What is Design for Manufacturability (DFM)?
Design for Manufacturability, also known as Design4Manufacturing or DFM, is the process of designing products in a way that optimizes ease of manufacturing and reduces manufacturing costs. DFM involves designing parts and products that can be produced efficiently, given the manufacturing processes available.
The main goal of DFM is to reduce the manufacturing costs and time while maintaining product quality and performance. This is achieved by simplifying product designs, minimizing the number of parts, standardizing components and materials, designing for ease of fabrication, assembly, and testing.
Why is Design for Manufacturability Important?
Implementing DFM principles early in the product development process can lead to significant benefits for companies, including:
-
Reduced Manufacturing Costs: DFM helps to minimize manufacturing costs by optimizing product designs for the chosen manufacturing processes, reducing material waste, and minimizing the need for specialized tooling or equipment.
-
Improved Product Quality: By considering manufacturing constraints and limitations during the design phase, DFM helps to ensure that products can be consistently produced to the required quality standards.
-
Faster Time-to-Market: DFM streamlines the manufacturing process, reducing lead times and enabling faster product launches.
-
Increased Profitability: By reducing manufacturing costs and improving product quality, DFM contributes to increased profitability for companies.
-
Enhanced Collaboration: DFM fosters collaboration between design and manufacturing teams, ensuring that designs are optimized for manufacturability from the outset.
Key Principles of Design for Manufacturability
To successfully implement DFM, designers should consider the following key principles:
1. Simplify Product Designs
One of the primary goals of DFM is to simplify product designs to reduce manufacturing complexity and costs. This can be achieved by:
- Minimizing the number of parts in an assembly
- Standardizing components and materials
- Designing parts for multi-functionality
- Avoiding unnecessary features or complexity
2. Design for Ease of Fabrication
Designers should consider the capabilities and limitations of the chosen manufacturing processes when creating product designs. This involves:
- Selecting materials that are compatible with the manufacturing process
- Designing parts with uniform wall thickness to avoid sink marks and warpage
- Avoiding sharp corners and edges that can cause stress concentrations
- Incorporating draft angles for easy ejection from molds
- Designing parts with appropriate tolerances for the manufacturing process
3. Design for Ease of Assembly
Designing products for easy assembly can significantly reduce manufacturing time and costs. Key considerations include:
- Minimizing the number of assembly steps required
- Designing parts for self-alignment and self-locating
- Avoiding the need for specialized assembly tools or equipment
- Providing adequate clearance and access for assembly operations
- Considering the use of snap-fits, press-fits, or other joining methods that eliminate the need for separate fasteners
4. Design for Ease of Testing
Incorporating design features that facilitate testing can help to reduce quality control costs and improve product reliability. This includes:
- Providing test points or access for functional testing
- Designing parts with features that allow for easy visual inspection
- Incorporating poka-yoke (mistake-proofing) features to prevent assembly errors
- Considering the use of automated testing equipment
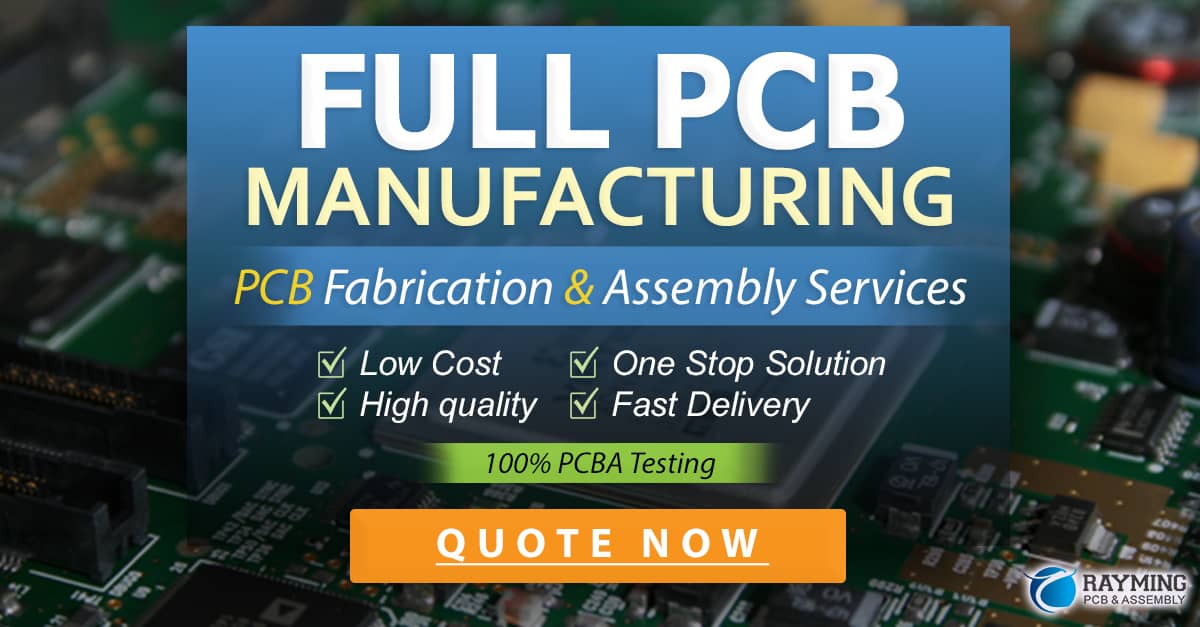
Implementing Design for Manufacturability
To successfully implement DFM, companies should follow a structured approach that involves the following steps:
-
Establish a Cross-Functional Team: Assemble a team that includes representatives from design, engineering, manufacturing, quality, and other relevant departments to ensure that all perspectives are considered.
-
Define Manufacturing Processes and Constraints: Clearly define the manufacturing processes that will be used and identify any constraints or limitations that need to be considered during the design phase.
