The Importance of PCBs in the Automotive Industry
PCBs are essential components in modern automobiles, enabling the integration of complex electronic systems that enhance vehicle performance, safety, and user experience. Some of the critical applications of PCBs in the automotive industry include:
-
Engine Control Units (ECUs): PCBs are used in ECUs to manage and optimize engine performance, fuel efficiency, and emissions control.
-
Infotainment Systems: PCBs enable the integration of advanced infotainment features, such as touchscreens, navigation, and audio systems.
-
Advanced Driver Assistance Systems (ADAS): PCBs are crucial for implementing ADAS features, such as adaptive cruise control, lane departure warnings, and automatic emergency braking.
-
Body Electronics: PCBs are used in various body electronic systems, including lighting control, climate control, and power windows.
-
Hybrid and Electric Vehicles: PCBs play a vital role in the power management and control systems of hybrid and electric vehicles.
Key Considerations for Selecting a PCB Manufacturer
When choosing a PCB manufacturer for automotive applications, several key factors must be considered to ensure the highest quality, reliability, and compliance with industry standards. These factors include:
-
Automotive Certifications: Ensure that the PCB manufacturer holds relevant automotive certifications, such as IATF 16949 and ISO 26262, which demonstrate their commitment to quality and safety standards.
-
Manufacturing Capabilities: Assess the manufacturer’s ability to produce PCBs with the required complexity, layer count, and material specifications for automotive applications.
-
Testing and Validation: Verify that the manufacturer has comprehensive testing and validation processes in place to ensure the reliability and performance of the PCBs under various environmental conditions.
-
Supply Chain Management: Consider the manufacturer’s supply chain management practices, including their ability to source high-quality raw materials and manage inventory to meet production demands.
-
Technical Support: Evaluate the level of technical support offered by the manufacturer, including design assistance, prototyping, and troubleshooting services.
Leading PCB Manufacturers for the Automotive Industry
Several PCB manufacturers have established themselves as leaders in serving the automotive industry. These companies offer a range of services and capabilities to meet the stringent requirements of Automotive PCB manufacturing. Some of the top PCB manufacturers for the automotive industry include:
1. TTM Technologies
TTM Technologies is a global leader in PCB manufacturing, offering advanced solutions for the automotive industry. They provide a wide range of PCB technologies, including high-density interconnect (HDI), flexible, and rigid-flex PCBs. TTM Technologies holds IATF 16949 certification and has a strong focus on quality and reliability.
2. Meiko Electronics
Meiko Electronics is a Japanese PCB manufacturer with a global presence, serving the automotive industry with high-quality PCBs. They offer a variety of PCB technologies, such as multi-layer, HDI, and flexible PCBs. Meiko Electronics is IATF 16949 certified and has a reputation for excellence in automotive PCB manufacturing.
3. Unimicron Technology
Unimicron Technology is a Taiwanese PCB manufacturer with a significant presence in the automotive industry. They provide a comprehensive range of PCB solutions, including multi-layer, HDI, and flexible PCBs. Unimicron Technology holds IATF 16949 certification and has a strong commitment to quality and innovation.
4. Chin Poon Industrial
Chin Poon Industrial is a leading PCB manufacturer based in Taiwan, serving the automotive industry with advanced PCB solutions. They offer a wide range of PCB technologies, such as multi-layer, HDI, and flexible PCBs. Chin Poon Industrial is IATF 16949 certified and has a strong focus on research and development to meet the evolving needs of the automotive industry.
5. Nippon Mektron
Nippon Mektron is a Japanese PCB manufacturer with a significant presence in the automotive industry. They provide a comprehensive range of PCB solutions, including multi-layer, HDI, and flexible PCBs. Nippon Mektron holds IATF 16949 certification and has a strong emphasis on quality and reliability in automotive PCB manufacturing.
