Introduction to Ni-Au PCB Finish
Nickel-gold (Ni-Au) is a popular surface finish for printed circuit boards (PCBs) that provides excellent solderability, durability, and corrosion resistance. The Ni-Au finish consists of an electroless nickel layer plated onto the copper pads, followed by a thin layer of immersion gold. This combination offers several advantages over other PCB finishes, making it a preferred choice for high-reliability applications in industries such as aerospace, military, and medical devices.
Key Benefits of Ni-Au PCB Finish
- Excellent solderability
- High corrosion resistance
- Good electrical conductivity
- Compatibility with wire bonding
- Extended shelf life
The Ni-Au Plating Process
The electrolytic Ni-Au plating process involves several steps to ensure a high-quality, uniform finish on the PCB surface.
Step 1: Surface Preparation
Before plating, the PCB surface must be thoroughly cleaned to remove any contaminants, oxides, or organic residues that could affect the adhesion and quality of the finish. This typically involves a series of cleaning steps, such as:
- Alkaline cleaning
- Micro-etching
- Acid dipping
- Rinsing with deionized water
Step 2: Electroless Nickel Plating
After surface preparation, the PCB is immersed in an electroless nickel plating bath. The bath contains a nickel salt solution, a reducing agent, and complexing agents that help maintain the stability of the solution. The nickel layer is deposited through an autocatalytic reaction, which means that the nickel ions are reduced to metallic nickel without the need for an external electric current.
The electroless nickel layer serves several purposes:
- It acts as a barrier layer, preventing the diffusion of copper into the gold layer.
- It provides a uniform, smooth surface for the subsequent gold plating.
- It enhances the corrosion resistance of the PCB.
The typical thickness of the electroless nickel layer ranges from 3 to 6 µm.
Step 3: Immersion Gold Plating
Following the electroless nickel plating, the PCB is immersed in an immersion gold plating bath. The gold layer is deposited through a displacement reaction, where the gold ions in the solution displace some of the nickel atoms on the surface of the PCB. This results in a thin, uniform layer of gold that provides excellent solderability and protection against oxidation.
The immersion gold layer is typically very thin, ranging from 0.05 to 0.2 µm. This thin layer is sufficient to provide the necessary protection and solderability, while keeping the cost of the finish relatively low compared to thicker gold layers.
Step 4: Rinsing and Drying
After the gold plating step, the PCB is thoroughly rinsed with deionized water to remove any residual plating chemicals. It is then dried using hot air or an oven to ensure that the surface is completely free of moisture.
Advantages of Electrolytic Ni-Au PCB Finish
The electrolytic Ni-Au finish offers several advantages over other PCB finishes, making it a popular choice for high-reliability applications.
Excellent Solderability
The thin immersion gold layer provides excellent solderability, allowing for easy and reliable soldering of components to the PCB. The gold layer prevents oxidation of the underlying nickel, ensuring that the surface remains solderable even after extended storage periods.
High Corrosion Resistance
The combination of the electroless nickel barrier layer and the immersion gold layer provides exceptional corrosion resistance. The nickel layer prevents the diffusion of copper to the surface, while the gold layer protects the nickel from oxidation and corrosion. This makes Ni-Au a suitable choice for applications exposed to harsh environments or corrosive agents.
Good Electrical Conductivity
The Ni-Au finish offers good electrical conductivity, ensuring reliable signal transmission and low contact resistance. The gold layer, despite being thin, provides a stable, non-reactive surface that maintains its electrical properties over time.
Compatibility with Wire Bonding
The Ni-Au finish is compatible with various wire bonding techniques, such as thermosonic and ultrasonic bonding. The gold layer provides a suitable surface for bonding gold or aluminum wires, making it a popular choice for applications requiring wire bonding, such as semiconductor packaging.
Extended Shelf Life
The Ni-Au finish provides an extended shelf life compared to other finishes, such as immersion silver or organic solderability preservatives (OSP). The gold layer protects the underlying nickel from oxidation, ensuring that the PCB remains solderable and functional even after prolonged storage periods.
