Introduction to PCB Layout
Printed Circuit Board (PCB) layout is the process of arranging and connecting electronic components on a board to create a functional circuit. It involves both artistic and technical skills to design an efficient, reliable and manufacturable board. The PCB designer must consider many factors such as component placement, signal integrity, power distribution, thermal management, and manufacturability.
PCB layout is a critical step in the electronics design process. A well-designed PCB can make the difference between a product that works flawlessly and one that is plagued with issues. Poor PCB layout can lead to signal integrity problems, electromagnetic interference (EMI), thermal issues, and manufacturing defects. On the other hand, a good PCB layout can improve performance, reduce noise, and increase reliability.
The PCB Design Process
The PCB design process typically involves the following steps:
-
Schematic Capture: The first step is to create a schematic diagram of the circuit using EDA (Electronic Design Automation) software. The schematic shows the components and their interconnections.
-
Component Placement: Once the schematic is complete, the components are placed on the board in a way that minimizes the length of traces and reduces interference. The placement also takes into account the mechanical constraints of the enclosure.
-
Routing: After the components are placed, the traces are routed to connect them according to the schematic. The routing must follow the design rules specified by the PCB manufacturer.
-
Design Rule Check (DRC): The completed layout is checked against the design rules to ensure that it meets the manufacturability requirements. Any violations are fixed at this stage.
-
Gerber File Generation: Once the layout is finalized, Gerber files are generated for each layer of the board. These files are sent to the PCB manufacturer for fabrication.
PCB Layer Stack-up
A typical PCB consists of multiple layers of copper separated by insulating material. The number of layers depends on the complexity of the circuit and the routing requirements. Here is a table showing a typical 4-layer PCB stack-up:
Layer | Material | Thickness (mil) |
---|---|---|
Top | Copper | 1.4 |
Prepreg | FR-4 (2 sheets) | 8 |
Inner 1 | Copper | 1.0 |
Core | FR-4 | 40 |
Inner 2 | Copper | 1.0 |
Prepreg | FR-4 (2 sheets) | 8 |
Bottom | Copper | 1.4 |
The copper layers are used for routing traces and planes. The inner layers are typically used for power and ground planes, while the outer layers are used for signal traces. The prepreg and core layers provide insulation between the copper layers.
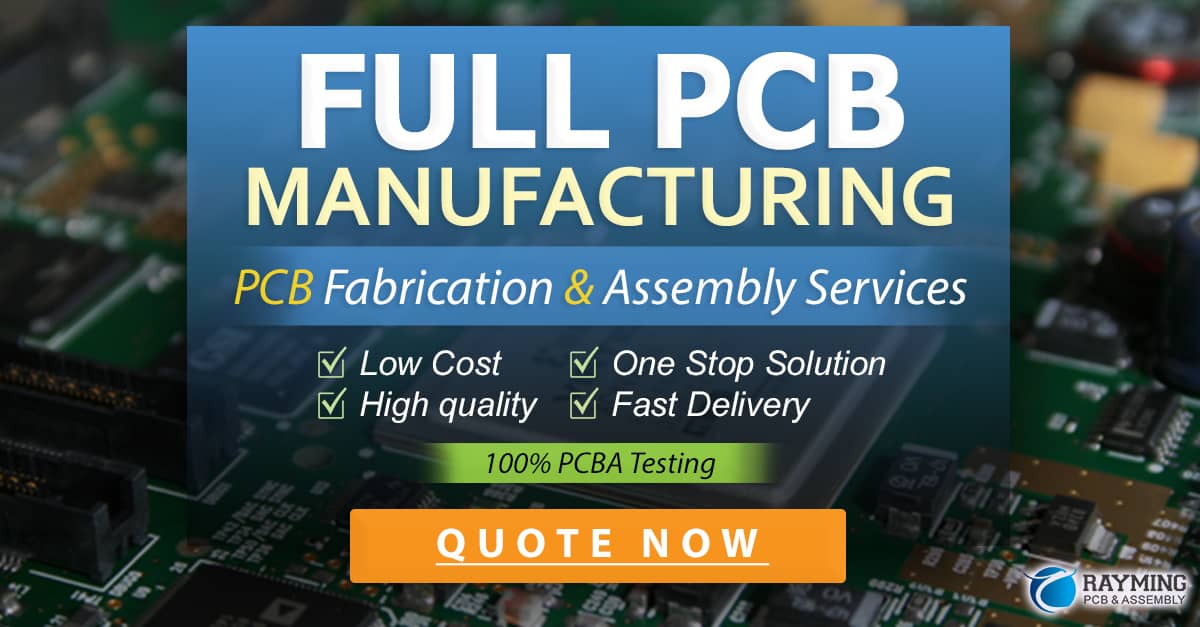
Component Placement Guidelines
Proper component placement is crucial for a successful PCB layout. Here are some guidelines to follow:
-
Group related components together: Components that are part of the same functional block should be placed close to each other to minimize trace lengths and improve signal integrity.
