What is PCB Corrosion?
PCB corrosion is the gradual deterioration of the metal surfaces on a printed circuit board due to chemical reactions with the environment. This process can cause the formation of oxides, sulfides, or other compounds that degrade the electrical and mechanical properties of the PCB.
Types of PCB Corrosion
There are several types of PCB corrosion, each with its own characteristics and causes:
- Atmospheric Corrosion: Caused by exposure to oxygen, moisture, and other gases in the atmosphere.
- Galvanic Corrosion: Occurs when two dissimilar metals are in contact with each other and an electrolyte, such as moisture.
- Chemical Corrosion: Results from exposure to harsh chemicals, such as acids, bases, or solvents.
- Electrolytic Corrosion: Happens when an electrical current passes through an electrolyte, causing the dissolution of metal ions.
Causes of PCB Corrosion
Several factors can contribute to the corrosion of printed circuit boards. Understanding these causes is crucial for developing effective prevention strategies.
Environmental Factors
Humidity and Moisture
High humidity and moisture levels can accelerate PCB corrosion by providing an electrolyte for electrochemical reactions. When water condenses on the PCB surface, it can dissolve contaminants and create an ionic solution that promotes corrosion.
Temperature Fluctuations
Frequent temperature changes can cause condensation on the PCB surface, leading to moisture accumulation and corrosion. Additionally, high temperatures can accelerate chemical reactions and increase the rate of corrosion.
Airborne Contaminants
Airborne contaminants, such as salt, dust, and pollution, can settle on the PCB surface and promote corrosion. These contaminants can absorb moisture from the air and create an electrolyte that facilitates electrochemical reactions.
Material Selection
Incompatible Materials
Using incompatible materials in PCB construction can lead to galvanic corrosion. When two dissimilar metals are in contact with each other and an electrolyte, an electrochemical reaction occurs, causing one metal to corrode preferentially.
Impurities and Contaminants
Impurities and contaminants in the PCB materials can promote corrosion by creating local anodic and cathodic sites. These impurities may include metal ions, organic compounds, or other foreign substances that can disrupt the protective oxide layer on the metal surface.
Manufacturing Processes
Inadequate Surface Finishing
Poor surface finishing techniques, such as improper plating or coating, can leave the PCB vulnerable to corrosion. Uneven or incomplete coverage of the protective layer can expose the underlying metal to the environment, allowing corrosion to occur.
Flux Residues
Flux is used during the soldering process to remove oxides and improve solder wettability. However, if the flux residues are not properly cleaned after soldering, they can absorb moisture and promote corrosion.
Mechanical Stress
Mechanical stress, such as bending or twisting of the PCB, can cause cracks or delamination in the protective coatings, exposing the underlying metal to the environment and increasing the risk of corrosion.
Preventing PCB Corrosion
To minimize the risk of PCB corrosion and ensure the longevity of electronic devices, several preventive measures can be implemented during the design, manufacturing, and operation stages.
Design Considerations
Material Selection
Choosing compatible and corrosion-resistant materials is crucial for preventing PCB corrosion. Some commonly used materials with good corrosion resistance include:
Material | Characteristics |
---|---|
Gold | Excellent corrosion resistance, high conductivity, and durability |
Silver | Good corrosion resistance, high conductivity, and reflectivity |
Tin | Good corrosion resistance, solderable, and low cost |
Nickel | Good corrosion resistance, hardness, and wear resistance |
When selecting materials, consider their galvanic compatibility to avoid creating corrosion-prone junctions.
Conformal Coating
Applying a conformal coating to the PCB surface can provide a barrier against moisture, contaminants, and other corrosive agents. Common conformal coating materials include:
- Acrylic
- Epoxy
- Polyurethane
- Silicone
Choose a coating material that is compatible with the PCB materials and provides adequate protection against the expected environmental conditions.
Proper Grounding and Shielding
Designing proper grounding and shielding can help prevent electrolytic corrosion by minimizing the presence of stray currents on the PCB. Ensure that all components are properly grounded and that sensitive areas are shielded from electromagnetic interference (EMI) and radio frequency interference (RFI).
Manufacturing Best Practices
Surface Finishing
Applying a high-quality surface finish to the PCB can provide a protective layer against corrosion. Some common surface finishing techniques include:
- Hot Air Solder Leveling (HASL)
- Electroless Nickel Immersion Gold (ENIG)
- Immersion Silver
- Immersion Tin
- Organic Solderability Preservative (OSP)
Select a surface finish that is compatible with the PCB materials and provides adequate protection for the intended application.
Cleaning and Contamination Control
Proper cleaning and contamination control during the manufacturing process can help prevent corrosion by removing flux residues, contaminants, and other harmful substances from the PCB surface. Use appropriate cleaning agents and techniques, such as:
- Solvent cleaning
- Aqueous cleaning
- Plasma cleaning
- Ultrasonic cleaning
Implement strict contamination control measures, such as using clean room environments, filtered air, and proper handling procedures to minimize the introduction of contaminants during manufacturing.
