Introduction to Blind-Buried-Vias
In the world of printed circuit board (PCB) design, vias play a crucial role in connecting different layers of the board. Among the various types of vias, blind and buried vias have gained significant popularity due to their ability to optimize board space and improve signal integrity. This article will dive deep into the concept of blind and buried vias, their advantages, manufacturing process, and their applications in modern PCB design.
What are Blind and Buried Vias?
Blind Vias
Blind vias are a type of via that starts from an outer layer of the PCB and terminates at an inner layer, without passing through the entire thickness of the board. In other words, blind vias are not visible on both sides of the PCB. They are typically used to connect the outer layers to the inner layers of the board, providing a more direct path for electrical signals.
Buried Vias
Buried vias, on the other hand, are vias that are located entirely within the inner layers of the PCB. They do not extend to either of the outer layers of the board. Buried vias are used to interconnect the inner layers of the PCB, allowing for more complex routing and better utilization of board space.
Advantages of Blind and Buried Vias
Space Optimization
One of the primary advantages of using blind and buried vias is the optimization of board space. By eliminating the need for vias to pass through the entire thickness of the board, designers can reduce the overall size of the PCB. This is particularly beneficial in applications where space is limited, such as in mobile devices, wearables, and other compact electronic products.
Improved Signal Integrity
Blind and buried vias also contribute to improved signal integrity in high-speed PCB designs. By providing shorter and more direct paths for electrical signals, these vias minimize the signal loss and distortion that can occur when signals travel through longer routes. This is especially important in applications that require high-speed data transmission, such as telecommunications, networking, and automotive electronics.
Increased Routing Density
The use of blind and buried vias allows for increased routing density on the inner layers of the PCB. With the ability to interconnect inner layers without occupying space on the outer layers, designers can route more traces and components on the inner layers. This leads to a more efficient utilization of the available board space and enables the design of more complex and feature-rich PCBs.
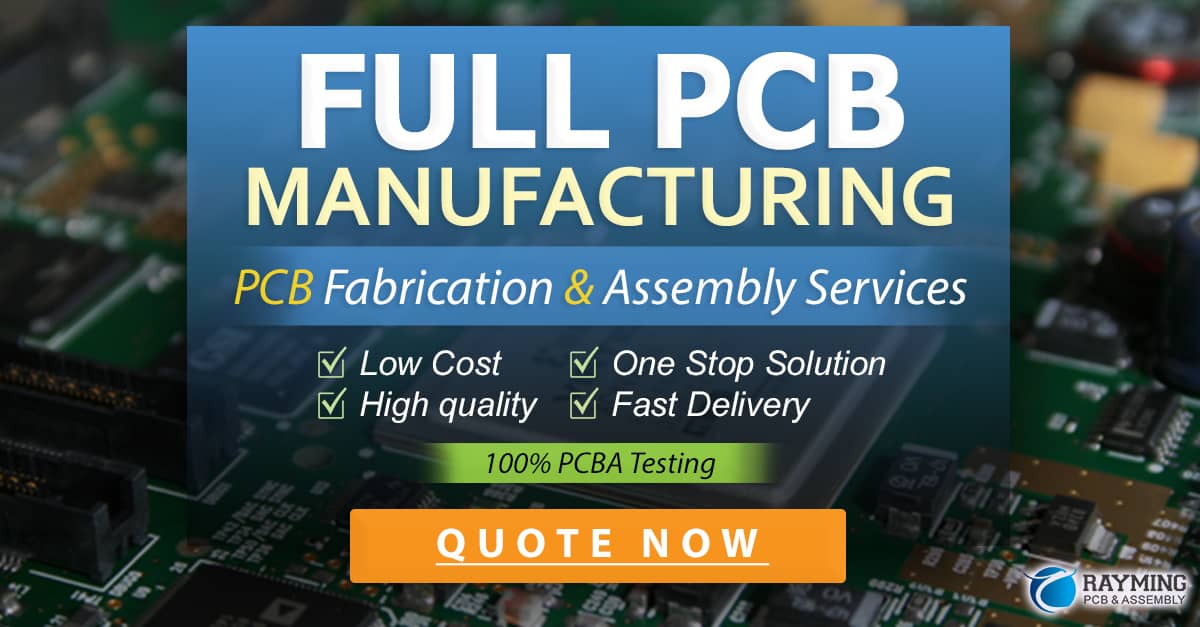
Manufacturing Process of Blind and Buried Vias
The manufacturing process of blind and buried vias is more complex compared to traditional through-hole vias. It involves several additional steps and requires specialized equipment and expertise. Here’s a general overview of the manufacturing process:
-
Layer Stacking: The PCB layers are stacked and aligned according to the design specifications. The number of layers and their arrangement depend on the specific requirements of the board.
