Understanding the Need for Backdrilling PCB
As technology advances and electronic devices become more sophisticated, the demand for high-speed PCBs has increased significantly. These PCBs are designed to handle high-frequency signals and maintain signal integrity throughout the board. However, one of the challenges faced in high-speed PCB design is the presence of unwanted signal reflections, which can lead to signal degradation and compromise the overall performance of the device.
Signal Reflections in High-Speed PCBs
When a high-speed signal travels through a via in a PCB, it encounters a change in impedance at the junction between the via and the surrounding dielectric material. This impedance mismatch causes a portion of the signal to reflect back, creating what is known as a signal reflection or stub reflection.
These signal reflections can have several negative effects on the performance of the PCB:
-
Signal Integrity Degradation: The reflected signals interfere with the original signal, causing distortion and reducing the overall signal quality.
-
Increased Crosstalk: Signal reflections can couple with adjacent traces, leading to increased crosstalk and noise on the board.
-
Timing Issues: Reflected signals can introduce timing delays and jitter, affecting the synchronization of various components on the PCB.
To mitigate these issues and ensure optimal signal integrity, PCB designers and manufacturers employ the technique of backdrilling.
What is Backdrilling in PCB Fabrication?
Backdrilling, also known as controlled depth drilling or stub drilling, is a process used to remove the unused portion of a via in a multi-layer PCB. By removing the excess via stub, backdrilling helps to minimize signal reflections and improve the overall signal integrity of the board.
The Backdrilling Process
The backdrilling process involves the following steps:
-
Identifying Vias for Backdrilling: The PCB designer identifies the vias that require backdrilling based on the signal integrity analysis and the desired performance characteristics of the board.
-
Determining Backdrilling Depth: The depth of backdrilling is calculated based on the via length and the desired stub length. The goal is to remove as much of the unused via stub as possible without compromising the integrity of the via.
-
Drilling from the Back Side: Using a specialized drill bit, the backdrilling process is performed from the back side of the PCB. The drill bit is carefully controlled to ensure that it stops at the predetermined depth, removing only the unused portion of the via.
-
Cleaning and Inspection: After backdrilling, the PCB undergoes cleaning to remove any debris or burrs created during the drilling process. The board is then inspected to ensure that the backdrilling has been performed accurately and that the vias meet the specified requirements.
Advantages of Backdrilling PCB
Backdrilling offers several key advantages in PCB fabrication:
-
Improved Signal Integrity: By removing the unused via stubs, backdrilling significantly reduces signal reflections and improves the overall signal integrity of the PCB. This results in cleaner and more reliable high-speed signal transmission.
-
Reduced Crosstalk: With the elimination of stub reflections, backdrilling helps to minimize crosstalk between adjacent traces, reducing noise and interference on the board.
-
Enhanced Timing Performance: Backdrilling reduces the timing delays and jitter caused by signal reflections, ensuring better synchronization and overall timing performance of the PCB.
-
Increased Bandwidth: By improving signal integrity and reducing reflections, backdrilling enables PCBs to support higher frequencies and increased bandwidth, meeting the demands of modern high-speed applications.
-
Cost-Effective Solution: Compared to other signal integrity enhancement techniques, such as using higher-quality dielectric materials or increasing the number of layers, backdrilling is a cost-effective solution that can be implemented without significant changes to the PCB design or manufacturing process.
Backdrilling Considerations and Best Practices
While backdrilling offers significant benefits, there are several considerations and best practices to keep in mind when implementing this technique in PCB fabrication:
-
Material Selection: The choice of PCB material is crucial for successful backdrilling. The material should have good drilling properties and be able to withstand the backdrilling process without delamination or other damage.
-
Via Design: Via design plays a critical role in the effectiveness of backdrilling. The via diameter, pad size, and hole size should be carefully selected to ensure proper backdrilling and signal integrity.
-
Depth Control: Accurate depth control is essential during the backdrilling process. Overdrilling can damage the via and compromise the integrity of the board, while underdrilling may leave excess stub length, reducing the effectiveness of the technique.
-
Drill Bit Selection: The choice of drill bit is important for achieving precise and clean backdrilling. High-quality, sharp drill bits with the appropriate diameter and geometry should be used to minimize debris and ensure accurate drilling.
-
Cleaning and Inspection: Thorough cleaning and inspection after backdrilling are crucial to remove any debris or burrs and verify the accuracy of the drilling process. This ensures that the PCB meets the required specifications and performs optimally.