Operational and Maintenance Strategies
Environmental Control
Controlling the operating environment can help prevent PCB corrosion by minimizing exposure to humidity, temperature fluctuations, and airborne contaminants. Some strategies include:
- Using air conditioning and dehumidification systems to maintain a stable temperature and humidity level
- Implementing air filtration systems to remove airborne contaminants
- Storing PCBs in sealed containers with desiccants when not in use
Regular Inspection and Maintenance
Conducting regular inspections and maintenance can help detect and address corrosion issues before they cause significant damage. Some best practices include:
- Visually inspecting PCBs for signs of corrosion, such as discoloration, pitting, or rust
- Using non-invasive testing methods, such as X-ray or ultrasonic inspection, to detect internal corrosion
- Cleaning PCBs regularly to remove contaminants and corrosion products
- Replacing corroded components or PCBs as necessary
By implementing a comprehensive maintenance program, the risk of PCB corrosion can be significantly reduced, extending the lifespan of electronic devices.
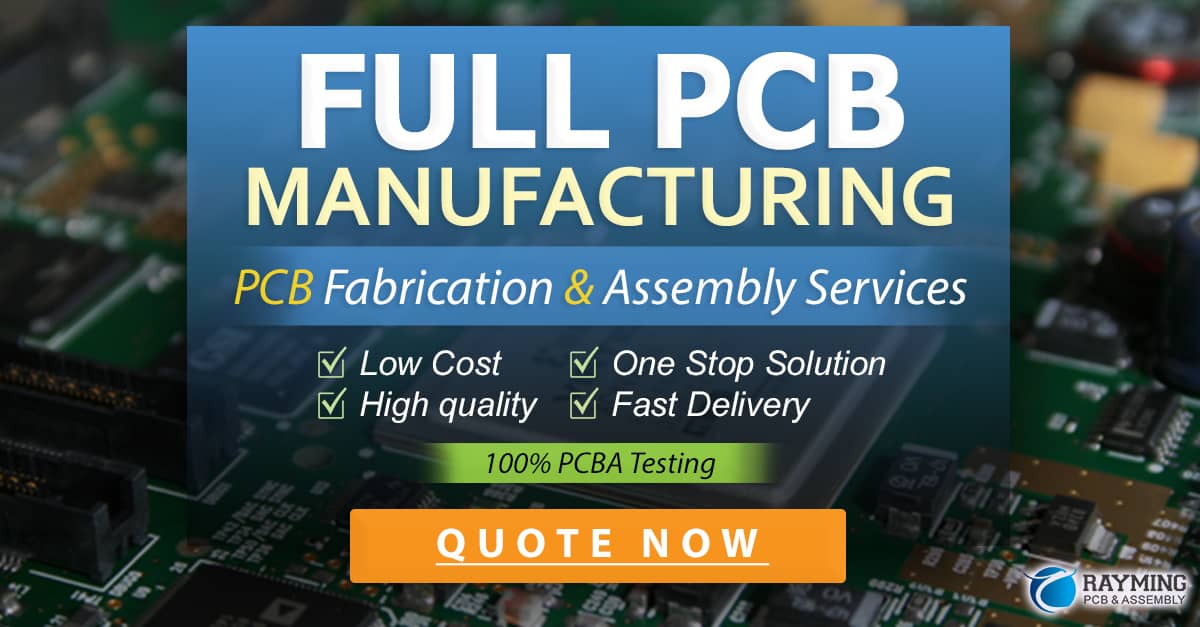
Frequently Asked Questions (FAQ)
- What are the most common signs of PCB corrosion?
- Discoloration or tarnishing of the metal surfaces
- Presence of rust, green or white deposits
- Pitting or etching of the metal surfaces
-
Reduced electrical conductivity or intermittent connections
-
Can PCB corrosion be repaired?
In some cases, minor PCB corrosion can be repaired by cleaning the affected area and applying a protective coating. However, if the corrosion is extensive or has caused significant damage to the PCB, it may be necessary to replace the affected components or the entire PCB. -
How often should PCBs be inspected for corrosion?
The frequency of PCB inspections depends on the operating environment and the criticality of the application. In general, it is recommended to inspect PCBs at least once a year, or more frequently if they are exposed to harsh environments or critical applications. -
Can conformal coating be applied to existing PCBs?
Yes, conformal coating can be applied to existing PCBs as a retrofitting measure. However, the PCB must be thoroughly cleaned and dried before applying the coating to ensure proper adhesion and coverage. -
What is the best way to store PCBs to prevent corrosion?
PCBs should be stored in a cool, dry environment with minimal temperature and humidity fluctuations. Use sealed containers with desiccants to absorb moisture and prevent contamination. Avoid storing PCBs in areas exposed to direct sunlight, heat sources, or corrosive chemicals.
Conclusion
PCB corrosion is a significant issue that can lead to device failure and reduced lifespan. By understanding the causes of PCB corrosion, such as environmental factors, material selection, and manufacturing processes, effective prevention strategies can be implemented. Designing PCBs with corrosion-resistant materials, applying conformal coatings, and ensuring proper grounding and shielding can help minimize the risk of corrosion. Implementing best practices during manufacturing, such as surface finishing and contamination control, further reduces the likelihood of corrosion. Regular inspection, maintenance, and environmental control during operation are also crucial for preventing and detecting PCB corrosion.
By adopting a comprehensive approach to PCB corrosion prevention, manufacturers and designers can ensure the reliability and longevity of electronic devices, ultimately saving costs and improving customer satisfaction. As technology continues to advance, it is essential to stay informed about the latest techniques and materials for preventing PCB corrosion and maintaining the integrity of electronic systems.
0 Comments