industrial Progress
PCB innovation is at the heart of driving progress in industrial applications. From enhancing reliability and performance to enabling the Internet of Things and Industry 4.0, PCBs are the foundation upon which modern industrial systems are built. As technologies continue to advance, PCB design and manufacturing will evolve to meet the ever-growing demands of industrial applications.
By embracing PCB innovations such as High-Density Interconnect (HDI), flexible and rigid-flex designs, thermal management, embedded components, and 3D structures, industrial organizations can unlock new possibilities for efficiency, functionality, and competitiveness. Furthermore, the integration of cybersecurity measures at the PCB level will be crucial in ensuring the security and integrity of connected industrial systems.
As we look to the future, the convergence of advanced materials, nanotechnology, additive manufacturing, and AI-powered design tools will shape the next generation of industrial PCBs. These innovations will enable the development of even smaller, smarter, and more efficient industrial devices, paving the way for a new era of industrial automation and progress.
In conclusion, PCB innovation is not just a trend but a necessity for industrial organizations seeking to stay ahead in an increasingly competitive and technology-driven landscape. By understanding and adopting the latest PCB advancements, industries can drive innovation, improve operational efficiency, and unlock new opportunities for growth and success.
0 Comments