Introduction to Digital Image Correlation (DIC) for PCBs
Digital Image Correlation, commonly known as DIC, is an optical measurement technique that has gained significant traction in various engineering fields, including printed circuit board (PCB) manufacturing. DIC enables non-contact, full-field strain and displacement measurements by comparing digital images of a sample surface captured before and after deformation. In the context of PCB manufacturing, DIC proves particularly beneficial for analyzing Lead-Free PCBs, which are more susceptible to thermal and mechanical stresses compared to their lead-containing counterparts.
How DIC Works
DIC utilizes high-resolution digital cameras to capture images of a sample surface at different stages of loading or deformation. The surface is typically prepared with a random speckle pattern, which serves as a unique fingerprint for tracking displacements. Specialized software then compares the images and calculates the displacement and strain fields based on the movement of the speckle pattern.
DIC Process Step | Description |
---|---|
Sample Preparation | Apply random speckle pattern to sample surface |
Image Capture | Record high-resolution images before and after deformation |
Image Analysis | Software compares images and calculates displacement and strain fields |
Advantages of DIC over Traditional Measurement Techniques
Compared to traditional strain measurement techniques like strain gauges, DIC offers several advantages:
- Non-contact measurement: DIC does not require physical contact with the sample, eliminating potential damage or interference.
- Full-field measurement: DIC provides strain and displacement data across the entire sample surface, rather than at discrete points.
- High spatial resolution: DIC can measure strains at sub-pixel levels, enabling the detection of localized deformations.
- Versatility: DIC can be applied to a wide range of materials and sample geometries.
Benefits of DIC in Lead-free PCB Manufacturing
The transition to lead-free PCBs has posed several challenges for manufacturers, primarily due to the higher processing temperatures and increased thermal and mechanical stresses. DIC has emerged as a powerful tool to address these challenges and optimize the lead-free PCB manufacturing process.
1. Thermal Strain Analysis
Lead-free solders, such as tin-silver-copper (SAC) alloys, require higher reflow temperatures compared to traditional lead-based solders. These elevated temperatures can induce significant thermal strains in the PCB, leading to warpage and other defects. DIC enables the accurate measurement of thermal strains during the reflow process, allowing manufacturers to optimize the temperature profile and minimize PCB warpage.
Solder Type | Reflow Temperature | Thermal Strain |
---|---|---|
Lead-based | 180-200°C | Low |
Lead-free (SAC) | 220-260°C | High |
By employing DIC, manufacturers can:
– Identify high-strain regions on the PCB
– Evaluate the effectiveness of different PCB designs and materials in mitigating thermal strains
– Optimize the reflow temperature profile to minimize warpage
2. Solder Joint Reliability Assessment
The reliability of solder joints is critical for the overall performance and longevity of PCBs. Lead-free solder joints are more prone to fatigue failures due to their higher stiffness and reduced ductility compared to lead-based solders. DIC can be used to assess the mechanical behavior and reliability of lead-free solder joints under various loading conditions, such as thermal cycling and vibration.
Solder Joint Property | Lead-based | Lead-free (SAC) |
---|---|---|
Stiffness | Low | High |
Ductility | High | Low |
Fatigue Resistance | High | Low |
DIC enables researchers and manufacturers to:
– Quantify the strain distribution within individual solder joints
– Identify potential failure sites and mechanisms
– Evaluate the impact of different solder compositions and PCB designs on joint reliability
– Validate and refine finite element models for solder joint behavior
3. PCB Warpage Measurement
PCB warpage is a critical issue in lead-free manufacturing, as it can lead to misalignment during component placement and soldering defects. Traditional warpage measurement techniques, such as shadow moiré and laser scanning, provide limited data points and may not capture localized deformations. DIC, on the other hand, offers full-field warpage measurements with high spatial resolution.
Warpage Measurement Technique | Measurement Type | Spatial Resolution |
---|---|---|
Shadow Moiré | Out-of-plane | Low |
Laser Scanning | Out-of-plane | Medium |
Digital Image Correlation (DIC) | In-plane and Out-of-plane | High |
By using DIC for PCB warpage measurement, manufacturers can:
– Obtain detailed warpage maps of the entire PCB surface
– Identify localized high-warpage regions
– Evaluate the effectiveness of different PCB substrate materials and stack-ups in reducing warpage
– Optimize the PCB design and assembly process to minimize warpage-related defects
4. Thermomechanical Stress Analysis
Lead-free PCBs experience higher thermomechanical stresses during manufacturing and operation due to the mismatch in coefficients of thermal expansion (CTE) between the PCB substrate, solder joints, and components. These stresses can lead to PCB deformation, solder joint failures, and component cracking. DIC can be used to analyze the thermomechanical stresses in lead-free PCBs under various thermal loading conditions.
Material | CTE (ppm/°C) |
---|---|
FR-4 PCB Substrate | 14-17 |
SAC Solder | 20-23 |
Copper | 16-17 |
Silicon | 2-3 |
By employing DIC for thermomechanical stress analysis, manufacturers can:
– Quantify the stress distribution across the PCB and components
– Identify high-stress regions prone to failure
– Evaluate the impact of different PCB designs, materials, and component layouts on thermomechanical stresses
– Optimize the PCB design and manufacturing process to minimize thermomechanical stress-related failures
5. Quality Control and Failure Analysis
DIC can be integrated into the quality control and failure analysis processes for lead-free PCBs. By comparing DIC measurements of production samples against established baselines, manufacturers can quickly identify PCBs with abnormal strain or warpage patterns, indicating potential defects or deviations from the desired specifications.
In case of PCB failures, DIC can be used to analyze the strain and deformation patterns around the failure site, helping to identify the root cause and mechanism of failure. This information can be used to improve PCB design, materials selection, and manufacturing processes to prevent future failures.
