Introduction to DFM and Its Importance
Design for Manufacturing (DFM) is a crucial aspect of product development that focuses on optimizing the design of a product to make it easier, faster, and more cost-effective to manufacture. By incorporating DFM principles early in the design process, companies can avoid costly redesigns, reduce time-to-market, and improve product quality. Outsourcing DFM services to experienced providers like RAYMING can help businesses streamline their product development process and achieve better results.
What is DFM?
DFM is a design approach that considers the manufacturing process during the product design stage. It involves designing products with the aim of simplifying the manufacturing process, reducing costs, and improving quality. DFM takes into account factors such as material selection, tolerances, design features, and assembly methods to create designs that are optimized for manufacturing.
Benefits of Implementing DFM
Implementing DFM offers several benefits to businesses, including:
- Cost reduction: By designing products that are easier and more efficient to manufacture, companies can reduce production costs and improve their bottom line.
- Faster time-to-market: DFM helps identify and address potential manufacturing issues early in the design process, reducing the need for redesigns and accelerating product launch.
- Improved product quality: DFM principles ensure that products are designed with manufacturing in mind, resulting in more reliable and consistent quality.
- Enhanced collaboration: DFM encourages collaboration between design and manufacturing teams, leading to better communication and more efficient problem-solving.
Why Outsource DFM Services?
Outsourcing DFM services to experienced providers like RAYMING can offer several advantages over in-house DFM efforts:
Access to Expertise and Resources
DFM service providers have dedicated teams of experts with extensive knowledge and experience in various manufacturing processes and industries. By outsourcing DFM, companies can tap into this expertise and gain access to the latest tools, technologies, and best practices in DFM.
Cost Savings
Outsourcing DFM can be more cost-effective than maintaining an in-house DFM team, especially for smaller companies or those with limited resources. DFM service providers can offer flexible engagement models and scalable services to meet the specific needs of each client.
Focus on Core Competencies
By outsourcing DFM, companies can focus on their core competencies, such as product innovation and marketing, while leaving the manufacturing optimization to the experts. This allows businesses to allocate their resources more effectively and stay competitive in their markets.
Faster Turnaround Times
DFM service providers have streamlined processes and dedicated resources to handle DFM projects efficiently. This can lead to faster turnaround times compared to in-house efforts, helping companies bring their products to market more quickly.
RAYMING: Your Trusted Partner for Outsourced DFM Services
RAYMING is a leading provider of outsourced DFM services, offering comprehensive solutions to help businesses optimize their product designs for manufacturing. With a team of experienced engineers and state-of-the-art tools, RAYMING is well-equipped to handle DFM projects across various industries.
RAYMING’s DFM Services
RAYMING offers a wide range of DFM services to support clients at every stage of the product development process:
- Design Review and Analysis: RAYMING’s experts review product designs to identify potential manufacturing issues and provide recommendations for optimization.
- Material Selection: RAYMING helps clients select the most suitable materials for their products, considering factors such as cost, performance, and manufacturability.
- Tolerance Analysis: RAYMING conducts tolerance analysis to ensure that product designs can be manufactured consistently and reliably.
- Design Optimization: RAYMING’s team works closely with clients to optimize product designs for manufacturing, incorporating DFM principles to reduce costs and improve quality.
- Prototyping and Testing: RAYMING provides prototyping and testing services to validate product designs and ensure they meet the required specifications.
RAYMING’s Expertise and Experience
RAYMING has a proven track record of delivering successful DFM projects for clients across various industries, including:
- Automotive
- Aerospace
- Medical devices
- Consumer electronics
- Industrial equipment
RAYMING’s team of engineers has extensive experience in a wide range of manufacturing processes, such as:
- Injection molding
- CNC machining
- Sheet metal fabrication
- 3D printing
- Electronics manufacturing
This diverse expertise enables RAYMING to provide tailored DFM solutions that meet the specific needs of each client.
Case Studies
Here are a few examples of how RAYMING has helped clients achieve success through outsourced DFM services:
Case Study 1: Automotive Component Manufacturer
An automotive component manufacturer approached RAYMING to optimize the design of a plastic bracket for injection molding. RAYMING’s DFM experts reviewed the design, identified areas for improvement, and provided recommendations to reduce the part’s complexity and improve its manufacturability. By implementing RAYMING’s suggestions, the client was able to reduce the bracket’s production cost by 25% and improve its quality and consistency.
Case Study 2: Medical Device Startup
A medical device startup engaged RAYMING to help develop a new product from concept to manufacturing. RAYMING’s team worked closely with the client to create a design that incorporated DFM principles from the outset. Through iterative design reviews and prototyping, RAYMING helped the startup create a product that was easy to manufacture, assemble, and use. The startup was able to bring their product to market faster and at a lower cost than they had initially anticipated.
Case Study 3: Industrial Equipment OEM
An industrial equipment OEM was experiencing quality issues and high production costs for a key component of their machines. RAYMING’s DFM experts analyzed the component’s design and manufacturing process, identifying several areas for improvement. By optimizing the design for CNC machining and implementing process improvements, RAYMING helped the OEM reduce the component’s production cost by 30% and improve its quality and reliability.