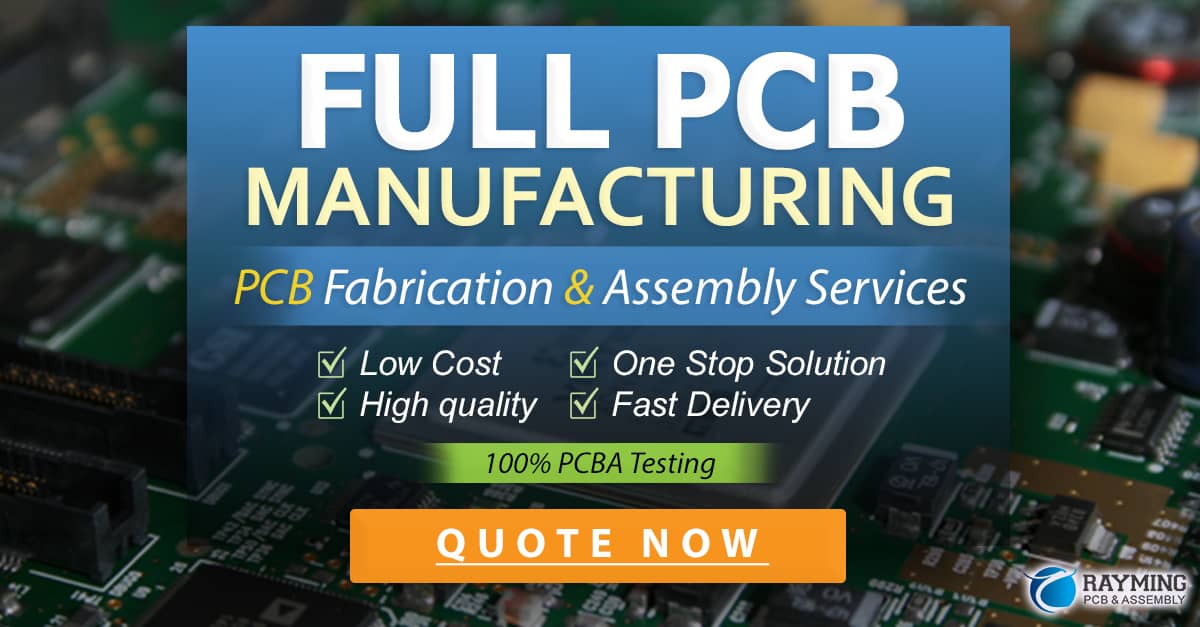
Backdrilling in High-Speed PCB Applications
Backdrilling finds extensive use in various high-speed PCB applications where signal integrity is of utmost importance. Some common applications include:
-
High-Speed Digital Systems: Backdrilling is widely used in high-speed digital systems, such as high-performance computing, data centers, and telecommunications equipment, where signal integrity is critical for reliable data transmission.
-
RF and Microwave Circuits: In radio frequency (RF) and microwave circuits, backdrilling is employed to minimize signal reflections and ensure proper impedance matching, enabling efficient and accurate signal propagation.
-
Automotive Electronics: With the increasing complexity of automotive electronics, backdrilling is used in PCBs for advanced driver assistance systems (ADAS), infotainment systems, and other high-speed automotive applications to ensure reliable and robust performance.
-
Medical Devices: In medical devices, such as imaging systems and diagnostic equipment, backdrilling is utilized to maintain signal integrity and avoid any signal distortions that could affect the accuracy and reliability of the devices.
-
Aerospace and Defense: Backdrilling is employed in PCBs for aerospace and defense applications, where high-speed communication, radar systems, and avionics require superior signal integrity and reliability.
Frequently Asked Questions (FAQ)
-
What is the purpose of backdrilling in PCB fabrication?
Backdrilling is used to remove the unused portion of a via in a multi-layer PCB to minimize signal reflections and improve signal integrity. -
How does backdrilling improve signal integrity?
By removing the unused via stubs, backdrilling reduces signal reflections, minimizes crosstalk, and enhances timing performance, resulting in cleaner and more reliable high-speed signal transmission. -
Is backdrilling suitable for all types of PCBs?
Backdrilling is primarily used in high-speed PCBs where signal integrity is critical. It may not be necessary for low-speed or general-purpose PCBs. -
What are the key considerations when implementing backdrilling?
Material selection, via design, depth control, drill bit selection, and thorough cleaning and inspection are important considerations when implementing backdrilling in PCB fabrication. -
Can backdrilling be performed on existing PCBs?
Backdrilling is typically performed during the PCB fabrication process and is not suitable for existing PCBs. It is important to incorporate backdrilling requirements into the PCB design from the beginning.
Conclusion
Backdrilling is a vital technique in PCB fabrication that addresses the challenges of signal integrity in high-speed PCBs. By removing the unused portion of vias, backdrilling minimizes signal reflections, reduces crosstalk, and enhances timing performance. This results in cleaner and more reliable high-speed signal transmission, making backdrilling an essential tool in the design and manufacturing of advanced electronic devices.
As technology continues to evolve and the demand for high-speed electronics grows, the importance of backdrilling in PCB fabrication will only increase. By understanding the principles, benefits, and best practices of backdrilling, PCB designers and manufacturers can ensure the production of high-quality, high-performance PCBs that meet the stringent requirements of today’s complex electronic systems.
0 Comments