What is CEM-1 PCB?
CEM-1 (Composite Epoxy Material-1) is a type of PCB substrate material that consists of a woven glass fabric core impregnated with an epoxy resin binder. The glass fabric provides mechanical strength and dimensional stability, while the epoxy resin offers excellent insulation properties and resistance to environmental factors.
Composition of CEM-1 PCB
The composition of CEM-1 PCB is as follows:
Component | Description |
---|---|
Woven Glass Fabric | Provides mechanical strength and dimensional stability |
Epoxy Resin | Acts as a binder and offers insulation properties |
Copper Foil | Used for creating conductive traces and pads |
The woven glass fabric used in CEM-1 PCBs is typically a plain weave, with a thickness ranging from 0.005 inches to 0.007 inches. The epoxy resin is a thermosetting polymer that cures when exposed to heat and pressure during the lamination process.
Properties of CEM-1 PCB
CEM-1 PCBs offer a range of properties that make them suitable for various electronic applications. Some of the key properties of CEM-1 PCBs include:
Electrical Properties
- Dielectric Constant (1 MHz): 4.7
- Dissipation Factor (1 MHz): 0.02
- Surface Resistivity: 10^6 to 10^9 ohms
- Volume Resistivity: 10^8 to 10^10 ohm-cm
Mechanical Properties
- Flexural Strength: 70,000 to 85,000 psi
- Tensile Strength: 45,000 to 55,000 psi
- Compressive Strength: 65,000 to 80,000 psi
- Izod Impact Strength: 6 to 10 ft-lb/in
Thermal Properties
- Glass Transition Temperature (Tg): 130°C to 140°C
- Thermal Conductivity: 0.3 to 0.4 W/m-K
- Coefficient of Thermal Expansion (CTE): 12 to 16 ppm/°C
These properties make CEM-1 PCBs suitable for a wide range of applications, including consumer electronics, industrial control systems, and telecommunications equipment.
Manufacturing Process of CEM-1 PCB
The manufacturing process of CEM-1 PCBs involves several steps, including:
-
Preparing the Substrate: The woven glass fabric is impregnated with the epoxy resin and partially cured to form a prepreg.
-
Lamination: The prepreg is sandwiched between copper foils and subjected to heat and pressure to form a laminated board.
-
Drilling: Holes are drilled into the laminated board to accommodate components and create vias for electrical connections.
-
Plating: The drilled holes are plated with copper to create conductive pathways between layers.
-
Etching: The unwanted copper is removed using a chemical etching process, leaving behind the desired circuit pattern.
-
Solder Mask Application: A solder mask is applied to protect the copper traces and prevent short circuits.
-
Silkscreen Printing: A silkscreen is printed on the PCB to add component labels, logos, and other markings.
-
Surface Finishing: A surface finish, such as HASL (Hot Air Solder Leveling) or ENIG (Electroless Nickel Immersion Gold), is applied to protect the exposed copper and enhance solderability.
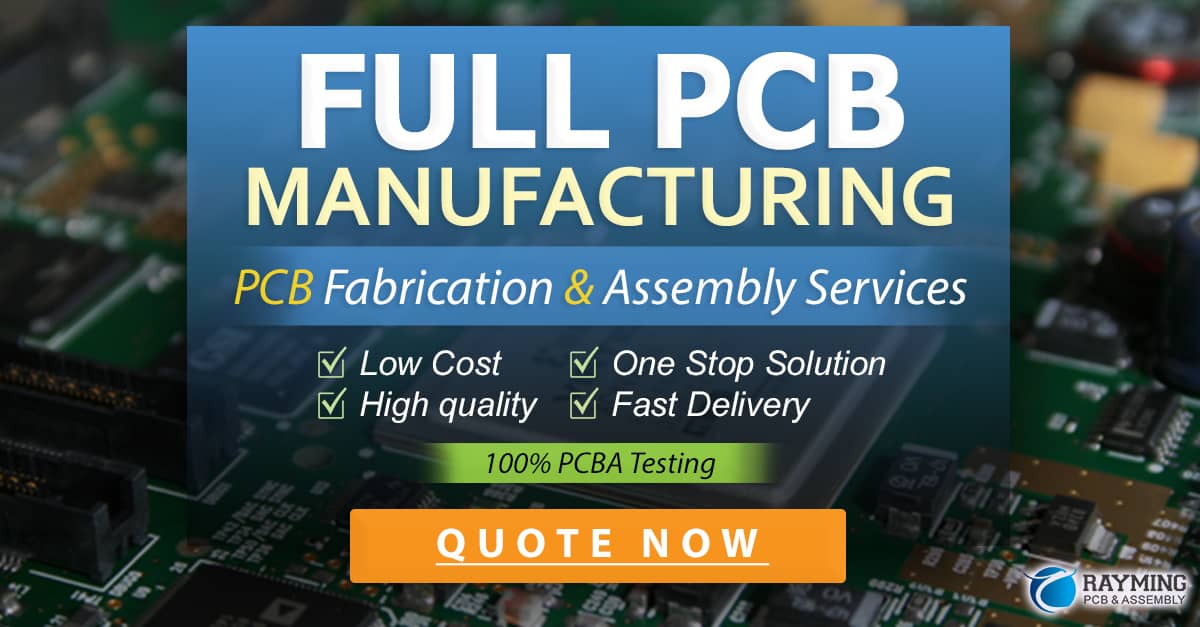
Applications of CEM-1 PCB
CEM-1 PCBs find applications in various industries and electronic products, including:
-
Consumer Electronics: CEM-1 PCBs are widely used in consumer electronic devices, such as smartphones, tablets, laptops, and home appliances.