-
Place decoupling capacitors close to ICs: Decoupling capacitors should be placed as close as possible to the power pins of ICs to reduce noise and improve power delivery.
-
Avoid placing components under connectors: Components placed under connectors can be difficult to assembly and rework. They also make it harder to debug the board.
-
Consider the mechanical constraints: The placement of components must take into account the mechanical constraints of the enclosure such as mounting holes, connectors, and heat sinks.
-
Use symmetry and alignment: Symmetrical and aligned placement of components makes the board easier to assemble and looks more professional.
Routing Guidelines
Routing is the process of creating the copper traces that connect the components on the PCB. Here are some guidelines for routing:
-
Keep traces as short as possible: Long traces can cause signal integrity issues and increase EMI. Try to minimize the length of traces by placing components close together and using direct paths.
-
Use appropriate trace widths: The width of the trace depends on the current it carries and the impedance requirements. Thicker traces can handle more current but may be harder to route. Thinner traces are easier to route but may have higher resistance.
-
Avoid sharp angles: Sharp angles in traces can cause signal reflections and EMI. Use 45-degree angles instead of 90-degree angles.
-
Keep sensitive signals away from noise sources: Sensitive signals such as clocks and analog signals should be routed away from noisy sources such as power traces and high-speed digital signals.
-
Use ground planes: Ground planes provide a low-impedance return path for signals and help reduce EMI. They also serve as a shield between layers.
-
Follow the manufacturer’s design rules: Each PCB manufacturer has their own set of design rules that specify the minimum trace widths, spacing, and hole sizes. Following these rules ensures that the board can be manufactured reliably.
Power Distribution Network (PDN)
The power distribution network (PDN) is responsible for delivering clean and stable power to all the components on the board. A poorly designed PDN can cause voltage drops, noise, and EMI issues. Here are some tips for designing a robust PDN:
-
Use wide traces for power: Power traces should be as wide as possible to reduce resistance and inductance. The width depends on the maximum current draw of the circuit.
-
Use multiple power and ground planes: Using dedicated power and ground planes provides a low-impedance path for current and helps reduce noise.
-
Place decoupling capacitors close to ICs: Decoupling capacitors help to filter out high-frequency noise and provide a local reservoir of charge for ICs. They should be placed as close as possible to the power pins of the ICs.
-
Use a star topology for power distribution: A star topology minimizes the voltage drop and ensures that each component receives a clean power supply.
-
Consider the current return path: The current return path should be as short as possible to minimize loop inductance. Use ground planes and keep signal traces close to their return path.
EMI and EMC Considerations
Electromagnetic interference (EMI) and electromagnetic compatibility (EMC) are important considerations in PCB layout. EMI can cause glitches, data corruption, and system failures. Here are some tips for reducing EMI:
-
Use shielding: Shielding sensitive components and traces with ground planes or conductive enclosures can help reduce EMI.
-
Keep high-speed signals away from the edge of the board: High-speed signals near the edge of the board can radiate EMI. Keep them at least 1/20th of a wavelength away from the edge.