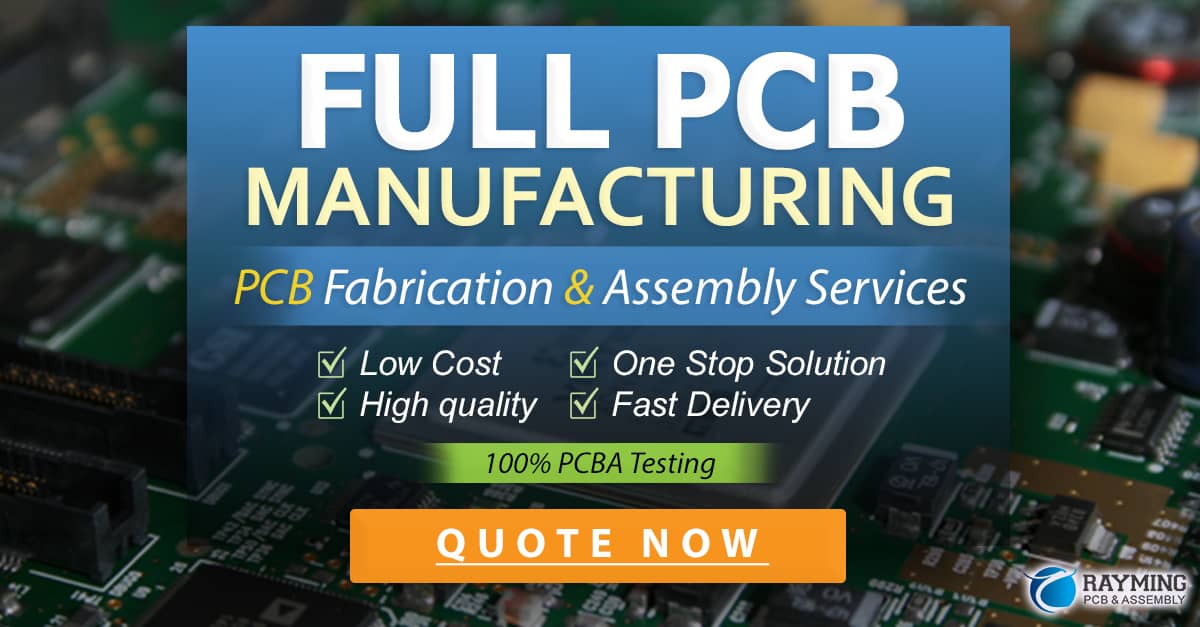
Automotive PCB Manufacturing Processes
To ensure the highest quality and reliability of PCBs for automotive applications, manufacturers employ specialized processes and techniques. Some of the key processes involved in automotive PCB manufacturing include:
1. Design and Prototyping
The design and prototyping phase is crucial for developing PCBs that meet the specific requirements of automotive applications. Manufacturers work closely with automotive engineers to create PCB designs that optimize performance, reliability, and manufacturability. Advanced software tools, such as computer-aided design (CAD) and simulation tools, are used to validate the design and ensure compliance with industry standards.
2. Material Selection
Material selection is a critical aspect of automotive PCB manufacturing, as the PCBs must withstand harsh environmental conditions and meet stringent safety requirements. Manufacturers use high-quality, automotive-grade materials, such as FR-4, polyimide, and high-temperature laminates, to ensure the durability and reliability of the PCBs. The choice of materials depends on the specific application, operating conditions, and performance requirements of the automotive system.
3. Fabrication
The fabrication process involves the actual manufacturing of the PCBs, including the creation of conductive patterns, drilling of holes, and lamination of multiple layers. Automotive PCB manufacturers use advanced equipment and techniques to ensure precise and consistent fabrication of complex PCB designs. This includes the use of high-speed drilling machines, laser drilling, and advanced lamination processes to achieve the required level of accuracy and reliability.
4. Assembly
PCB Assembly involves the placement and soldering of electronic components onto the fabricated PCB. Automotive PCB manufacturers employ automated assembly processes, such as surface mount technology (SMT) and through-hole technology (THT), to ensure accurate and efficient assembly of components. Advanced inspection techniques, such as automated optical inspection (AOI) and X-ray inspection, are used to detect any defects or issues during the assembly process.
5. Testing and Validation
Rigorous testing and validation processes are essential for ensuring the quality and reliability of automotive PCBs. Manufacturers conduct a range of tests to verify the performance, functionality, and durability of the PCBs under various environmental conditions. These tests include thermal cycling, vibration testing, shock testing, and electrical testing. Manufacturers also employ advanced testing equipment, such as flying probe testers and in-circuit testers, to detect any faults or anomalies in the PCBs.
