What is the Purpose of PCB Etchback?
The primary purpose of PCB etchback is to ensure optimal performance and reliability of the printed circuit board by:
- Improving adhesion between copper and dielectric layers
- Enhancing signal integrity by reducing impedance discontinuities
- Increasing the reliability of copper interconnects and vias
- Facilitating the deposition of subsequent layers in the PCB stack-up
Advantages of PCB Etchback
PCB etchback offers several advantages that contribute to the overall performance and reliability of the printed circuit board:
Improved Adhesion
By selectively removing a portion of the dielectric material around the copper features, PCB etchback creates a rough surface that promotes better adhesion between the copper and the dielectric layers. This improved adhesion reduces the risk of delamination and enhances the mechanical stability of the PCB.
Enhanced Signal Integrity
PCB etchback helps to maintain consistent impedance throughout the copper interconnects and vias by creating a uniform dielectric thickness surrounding the copper features. This uniformity minimizes impedance discontinuities, which can cause signal reflections and distortions, thereby improving the overall signal integrity of the PCB.
Increased Reliability
The etchback process strengthens the mechanical connection between the copper features and the dielectric layers, making the PCB more resistant to thermal and mechanical stresses. This increased reliability is particularly important for high-density PCBs and those used in harsh environmental conditions.
Facilitates Subsequent Layer Deposition
By creating a controlled depth for the copper features, PCB etchback ensures a smooth and consistent surface for the deposition of subsequent layers in the PCB stack-up. This uniform surface promotes better adhesion and reduces the risk of defects in the final product.
Applications of PCB Etchback
PCB etchback is widely used in various applications that require high-performance and reliable printed circuit boards:
- High-speed digital circuits
- RF and microwave circuits
- Aerospace and defense electronics
- Medical devices
- Automotive electronics
- Industrial control systems
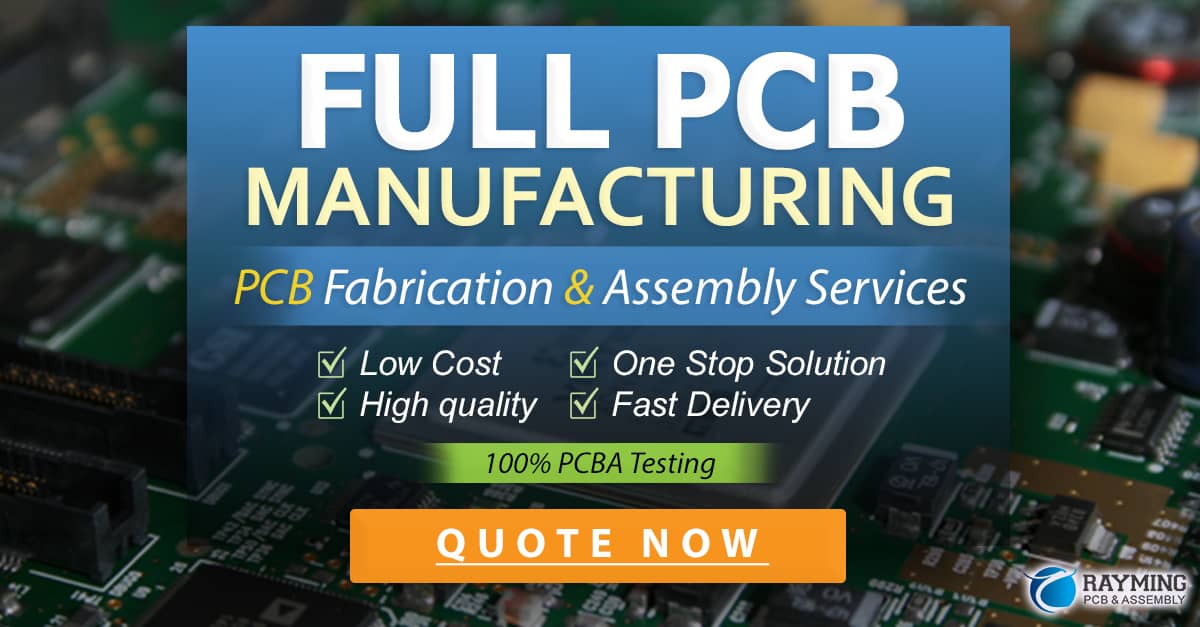
Methods of PCB Etchback
There are several methods used to achieve PCB etchback, each with its own advantages and limitations:
Chemical Etchback
Chemical etchback involves using a chemical solution to selectively remove the dielectric material around the copper features. The most common chemical etchants used for this process are potassium permanganate (KMnO4) and sodium persulfate (Na2S2O8). The chemical etchback process typically consists of the following steps:
- Cleaning the PCB surface
- Applying a photoresist mask to protect the areas that should not be etched
- Immersing the PCB in the chemical etchant solution
- Removing the photoresist mask
- Cleaning and drying the PCB
Advantages of chemical etchback include its relatively low cost and the ability to process multiple PCBs simultaneously. However, it can be challenging to achieve a consistent etch depth across the entire PCB surface, and the process may require careful control of the etchant concentration and temperature.