Failure Type | Potential Causes | DIC Analysis |
---|---|---|
Solder Joint Crack | – Thermal stress – Mechanical shock – Fatigue |
– Strain distribution around crack – Crack propagation path |
PCB Warpage | – Uneven heating – CTE mismatch – Improper handling |
– Full-field warpage map – Localized high-warpage regions |
Component Crack | – Thermal stress – Mechanical stress – Manufacturing defect |
– Strain distribution within component – Crack origin and propagation |
Frequently Asked Questions (FAQ)
1. What are the main challenges in lead-free PCB manufacturing?
Lead-free PCB manufacturing faces several challenges, including:
– Higher reflow temperatures leading to increased thermal stress and warpage
– Reduced ductility and fatigue resistance of lead-free solder joints
– Greater sensitivity to thermomechanical stresses due to CTE mismatches
– Potential for defects such as head-in-pillow, solder bridging, and component cracking
2. How does DIC compare to other warpage measurement techniques?
Compared to techniques like shadow moiré and laser scanning, DIC offers:
– Full-field warpage measurements with high spatial resolution
– The ability to measure both in-plane and out-of-plane deformations
– Non-contact measurement, eliminating potential interference with the sample
– Versatility in measuring warpage under various thermal and mechanical loading conditions
3. Can DIC be used for real-time monitoring of PCB manufacturing processes?
Yes, DIC can be integrated into real-time monitoring systems for PCB manufacturing processes, such as reflow soldering and component placement. By continuously analyzing DIC data, manufacturers can quickly detect and respond to abnormal strain or warpage patterns, enabling early intervention and reducing the occurrence of defects.
4. How does DIC contribute to the development of more reliable lead-free PCBs?
DIC contributes to the development of more reliable lead-free PCBs by:
– Providing detailed insights into the thermal and mechanical behavior of PCBs and components
– Enabling the identification of high-stress and high-warpage regions prone to failure
– Allowing the evaluation and optimization of PCB designs, materials, and manufacturing processes
– Facilitating the validation and refinement of computational models for PCB and solder joint reliability
5. What are the limitations of DIC in lead-free PCB manufacturing?
Some limitations of DIC in lead-free PCB manufacturing include:
– The need for sample surface preparation (speckle pattern application), which may not be feasible for all PCBs
– The requirement for specialized hardware (high-resolution cameras) and software for data acquisition and analysis
– Potential challenges in measuring strains in highly reflective or transparent surfaces
– The need for skilled operators and data interpretation to ensure accurate and reliable results
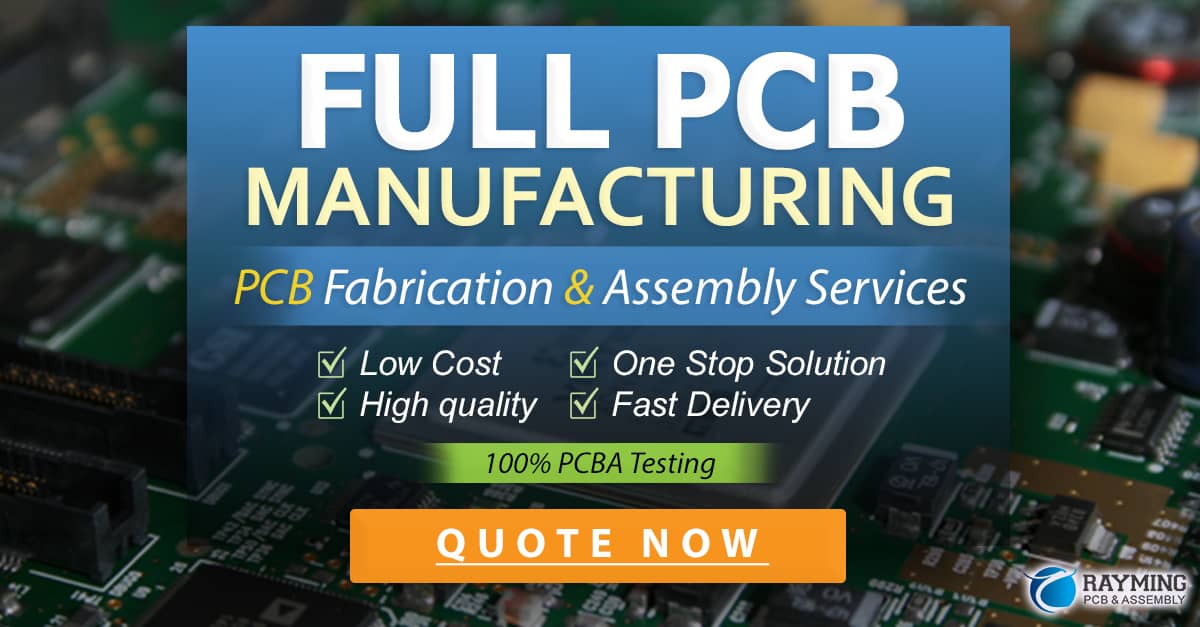
Conclusion
Digital Image Correlation (DIC) has emerged as a powerful tool in lead-free PCB manufacturing, offering numerous benefits in thermal strain analysis, solder joint reliability assessment, PCB warpage measurement, thermomechanical stress analysis, and quality control. By providing detailed, full-field strain and deformation data, DIC enables manufacturers to optimize their processes, improve PCB designs, and develop more reliable lead-free PCBs.
As the demand for high-performance, environmentally friendly electronics continues to grow, the adoption of DIC in lead-free PCB manufacturing is expected to increase. Manufacturers that embrace this technology will be well-positioned to overcome the challenges associated with lead-free PCBs and deliver products that meet the ever-increasing reliability and quality requirements of the industry.
0 Comments