-
Conduct Design Reviews: Regularly review product designs with the cross-functional team to identify potential manufacturability issues and opportunities for improvement.
-
Use DFM Software Tools: Utilize CAD/CAM software with built-in DFM analysis tools to assess the manufacturability of designs and identify areas for optimization.
-
Collaborate with Suppliers: Engage with suppliers early in the design process to ensure that components and materials meet DFM requirements and to identify potential cost-saving opportunities.
-
Continuously Monitor and Improve: Regularly assess the effectiveness of DFM efforts and identify opportunities for continuous improvement.
DFM Techniques for Common Manufacturing Processes
The specific DFM techniques used will depend on the manufacturing processes employed. Some common examples include:
Injection Molding
- Design parts with uniform wall thickness
- Avoid undercuts and negative draft angles
- Use ribs and gussets to improve structural integrity
- Incorporate appropriate draft angles for easy ejection from molds
- Consider the use of multi-cavity molds for higher production volumes
CNC Machining
- Avoid deep pockets or cavities that require long tool extensions
- Design parts with standard hole sizes and thread pitches
- Minimize the need for secondary operations such as drilling or tapping
- Consider the use of standard tooling to reduce costs
- Design parts with appropriate tolerances for the machining process
Sheet Metal Fabrication
- Design parts with uniform bend radii
- Avoid tight corners or small features that can be difficult to form
- Consider the use of standard gauge materials to reduce costs
- Minimize the need for secondary operations such as welding or painting
- Design parts with appropriate clearances for the fabrication process
3D Printing
- Design parts with appropriate wall thickness and infill density for the printing process
- Avoid large overhangs or unsupported structures
- Consider the use of support structures for complex geometries
- Optimize part orientation to minimize print time and material usage
- Select materials that are compatible with the printing process and meet performance requirements
DFM Case Studies
To illustrate the benefits of DFM, let’s consider a few case studies:
Case Study 1: Automotive Component Redesign
A Tier 1 automotive supplier was experiencing high manufacturing costs and quality issues with a critical component. By applying DFM principles, the company was able to:
- Reduce the number of parts in the assembly from 15 to 7
- Standardize materials and components across multiple product variants
- Redesign the component for ease of assembly, reducing assembly time by 30%
- Incorporate features for automated testing, improving quality control efficiency by 25%
As a result, the company achieved a 20% reduction in manufacturing costs and a 50% reduction in quality issues, leading to significant savings and improved customer satisfaction.
Case Study 2: Consumer Electronics Enclosure Optimization
A consumer electronics company was looking to reduce the cost and time-to-market for a new product enclosure. By implementing DFM techniques, the company was able to:
- Optimize the enclosure design for injection molding, reducing the number of mold cavities required
- Incorporate snap-fit features to eliminate the need for separate fasteners and reduce assembly time
- Design the enclosure with uniform wall thickness to minimize warpage and improve cosmetic appearance
- Collaborate with suppliers to identify cost-saving opportunities in material selection and tooling design
As a result, the company achieved a 15% reduction in manufacturing costs and a 20% reduction in time-to-market, enabling a successful product launch and improved market share.
Frequently Asked Questions (FAQ)
- What is the difference between Design for Manufacturability (DFM) and Design for Assembly (DFA)?
Design for Manufacturability (DFM) focuses on optimizing product designs for ease of manufacturing and reducing manufacturing costs, while Design for Assembly (DFA) focuses specifically on designing products for easy and efficient assembly. DFA is a subset of DFM and is often used in conjunction with DFM principles to optimize overall product design for manufacturability.
- How does DFM impact product quality?
DFM helps to improve product quality by considering manufacturing constraints and limitations during the design phase. By designing products that can be consistently produced to the required quality standards, DFM reduces the risk of quality issues and product defects. Additionally, DFM techniques such as poka-yoke (mistake-proofing) and design for testing help to ensure that products meet quality requirements.
- At what stage of the product development process should DFM be implemented?
DFM should be implemented as early as possible in the product development process, ideally during the conceptual design phase. By considering manufacturability constraints and optimizing designs early on, companies can avoid costly design changes and delays later in the development process. However, DFM principles should be continuously applied throughout the entire product development lifecycle to ensure ongoing optimization and improvement.
- What are some common challenges in implementing DFM?
Some common challenges in implementing DFM include:
- Resistance to change from design teams who may be accustomed to traditional design practices
- Lack of communication and collaboration between design and manufacturing teams
- Insufficient knowledge or expertise in DFM principles and techniques
- Balancing DFM considerations with other product requirements such as functionality, aesthetics, and cost
-
Adapting to new technologies and manufacturing processes that may require different DFM approaches
-
How can companies measure the success of their DFM efforts?
Companies can measure the success of their DFM efforts by tracking key performance indicators (KPIs) such as:
- Manufacturing cost reductions
- Improved product quality and reduced defect rates
- Faster time-to-market and reduced product development cycles
- Increased production efficiency and throughput
- Improved customer satisfaction and reduced warranty claims
By regularly monitoring and analyzing these KPIs, companies can assess the effectiveness of their DFM initiatives and identify areas for continuous improvement.
Conclusion
Design for Manufacturability (DFM) is a critical approach for companies looking to optimize product designs, reduce manufacturing costs, and improve overall product quality and performance. By considering manufacturing constraints and limitations early in the design process and applying key DFM principles and techniques, companies can achieve significant benefits in terms of cost savings, time-to-market, and customer satisfaction.
To successfully implement DFM, companies should adopt a structured approach that involves cross-functional collaboration, regular design reviews, and continuous monitoring and improvement. By embracing DFM as a core part of their product development strategy, companies can position themselves for success in today’s competitive manufacturing landscape.
0 Comments