Plasma Etchback
Plasma etchback uses a plasma gas to remove the dielectric material around the copper features. The plasma is generated using a high-frequency electric field in a vacuum chamber, and the PCB is exposed to the reactive plasma species. The most common gases used for plasma etchback are oxygen (O2) and tetrafluoromethane (CF4).
The plasma etchback process typically consists of the following steps:
- Loading the PCB into the vacuum chamber
- Pumping down the chamber to create a vacuum
- Introducing the plasma gas and igniting the plasma
- Exposing the PCB to the reactive plasma species for a controlled duration
- Venting the chamber and removing the PCB
Advantages of plasma etchback include its high precision, consistency, and the ability to achieve uniform etch depths across the entire PCB surface. However, the process requires specialized equipment and may have a higher cost compared to chemical etchback.
Laser Etchback
Laser etchback uses a high-energy laser beam to selectively remove the dielectric material around the copper features. The laser beam is focused on the PCB surface, and the dielectric material is vaporized or ablated by the intense heat generated by the laser.
The laser etchback process typically consists of the following steps:
- Designing the laser etchback pattern using CAD software
- Setting up the laser system and aligning the PCB
- Exposing the PCB to the laser beam according to the designed pattern
- Cleaning the PCB to remove any debris generated during the process
Advantages of laser etchback include its high precision, flexibility in creating complex etchback patterns, and the ability to achieve consistent etch depths. However, the process requires specialized laser equipment and may have a higher cost compared to other etchback methods.
Comparison of PCB Etchback Methods
Method | Advantages | Disadvantages |
---|---|---|
Chemical Etchback | – Relatively low cost – Can process multiple PCBs simultaneously |
– Challenging to achieve consistent etch depth – Requires careful control of etchant concentration and temperature |
Plasma Etchback | – High precision and consistency – Uniform etch depths across the PCB surface |
– Requires specialized equipment – Higher cost compared to chemical etchback |
Laser Etchback | – High precision – Flexibility in creating complex etchback patterns – Consistent etch depths |
– Requires specialized laser equipment – Higher cost compared to other methods |
Frequently Asked Questions (FAQ)
1. What is the difference between PCB etchback and PCB Etching?
PCB etchback is a process that selectively removes the dielectric material around the copper features, while PCB etching is the process of removing unwanted copper from the PCB surface to create the desired circuit pattern.
2. Is PCB etchback necessary for all PCBs?
No, PCB etchback is not necessary for all PCBs. It is typically used for high-performance, high-reliability applications where signal integrity, adhesion, and mechanical stability are critical.
3. Can PCB etchback be performed on both rigid and flexible PCBs?
Yes, PCB etchback can be performed on both rigid and flexible PCBs, although the specific methods and parameters may vary depending on the material properties and requirements of each type of PCB.
4. How does PCB etchback affect the impedance of the copper interconnects?
PCB etchback helps to maintain consistent impedance throughout the copper interconnects by creating a uniform dielectric thickness surrounding the copper features. This uniformity minimizes impedance discontinuities, which can cause signal reflections and distortions.
5. What are the safety considerations when performing PCB etchback?
When performing PCB etchback, it is essential to follow proper safety guidelines, such as wearing appropriate personal protective equipment (PPE), handling chemicals and gases with care, and ensuring adequate ventilation in the work area. Operators should also be trained in the safe use of the specific equipment and processes involved in PCB etchback.
Conclusion
PCB etchback is a critical process in the manufacturing of high-performance, reliable printed circuit boards. By selectively removing the dielectric material around the copper features, etchback improves adhesion, signal integrity, and mechanical stability of the PCB. The three primary methods of PCB etchback – chemical, plasma, and laser – each offer unique advantages and limitations, and the choice of method depends on the specific requirements and constraints of the application. As PCB designs continue to push the boundaries of performance and complexity, the importance of PCB etchback in ensuring optimal functionality and reliability will only continue to grow.
0 Comments