Understanding Flexible PCBs and Their Advantages
Flexible PCBs, also known as flex circuits or flexible printed circuit boards, are a type of printed circuit board that can bend and conform to various shapes. Unlike traditional rigid PCBs, flexible PCBs are made using a flexible substrate material, such as polyimide or polyester, which allows them to be bent, twisted, and folded without damaging the circuitry.
Flexible PCBs offer several advantages over rigid PCBs, including:
- Space savings: Flexible PCBs can be folded and bent to fit into smaller spaces, making them ideal for compact electronic devices.
- Weight reduction: Due to their thin and lightweight nature, flexible PCBs can significantly reduce the overall weight of electronic products.
- Increased reliability: Flexible PCBs are more resistant to vibration and shock, which can improve the reliability of electronic devices in harsh environments.
- Enhanced design flexibility: The ability to bend and fold flexible PCBs allows for more creative and efficient product designs.
- Reduced assembly costs: Flexible PCBs can simplify the assembly process by reducing the number of connectors and wires needed, leading to lower assembly costs.
Types of Flexible PCBs
There are several types of flexible PCBs, each with its own unique characteristics and applications:
- Single-sided flex PCBs: These have conductive circuitry on only one side of the flexible substrate and are the most basic and cost-effective type of flexible PCB.
- Double-sided flex PCBs: These have conductive circuitry on both sides of the flexible substrate, allowing for more complex designs and higher component density.
- Multi-layer flex PCBs: These consist of multiple layers of flexible substrates with conductive circuitry, offering the highest level of design complexity and component density.
- Rigid-flex PCBs: These combine rigid and flexible PCB sections, allowing for the integration of both types of circuits into a single board.
Factors Affecting Flexible PCB Quotes
When requesting quotes for flexible PCBs, several factors can influence the price:
- Material selection: The choice of flexible substrate material, such as polyimide or polyester, can impact the cost of the flexible PCB.
- Number of layers: The more layers a flexible PCB has, the higher the manufacturing cost.
- Circuit complexity: Complex circuit designs with high component density and fine trace widths will generally result in higher quotes.
- Quantity: Higher order quantities often lead to lower per-unit costs due to economies of scale.
- Turnaround time: Faster turnaround times may result in higher quotes, as manufacturers may need to prioritize your order over others.
- Certifications and standards: Meeting specific industry certifications or standards, such as UL or IPC, can add to the cost of flexible PCBs.
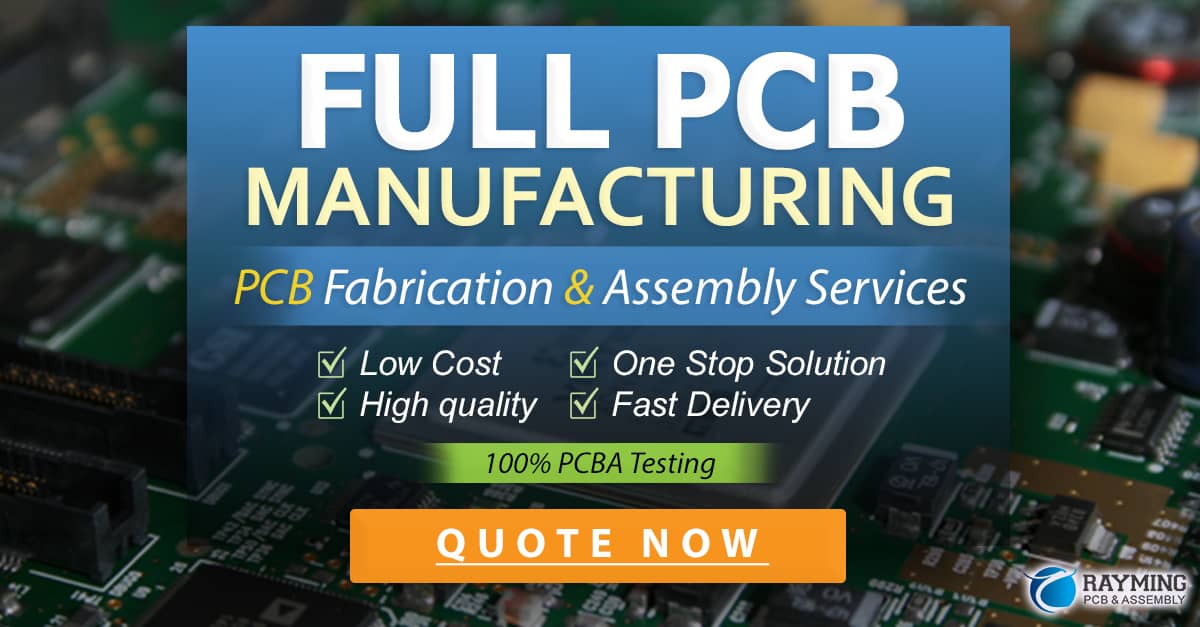
Obtaining Flexible PCB Quotes
To get accurate and competitive quotes for your flexible PCB project, follow these steps:
- Create a detailed specification document: Include information such as the number of layers, material requirements, circuit complexity, and any special requirements (e.g., impedance control, via size, etc.).