Automotive PCB Design Considerations
Designing PCBs for automotive applications requires careful consideration of various factors to ensure optimal performance, reliability, and safety. Some of the key design considerations for automotive PCBs include:
1. Signal Integrity
Signal integrity is critical in automotive PCBs, as the electronic systems must operate reliably in noisy and harsh environments. Designers must consider factors such as impedance control, crosstalk, and electromagnetic interference (EMI) when designing PCBs to ensure the integrity of the signals. Techniques such as proper grounding, shielding, and the use of differential signaling can help mitigate signal integrity issues.
2. Thermal Management
Automotive PCBs are often exposed to extreme temperature variations and must be designed to dissipate heat effectively. Thermal management is crucial to prevent overheating and ensure the reliable operation of electronic components. Designers must consider factors such as component placement, copper weight, and the use of thermal vias to optimize heat dissipation. Thermal simulations and analysis tools are used to validate the thermal performance of the PCB design.
3. Vibration and Shock Resistance
Automotive PCBs are subjected to constant vibration and potential shock loads during vehicle operation. The PCB design must account for these mechanical stresses to prevent damage to the components and ensure reliable performance. Designers must consider factors such as component placement, mounting techniques, and the use of reinforced materials to enhance the vibration and shock resistance of the PCBs. Finite element analysis (FEA) tools are used to simulate and optimize the mechanical performance of the PCB design.
4. Size and Weight Optimization
With the increasing complexity of automotive electronic systems, PCB designers must strive to optimize the size and weight of the PCBs to fit within the limited space available in vehicles. Miniaturization techniques, such as HDI and embedded component technologies, are used to reduce the size and weight of automotive PCBs. Designers also consider the use of lightweight materials and innovative packaging solutions to further optimize the PCB design.
5. Manufacturability and Cost
Designing automotive PCBs requires a balance between performance, reliability, and cost-effectiveness. Designers must consider the manufacturability of the PCB design to ensure efficient and cost-effective production. This includes factors such as design for manufacturing (DFM) principles, component selection, and the use of standardized processes. Collaboration between designers and manufacturers is essential to optimize the PCB design for manufacturability and cost-effectiveness.
Future Trends in Automotive PCB Manufacturing
The automotive industry is undergoing significant transformations, driven by the adoption of advanced technologies and the push towards electrification and autonomous driving. These trends are shaping the future of automotive PCB manufacturing, presenting new challenges and opportunities for manufacturers. Some of the key future trends in automotive PCB manufacturing include:
1. Advanced Driver Assistance Systems (ADAS) and Autonomous Driving
The increasing adoption of ADAS features and the development of autonomous driving technologies are driving the demand for more complex and high-performance PCBs. These systems require PCBs with advanced signal processing capabilities, high-speed data transmission, and robust reliability. Manufacturers must adapt their PCB design and manufacturing processes to meet the demanding requirements of ADAS and autonomous driving applications.
2. Electrification and High-Voltage Systems
The shift towards electric vehicles (EVs) is accelerating the need for high-voltage PCBs capable of handling the increased power requirements of EV systems. Manufacturers must develop specialized PCB solutions that can withstand high voltages, ensure electrical safety, and provide efficient power management. This includes the use of advanced materials, such as ceramic substrates and high-voltage laminates, and the development of innovative PCB designs for EV applications.
3. Miniaturization and High-Density Interconnect (HDI)
The trend towards miniaturization and the integration of more electronic features into vehicles is driving the demand for HDI PCBs. HDI technology enables the fabrication of high-density, multi-layer PCBs with fine pitch traces and micro vias. Manufacturers must invest in advanced HDI manufacturing capabilities to meet the increasing complexity and density requirements of automotive PCBs.
4. Flexible and Stretchable Electronics
The integration of flexible and stretchable electronics into automotive systems is gaining traction, particularly in applications such as sensors, displays, and wearable devices. Flexible and stretchable PCBs offer the ability to conform to irregular shapes and withstand mechanical deformations. Manufacturers must develop specialized materials, fabrication processes, and assembly techniques to enable the production of reliable and durable flexible and stretchable PCBs for automotive applications.