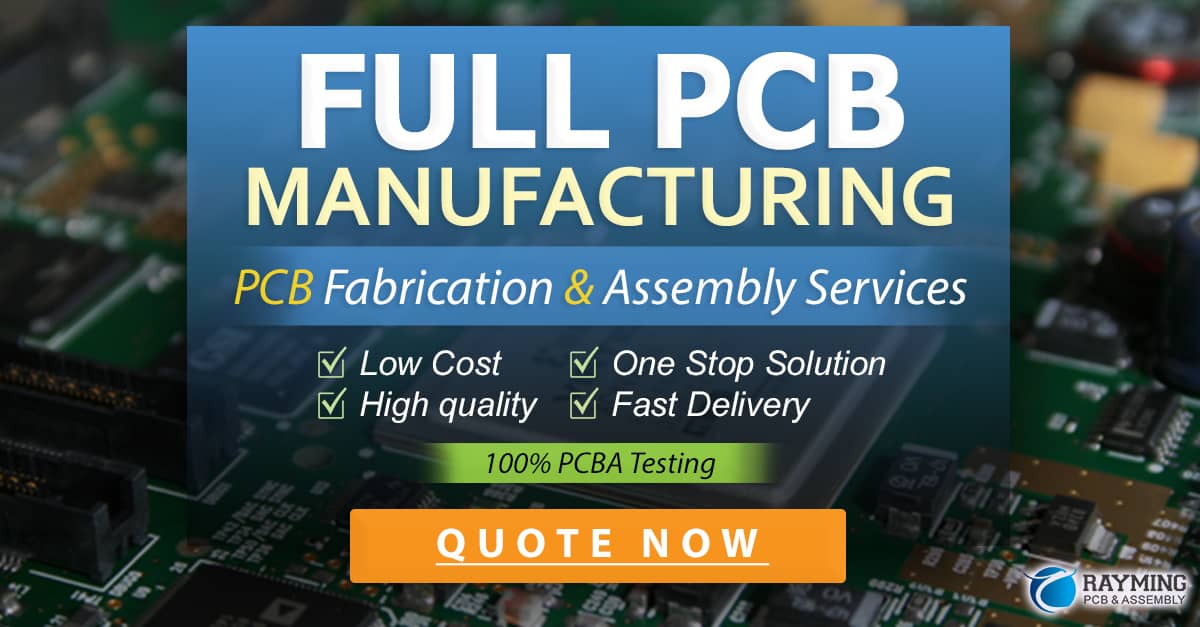
Comparison with Other PCB Finishes
The following table compares the properties of electrolytic Ni-Au with other common PCB finishes:
Property | Ni-Au | ENIG | Immersion Tin | Immersion Silver | OSP |
---|---|---|---|---|---|
Solderability | +++ | +++ | ++ | ++ | + |
Corrosion Resistance | +++ | +++ | + | ++ | + |
Electrical Conductivity | ++ | ++ | ++ | ++ | + |
Wire Bonding Compatibility | +++ | +++ | + | + | – |
Shelf Life | +++ | +++ | + | ++ | + |
- Good ++ Very Good +++ Excellent – Not Suitable
As shown in the table, Ni-Au offers excellent performance in most categories, making it a versatile choice for a wide range of applications. However, it is important to consider the specific requirements of the application when selecting a PCB finish.
Design Considerations for Ni-Au PCB Finish
When designing a PCB with an electrolytic Ni-Au finish, several factors should be considered to ensure optimal performance and reliability.
Pad and Via Sizing
The Ni-Au plating process can result in slight variations in the final dimensions of pads and vias due to the additional thickness of the plated layers. Designers should take this into account and adjust the pad and via sizes accordingly to ensure proper solderability and component fit.
Solder Mask Clearance
Adequate solder mask clearance should be provided around the pads and vias to prevent solder mask from encroaching on the plated surfaces during the solder mask application process. This ensures that the entire pad surface is available for soldering and helps prevent solder joint defects.
Plating Thickness Specifications
The thickness of the electroless nickel and immersion gold layers should be specified based on the requirements of the application. Thicker nickel layers may be necessary for applications requiring enhanced corrosion resistance or mechanical durability, while thicker gold layers may be needed for improved wire bonding performance.
Controlled Impedance Design
For high-speed or high-frequency applications, controlled impedance design may be necessary to ensure proper signal integrity. The Ni-Au finish can affect the impedance of the PCB traces, so designers should take this into account when calculating the required trace widths and spacings.
FAQ
1. What is the typical thickness of the electroless nickel layer in a Ni-Au PCB finish?
The typical thickness of the electroless nickel layer in a Ni-Au PCB finish ranges from 3 to 6 µm. This thickness provides a sufficient barrier layer to prevent copper diffusion and enhance corrosion resistance.
2. How does the Ni-Au finish compare to ENIG in terms of cost?
The electrolytic Ni-Au finish is generally less expensive than the electroless nickel immersion gold (ENIG) finish. This is because the electrolytic process is simpler and faster, requiring fewer process steps and chemicals. However, the exact cost difference may vary depending on the specific PCB manufacturer and the production volume.
3. Can the Ni-Au finish be used for high-temperature applications?
Yes, the Ni-Au finish is suitable for high-temperature applications. The electroless nickel layer provides a stable, heat-resistant base, while the gold layer protects the nickel from oxidation at elevated temperatures. However, for extremely high-temperature applications, other finishes such as gold over palladium or gold over palladium-nickel may be more appropriate.
4. Is the Ni-Au finish RoHS compliant?
Yes, the Ni-Au finish is RoHS (Restriction of Hazardous Substances) compliant. The process does not involve the use of any restricted substances such as lead, cadmium, or hexavalent chromium. This makes Ni-Au a suitable choice for applications that require compliance with RoHS regulations.
5. How does the shelf life of Ni-Au compare to other PCB finishes?
The Ni-Au finish provides an extended shelf life compared to other finishes such as immersion silver or OSP. The gold layer protects the underlying nickel from oxidation, ensuring that the PCB remains solderable and functional even after prolonged storage periods. In general, a Ni-Au finished PCB can be stored for 12 months or more without significant degradation in solderability or performance.
Conclusion
The electrolytic Ni-Au PCB finish is a popular choice for high-reliability applications due to its excellent solderability, corrosion resistance, and compatibility with wire bonding. The combination of an electroless nickel barrier layer and a thin immersion gold layer provides a durable, stable surface finish that maintains its properties over extended periods.
When designing PCBs with a Ni-Au finish, it is important to consider factors such as pad and via sizing, solder mask clearance, plating thickness specifications, and controlled impedance design. By taking these factors into account and working closely with the PCB manufacturer, designers can ensure that their PCBs meet the required performance and reliability standards.
As the electronics industry continues to evolve and demand higher performance and reliability, the electrolytic Ni-Au PCB finish is likely to remain a popular choice for a wide range of applications. Its combination of technical advantages and cost-effectiveness make it a versatile solution for designers and manufacturers alike.
0 Comments