What is Manual Assembly?
Manual assembly refers to the process of assembling products or components by hand, using human labor. This method relies on skilled workers who use hand tools, jigs, and fixtures to put together various parts of a product. Manual assembly is often used for low-volume production, prototyping, or highly customized products that require a high degree of flexibility and adaptability.
Advantages of Manual Assembly
-
Flexibility: Manual assembly allows for quick changes in product design or assembly processes, making it ideal for businesses that require frequent adjustments or customization.
-
Lower initial investment: Compared to automated assembly, manual assembly requires a lower upfront investment in equipment and infrastructure.
-
Skilled workforce: Manual assembly relies on the expertise and craftsmanship of skilled workers, which can result in high-quality products.
-
Adaptability: Human workers can easily adapt to changes in the assembly process or product design, making manual assembly suitable for products with high variability.
Disadvantages of Manual Assembly
-
Lower productivity: Manual assembly is generally slower than automated assembly, resulting in lower production rates.
-
Inconsistent quality: The quality of manually assembled products may vary due to human error or inconsistencies in the assembly process.
-
Higher labor costs: Manual assembly requires a larger workforce, which can lead to higher labor costs, especially in regions with high wage rates.
-
Ergonomic challenges: Repetitive tasks and manual handling of components can lead to ergonomic issues and potential injuries for workers.
What is Automated Assembly?
Automated assembly involves the use of machinery, robots, and other automated systems to assemble products or components. This method is suitable for high-volume production, where speed, consistency, and accuracy are critical factors. Automated assembly lines can be programmed to perform specific tasks, reducing the need for human intervention and minimizing the risk of errors.
Advantages of Automated Assembly
-
Higher productivity: Automated assembly lines can operate at much higher speeds than manual assembly, resulting in increased production rates.
-
Consistent quality: Automated systems ensure consistent product quality by minimizing human error and maintaining precise control over the assembly process.
-
Reduced labor costs: Automated assembly requires fewer workers, which can lead to significant savings in labor costs over time.
-
Improved safety: Automated systems can handle hazardous or repetitive tasks, reducing the risk of worker injuries and improving overall workplace safety.
Disadvantages of Automated Assembly
-
Higher initial investment: Implementing an automated assembly line requires a significant upfront investment in equipment, software, and infrastructure.
-
Limited flexibility: Automated systems are often designed for specific products or processes, making it more challenging to accommodate changes or customization.
-
Maintenance and downtime: Automated equipment requires regular maintenance and may experience downtime due to repairs or upgrades, which can impact production schedules.
-
Skilled technicians: Operating and maintaining automated assembly lines requires skilled technicians, which can be challenging to find and retain.
Factors to Consider When Choosing Between Manual and Automated Assembly
When deciding between manual and automated assembly for your business, consider the following factors:
-
Production volume: Automated assembly is generally more suitable for high-volume production, while manual assembly is better suited for low-volume or custom orders.
-
Product complexity: Simple products with fewer components may be more easily assembled using manual methods, while complex products with many parts may benefit from automated assembly.
-
Available resources: Consider your current workforce, their skills, and the availability of skilled technicians for operating and maintaining automated systems.
-
Budget: Evaluate your financial resources and the return on investment (ROI) for each assembly method. While automated assembly requires a higher initial investment, it may offer long-term cost savings through increased productivity and reduced labor costs.
-
Flexibility and adaptability: Assess your need for flexibility in product design and assembly processes. Manual assembly offers greater adaptability, while automated assembly is more suitable for stable, high-volume production.
-
Quality requirements: Consider the desired level of product quality and consistency. Automated assembly generally provides more consistent results, while manual assembly relies on the skill and expertise of workers.
-
Industry and market demand: Evaluate your industry’s standards and customer expectations. Some industries, such as automotive or electronics, may require the precision and speed of automated assembly to remain competitive.