5. Sustainability and Eco-Friendly Manufacturing
The automotive industry is increasingly focusing on sustainability and reducing its environmental impact. This trend is also influencing automotive PCB manufacturing, with a growing emphasis on eco-friendly materials and processes. Manufacturers are exploring the use of biodegradable and recyclable PCB materials, as well as the adoption of green manufacturing practices, such as lead-free soldering and the reduction of hazardous substances. Sustainable PCB manufacturing will become an increasingly important consideration for automotive OEMs and suppliers.
Frequently Asked Questions (FAQ)
- What is the importance of IATF 16949 certification for automotive PCB manufacturers?
IATF 16949 is a quality management system standard specifically developed for the automotive industry. It ensures that PCB manufacturers have robust processes in place to meet the stringent quality, safety, and reliability requirements of automotive applications. IATF 16949 certification demonstrates a manufacturer’s commitment to continuous improvement, risk management, and customer satisfaction, which are critical factors for automotive OEMs and suppliers.
- What are the key challenges in manufacturing PCBs for automotive applications?
Manufacturing PCBs for automotive applications presents several key challenges, including:
– Meeting the high reliability and durability requirements for automotive environments
– Ensuring compliance with strict quality and safety standards, such as IATF 16949 and ISO 26262
– Managing the complexity of advanced automotive electronic systems, such as ADAS and infotainment
– Achieving miniaturization and high-density interconnect (HDI) designs while maintaining performance and reliability
– Adapting to the rapid technological advancements and evolving requirements of the automotive industry
- How do automotive PCB manufacturers ensure the reliability of their products?
Automotive PCB manufacturers employ various strategies to ensure the reliability of their products, including:
– Implementing comprehensive quality management systems, such as IATF 16949, to ensure consistent and controlled processes
– Conducting rigorous testing and validation, including environmental stress testing, vibration testing, and electrical testing
– Using high-quality, automotive-grade materials and components that meet the required performance and reliability standards
– Employing advanced manufacturing processes, such as automated assembly and inspection, to minimize defects and ensure consistency
– Collaborating closely with automotive OEMs and suppliers to understand their specific requirements and develop tailored PCB solutions
- What are the benefits of using HDI technology in automotive PCBs?
High-density interconnect (HDI) technology offers several benefits for automotive PCBs, including:
– Miniaturization: HDI enables the fabrication of smaller and more compact PCBs, which is crucial for space-constrained automotive applications
– Improved signal integrity: HDI designs allow for shorter signal paths and reduced crosstalk, enhancing signal integrity and performance
– Higher component density: HDI technology enables the integration of more components and features on a single PCB, supporting the increasing complexity of automotive electronic systems
– Reduced weight: By enabling miniaturization, HDI PCBs contribute to overall weight reduction in vehicles, which is important for fuel efficiency and performance
- How are automotive PCB manufacturers addressing the challenges of electric vehicle (EV) applications?
Automotive PCB manufacturers are adapting to the specific challenges of EV applications by:
– Developing specialized PCB solutions that can handle high voltages and currents associated with EV power systems
– Using advanced materials, such as ceramic substrates and high-voltage laminates, to ensure electrical safety and reliability
– Designing PCBs with efficient thermal management to dissipate the heat generated by high-power EV components
– Collaborating with EV manufacturers to understand their unique requirements and develop customized PCB solutions
– Investing in research and development to stay at the forefront of EV technology trends and innovations
Conclusion
PCB manufacturing plays a vital role in the automotive industry, enabling the integration of advanced electronic systems that enhance vehicle performance, safety, and user experience. As the automotive industry continues to evolve, driven by trends such as electrification, autonomous driving, and miniaturization, PCB manufacturers must adapt to meet the increasing demands and challenges.
Selecting the right PCB manufacturer is crucial for automotive OEMs and suppliers to ensure the highest quality, reliability, and compliance with industry standards. Leading PCB manufacturers, such as TTM Technologies, Meiko Electronics, Unimicron Technology, Chin Poon Industrial, and Nippon Mektron, have established themselves as trusted partners for the automotive industry, offering advanced PCB solutions and expertise.
To stay competitive in the dynamic automotive landscape, PCB manufacturers must continuously innovate and invest in advanced technologies, such as HDI, flexible electronics, and eco-friendly manufacturing processes. By collaborating closely with automotive stakeholders and staying at the forefront of industry trends, PCB manufacturers can drive the future of automotive electronics and contribute to the development of safer, smarter, and more sustainable vehicles.
0 Comments