- Generate fabrication files: Provide the necessary design files, such as Gerber files, drill files, and a bill of materials (BOM), to the PCB manufacturer.
- Research and select potential manufacturers: Look for manufacturers with experience in producing flexible PCBs and a good reputation for quality and reliability.
- Request quotes from multiple manufacturers: Provide your specification document and fabrication files to several manufacturers to obtain competitive quotes.
- Review and compare quotes: Carefully review each quote, considering factors such as price, turnaround time, and any additional services offered (e.g., assembly, testing, etc.).
- Negotiate and finalize the order: Once you have selected a manufacturer, discuss any final details and negotiate the terms of your order, including payment terms and delivery dates.
Flexible PCB Design Considerations
To ensure the best performance and reliability of your flexible PCBs, keep the following design considerations in mind:
- Bend radius: The minimum bend radius of a flexible PCB depends on factors such as the substrate material, number of layers, and copper thickness. Consult with your manufacturer to determine the appropriate bend radius for your design.
- Strain relief: Incorporate strain relief features, such as stiffeners or anchors, to prevent excessive stress on the flexible PCB during bending and flexing.
- Copper weight: Choose the appropriate copper weight for your flexible PCB based on the current carrying requirements and the desired flexibility.
- Trace width and spacing: Use appropriate trace widths and spacing to ensure reliable electrical performance and minimize the risk of short circuits or signal integrity issues.
- Coverlay and solder mask: Apply coverlay and solder mask to protect the circuitry and improve the durability of the flexible PCB.
Flexible PCB Manufacturing Process
The manufacturing process for flexible PCBs involves several key steps:
- Material selection: The appropriate flexible substrate material is chosen based on the requirements of the application.
- Copper lamination: Copper foil is laminated onto the flexible substrate using heat and pressure.
- Patterning: The desired circuit pattern is transferred onto the copper layer using photolithography and etching processes.
- Drilling: Any necessary holes, such as vias or through-holes, are drilled into the flexible PCB.
- Plating: Additional copper plating is applied to the drilled holes and traces to improve conductivity and durability.
- Solder mask and coverlay application: Solder mask and coverlay are applied to protect the circuitry and improve the appearance of the flexible PCB.
- Surface finishing: The exposed copper areas are finished with a protective coating, such as ENIG (electroless nickel immersion gold) or OSP (organic solderability preservative), to prevent oxidation and enhance solderability.
- Cutting and formatting: The flexible PCB panel is cut and formatted to the desired shape and size using a variety of methods, such as die-cutting, laser cutting, or routing.
Applications of Flexible PCBs
Flexible PCBs find applications in a wide range of industries and products, including:
- Consumer electronics: Smartphones, wearables, and other compact devices often utilize flexible PCBs to save space and improve reliability.
- Medical devices: Flexible PCBs are used in medical devices such as hearing aids, pacemakers, and implantable sensors, where their flexibility and compact size are essential.
- Automotive electronics: Flexible PCBs are used in various automotive applications, such as instrument clusters, infotainment systems, and sensors, due to their resistance to vibration and harsh environments.
- Aerospace and defense: The lightweight and compact nature of flexible PCBs makes them ideal for use in aerospace and defense applications, such as satellites, unmanned aerial vehicles (UAVs), and military communication systems.
- Industrial automation: Flexible PCBs are used in industrial automation applications, such as robotics and machine vision systems, where their flexibility and durability are valuable assets.
Choosing the Right Flexible PCB Manufacturer
Selecting the right flexible PCB manufacturer is crucial to the success of your project. Consider the following factors when evaluating potential manufacturers:
- Experience and expertise: Look for manufacturers with a proven track record of producing high-quality flexible PCBs and experience in your specific industry or application.
- Quality control and certifications: Ensure that the manufacturer has robust quality control processes in place and holds relevant certifications, such as ISO 9001, UL, or IPC.
- Technical support and communication: Choose a manufacturer that offers responsive technical support and maintains clear communication throughout the project.
- Manufacturing capabilities: Verify that the manufacturer has the necessary equipment and capabilities to produce your specific flexible PCB design, including the ability to handle your required materials, layer counts, and feature sizes.
- Lead times and pricing: Consider the manufacturer’s lead times and pricing structure to ensure they align with your project timeline and budget.
Tips for Optimizing Flexible PCB Costs
To help optimize the cost of your flexible PCB project, consider the following tips:
- Simplify your design: Where possible, simplify your circuit design to reduce complexity and minimize the number of layers required.
- Standardize materials and processes: Using standard materials and processes can often result in lower costs compared to custom or specialized options.
