The Role of AI in PCB Design
One of the most significant applications of AI in the PCB manufacturing industry is in the design process. Traditionally, PCB design has been a time-consuming and labor-intensive task that requires skilled engineers to manually create complex layouts and schematics. However, with the advent of AI-powered design tools, this process has become much more efficient and streamlined.
AI-Assisted PCB Design Software
AI-assisted PCB design software uses machine learning algorithms to automate many of the tedious and repetitive tasks involved in PCB design. These tools can analyze vast amounts of data from previous designs and use this information to generate optimized layouts and schematics based on specific design requirements. Some of the key benefits of AI-assisted PCB design software include:
- Faster design times: AI-powered tools can generate optimized layouts and schematics in a fraction of the time it would take a human designer to do so manually.
- Improved accuracy: By leveraging vast amounts of data from previous designs, AI-assisted software can generate layouts that are more accurate and less prone to errors.
- Increased efficiency: AI-powered tools can automate many of the repetitive tasks involved in PCB design, freeing up engineers to focus on more complex and creative aspects of the design process.
AI-Assisted PCB Design Software | Benefits |
---|---|
Faster design times | AI-powered tools can generate optimized layouts and schematics in a fraction of the time it would take a human designer to do so manually. |
Improved accuracy | By leveraging vast amounts of data from previous designs, AI-assisted software can generate layouts that are more accurate and less prone to errors. |
Increased efficiency | AI-powered tools can automate many of the repetitive tasks involved in PCB design, freeing up engineers to focus on more complex and creative aspects of the design process. |
Generative Design
Another exciting application of AI in PCB design is generative design. Generative design is a process where AI algorithms are used to generate multiple design options based on specific performance criteria and constraints. This approach allows engineers to explore a wider range of design possibilities and identify the most optimal solution for a given application.
Generative design in PCB manufacturing involves feeding the AI system with a set of design parameters, such as the desired size, shape, and functionality of the PCB. The AI algorithm then generates a large number of potential designs that meet these criteria, allowing engineers to select the most suitable option for their specific needs.
Some of the key benefits of generative design in PCB manufacturing include:
- Improved performance: By exploring a wider range of design possibilities, generative design can help engineers identify the most optimal solution for a given application, resulting in improved performance and functionality.
- Reduced design time: Generative design can significantly reduce the time required to develop new PCB designs, as the AI algorithm can generate multiple options in a fraction of the time it would take a human designer to do so manually.
- Cost savings: By identifying the most optimal design solution, generative design can help reduce material costs and improve manufacturing efficiency, leading to significant cost savings.
AI in PCB Manufacturing Processes
In addition to revolutionizing PCB design, AI is also playing an increasingly important role in the manufacturing process itself. From automated optical inspection (AOI) to predictive maintenance, AI is helping PCB manufacturers improve quality control, reduce downtime, and increase overall efficiency.
Automated Optical Inspection (AOI)
Automated optical inspection (AOI) is a process where high-resolution cameras and computer vision algorithms are used to detect defects and anomalies in PCBs during the manufacturing process. Traditional AOI systems rely on pre-programmed rules and thresholds to identify defects, which can be time-consuming and prone to errors.
However, with the integration of AI and machine learning, AOI systems are becoming more intelligent and adaptive. AI-powered AOI systems can learn from vast amounts of data collected during the inspection process and continuously improve their defect detection capabilities over time. This not only improves the accuracy and reliability of the inspection process but also reduces the need for manual intervention and rework.
Traditional AOI Systems | AI-Powered AOI Systems |
---|---|
Rely on pre-programmed rules and thresholds | Learn from vast amounts of data collected during the inspection process |
Time-consuming and prone to errors | Continuously improve defect detection capabilities over time |
Require manual intervention and rework | Reduce the need for manual intervention and rework |
Predictive Maintenance
Predictive maintenance is another area where AI is making a significant impact in the PCB manufacturing industry. Predictive maintenance involves using machine learning algorithms to analyze sensor data from manufacturing equipment and predict when maintenance or repairs will be required.
By continuously monitoring equipment performance and identifying potential issues before they occur, predictive maintenance can help PCB manufacturers reduce unplanned downtime, improve equipment reliability, and extend the overall lifespan of their assets. This not only improves operational efficiency but also helps reduce maintenance costs and increase overall profitability.
