Optimize PCB Design for Manufacturing
One of the most critical factors in achieving high efficiency in PCB Assembly is the design of the board itself. By optimizing the PCB design for manufacturing (DFM), you can minimize the potential for errors, reduce assembly time, and improve overall quality. Here are some key considerations for DFM:
Use Standard Component Sizes and Footprints
Using standard component sizes and footprints can significantly simplify the assembly process and reduce the need for custom tooling. This approach also makes it easier to source components from multiple suppliers, reducing the risk of supply chain disruptions.
Minimize the Number of Unique Components
Reducing the number of unique components on a PCB can help streamline the assembly process and minimize the potential for errors. This can be achieved by using common components across multiple designs and consolidating similar functions onto a single component whenever possible.
Provide Adequate Spacing Between Components
Ensuring adequate spacing between components is essential for reliable soldering and minimizing the risk of short circuits. The following table provides general guidelines for component spacing based on the size of the component:
Component Size | Minimum Spacing |
---|---|
0201 | 0.2 mm |
0402 | 0.3 mm |
0603 | 0.4 mm |
0805 | 0.5 mm |
1206 | 0.6 mm |
Use Consistent and Clear Labeling
Clear and consistent labeling of components, pin 1 indicators, and polarity markers can help prevent assembly errors and improve overall efficiency. Use industry-standard labeling practices and ensure that all labels are easily readable and properly aligned.
Implement Lean Manufacturing Principles
Lean manufacturing is a methodology that focuses on minimizing waste and maximizing value in the production process. By implementing lean principles in PCB assembly, manufacturers can significantly enhance efficiency and reduce costs. Some key lean manufacturing techniques include:
Value Stream Mapping
Value stream mapping involves creating a visual representation of the entire production process, from raw materials to finished products. By identifying and eliminating non-value-added steps, manufacturers can streamline their processes and reduce lead times.
5S Workplace Organization
The 5S system is a lean manufacturing tool that focuses on creating a clean, organized, and efficient workplace. The five steps of 5S are:
- Sort (Seiri): Remove unnecessary items from the work area
- Set in Order (Seiton): Arrange necessary items in a logical and easily accessible manner
- Shine (Seiso): Clean and maintain the work area regularly
- Standardize (Seiketsu): Establish standards for maintaining the first three steps
- Sustain (Shitsuke): Ensure ongoing adherence to the 5S system
Kaizen Continuous Improvement
Kaizen is a philosophy of continuous improvement that involves all employees in identifying and implementing small, incremental changes to enhance efficiency and quality. By fostering a culture of continuous improvement, PCB manufacturers can consistently optimize their processes over time.
Invest in Automation and Advanced Technologies
Automation and advanced technologies play a crucial role in enhancing the efficiency of PCB assembly manufacturing. By investing in the right equipment and software, manufacturers can reduce manual labor, minimize errors, and improve overall productivity. Some key areas for investment include:
Surface Mount Technology (SMT) Equipment
SMT equipment, such as pick-and-place machines and reflow ovens, can significantly increase the speed and accuracy of component placement and soldering. Modern SMT equipment often includes features like vision systems, real-time monitoring, and automatic changeovers, further enhancing efficiency.
Automated Optical Inspection (AOI)
AOI systems use high-resolution cameras and advanced algorithms to inspect PCBs for defects, such as missing components, incorrect polarities, and solder joint issues. By catching defects early in the assembly process, AOI can help reduce rework and scrap, ultimately improving efficiency.
Manufacturing Execution Systems (MES)
MES software provides real-time visibility into the entire production process, enabling manufacturers to track work-in-progress, monitor equipment performance, and identify bottlenecks. By leveraging MES data, manufacturers can make informed decisions to optimize their processes and enhance overall efficiency.
