What are Military PCB Fabrication Companies (MPCBFC)?
Military PCB Fabrication Companies (MPCBFC) are specialized manufacturers that produce printed circuit boards (PCBs) for use in military applications. These companies adhere to strict quality standards and regulations set by the defense industry to ensure the reliability, durability, and performance of their products in harsh environments.
MPCBFCs play a crucial role in the development and production of electronics for military equipment, including:
- Communication systems
- Radar and sonar devices
- Aerospace and avionics
- Weapon systems
- Vehicles and tanks
- Satellites and space exploration equipment
Key Characteristics of Military PCB Fabrication Companies
-
Adherence to Military Standards: MPCBFCs follow rigorous military standards such as MIL-PRF-31032, MIL-PRF-55110, and IPC-6012 Class 3, which outline the requirements for the design, fabrication, and testing of military-grade PCBs.
-
High-Quality Materials: These companies use high-quality, military-grade materials such as polyimide, PTFE, and FR-4 to ensure the PCBs can withstand extreme temperatures, vibrations, and shock.
-
Advanced Manufacturing Processes: MPCBFCs employ advanced manufacturing processes, including controlled impedance, high-density interconnect (HDI), and rigid-flex PCBs, to meet the complex requirements of military applications.
-
Stringent Quality Control: Military PCB manufacturers implement strict quality control measures, such as automated optical inspection (AOI), X-ray inspection, and electrical testing, to ensure the highest level of quality and reliability.
-
Security and Confidentiality: MPCBFCs maintain strict security protocols to protect sensitive military information and intellectual property.
The Importance of Military PCB Fabrication Companies
MPCBFCs are essential to the defense industry, as they provide the foundation for advanced electronic systems that ensure the safety and effectiveness of military personnel and equipment. Some of the key reasons why MPCBFCs are crucial include:
-
Reliability in Harsh Environments: Military PCBs must withstand extreme conditions, such as high temperatures, humidity, vibrations, and electromagnetic interference (EMI). MPCBFCs ensure that the PCBs can perform reliably in these challenging environments.
-
Enabling Advanced Technologies: As military technologies become more sophisticated, MPCBFCs play a vital role in enabling the development and integration of cutting-edge electronics, such as artificial intelligence, robotics, and Internet of Things (IoT) devices.
-
Supporting National Security: By providing high-quality PCBs for military applications, MPCBFCs contribute to the overall security and defense capabilities of a nation.
-
Driving Innovation: The demanding requirements of military PCBs often lead to innovations in materials, manufacturing processes, and design techniques, which can benefit other industries as well.
Challenges Faced by Military PCB Fabrication Companies
Despite their critical role, MPCBFCs face several challenges in today’s rapidly evolving technology landscape:
-
Keeping Up with Technological Advancements: As military technologies become more complex, MPCBFCs must continuously invest in research and development to stay ahead of the curve and meet the ever-increasing demands of the defense industry.
-
Supply Chain Management: MPCBFCs often rely on a global supply chain for raw materials and components, which can be subject to disruptions due to geopolitical events, natural disasters, or other unforeseen circumstances.
-
Skilled Labor Shortage: The complex nature of military PCB fabrication requires highly skilled technicians and engineers. However, the industry faces a shortage of qualified personnel, making it challenging for MPCBFCs to maintain a capable workforce.
-
Regulatory Compliance: MPCBFCs must navigate a complex web of regulations and standards, which can be time-consuming and costly to implement and maintain.
-
Cybersecurity Threats: As PCBs become more connected and intelligent, they also become more vulnerable to cyber attacks. MPCBFCs must invest in robust cybersecurity measures to protect their products and sensitive information from potential breaches.
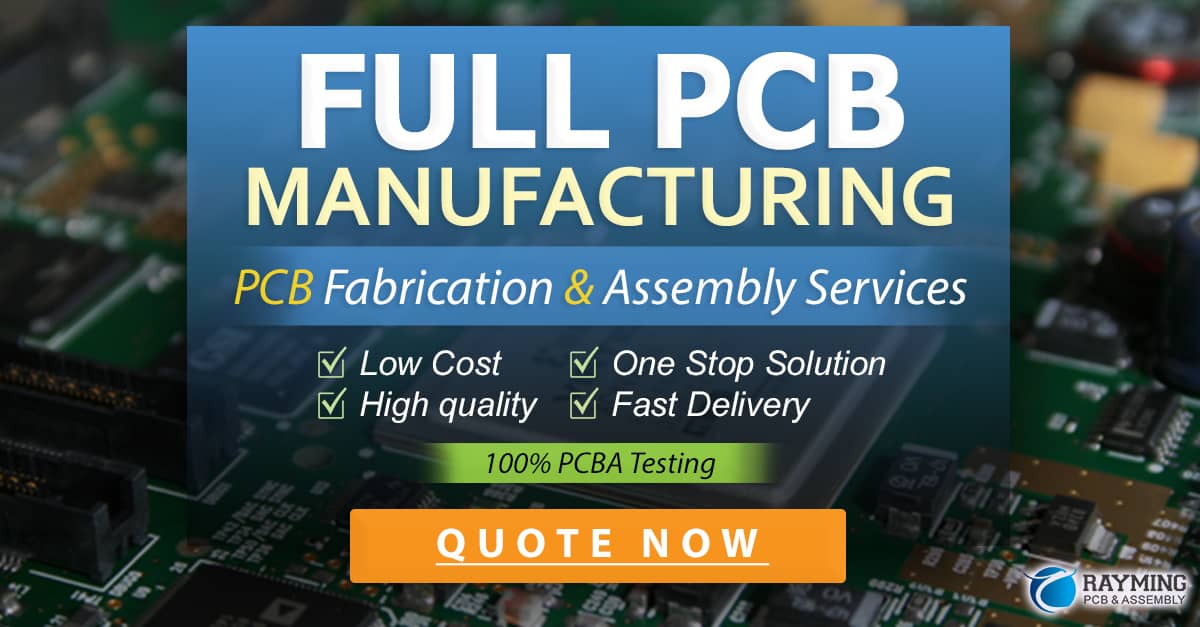
Leading Military PCB Fabrication Companies
Several companies have established themselves as leaders in the military PCB fabrication industry. Some of the most notable ones include:
-
TTM Technologies: TTM is a global leader in PCB manufacturing, offering a wide range of services for military and aerospace applications, including HDI, rigid-flex, and RF PCBs.
