Introduction to Solder Mask and Its Importance
Solder mask, also known as solder resist or solder stop mask, is a thin protective layer applied to the copper traces of a printed circuit board (PCB). Its primary purpose is to prevent solder from adhering to areas where it is not intended, thus preventing short circuits and ensuring the proper functioning of the PCB. Additionally, solder mask serves as an insulating layer, protecting the copper traces from oxidation and environmental factors that could cause damage over time.
Solder mask is typically a polymer-based material that is applied to the PCB surface through various methods, such as screen printing, liquid photoimageable (LPI) coating, or dry film lamination. The most common colors for solder mask are green, red, blue, and black, although other colors are available for specific applications or aesthetic purposes.
The importance of a properly applied and maintained solder mask cannot be overstated. It plays a crucial role in:
- Preventing solder bridges and short circuits
- Providing electrical insulation between adjacent traces
- Protecting the copper traces from oxidation and corrosion
- Improving the PCB’s overall durability and longevity
- Enhancing the aesthetics of the PCB
Given the critical functions of solder mask, it is essential to ensure its integrity throughout the PCB’s lifecycle. However, various factors can lead to damage or degradation of the solder mask, necessitating repair to maintain the PCB’s performance and reliability.
Common Causes of Solder mask damage
Solder mask damage can occur due to several reasons, ranging from manufacturing defects to environmental factors and improper handling. Some of the most common causes of solder mask damage include:
- Manufacturing defects
- Improper solder mask application
- Incomplete or uneven coverage
-
Contamination during the manufacturing process
-
Environmental factors
- Exposure to harsh chemicals or solvents
- Prolonged exposure to high temperatures or humidity
-
UV radiation causing solder mask degradation
-
Mechanical damage
- Scratches or abrasions during handling or assembly
- Impact damage from drops or collisions
-
Excessive flexing or bending of the PCB
-
Soldering-related issues
- Excessive heat during soldering, causing solder mask to blister or peel
- Improper solder mask clearance around pads, leading to solder mask lifting
-
Solder mask contamination due to flux residue or other contaminants
-
Age-related degradation
- Gradual deterioration of solder mask properties over time
- Embrittlement or cracking due to repeated thermal cycling
Understanding the root causes of solder mask damage is essential for preventing future issues and determining the most appropriate repair methods.
Assessing Solder Mask Damage
Before attempting to Repair Solder Mask damage, it is crucial to assess the extent and nature of the damage. This assessment will help determine the most suitable repair approach and ensure that the repair process does not compromise the PCB’s functionality or integrity.
To assess solder mask damage, follow these steps:
- Visual inspection
- Examine the PCB under adequate lighting conditions
- Look for obvious signs of damage, such as cracks, peeling, or discoloration
-
Use a magnifying glass or microscope for closer inspection of smaller areas
-
Continuity testing
- Use a multimeter to check for short circuits or open connections
-
Verify that the damaged solder mask has not caused any electrical issues
-
Insulation resistance testing
- Measure the insulation resistance between adjacent traces
-
Ensure that the damaged solder mask has not compromised the electrical insulation
-
Contamination assessment
- Check for the presence of flux residue, dirt, or other contaminants
-
Determine if the contamination has contributed to the solder mask damage
-
Documentation
- Record the location, extent, and nature of the solder mask damage
- Take photographs or create detailed sketches for reference during the repair process
By thoroughly assessing the solder mask damage, you can make informed decisions about the most appropriate repair methods and minimize the risk of further damage during the repair process.
