What Are PCB box-build Services?
PCB box-build, also known as systems integration or electro-mechanical assembly, involves assembling printed circuit board assemblies (PCBAs) into complete functional units within an enclosure or box. It goes beyond standard PCB assembly to include mounting the PCBA into a chassis or enclosure along with any required wiring, displays, switches, connectors, and other hardware.
The result is a fully integrated and tested electronic subassembly or finished product ready for use in a larger system or as a standalone unit. Box-build services are commonly used for:
- Electronic control units (ECUs)
- Industrial control panels
- Medical devices
- IoT gateways and sensor nodes
- Communications equipment
- Point-of-sale systems
- Security and access control devices
Outsourcing box-build assembly allows OEMs to focus on core competencies like product design and marketing while leaving manufacturing to an experienced EMS partner. A full-service box-build provider will handle the entire assembly process including:
- PCB assembly (SMT and through-hole)
- Mechanical assembly and integration
- Wire harnessing and cable assembly
- Functional testing and programming
- Packaging and shipping logistics
EMS companies that specialize in box-builds often support both low-volume high-mix and high-volume production. They can scale manufacturing to meet changing demand and offer flexibility that in-house assembly shops cannot always provide.
The PCB Box-Build Process
The box-build process flow typically includes the following steps:
-
Incoming Materials – PCBs, enclosures, wiring, and other components are received and inspected per the BOM.
-
Kitting – All parts needed for each subassembly or product are kitted together.
-
Mechanical Assembly – The PCB is mounted into the enclosure or chassis and secured.
-
Wiring and Soldering – Wires are cut, stripped, and connected to the PCB, switches, sensors, and other components. Wire ties and guides are added for strain relief. Soldering may be done manually or using robotic soldering equipment.
-
Functional Test – Power is applied and the assembly is tested for proper operation based on a test procedure. Units that fail are troubleshot and reworked.
-
Quality Control – Inspectors do a final visual check and may conduct additional tests on a sample basis.
-
Packaging – The finished box-builds are packaged with any required accessories, manuals, etc. and prepared for shipment.
-
Shipping – The products are shipped directly to the OEM, distribution center, or end customer.
The exact process will vary depending on product complexity, volume, and customer requirements. Complex multi-part assemblies may require several sub-processes. Automated assembly and test equipment will be used for higher volume production. And some box-build projects may also require custom functional test development.
Benefits of Using Complete PCB Box-Build Services
Outsourcing box-build assembly to an experienced EMS partner offers several advantages:
Focus on Core Competencies
Removing the need to build and maintain in-house manufacturing capabilities allows OEMs to focus on product design, marketing, and other core competencies. This is especially valuable for startups and smaller companies with limited resources.
Access to Expertise
An established box-build partner will have skilled personnel and processes already in place. They can apply best practices across electrical, mechanical, and test engineering along with supply chain management and quality control.
Scalability
Box-build services providers are accustomed to meeting variable demand and scaling production up or down as needed. They often serve multiple markets and customers which allows them to level-load their factories and offer greater flexibility.
Reduced Labor Costs
Outsourcing can reduce manufacturing overhead, especially related to assembler labor costs. EMS partners strategically locate facilities in lower-cost regions while still meeting quality expectations.
Supply Chain Management
Experienced box-build partners will assist with component sourcing including hard-to-find or long lead-time parts. They often leverage a global network of suppliers and distributors to secure the best pricing and availability.
Testing Capabilities
Catching defects and reliability issues early is critical. A box-build assembler should have robust testing capabilities including flying probe, in-circuit test (ICT), automated optical inspection (AOI), burn-in, and functional test. Some may even offer custom functional test development.
Faster Time to Market
The end result is typically a faster time to market for new products. Companies can take advantage of an established process and supply chain to ramp production more quickly.