-
Drilling: The blind and buried vias are drilled using laser or mechanical drilling techniques. Laser drilling is commonly used for smaller via sizes and higher precision, while mechanical drilling is suitable for larger vias.
-
Plating: After drilling, the vias are plated with a conductive material, typically copper, to create an electrical connection between the layers. The plating process ensures that the vias have the necessary conductivity and durability.
-
Filling: In some cases, the blind and buried vias are filled with a non-conductive material, such as epoxy or resin, to improve the structural integrity of the board and prevent any air gaps or voids.
-
Lamination: The PCB layers are laminated together under high pressure and temperature to form a solid and cohesive board.
-
Outer Layer Processing: The outer layers of the PCB undergo additional processing steps, such as patterning, etching, and surface finishing, to create the desired circuit patterns and protect the board from environmental factors.
Applications of Blind and Buried Vias
Blind and buried vias find applications in various industries and products where PCB space optimization, signal integrity, and high-density routing are critical. Some common applications include:
-
Smartphone and Tablet PCBs: The compact nature of smartphones and tablets requires the use of blind and buried vias to minimize board size and accommodate the high-density components and circuitry.
-
Wearable Electronics: Wearable devices, such as smartwatches and fitness trackers, benefit from the space-saving and signal integrity improvements offered by blind and buried vias.
-
High-Speed Networking Equipment: Network switches, routers, and other high-speed networking devices rely on blind and buried vias to handle the complex routing and ensure reliable data transmission.
-
Automotive Electronics: The automotive industry increasingly uses blind and buried vias in PCBs for various electronic systems, such as infotainment, advanced driver assistance systems (ADAS), and engine control units (ECUs).
-
Medical Devices: Medical equipment, including implantable devices and diagnostic tools, utilize blind and buried vias to achieve miniaturization and reliable performance.
Challenges and Considerations
While blind and buried vias offer numerous benefits, there are some challenges and considerations to keep in mind when incorporating them into PCB designs:
-
Increased Manufacturing Complexity: The manufacturing process for blind and buried vias is more complex and requires specialized equipment and expertise. This can lead to higher manufacturing costs and longer lead times compared to traditional PCBs.
-
Design Considerations: Designing PCBs with blind and buried vias requires careful planning and adherence to design guidelines. Factors such as via size, placement, and spacing need to be considered to ensure manufacturability and reliability.
-
Testing and Inspection: The buried nature of blind and buried vias makes them more challenging to test and inspect compared to through-hole vias. Specialized testing methods, such as X-ray inspection or electrical testing, may be necessary to ensure the integrity of the connections.
-
Cost Implications: The additional manufacturing steps and complexity associated with blind and buried vias can increase the overall cost of the PCB. However, the cost impact should be weighed against the benefits of space optimization, signal integrity, and improved functionality.
Frequently Asked Questions (FAQ)
- What is the difference between blind and buried vias?
-
Blind vias start from an outer layer and terminate at an inner layer, while buried vias are located entirely within the inner layers of the PCB.
-
What are the advantages of using blind and buried vias in PCB design?
-
Blind and buried vias offer several advantages, including space optimization, improved signal integrity, and increased routing density on the inner layers of the PCB.
-
How are blind and buried vias manufactured?
-
The manufacturing process for blind and buried vias involves layer stacking, drilling (laser or mechanical), plating, filling (optional), lamination, and outer layer processing.
-
In which industries are blind and buried vias commonly used?
-
Blind and buried vias are commonly used in industries such as smartphones and tablets, wearable electronics, high-speed networking equipment, automotive electronics, and medical devices.
-
What are the challenges and considerations when using blind and buried vias in PCB design?
- The challenges and considerations include increased manufacturing complexity, specific design considerations, testing and inspection challenges, and potential cost implications.
Conclusion
Blind and buried vias have revolutionized the world of PCB design, offering numerous benefits in terms of space optimization, signal integrity, and routing density. By understanding the concepts, advantages, manufacturing process, and applications of blind and buried vias, PCB designers and engineers can leverage these technologies to create more compact, efficient, and high-performance electronic products.
As the demand for miniaturization and advanced functionality continues to grow across various industries, the use of blind and buried vias will likely become increasingly prevalent in PCB design. However, it is essential to carefully consider the challenges and trade-offs associated with these technologies and work closely with experienced PCB manufacturers to ensure successful implementation.
By staying up-to-date with the latest advancements in blind and buried via technology and following best design practices, PCB designers can unlock new possibilities and push the boundaries of electronic product innovation.
0 Comments