-
Sanmina: Sanmina is a leading provider of end-to-end manufacturing solutions for the defense industry, with expertise in PCB fabrication, assembly, and testing.
-
Eltek: Eltek is an Israeli company specializing in high-reliability PCBs for military, aerospace, and medical applications. They offer a range of services, including rigid, flex, and rigid-flex PCBs.
-
Epec Engineered Technologies: Epec is a US-based company that provides custom PCB solutions for military and aerospace customers, with a focus on quick-turn prototyping and low-volume production.
-
Sunstone Circuits: Sunstone Circuits is a PCB manufacturer that offers a range of services for military applications, including prototyping, small-batch production, and full-scale manufacturing.
Company | Headquarters | Key Services |
---|---|---|
TTM Technologies | USA | HDI, rigid-flex, RF PCBs |
Sanmina | USA | PCB fabrication, assembly, testing |
Eltek | Israel | Rigid, flex, rigid-flex PCBs for military and aerospace |
Epec Engineered Technologies | USA | Custom PCB solutions, quick-turn prototyping, low-volume production |
Sunstone Circuits | USA | Prototyping, small-batch production, full-scale manufacturing |
The Future of Military PCB Fabrication Companies
As military technologies continue to advance, MPCBFCs will play an increasingly important role in enabling the development and deployment of cutting-edge electronic systems. Some of the key trends and opportunities that will shape the future of the industry include:
-
Additive Manufacturing: 3D printing technologies, such as direct write and aerosol jet printing, offer new possibilities for PCB fabrication, enabling faster prototyping, more complex designs, and reduced waste.
-
Advanced Materials: The development of new materials, such as graphene and carbon nanotubes, could lead to the creation of PCBs with enhanced thermal, electrical, and mechanical properties.
-
Embedded Electronics: The integration of electronic components directly into the PCB substrate, known as embedded electronics, can lead to smaller, lighter, and more reliable military electronics.
-
Artificial Intelligence: The incorporation of AI algorithms into military PCBs could enable more intelligent and autonomous systems, such as self-diagnosing and self-healing electronics.
-
Collaboration and Partnerships: MPCBFCs will need to foster closer collaborations with military customers, research institutions, and technology partners to stay at the forefront of innovation and meet the evolving needs of the defense industry.
Frequently Asked Questions (FAQ)
-
What are the main differences between military and commercial PCBs?
Military PCBs are designed to withstand harsh environments and meet strict quality standards, while commercial PCBs are typically less robust and have more relaxed requirements. Military PCBs also often require specialized materials, manufacturing processes, and testing procedures. -
How do I choose the right military PCB fabrication company for my project?
When selecting an MPCBFC, consider factors such as their experience with military standards, manufacturing capabilities, quality control processes, and ability to meet your specific requirements. It’s also important to assess their security measures and ability to protect sensitive information. -
What are the most common military standards for PCB fabrication?
Some of the most common military standards for PCB fabrication include MIL-PRF-31032, MIL-PRF-55110, and IPC-6012 Class 3. These standards outline the requirements for the design, fabrication, and testing of military-grade PCBs. -
How long does it typically take to produce a military-grade PCB?
The lead time for a military-grade PCB can vary depending on the complexity of the design, the materials used, and the manufacturing processes involved. On average, it can take several weeks to several months to produce a military-grade PCB, although some MPCBFCs offer expedited services for urgent projects. -
Are there any specific certifications that military PCB fabrication companies should have?
While there are no mandatory certifications for MPCBFCs, many companies choose to obtain certifications such as ISO 9001 (quality management), AS9100 (aerospace quality management), and ITAR (International Traffic in Arms Regulations) to demonstrate their commitment to quality and compliance with military standards.
Conclusion
Military PCB Fabrication Companies play a vital role in the defense industry, providing the foundation for advanced electronic systems that ensure the safety and effectiveness of military personnel and equipment. These companies face unique challenges, such as keeping up with technological advancements, managing complex supply chains, and navigating strict regulations and standards.
As military technologies continue to evolve, MPCBFCs will need to invest in research and development, embrace new manufacturing processes and materials, and foster closer collaborations with customers and partners to stay at the forefront of innovation. By doing so, they will not only support the defense capabilities of nations but also drive technological progress that can benefit other industries and society as a whole.
0 Comments