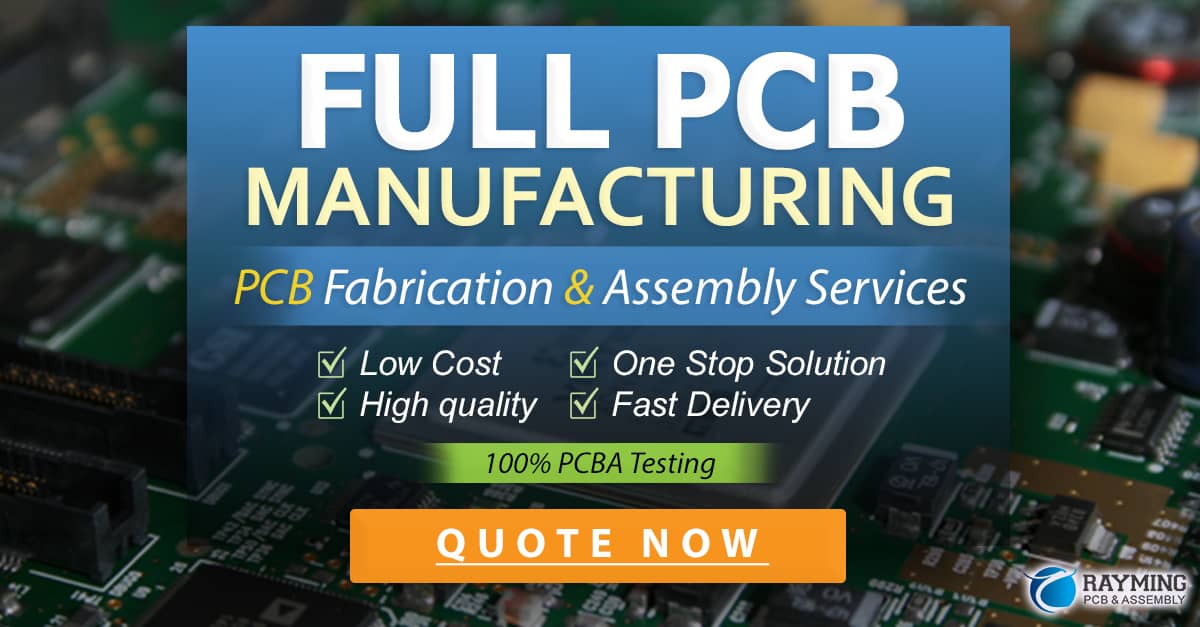
Comparison Table: Manual vs. Automated Assembly
Factor | Manual Assembly | Automated Assembly |
---|---|---|
Flexibility | High | Low |
Initial investment | Low | High |
Labor costs | High | Low |
Production volume | Low to medium | High |
Product complexity | Simple to complex | Medium to highly complex |
Quality consistency | Variable | High |
Adaptability | High | Low |
Maintenance requirements | Low | High |
Hybrid Approach: Combining Manual and Automated Assembly
In some cases, a hybrid approach that combines both manual and automated assembly methods may be the most effective solution. This approach allows businesses to leverage the benefits of both methods while minimizing their drawbacks. For example, a company may use automated assembly for high-volume, repetitive tasks while relying on manual assembly for more complex or customized components.
A hybrid approach can also help businesses gradually transition from manual to automated assembly as their production needs evolve. By starting with a partially automated assembly line and progressively adding more automated systems, companies can spread out their investment costs and allow their workforce to adapt to new technologies over time.
Frequently Asked Questions (FAQ)
-
Q: How do I determine the ROI for investing in automated assembly?
A: To calculate the ROI for automated assembly, consider factors such as the initial investment cost, expected increase in productivity, reduction in labor costs, and potential improvements in product quality. Compare these benefits to the ongoing costs of maintenance and training to determine the long-term financial viability of the investment. -
Q: Can manual assembly be used for high-volume production?
A: While manual assembly is generally better suited for low-volume production, it can be used for high-volume production in certain situations. This may require a larger workforce, streamlined processes, and efficient use of jigs and fixtures to minimize assembly time and maintain consistency. -
Q: How can I ensure consistent quality with manual assembly?
A: To ensure consistent quality with manual assembly, invest in employee training, develop clear work instructions and quality control procedures, and implement regular quality audits. Encourage open communication and continuous improvement among your workforce to identify and address any issues that may affect product quality. -
Q: What are the main challenges in implementing automated assembly?
A: The main challenges in implementing automated assembly include the high initial investment cost, the need for skilled technicians to operate and maintain the equipment, and the potential for production downtime due to maintenance or repairs. Additionally, automated systems may have limited flexibility, making it more difficult to accommodate product changes or customization. -
Q: How can I train my workforce to adapt to automated assembly?
A: To help your workforce adapt to automated assembly, provide comprehensive training on the new equipment and processes. Encourage a culture of continuous learning and offer opportunities for employees to acquire new skills related to automation. Involve your workforce in the implementation process and seek their input to foster a sense of ownership and engagement.
Conclusion
Choosing between manual and automated assembly requires careful consideration of your business’s unique needs, resources, and goals. While manual assembly offers flexibility, adaptability, and lower initial costs, automated assembly provides higher productivity, consistent quality, and potential long-term cost savings. By evaluating factors such as production volume, product complexity, budget, and workforce skills, you can determine which method, or combination of methods, is best suited for your organization.
Ultimately, the decision to invest in manual or automated assembly should align with your overall business strategy and long-term objectives. By carefully weighing the advantages and disadvantages of each approach and considering a hybrid solution when appropriate, you can optimize your assembly processes, improve product quality, and enhance your competitiveness in today’s dynamic manufacturing landscape.
0 Comments