-
Industrial Control Systems: CEM-1 PCBs are employed in industrial control systems, such as programmable logic controllers (PLCs), human-machine interfaces (HMIs), and automation equipment.
-
Telecommunications Equipment: CEM-1 PCBs are used in telecommunications equipment, such as routers, switches, and modems.
-
Automotive Electronics: CEM-1 PCBs find applications in automotive electronics, such as engine control units (ECUs), infotainment systems, and driver assistance systems.
-
Medical Devices: CEM-1 PCBs are used in medical devices, such as patient monitoring systems, diagnostic equipment, and wearable health devices.
Advantages of CEM-1 PCB
CEM-1 PCBs offer several advantages over other PCB substrate materials, including:
-
Cost-effectiveness: CEM-1 PCBs are less expensive compared to other high-performance substrate materials, such as FR-4.
-
Good Electrical Properties: CEM-1 PCBs provide good electrical insulation and low dielectric losses, making them suitable for high-frequency applications.
-
Mechanical Strength: The woven glass fabric core in CEM-1 PCBs offers excellent mechanical strength and dimensional stability.
-
Environmental Resistance: CEM-1 PCBs exhibit good resistance to moisture, chemicals, and temperature variations.
-
Ease of Processing: CEM-1 PCBs are easy to process and manufacture, enabling faster production times and lower costs.
Limitations of CEM-1 PCB
Despite their numerous advantages, CEM-1 PCBs have some limitations, including:
-
Lower Performance: Compared to high-performance substrate materials like FR-4, CEM-1 PCBs may not be suitable for extremely demanding applications that require exceptional electrical or thermal properties.
-
Limited Layer Count: CEM-1 PCBs are typically limited to a maximum of 4 layers, which may not be sufficient for complex, high-density designs.
-
Susceptibility to Warping: CEM-1 PCBs may be more susceptible to warping during the manufacturing process, especially for larger board sizes.
Frequently Asked Questions (FAQs)
-
Q: What is the difference between CEM-1 and FR-4 PCBs?
A: FR-4 PCBs offer better electrical and thermal properties compared to CEM-1 PCBs, making them suitable for more demanding applications. However, CEM-1 PCBs are more cost-effective and still provide good performance for many general-purpose applications. -
Q: Can CEM-1 PCBs be used for high-frequency applications?
A: Yes, CEM-1 PCBs can be used for high-frequency applications due to their good electrical insulation properties and low dielectric losses. However, for extremely high-frequency applications, other substrate materials like Rogers or Teflon may be more suitable. -
Q: Are CEM-1 PCBs suitable for multilayer designs?
A: CEM-1 PCBs are typically limited to a maximum of 4 layers. For more complex, high-density designs requiring a higher layer count, other substrate materials like FR-4 may be more appropriate. -
Q: How do CEM-1 PCBs compare to other PCB substrate materials in terms of cost?
A: CEM-1 PCBs are generally less expensive compared to other high-performance substrate materials, such as FR-4, Rogers, or Teflon. This makes them a cost-effective solution for many general-purpose electronic applications. -
Q: What surface finishes are commonly used on CEM-1 PCBs?
A: Common surface finishes for CEM-1 PCBs include HASL (Hot Air Solder Leveling), ENIG (Electroless Nickel Immersion Gold), and OSP (Organic Solderability Preservative). The choice of surface finish depends on the specific application requirements, such as solderability, durability, and cost.
Conclusion
CEM-1 PCBs are a popular choice for a wide range of electronic applications due to their cost-effectiveness, good electrical and mechanical properties, and ease of processing. While they may not offer the same level of performance as high-end substrate materials like FR-4, CEM-1 PCBs provide a reliable and economical solution for many general-purpose applications.
By understanding the composition, properties, manufacturing process, and applications of CEM-1 PCBs, engineers and designers can make informed decisions when selecting the appropriate substrate material for their projects. As technology continues to advance, it is likely that CEM-1 PCBs will remain a valuable option in the world of printed circuit board manufacturing.
0 Comments