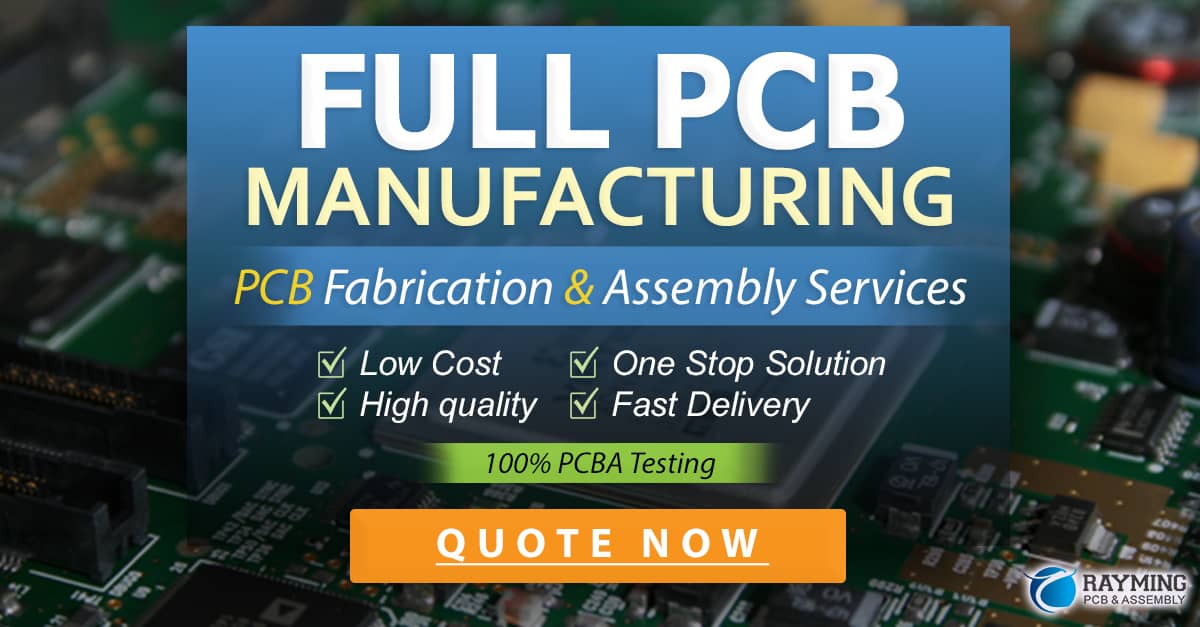
Preparing the PCB for Solder Mask Repair
Once you have assessed the solder mask damage, the next step is to prepare the PCB for repair. Proper preparation is essential to ensure that the repair process is effective and does not introduce additional issues. Follow these steps to prepare the PCB:
- Cleaning
- Remove any dirt, debris, or contaminants from the PCB surface
- Use isopropyl alcohol and a soft brush or lint-free cloth to clean the area around the damaged solder mask
-
Ensure that the cleaning process does not cause further damage to the solder mask or other components
-
Drying
- Allow the cleaned PCB to dry completely before proceeding with the repair
-
Use compressed air or a gentle heat source to accelerate the drying process, if necessary
-
Masking
- Apply masking tape or other protective materials to areas surrounding the damaged solder mask
-
This step helps prevent inadvertent damage or contamination during the repair process
-
Grounding
- Ensure that you are properly grounded to prevent electrostatic discharge (ESD) damage to the PCB
-
Use an ESD-safe workstation, wrist strap, or other grounding equipment
-
Ventilation
- Work in a well-ventilated area, especially if using chemicals or solvents during the repair process
- Use appropriate personal protective equipment (PPE), such as gloves and safety glasses
By properly preparing the PCB for solder mask repair, you can minimize the risk of further damage and ensure that the repair process is as effective as possible.
Solder Mask Repair Methods
There are several methods for repairing damaged solder mask, each with its own advantages and limitations. The choice of repair method depends on factors such as the extent of the damage, the available tools and materials, and the desired outcome. Some of the most common solder mask repair methods include:
- Liquid solder mask
- Use a liquid solder mask material, such as a UV-curable or thermally-curable polymer
- Apply the liquid solder mask to the damaged area using a fine-tipped applicator or brush
- Cure the solder mask according to the manufacturer’s instructions (e.g., exposure to UV light or heat)
- Advantages: Provides a smooth, even finish; suitable for larger areas of damage
-
Limitations: Requires specialized equipment for curing; may not match the color or texture of the original solder mask perfectly
-
Solder mask pens
- Use a solder mask pen, which contains a quick-drying, pigmented polymer
- Apply the solder mask directly to the damaged area, taking care to avoid adjacent components or traces
- Allow the solder mask to dry according to the manufacturer’s instructions
- Advantages: Easy to use; ideal for small, localized repairs; available in various colors
-
Limitations: May not provide an even finish; not suitable for larger areas of damage
-
Epoxy-based repair kits
- Use a two-part epoxy-based repair kit specifically designed for solder mask repair
- Mix the epoxy components according to the manufacturer’s instructions
- Apply the epoxy to the damaged area using a fine-tipped applicator or brush
- Allow the epoxy to cure according to the manufacturer’s instructions
- Advantages: Provides a durable, long-lasting repair; suitable for larger areas of damage
-
Limitations: May not match the color or texture of the original solder mask perfectly; requires careful mixing and application
-
UV-curable solder mask patches
- Use pre-cut, UV-curable solder mask patches that match the size and shape of the damaged area
- Apply the patch to the damaged area, ensuring that it adheres properly
- Cure the patch using a UV light source according to the manufacturer’s instructions
- Advantages: Quick and easy to apply; provides a uniform appearance; suitable for small to medium-sized repairs
- Limitations: May not be available in all colors; requires a UV light source for curing
When selecting a solder mask repair method, consider the specific requirements of your PCB and the resources available to you. It may be necessary to experiment with different methods to determine which one works best for your particular situation.
