What is a Circuit Board?
A circuit board, also known as a printed circuit board (PCB), is a fundamental component of modern electronic devices. It is a flat, insulating board made from materials such as fiberglass, composite epoxy, or other laminate materials. The primary purpose of a circuit board is to provide a stable platform for electronic components to be mounted and interconnected through conductive pathways, tracks, or signal traces etched from copper sheets laminated onto the non-conductive substrate.
Types of Circuit Boards
There are several types of circuit boards, each designed to serve specific purposes and applications:
-
Single-sided PCB: These boards have conductive traces on only one side of the substrate. They are simple, cost-effective, and suitable for low-density designs.
-
Double-sided PCB: These boards have conductive traces on both sides of the substrate, allowing for more complex designs and higher component density. The two sides are connected through vias (vertical interconnect access).
-
Multi-layer PCB: These boards consist of multiple layers of conductive traces separated by insulating layers. They offer the highest density and complexity, making them suitable for advanced applications such as high-speed digital devices, servers, and telecommunications equipment.
-
Flexible PCB: These boards are made from flexible materials, such as polyimide, allowing them to bend and conform to various shapes. They are used in applications that require flexibility or where space is limited.
-
Rigid-Flex PCB: These boards combine the features of rigid and flexible PCBs, consisting of both rigid and flexible sections. They offer the benefits of both types, such as stability and flexibility, and are used in applications that require both characteristics.
The Importance of Digital Circuit Boards
Digital circuit boards play a crucial role in the functioning of electronic devices. They provide the necessary infrastructure for digital components, such as microprocessors, memory chips, and digital signal processors, to operate and communicate with each other. Some key reasons why digital circuit boards are essential include:
-
Signal Integrity: Digital circuit boards are designed to maintain the integrity of digital signals as they travel through the conductive traces. This is achieved through proper design techniques, such as controlled impedance, matched trace lengths, and proper termination, which minimize signal reflections, crosstalk, and other signal integrity issues.
-
High-Speed Operation: Digital devices often operate at high frequencies, requiring circuit boards that can handle high-speed signals. Multi-layer PCBs with carefully designed signal traces and ground planes help minimize signal distortion and ensure reliable high-speed operation.
-
Miniaturization: As electronic devices become smaller and more compact, digital circuit boards need to accommodate a higher density of components in a limited space. Multi-layer PCBs and advanced manufacturing techniques enable the creation of compact, high-density digital circuit boards.
-
Reliability: Digital circuit boards are designed and manufactured to withstand various environmental factors, such as temperature fluctuations, vibrations, and humidity. Proper material selection, manufacturing processes, and quality control ensure that digital circuit boards are reliable and durable.
Designing Digital Circuit Boards
Designing a digital circuit board involves several key steps and considerations:
-
Schematic Design: The first step is to create a schematic diagram that represents the electronic circuit. This includes selecting the appropriate components, defining their connections, and ensuring that the circuit functions as intended.
-
Component Placement: Once the schematic is finalized, the components are placed on the circuit board layout. The placement should consider factors such as signal integrity, power distribution, thermal management, and manufacturability.
-
Routing: After component placement, the conductive traces are routed to interconnect the components according to the schematic. Routing should follow best practices, such as minimizing trace lengths, avoiding sharp angles, and maintaining proper spacing between traces to minimize signal interference.
-
Power and Ground Planes: Digital circuit boards often include power and ground planes to provide a stable reference voltage and minimize noise. These planes are typically placed on separate layers and connected to the components through vias.
-
Design Rule Check (DRC): Before finalizing the design, a DRC is performed to ensure that the layout adheres to the manufacturing constraints and design rules. This includes checking for minimum trace widths, spacings, drill sizes, and other parameters specified by the PCB manufacturer.
-
Gerber File Generation: Once the design is finalized and verified, Gerber files are generated. These files contain the information needed by the PCB manufacturer to fabricate the board, including the layer layouts, drill files, and solder mask and silkscreen data.
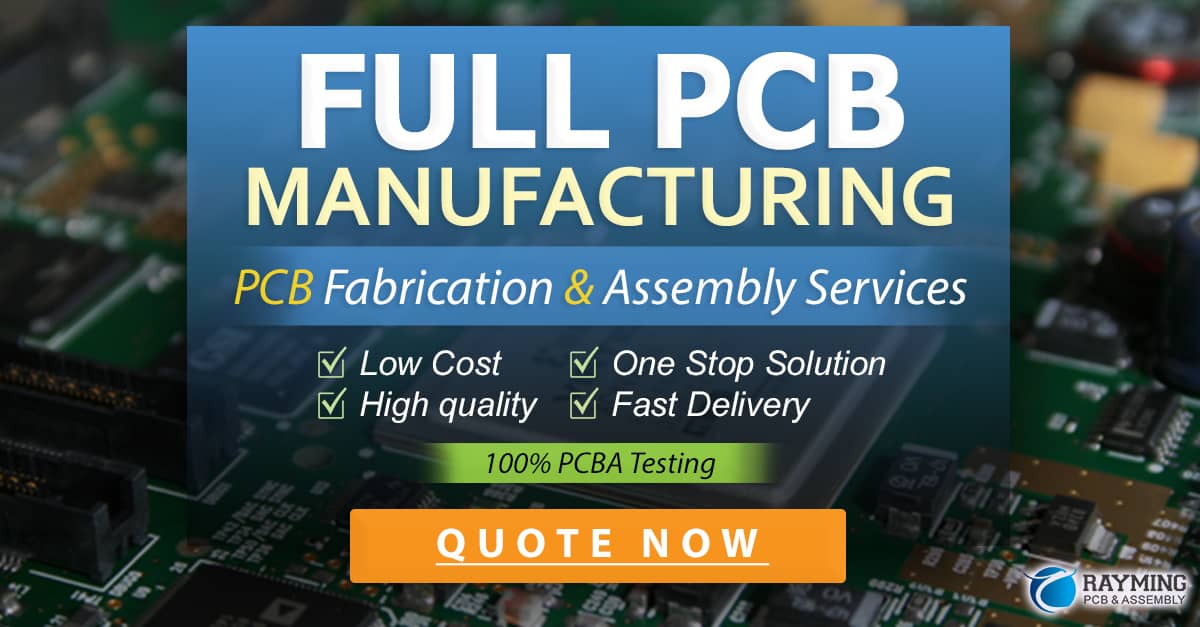
Manufacturing Digital Circuit Boards
The manufacturing process for digital circuit boards involves several steps:
-
PCB Fabrication: The bare PCB is fabricated based on the Gerber files. This includes creating the conductive traces, drilling holes, and applying the solder mask and silkscreen.