Some of the key benefits of predictive maintenance in PCB manufacturing include:
- Reduced downtime: By identifying potential issues before they occur, predictive maintenance can help reduce unplanned downtime and minimize disruptions to the manufacturing process.
- Improved equipment reliability: Predictive maintenance helps ensure that manufacturing equipment is operating at optimal performance levels, reducing the risk of failures and defects.
- Extended asset lifespan: By proactively addressing potential issues, predictive maintenance can help extend the overall lifespan of manufacturing assets, reducing the need for costly replacements.
AI in Quality Control and Testing
Quality control and testing are critical aspects of the PCB manufacturing process, as they help ensure that the final product meets the required specifications and performance standards. AI is playing an increasingly important role in this area, helping manufacturers automate and streamline their quality control and testing processes.
Automated Testing
Automated testing is a process where AI algorithms are used to analyze test data and identify defects or anomalies in PCBs. Traditional automated testing systems rely on pre-programmed rules and thresholds to determine whether a PCB passes or fails a particular test. However, with the integration of AI and machine learning, automated testing systems are becoming more intelligent and adaptive.
AI-powered automated testing systems can learn from vast amounts of test data and continuously improve their defect detection capabilities over time. This not only improves the accuracy and reliability of the testing process but also reduces the need for manual intervention and rework.
Some of the key benefits of AI-powered automated testing in PCB manufacturing include:
- Improved accuracy: AI algorithms can analyze vast amounts of test data and identify defects or anomalies that may be missed by traditional testing methods.
- Increased efficiency: Automated testing can significantly reduce the time and resources required for quality control and testing, allowing manufacturers to focus on other aspects of the production process.
- Reduced costs: By identifying defects early in the manufacturing process, automated testing can help reduce the cost of rework and scrap, leading to significant cost savings.
Predictive Quality Control
Predictive quality control is another exciting application of AI in PCB manufacturing. Predictive quality control involves using machine learning algorithms to analyze process data and identify potential quality issues before they occur.
By continuously monitoring process parameters such as temperature, pressure, and flow rates, predictive quality control systems can identify trends and patterns that may indicate a potential quality issue. This allows manufacturers to take proactive measures to address the issue before it results in defects or failures.
Some of the key benefits of predictive quality control in PCB manufacturing include:
- Improved product quality: By identifying potential quality issues early in the manufacturing process, predictive quality control can help ensure that the final product meets the required specifications and performance standards.
- Reduced scrap and rework: Predictive quality control can help reduce the amount of scrap and rework required, leading to significant cost savings and improved efficiency.
- Increased customer satisfaction: By delivering high-quality products that meet or exceed customer expectations, predictive quality control can help improve customer satisfaction and loyalty.
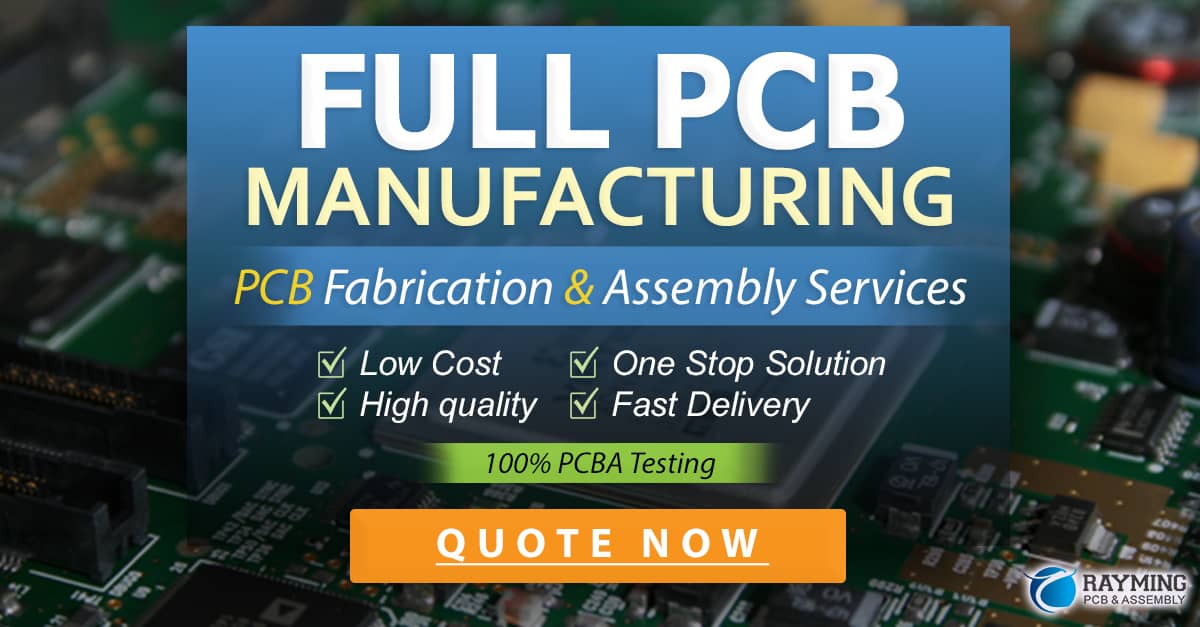
The Future of AI in PCB Manufacturing
As AI technology continues to evolve and mature, it is expected to play an increasingly important role in the PCB manufacturing industry. Some of the key areas where AI is expected to make a significant impact in the coming years include:
Digital Twins
Digital twins are virtual replicas of physical objects or systems that can be used to simulate and optimize their performance. In the context of PCB manufacturing, digital twins can be used to create virtual models of PCBs and simulate their performance under various conditions.