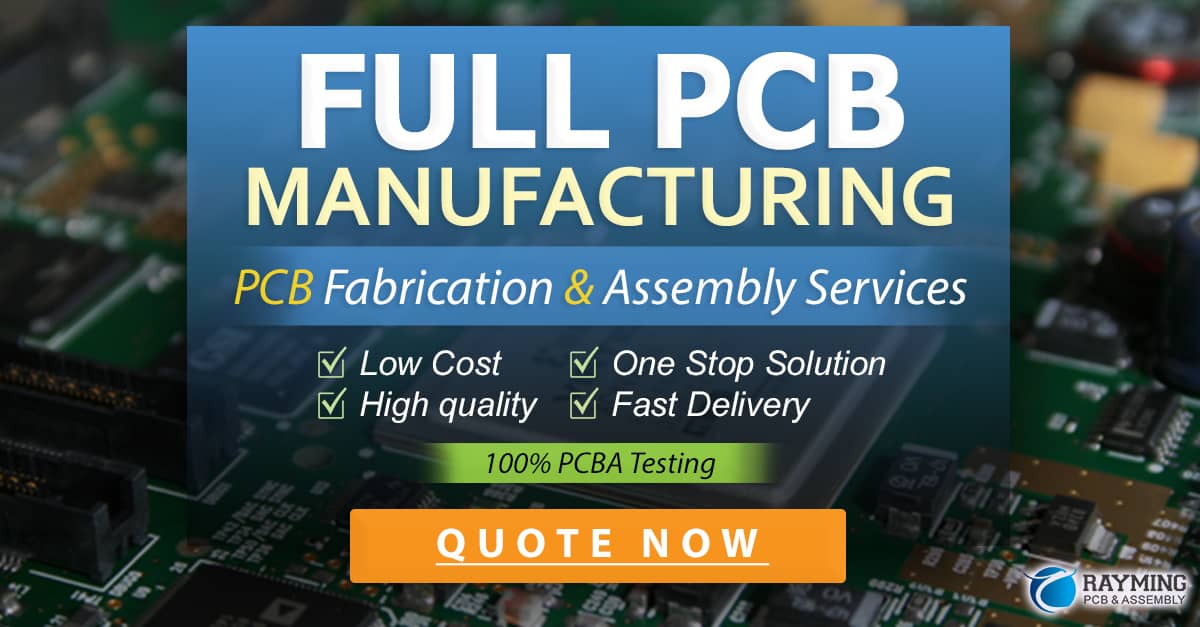
Choosing a PCB Box-Build Partner
Not all EMS providers are created equal when it comes to box-build assembly capabilities. Important considerations when selecting a partner include:
Technical Capabilities
Do they have experience with similar products in terms of complexity, component types, volumes, etc? Are engineering and test development services offered?
Industry Knowledge
Knowledge of industry-specific standards and common design approaches is important, especially for highly regulated industries like medical equipment and aerospace.
Quality Systems
Look for a provider with robust quality management systems. Ideally they will be certified to relevant standards such as ISO 9001, ISO 13485 (for medical devices), or AS9100 (for aerospace).
Location and Logistics
Where are their manufacturing facilities located relative to your design team and customer base? What logistics capabilities do they offer in terms of warehousing, order fulfillment, and shipping?
Support and Communication
Evaluate how responsive they are during the quoting and engineering review process. Will you have a dedicated program manager? What systems are in place for providing project status updates?
NPI and DFX Capabilities
For new products, look for a partner that can add value during the design and development phases. Can they provide design for manufacturability (DFM), design for assembly (DFA), and design for test (DFT) feedback?
PCB Box-Build Services Comparison
To help compare potential partners, here is a table summarizing key service offerings and capabilities:
Service | Provider A | Provider B | Provider C |
---|---|---|---|
PCB Assembly | ✓ | ✓ | ✓ |
Mechanical Assembly | ✓ | ✓ | X |
Cable and Wire Harness Assembly | ✓ | X | ✓ |
Functional Testing | ✓ | ✓ | ✓ |
Custom Test Development | X | ✓ | ✓ |
Supply Chain Management | ✓ | ✓ | ✓ |
Logistics and Fulfillment | X | ✓ | ✓ |
Prototyping | ✓ | X | ✓ |
Engineering Support | ✓ | ✓ | X |
Box-Build vs. Consignment Assembly
In some cases, an OEM may choose to do PCB assembly in-house and then outsource just the final mechanical assembly, test, and packaging. This is often referred to as consignment assembly since the PCBA is consigned to the box-build partner.
Consignment assembly can offer some advantages:
- More control over PCBA process and supply chain
- Ability to leverage existing SMT lines and personnel
- Faster turnaround for PCBA changes and prototypes
However, using separate vendors for PCBA and box-build creates additional logistics challenges and potential failure points. It may also limit end-to-end product traceability. In most cases, outsourcing the entire box-build process offers the most effective and streamlined approach.