- Consider panelization: Panelizing your flexible PCBs can help reduce manufacturing costs by allowing multiple boards to be produced on a single panel.
- Order in bulk: Ordering larger quantities of flexible PCBs can often result in lower per-unit costs due to economies of scale.
- Plan ahead: Allowing for longer lead times can help reduce manufacturing costs, as rushed orders often incur additional fees.
Future Trends in Flexible PCBs
As technology continues to advance, several trends are shaping the future of flexible PCBs:
- Increased adoption of stretchable electronics: Stretchable flexible PCBs, which can extend and contract without losing functionality, are gaining traction in applications such as wearables and medical devices.
- Integration of printed electronics: The integration of printed electronics, such as conductive inks and pastes, with flexible PCBs is opening up new possibilities for low-cost, disposable electronic devices.
- Advancements in materials: Ongoing research and development of new flexible substrate materials, such as thermoplastic polyurethane (TPU) and liquid crystal polymer (LCP), are expanding the range of applications for flexible PCBs.
- Growth in the Internet of Things (IoT): The proliferation of IoT devices is driving demand for compact, flexible, and reliable electronic circuits, further fueling the growth of the flexible PCB market.
Conclusion
Flexible PCBs offer numerous advantages over traditional rigid PCBs, including space savings, weight reduction, increased reliability, and enhanced design flexibility. When seeking quotes for flexible PCBs, it is essential to consider factors such as material selection, circuit complexity, and manufacturing capabilities. By carefully evaluating potential manufacturers and optimizing your design for cost-effectiveness, you can ensure the success of your flexible PCB project and take advantage of the latest trends and advancements in this exciting field.
Frequently Asked Questions (FAQ)
-
Q: What is the minimum bend radius for a flexible PCB?
A: The minimum bend radius for a flexible PCB depends on factors such as the substrate material, number of layers, and copper thickness. Generally, the minimum bend radius is about 6 times the total thickness of the flexible PCB. However, it is best to consult with your manufacturer to determine the appropriate bend radius for your specific design. -
Q: Can flexible PCBs be used in high-temperature environments?
A: Yes, certain types of flexible PCBs can be designed to withstand high-temperature environments. Polyimide, a common flexible substrate material, has a high glass transition temperature and can maintain its properties in temperatures up to 300°C. However, the specific temperature range will depend on the materials used and the design of the flexible PCB. -
Q: Are flexible PCBs more expensive than rigid PCBs?
A: In general, flexible PCBs tend to be more expensive than rigid PCBs due to the specialized materials and manufacturing processes involved. However, the cost difference can be offset by the benefits of using flexible PCBs, such as space savings, weight reduction, and improved reliability. Additionally, the cost of flexible PCBs can be optimized through careful design and manufacturing choices. -
Q: What is the typical turnaround time for flexible PCB manufacturing?
A: The turnaround time for flexible PCB manufacturing can vary depending on factors such as the complexity of the design, the chosen manufacturer, and the order quantity. Typical turnaround times range from 1-2 weeks for prototypes or small orders to 4-6 weeks for larger production runs. However, some manufacturers may offer expedited services for an additional fee. -
Q: Can flexible PCBs be assembled using standard SMT processes?
A: Yes, flexible PCBs can be assembled using standard surface mount technology (SMT) processes, such as solder paste printing, component placement, and reflow soldering. However, some additional considerations may be necessary, such as using low-temperature solder paste to prevent damage to the flexible substrate or incorporating strain relief features to protect components during flexing.
Factor | Impact on Flexible PCB Quote |
---|---|
Material Selection | The choice of substrate material (e.g., polyimide, polyester) can affect the cost of the flexible PCB. |
Number of Layers | More layers in a flexible PCB design will generally result in higher manufacturing costs. |
Circuit Complexity | Complex designs with high component density and fine trace widths will often lead to higher quotes. |
Quantity | Higher order quantities can result in lower per-unit costs due to economies of scale. |
Turnaround Time | Faster turnaround times may incur additional fees, as manufacturers prioritize rush orders. |
Certifications and Standards | Meeting specific industry certifications (e.g., UL, IPC) can add to the cost of flexible PCBs. |
Flexible PCB Type | Characteristics and Applications |
---|---|
Single-sided Flex PCBs | – Conductive circuitry on one side of the substrate – Most basic and cost-effective type – Suitable for simple designs and low-density applications |
Double-sided Flex PCBs | – Conductive circuitry on both sides of the substrate – Allows for more complex designs and higher component density – Commonly used in consumer electronics and medical devices |
Multi-layer Flex PCBs | – Multiple layers of flexible substrates with conductive circuitry – Offers the highest level of design complexity and component density – Used in advanced applications such as aerospace and defense |
Rigid-flex PCBs | – Combines rigid and flexible PCB sections – Allows for the integration of both types of circuits into a single board – Ideal for applications requiring both flexibility and structural support |
0 Comments