-
Use differential signaling: Differential signaling cancels out the magnetic fields and reduces EMI. It also provides better noise immunity than single-ended signaling.
-
Terminate unused pins: Unused pins on ICs can act as antennas and pick up noise. Terminate them to ground or VCC with a resistor.
-
Follow EMC standards: Follow the relevant EMC standards for your product such as FCC Part 15, EN 55022, or CISPR 22. These standards specify the limits for radiated and conducted emissions.
Thermal Management
Thermal management is the process of dissipating heat generated by components on the PCB. Overheating can cause components to fail prematurely or even catch fire. Here are some tips for thermal management:
-
Use a larger copper area for power components: Components that generate a lot of heat such as voltage regulators and power transistors should have a larger copper area to dissipate heat.
-
Place hot components away from sensitive components: Hot components should be placed away from sensitive components such as oscillators and sensors to avoid thermal coupling.
-
Use thermal vias: Thermal vias are plated through-holes that transfer heat from the component to the other side of the board. They help to spread the heat and reduce thermal resistance.
-
Consider using a heat sink: For components that generate a lot of heat, a heat sink may be necessary to dissipate the heat. The heat sink should be placed close to the component and have a low thermal resistance.
-
Use a temperature sensor: A temperature sensor can be used to monitor the temperature of critical components and trigger a shutdown if the temperature exceeds a safe limit.
Manufacturability
PCB manufacturability refers to the ease with which a board can be fabricated and assembled. A board that is difficult to manufacture can lead to higher costs, longer lead times, and lower reliability. Here are some tips for improving manufacturability:
-
Follow the manufacturer’s design rules: Each PCB manufacturer has their own set of design rules that specify the minimum trace widths, spacing, and hole sizes. Following these rules ensures that the board can be manufactured reliably.
-
Use standard sizes and shapes: Using standard sizes and shapes for the board and components makes it easier for the manufacturer to fabricate and assemble the board.
-
Avoid using too many layers: Using too many layers can increase the cost and complexity of the board. Use the minimum number of layers required for the design.
-
Provide clear labeling and markings: Providing clear labeling and markings on the board makes it easier for the assembler to place the components correctly.
-
Consider the assembly process: Consider the assembly process when placing components. Components should be placed in a way that minimizes the number of rotations and flips required during assembly.
FAQ
What is the difference between a schematic and a PCB layout?
A schematic is a diagram that shows the electrical connections between components using symbols. A PCB layout is a physical representation of the schematic that shows the actual placement and routing of components on a board.
What is the purpose of a ground plane?
A ground plane is a large area of copper on a PCB layer that is connected to the ground. It provides a low-impedance return path for signals and helps to reduce EMI. Ground planes also serve as a shield between layers and help to distribute heat.
What is the difference between a through-hole and a surface-mount component?
A through-hole component has leads that are inserted into holes drilled in the PCB and soldered on the opposite side. A surface-mount component is soldered directly onto pads on the surface of the PCB. Surface-mount components are smaller and cheaper than through-hole components but require more precise placement and soldering.
What is the purpose of a decoupling capacitor?
A decoupling capacitor is a capacitor placed close to an IC to filter out high-frequency noise on the power supply lines. It provides a local reservoir of charge for the IC and helps to stabilize the voltage. Decoupling capacitors are typically placed as close as possible to the power pins of the IC.
What is the difference between a two-layer and a four-layer PCB?
A two-layer PCB has copper layers on the top and bottom of the board, while a four-layer PCB has additional copper layers in the middle of the board. Four-layer PCBs are more expensive than two-layer PCBs but offer better signal integrity, power distribution, and EMI reduction. They are typically used for more complex designs with higher component densities.
Conclusion
PCB layout is a critical step in the electronics design process that requires both artistic and technical skills. A well-designed PCB can make the difference between a product that works flawlessly and one that is plagued with issues. By following best practices for component placement, routing, power distribution, EMI reduction, thermal management, and manufacturability, designers can create PCBs that are reliable, efficient, and cost-effective.
0 Comments