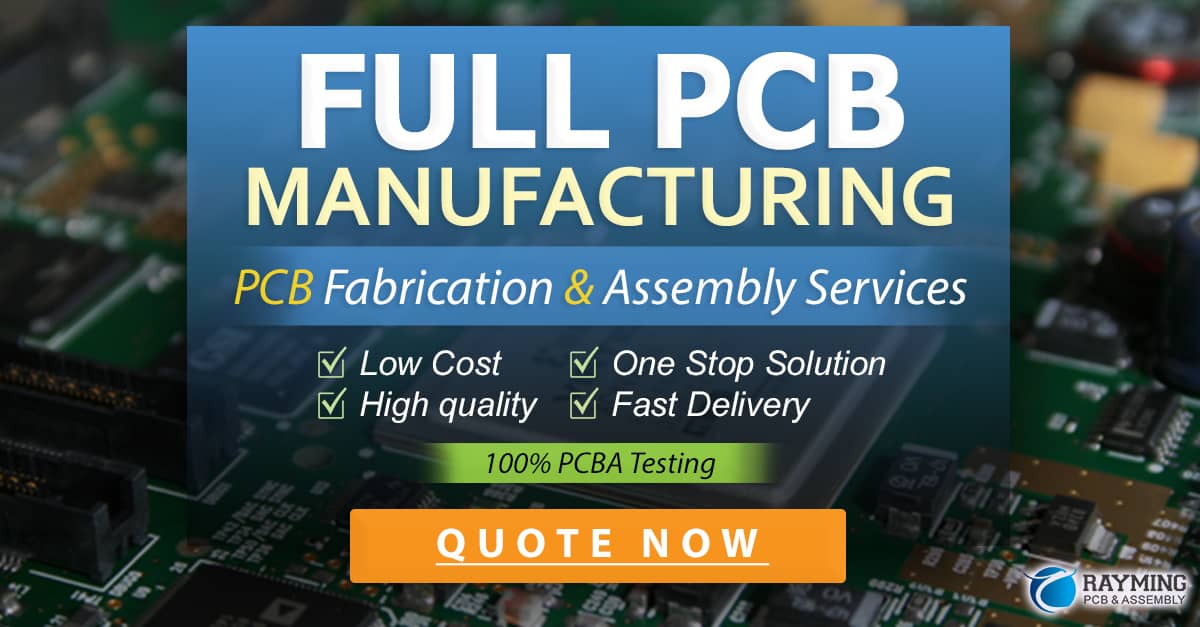
The RAYMING Advantage
Outsourcing DFM services to RAYMING offers several advantages that set it apart from other providers:
- Comprehensive Services: RAYMING offers end-to-end DFM services, from design review to prototyping and testing, ensuring that clients receive comprehensive support throughout the product development process.
- Experienced Team: RAYMING’s team of engineers has extensive experience in various industries and manufacturing processes, enabling them to provide expert guidance and solutions tailored to each client’s needs.
- State-of-the-Art Tools: RAYMING invests in the latest software and hardware tools to support its DFM services, ensuring that clients benefit from the most advanced technologies and techniques.
- Flexible Engagement Models: RAYMING offers flexible engagement models to suit the needs and budgets of different clients, from one-off projects to long-term partnerships.
- Proven Results: RAYMING has a track record of delivering successful DFM projects that have helped clients reduce costs, improve quality, and accelerate time-to-market.
Getting Started with RAYMING’s DFM Services
Starting a DFM project with RAYMING is easy. Simply follow these steps:
- Contact RAYMING to discuss your project needs and objectives.
- Provide RAYMING with your product design files and any relevant information about your manufacturing requirements.
- RAYMING’s team will review your design and provide a detailed proposal outlining the scope of work, timeline, and cost.
- Upon acceptance of the proposal, RAYMING will begin working on your DFM project, providing regular updates and collaborating closely with your team.
- RAYMING will deliver the optimized design files and any additional deliverables, such as prototypes or test reports, as per the agreed-upon scope of work.
Conclusion
Outsourcing DFM services to experienced providers like RAYMING can help businesses optimize their product designs for manufacturing, reducing costs, improving quality, and accelerating time-to-market. With its comprehensive services, experienced team, and state-of-the-art tools, RAYMING is well-positioned to support clients across various industries in achieving their DFM objectives. By partnering with RAYMING, companies can focus on their core competencies while benefiting from expert guidance and support in optimizing their product designs for manufacturing success.
Frequently Asked Questions (FAQ)
-
What industries does RAYMING serve with its DFM services?
RAYMING serves clients across various industries, including automotive, aerospace, medical devices, consumer electronics, and industrial equipment, among others. -
How long does a typical DFM project with RAYMING take?
The duration of a DFM project depends on the complexity of the product design and the scope of work. RAYMING works closely with clients to establish project timelines and milestones based on their specific needs and objectives. -
Does RAYMING offer Prototyping Services as part of its DFM offerings?
Yes, RAYMING offers prototyping services to validate product designs and ensure they meet the required specifications. This includes various prototyping methods, such as 3D printing, CNC machining, and injection molding. -
Can RAYMING help with material selection for my product?
Yes, RAYMING’s DFM experts can help clients select the most suitable materials for their products, considering factors such as cost, performance, and manufacturability. -
How do I get started with a DFM project with RAYMING?
To get started with a DFM project, simply contact RAYMING to discuss your project needs and objectives. RAYMING’s team will work with you to develop a tailored proposal and guide you through the process of optimizing your product design for manufacturing.
0 Comments