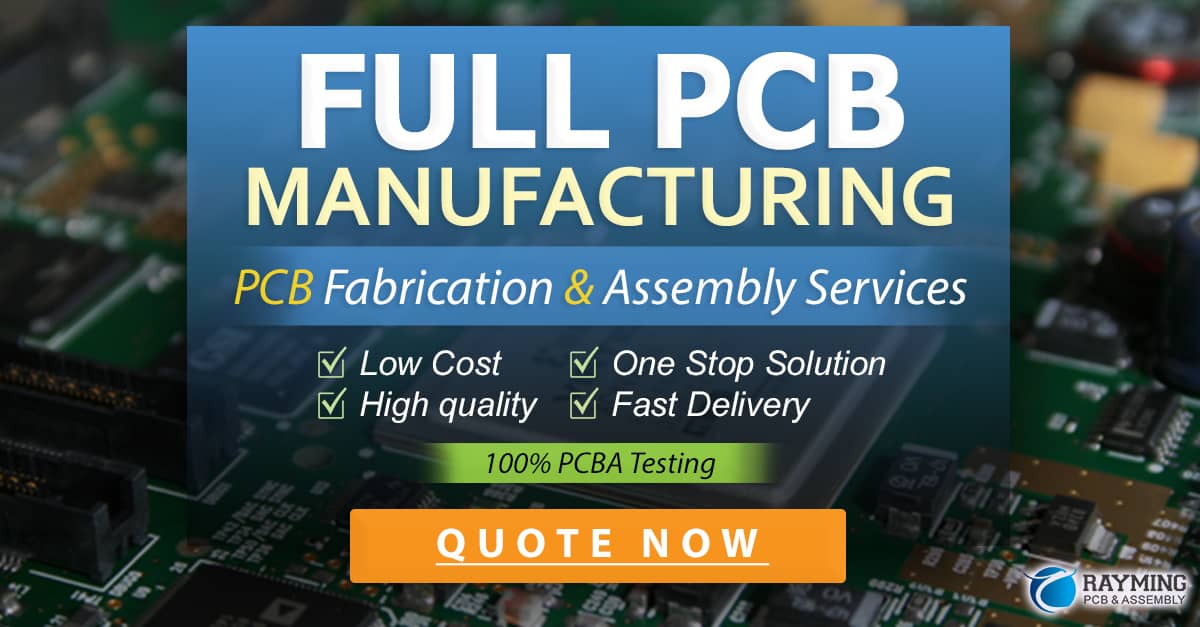
Foster a Culture of Continuous Learning and Development
Investing in the skills and knowledge of your workforce is essential for maintaining high levels of efficiency in PCB assembly manufacturing. By providing ongoing training and development opportunities, you can ensure that your employees have the expertise needed to adapt to new technologies, implement best practices, and drive continuous improvement. Some key areas for training and development include:
- PCB design and DFM principles
- SMT equipment operation and maintenance
- Quality control and inspection techniques
- Lean manufacturing and continuous improvement methodologies
- Soft skills, such as communication, teamwork, and problem-solving
Frequently Asked Questions (FAQ)
1. What is PCB assembly manufacturing?
PCB assembly manufacturing is the process of assembling electronic components onto a printed circuit board to create a functional electronic device. The process involves multiple steps, including component placement, soldering, and inspection.
2. Why is efficiency important in PCB assembly manufacturing?
Efficiency is crucial in PCB assembly manufacturing because it directly impacts production costs, lead times, and overall competitiveness. By optimizing processes for maximum efficiency, manufacturers can reduce waste, improve quality, and better meet customer demands.
3. What are some common challenges in achieving high efficiency in PCB assembly?
Common challenges in achieving high efficiency in PCB assembly include:
- Complex PCB designs with high component densities
- Frequent product changeovers and short production runs
- Inconsistent component quality and supply chain disruptions
- Limited automation and outdated equipment
- Insufficient employee training and high turnover rates
4. How can automation improve efficiency in PCB assembly manufacturing?
Automation can improve efficiency in PCB assembly manufacturing by:
- Increasing the speed and accuracy of component placement and soldering
- Reducing manual labor and minimizing the potential for human error
- Enabling real-time monitoring and data collection for process optimization
- Facilitating faster changeovers between different product types
- Improving overall quality and consistency of the assembled PCBs
5. What role does continuous improvement play in enhancing PCB assembly efficiency?
Continuous improvement is essential for enhancing PCB assembly efficiency because it enables manufacturers to consistently identify and address inefficiencies in their processes. By fostering a culture of continuous improvement and empowering employees to drive change, manufacturers can achieve incremental gains in efficiency over time, ultimately leading to significant improvements in productivity and competitiveness.
In conclusion, enhancing the efficiency of PCB assembly manufacturing requires a multi-faceted approach that encompasses PCB design optimization, lean manufacturing principles, investment in automation and advanced technologies, and a strong focus on employee training and development. By implementing these strategies and fostering a culture of continuous improvement, PCB manufacturers can streamline their processes, reduce costs, and improve overall competitiveness in an increasingly demanding market.
0 Comments