-
Component Placement: The electronic components are placed on the PCB using automated pick-and-place machines. The machines use the component placement data from the design files to accurately position the components on the board.
-
Soldering: After component placement, the board goes through a soldering process to establish electrical connections between the components and the PCB traces. This can be done through wave soldering, reflow soldering, or selective soldering, depending on the type of components and the board design.
-
Inspection and Testing: The assembled PCB undergoes various inspections and tests to ensure proper functionality and quality. This includes automated optical inspection (AOI), in-circuit testing (ICT), and functional testing.
-
Conformal Coating and Finishing: If required, the PCB may undergo additional steps such as conformal coating to protect against environmental factors or finishing processes like surface plating or labeling.
Advancements in Digital Circuit Board Technology
Digital circuit board technology continues to evolve to meet the demands of modern electronic devices. Some notable advancements include:
-
High-Density Interconnect (HDI): HDI PCBs feature finer trace widths, smaller vias, and higher component density, enabling the creation of more compact and complex digital devices.
-
Embedded Components: Some advanced PCBs incorporate embedded components, such as capacitors or resistors, within the layers of the board. This saves space and improves performance by reducing the distance between components.
-
3D Printing: Additive manufacturing techniques, such as 3D printing, are being explored for creating PCBs. This allows for the creation of complex, three-dimensional structures and the integration of electronics into non-traditional form factors.
-
Advanced Materials: New materials, such as high-frequency laminates and low-loss dielectrics, are being developed to improve the performance of digital circuit boards at higher frequencies and data rates.
Frequently Asked Questions (FAQ)
-
What is the difference between a digital and an analog circuit board?
Digital circuit boards are designed to handle discrete, binary signals (0s and 1s), while analog circuit boards deal with continuous signals that vary in amplitude and frequency. Digital boards often have more complex layouts and require careful design to ensure signal integrity at high speeds. -
Can a digital circuit board have both surface-mount and through-hole components?
Yes, a digital circuit board can accommodate both surface-mount (SMD) and through-hole (THT) components. SMD components are more common in modern digital designs due to their smaller size and better high-frequency performance, but THT components are still used for certain applications or when mechanical strength is required. -
What is the role of vias in a digital circuit board?
Vias are conductive holes that allow signals to pass through different layers of a multi-layer PCB. They are used to interconnect traces on different layers, create ground or power connections, and route signals between components on opposite sides of the board. -
How do you ensure signal integrity in a high-speed digital circuit board?
To ensure signal integrity in a high-speed digital circuit board, designers use various techniques, such as controlled impedance traces, differential signaling, proper termination, and ground planes. They also minimize trace lengths, avoid sharp angles, and maintain proper spacing between traces to reduce crosstalk and signal reflections. -
What are the challenges in manufacturing high-density digital circuit boards?
Manufacturing high-density digital circuit boards presents several challenges, including: - Achieving fine trace widths and spacings
- Drilling small, precise vias
- Ensuring proper alignment and registration of layers
- Managing heat dissipation and thermal stress
- Maintaining high yields and quality control
To overcome these challenges, manufacturers use advanced equipment, materials, and processes, such as high-resolution imaging, laser drilling, and automated inspection systems.
In conclusion, digital circuit boards are the backbone of modern electronic devices, providing the necessary infrastructure for digital components to operate and communicate effectively. Designing and manufacturing these boards requires careful consideration of signal integrity, high-speed performance, miniaturization, and reliability. As technology advances, digital circuit boards continue to evolve, incorporating new materials, techniques, and manufacturing processes to meet the ever-increasing demands of the digital world.
Component Type | Advantages | Disadvantages |
---|---|---|
Surface-mount (SMD) | Smaller size, better high-frequency performance, higher component density | More challenging to hand-solder, more susceptible to thermal stress |
Through-hole (THT) | Stronger mechanical connection, easier to hand-solder, better for high-power components | Larger size, limited high-frequency performance, lower component density |
PCB Type | Layers | Applications |
---|---|---|
Single-sided | 1 | Simple, low-cost, low-density designs |
Double-sided | 2 | More complex designs, higher component density |
Multi-layer | 4, 6, 8, or more | High-density, high-speed, complex designs |
Flexible | Varies | Applications requiring flexibility or conformity |
Rigid-Flex | Varies | Applications requiring both rigidity and flexibility |
0 Comments