Step-by-Step Guide to Repairing Solder Mask
Once you have selected the appropriate solder mask repair method, follow these general steps to carry out the repair:
- Prepare the PCB
- Clean the area around the damaged solder mask, as described in the “Preparing the PCB for Solder Mask Repair” section
-
Apply masking tape or other protective materials to surrounding areas, if necessary
-
Apply the repair material
- Liquid solder mask: Use a fine-tipped applicator or brush to apply the liquid solder mask to the damaged area, taking care to avoid adjacent components or traces
- Solder mask pen: Apply the solder mask directly to the damaged area, using the pen’s built-in applicator
- Epoxy-based repair kit: Mix the epoxy components according to the manufacturer’s instructions, then apply the epoxy to the damaged area using a fine-tipped applicator or brush
-
UV-curable solder mask patch: Apply the pre-cut patch to the damaged area, ensuring that it adheres properly
-
Cure the repair material
- Follow the manufacturer’s instructions for curing the repair material
- Liquid solder mask and UV-curable solder mask patches typically require exposure to UV light for a specified duration
-
Solder mask pens and epoxy-based repair kits may require air-drying or thermal curing
-
Inspect the repair
- Examine the repaired area under adequate lighting conditions to ensure that the repair material has been applied evenly and completely
-
Check for any excess repair material that may have inadvertently contaminated adjacent areas, and remove it if necessary
-
Test the PCB
- Perform continuity and insulation resistance tests to verify that the repair has not compromised the PCB’s electrical integrity
- If possible, subject the repaired PCB to its normal operating conditions to ensure that the repair holds up under typical use
By following these steps and paying close attention to detail, you can effectively repair damaged solder mask and restore your PCB’s functionality and reliability.
Tips for Successful Solder Mask Repair
To ensure the best possible outcome when repairing solder mask, keep these tips in mind:
- Choose the right repair method
- Consider the extent of the damage, the available tools and materials, and the desired outcome when selecting a repair method
-
If unsure, start with a less invasive method and progress to more advanced techniques if necessary
-
Work in a clean, well-lit environment
- Minimize the risk of contamination by working in a clean, dust-free area
-
Ensure that you have adequate lighting to clearly see the damaged area and the repair process
-
Use high-quality materials
- Invest in high-quality repair materials from reputable manufacturers
-
Using subpar materials may result in inadequate repairs or additional damage to the PCB
-
Practice proper ESD protection
- Always use appropriate ESD protection equipment, such as grounded workstations and wrist straps
-
ESD damage can cause irreparable harm to sensitive electronic components
-
Be patient and precise
- Take your time when applying repair materials, and avoid rushing the process
-
Precise application and attention to detail will result in a higher-quality repair
-
Allow adequate curing time
- Follow the manufacturer’s instructions for curing repair materials
-
Attempting to use or handle the PCB before the repair material has fully cured can compromise the repair’s integrity
-
Document the repair process
- Keep detailed records of the repair process, including the materials used, the steps followed, and any observations made
- This documentation can be valuable for future reference or troubleshooting
By following these tips and adhering to best practices, you can maximize the success of your solder mask repair efforts and ensure the long-term reliability of your PCBs.
Conclusion
Repairing damaged solder mask is a critical skill for anyone working with PCBs, as it helps to maintain the boards’ functionality, reliability, and longevity. By understanding the common causes of solder mask damage, assessing the extent of the damage, and selecting the appropriate repair method, you can effectively restore your PCBs to their original condition.
Remember to work in a clean, well-lit environment, use high-quality materials, and follow best practices for ESD protection and documentation. With patience, precision, and attention to detail, you can successfully repair solder mask and keep your PCBs operating at peak performance.
Frequently Asked Questions (FAQ)
-
Q: Can I use regular paint or markers to repair solder mask?
A: No, it is not recommended to use regular paint or markers for solder mask repair. These materials may not provide the necessary insulation, durability, or compatibility with the PCB materials. Always use repair materials specifically designed for solder mask repair. -
Q: How long does it take for solder mask repair materials to cure?
A: The curing time for solder mask repair materials varies depending on the specific product and the curing method used. UV-curable materials typically cure within seconds to minutes when exposed to the appropriate UV light source, while air-drying or thermally-cured materials may take several hours to fully cure. Always refer to the manufacturer’s instructions for specific curing times and methods. -
Q: Can I repair solder mask damage if the copper traces are exposed?
A: It is possible to repair solder mask damage even if the copper traces are exposed. However, it is important to ensure that the copper traces are not contaminated, corroded, or otherwise damaged before applying the repair material. If the copper traces are damaged, additional repairs may be necessary before addressing the solder mask damage. -
Q: How can I prevent solder mask damage in the future?
A: To prevent solder mask damage, follow these best practices:- Handle PCBs with care, avoiding excessive flexing, bending, or impacts
- Use appropriate storage and packaging materials to protect PCBs during transport and storage
- Follow proper soldering techniques, avoiding excessive heat or prolonged exposure to high temperatures
- Use compatible cleaning agents and avoid harsh chemicals or solvents that may degrade the solder mask
- Implement ESD protection measures to prevent electrostatic discharge damage
-
Q: Can I use solder mask repair materials for other applications, such as insulating wires or components?
A: While solder mask repair materials are primarily designed for repairing damaged solder mask on PCBs, some products may be suitable for other insulation or protection applications. However, it is essential to consult the manufacturer’s specifications and recommendations before using solder mask repair materials for any purpose other than their intended use. In many cases, it may be more appropriate to use dedicated products specifically designed for insulating wires or components.
0 Comments