Introduction
When it comes to PCB (Printed Circuit Board) manufacturing, the cost is often a significant factor in decision-making. Many companies and individuals are tempted to opt for the cheapest options available to save money. However, with 9 years of experience in the PCB industry, we can confidently say that choosing the cheapest PCB can lead to a big trap that can cost you more in the long run. In this article, we will explore the pitfalls of cheap PCBs and why investing in quality is crucial for the success of your projects.
The Allure of Cheap PCBs
Lower Upfront Costs
One of the main reasons people gravitate towards cheap PCBs is the lower upfront costs. When comparing prices from different PCB Manufacturers, it’s easy to be swayed by the lowest price tag. However, it’s essential to understand that the initial cost savings may not translate to long-term benefits.
Competitive Market Pressure
In today’s competitive market, there is immense pressure to reduce costs and maximize profits. This pressure can lead companies to prioritize short-term cost savings over long-term quality and reliability. As a result, many PCB manufacturers offer cheap PCBs to attract customers and stay competitive.
The Hidden Costs of Cheap PCBs
Inferior Materials
One of the primary reasons cheap PCBs are inexpensive is the use of inferior materials. Lower-quality substrates, copper, and solder mask can lead to a host of problems, such as:
- Reduced durability and lifespan of the PCB
- Increased susceptibility to environmental factors (e.g., moisture, temperature)
- Poor electrical performance and signal integrity
Substandard Manufacturing Processes
Cheap PCB manufacturers often cut corners in their manufacturing processes to keep costs low. This can result in:
- Inconsistent etching and plating
- Inadequate quality control and testing
- Higher defect rates and lower yields
These issues can lead to unreliable PCBs that fail prematurely or perform poorly in the field.
Longer Lead Times and Delays
While cheap PCB manufacturers may offer attractive pricing, they often have longer lead times and are more prone to delays. This can be due to several factors, such as:
- Overbooked production schedules
- Limited capacity and resources
- Prioritizing quantity over quality
Delays in PCB delivery can have a cascading effect on your project timeline, causing setbacks and increasing overall costs.
Increased Rework and Replacement Costs
When cheap PCBs fail or perform poorly, it often leads to increased rework and replacement costs. Consider the following scenarios:
- A cheap PCB fails during assembly, requiring additional labor and materials to rework or replace the board.
- A product with a cheap PCB is shipped to customers, leading to higher warranty claims and returns.
- A cheap PCB causes system downtime or malfunctions, resulting in lost productivity and revenue.
These hidden costs can quickly add up, eroding any initial cost savings from choosing a cheap PCB.
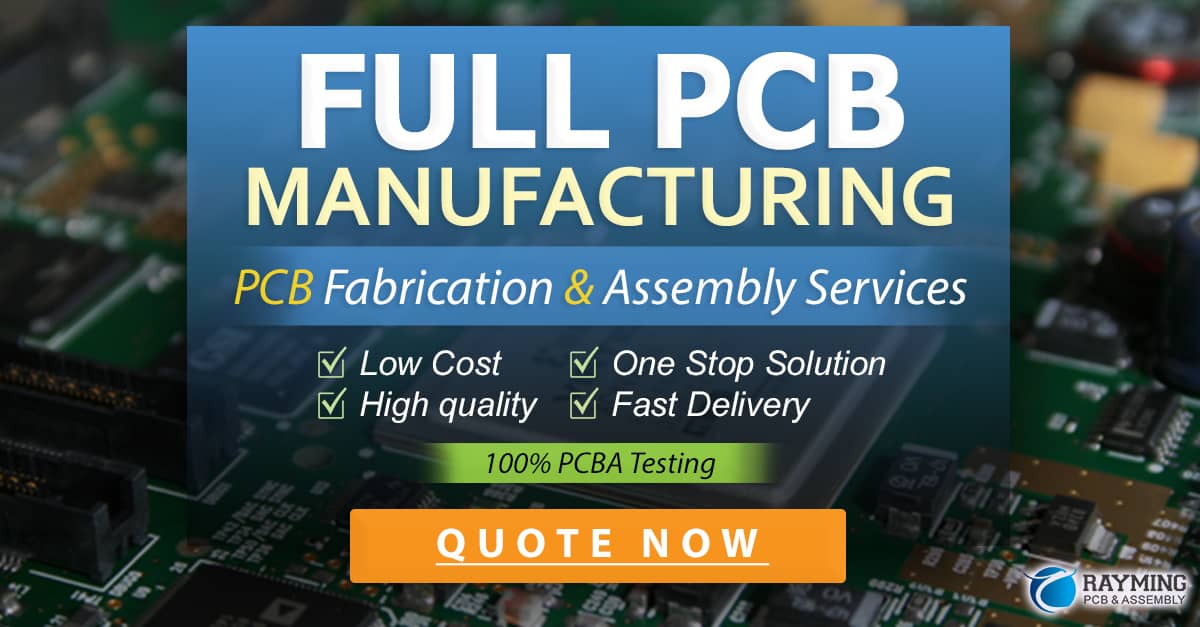
The Benefits of Investing in Quality PCBs
Reliability and Longevity
Quality PCBs are manufactured using high-grade materials and adhering to strict quality control standards. This results in PCBs that are:
- More durable and resistant to environmental stresses
- Less likely to fail or malfunction over time
- Able to maintain consistent electrical performance
Investing in quality PCBs ensures that your products and systems operate reliably, reducing the risk of costly failures and downtime.