Box-Build Assembly Cost Considerations
Several factors will affect the total cost of PCB box-build services:
-
Material costs – Component costs are typically 75-80% of the total PCBA cost. More complex boards with high layer counts and dense BGAs will typically be more expensive.
-
Labor costs – The time and skill required for assembly will depend on complexity, component types, and mechanical assembly requirements. Products with intricate wiring and manual assembly will have higher labor costs.
-
Test costs – More complex products may require expensive test fixtures and longer test times. Custom functional test development will also add to the total cost.
-
Shipping costs – Logistics costs depend on manufacturing location, shipment sizes, and delivery terms. Choosing a global manufacturing partner with facilities near the end market can reduce shipping costs.
-
NRE and tooling costs – There may be significant up-front costs for design, DFM review, test development, and assembly fixtures and jigs. These non-recurring engineering (NRE) costs are typically amortized over the production volume.
In general, labor cost per unit will decrease with higher volumes due to economies of scale and more automated assembly approaches. And greater volumes make it easier to negotiate lower material costs. For an accurate cost estimate, work with potential box-build partners to get a detailed quote based on the BOM, mechanical drawings, and testing requirements.
Streamlining the Box-Build Process
There are several steps OEMs can take to streamline the PCB box-build process and ensure a successful outsourcing partnership:
Define Requirements Early
Involve the EMS partner early, ideally during the design phase. Clearly communicate the product vision, target market, expected volumes, and unique application requirements.
Leverage the EMS Partner’s Expertise
Take advantage of the box-build partner’s DFM, DFA, and DFT knowledge to optimize the design for manufacturability, cost, and reliability. Consider their standard processes, approved vendor lists, and preferred parts.
Invest in Documentation
Develop a clear and complete documentation package including BOMs, assembly drawings, work instructions, and test procedures. Ensure all stakeholders have access to the latest revisions.
Plan for Test
Start test development early, especially for custom functional tests. Specify which records need to be kept for traceability. Consider programming and calibration requirements.
Communicate and Collaborate
Establish clear points of contact and regular communication channels. Use a project management platform to share documents, schedules, and status updates. Visit the factory in person if possible to build the relationship.
By working closely with an experienced box-build partner and following these best practices, OEMs can bring products to market faster while minimizing manufacturing risks and costs.
Frequently Asked Questions (FAQ)
What is the difference between PCB assembly and box-build?
PCB assembly refers to soldering electronic components onto a printed circuit board (PCB). Box-build goes a step further to integrate the populated PCB into a fully enclosed unit along with any displays, switches, wiring, and mechanical hardware.
Do box-build services include design?
Some box-build partners do offer design and engineering services, but typically the OEM is responsible for the overall product design. However, a good partner will provide DFM and DFA feedback to help optimize the PCB and enclosure design for manufacturing.
What testing is typically included with PCB box-build?
Most box-build partners will conduct a full functional test of the final assembly based on the OEM’s specifications and test procedure. This may include testing power supplies, buttons and switches, displays, I/O ports, and sensors. More complex products may also require custom functional test fixtures and programming.
How long does the box-build process take?
The manufacturing lead time depends on the complexity, volume, and material lead times. Simple products may take just a few days while complex systems could require several weeks. Higher volumes can also require more time for production planning and material procurement. Work with your partner to understand the timeline and plan accordingly.
What are the key challenges with outsourcing box-builds?
Communication and long-distance collaboration can be challenging, especially when design changes or production issues arise. Time zone differences, language barriers, and cultural differences may need to be navigated. Choosing a partner with a local presence and robust program management capabilities is important.
Conclusion
PCB box-build services provide an efficient and cost-effective approach to electronics manufacturing for OEMs of all sizes. By combining PCB assembly, mechanical assembly, test, and packaging into one streamlined process, box-build services can dramatically reduce time to market and manufacturing complexity.
OEMs should carefully evaluate the technical capabilities, quality systems, design support, and logistics services of potential box-build partners. Open communication and close collaboration throughout the design and NPI process are also critical for success.
With the right EMS partner and a DFM-optimized product design, PCB box-build services can unlock new innovations across a range of industries and applications. As electronics become increasingly integrated and complex, box-build assembly will play an essential role in bringing next-generation products to life.
0 Comments