By using AI and machine learning algorithms to analyze the data generated by these simulations, manufacturers can identify potential issues and optimize the design and manufacturing process for improved performance and reliability.
Autonomous Manufacturing
Autonomous manufacturing is another area where AI is expected to make a significant impact in the coming years. Autonomous manufacturing involves using AI-powered robots and automation systems to perform various tasks in the manufacturing process, from assembly and inspection to packaging and logistics.
By leveraging the power of AI and machine learning, autonomous manufacturing systems can learn from vast amounts of data and continuously improve their performance over time. This not only improves efficiency and reduces costs but also allows manufacturers to respond more quickly to changing market demands and customer needs.
Supply Chain Optimization
AI is also expected to play a significant role in optimizing the supply chain for PCB manufacturing. By analyzing vast amounts of data from various sources, including suppliers, manufacturers, and customers, AI algorithms can help identify potential bottlenecks and inefficiencies in the supply chain.
This can help manufacturers optimize their inventory levels, reduce lead times, and improve overall supply chain performance. By leveraging the power of AI and machine learning, PCB manufacturers can create more agile and responsive supply chains that can adapt quickly to changing market conditions and customer needs.
Frequently Asked Questions (FAQ)
-
What is AI-PCB?
AI-PCB refers to the application of artificial intelligence (AI) technology in the printed circuit board (PCB) manufacturing industry. This includes the use of AI in PCB design, manufacturing processes, quality control, and testing. -
How does AI improve PCB design?
AI-assisted PCB design software uses machine learning algorithms to automate many of the tedious and repetitive tasks involved in PCB design. This can lead to faster design times, improved accuracy, and increased efficiency. -
What is generative design in PCB manufacturing?
Generative design is a process where AI algorithms are used to generate multiple design options based on specific performance criteria and constraints. This approach allows engineers to explore a wider range of design possibilities and identify the most optimal solution for a given application. -
How does AI improve quality control in PCB manufacturing?
AI-powered automated testing systems can learn from vast amounts of test data and continuously improve their defect detection capabilities over time. This improves the accuracy and reliability of the testing process and reduces the need for manual intervention and rework. -
What is the future of AI in PCB manufacturing?
As AI technology continues to evolve and mature, it is expected to play an increasingly important role in the PCB manufacturing industry. Some of the key areas where AI is expected to make a significant impact in the coming years include digital twins, autonomous manufacturing, and supply chain optimization.
Conclusion
Artificial intelligence is rapidly becoming the next frontier in the PCB manufacturing industry. From AI-assisted PCB design software and generative design to automated optical inspection and predictive maintenance, AI is helping manufacturers improve efficiency, reduce costs, and deliver higher-quality products to their customers.
As AI technology continues to evolve and mature, it is expected to play an increasingly important role in the PCB manufacturing industry. By leveraging the power of AI and machine learning, manufacturers can create more agile and responsive supply chains, optimize their manufacturing processes, and deliver innovative products that meet the evolving needs of their customers.
While there are still challenges to be addressed, such as data security and the need for skilled talent, the potential benefits of AI in PCB manufacturing are too significant to ignore. As more and more manufacturers adopt AI technologies, we can expect to see a new era of innovation and growth in the PCB industry, driven by the power of artificial intelligence.
0 Comments