Better Electrical Performance
Quality PCBs are designed and manufactured to optimize electrical performance. This includes:
- Proper impedance control and signal integrity
- Reduced crosstalk and electromagnetic interference (EMI)
- Consistent power delivery and distribution
By choosing quality PCBs, you can ensure that your products meet or exceed performance expectations, leading to better customer satisfaction and brand reputation.
Faster Time-to-Market
While quality PCBs may have a higher upfront cost, they often lead to faster time-to-market. This is because:
- Quality PCB manufacturers have streamlined processes and experienced staff
- Higher yields and lower defect rates reduce the need for rework and delays
- Reliable PCBs minimize the risk of product recalls or redesigns
By partnering with a quality PCB manufacturer, you can bring your products to market faster, gaining a competitive edge and maximizing revenue potential.
Cost Savings in the Long Run
Investing in quality PCBs can lead to significant cost savings in the long run. Consider the following:
- Reduced rework and replacement costs
- Lower warranty claims and returns
- Increased product lifespan and customer satisfaction
- Minimized downtime and lost productivity
By choosing quality over the lowest price, you can avoid the hidden costs associated with cheap PCBs and realize long-term cost savings for your business.
How to Choose a Quality PCB Manufacturer
Look Beyond Price
When selecting a PCB manufacturer, it’s crucial to look beyond the price tag. Consider factors such as:
- Reputation and experience in the industry
- Quality control processes and certifications (e.g., ISO 9001, UL)
- Manufacturing capabilities and technology
- Customer support and communication
By evaluating PCB manufacturers holistically, you can make an informed decision that balances cost, quality, and service.
Establish Clear Requirements and Specifications
To ensure that you receive quality PCBs that meet your needs, it’s essential to establish clear requirements and specifications. This includes:
- PCB design files and Gerber data
- Material specifications (e.g., substrate, copper weight)
- Surface finish and solder mask requirements
- Electrical and mechanical specifications
- Testing and inspection criteria
By communicating your requirements clearly and working closely with your PCB manufacturer, you can avoid misunderstandings and ensure that your PCBs are manufactured to your exact specifications.
Develop a Long-Term Partnership
Establishing a long-term partnership with a quality PCB manufacturer can bring numerous benefits, such as:
- Consistent quality and reliability
- Improved communication and collaboration
- Access to technical expertise and support
- Potential cost savings through volume discounts and optimized processes
By fostering a strong relationship with your PCB manufacturer, you can create a foundation for success and growth in your business.
FAQs
1. Are cheap PCBs always low quality?
Not necessarily. Some PCB manufacturers may offer competitive pricing while still maintaining acceptable quality standards. However, it’s essential to carefully evaluate the manufacturer’s capabilities, processes, and reputation before making a decision based solely on price.
2. Can I negotiate pricing with PCB manufacturers?
Yes, it’s common to negotiate pricing with PCB manufacturers, especially for larger orders or ongoing partnerships. However, be cautious of manufacturers who offer prices significantly lower than the market average, as this may indicate compromises in quality or service.
3. How can I ensure the quality of my PCBs?
To ensure the quality of your PCBs, work closely with your PCB manufacturer and establish clear requirements and specifications. Implement a robust quality control process that includes inspections, testing, and regular communication with your manufacturer.
4. What are the risks of using cheap PCBs in critical applications?
Using cheap PCBs in critical applications can lead to increased risk of failure, malfunction, or poor performance. This can result in safety hazards, system downtime, and costly repairs or replacements. For critical applications, it’s crucial to prioritize quality and reliability over cost savings.
5. How do I balance cost and quality when choosing a PCB manufacturer?
To balance cost and quality, evaluate PCB manufacturers based on a combination of factors, including price, reputation, capabilities, and customer service. Look for manufacturers who offer competitive pricing while still maintaining high-quality standards and a commitment to customer satisfaction.
Conclusion
In conclusion, the big trap of cheap PCBs is a temptation that can lead to significant long-term costs and challenges. While the allure of lower upfront prices may be appealing, the hidden costs of inferior materials, substandard manufacturing processes, and increased rework and replacement expenses can quickly erode any initial savings.
By investing in quality PCBs from reputable manufacturers, you can ensure the reliability, performance, and longevity of your products. Quality PCBs not only minimize the risk of failures and delays but also contribute to faster time-to-market and long-term cost savings.
When choosing a PCB manufacturer, it’s essential to look beyond price and consider factors such as reputation, capabilities, and customer support. By establishing clear requirements, fostering long-term partnerships, and prioritizing quality, you can navigate the competitive PCB market and set your business up for success.
Remember, in the world of PCBs, the cheapest option is rarely the best choice. Invest in quality, and your products, customers, and bottom line will thank you in the long run.
0 Comments