Understanding the Requirements for PCBA Enclosure Design
Before starting the design process, it is essential to understand the specific requirements for your PCBA enclosure. Consider the following factors:
Environmental Conditions
- Operating temperature range
- Humidity levels
- Exposure to dust, moisture, or other contaminants
- Vibration and shock resistance
Mechanical Requirements
- Size constraints
- Weight limitations
- Mounting options (e.g., wall-mounted, desktop, or handheld)
- Accessibility for maintenance or battery replacement
Electrical Requirements
- Electromagnetic Interference (EMI) shielding
- Electrostatic Discharge (ESD) protection
- Grounding and shielding
Aesthetics and Ergonomics
- Product branding and visual appeal
- User interaction and ergonomics
- Color, texture, and Surface Finish options
Selecting the Right Material for Your PCBA Enclosure
The choice of material for your PCBA enclosure depends on several factors, such as the operating environment, mechanical requirements, and cost considerations. Some common materials used for PCBA enclosures include:
Plastic
- Injection-molded plastics (e.g., ABS, polycarbonate, or nylon)
- Advantages: lightweight, cost-effective, and easy to mold into complex shapes
- Disadvantages: limited temperature range and lower strength compared to metals
Metal
- Sheet metal (e.g., aluminum, steel, or stainless steel)
- Die-cast metals (e.g., aluminum or zinc alloys)
- Advantages: high strength, excellent thermal conductivity, and EMI Shielding properties
- Disadvantages: higher cost and weight compared to plastics
Composite Materials
- Carbon fiber or glass-reinforced plastics
- Advantages: high strength-to-weight ratio and good thermal stability
- Disadvantages: higher cost and limited manufacturing options
Material | Advantages | Disadvantages |
---|---|---|
Plastic | Lightweight, cost-effective, easy to mold | Limited temperature range, lower strength |
Metal | High strength, excellent thermal conductivity, EMI shielding | Higher cost and weight compared to plastics |
Composite Materials | High strength-to-weight ratio, good thermal stability | Higher cost, limited manufacturing options |
Thermal Management Considerations
Proper thermal management is crucial for ensuring the reliability and longevity of your PCBA. The enclosure design plays a significant role in dissipating heat generated by the electronic components. Consider the following thermal management techniques:
Passive Cooling
- Natural convection: Utilize vents or openings in the enclosure to allow air circulation
- Heat sinks: Attach heat sinks to high-power components to dissipate heat
- Thermal interface materials: Use Thermal Pads or compounds to improve heat transfer between components and the enclosure
Active Cooling
- Fans: Incorporate fans to force air circulation and enhance cooling
- Thermoelectric coolers: Use Peltier devices to actively pump heat away from sensitive components
- Liquid cooling: Implement a liquid cooling system for high-power applications
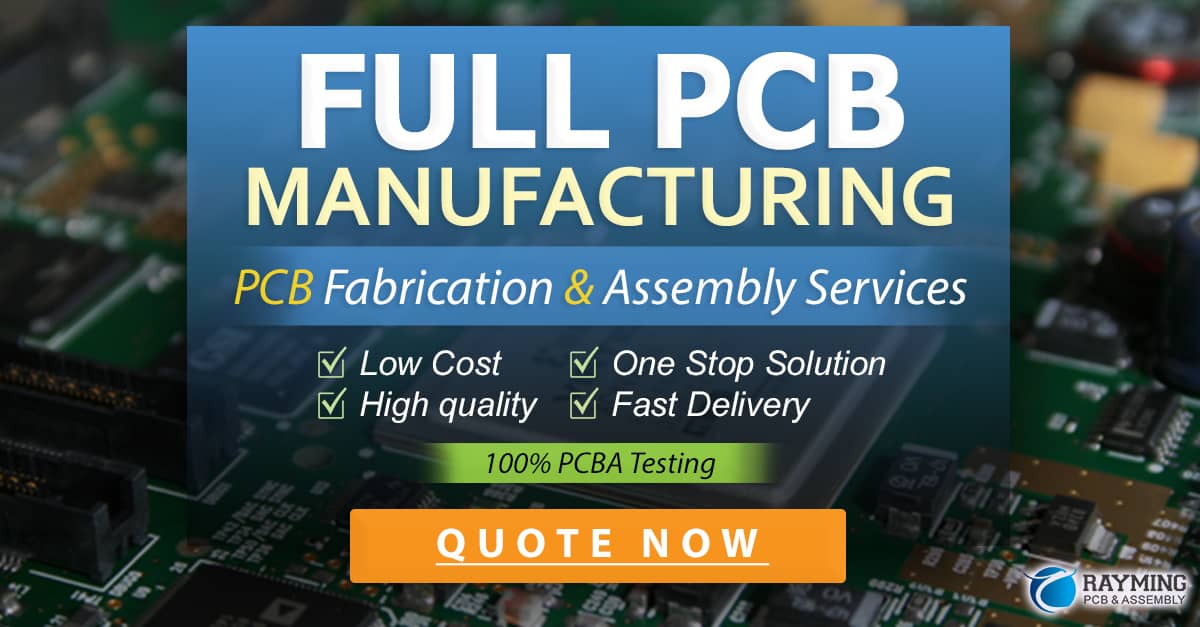
EMI Shielding and Grounding
Electromagnetic Interference (EMI) can disrupt the functioning of your PCBA and cause compliance issues with regulatory standards. Proper EMI shielding and grounding techniques should be incorporated into your enclosure design:
Shielding Materials
- Conductive coatings: Apply Conductive Paints or sprays to the interior of plastic enclosures
- Metal shielding: Use metal enclosures or metal shielding gaskets to create a Faraday cage
- Conductive plastics: Utilize plastics with embedded conductive fillers for shielding
Grounding Techniques
- Grounding points: Provide dedicated grounding points on the PCBA and enclosure
- Shielding gaskets: Use conductive gaskets to ensure proper contact between the PCBA and enclosure
- Cable shielding: Shield external cables and connectors to prevent EMI ingress or egress
Manufacturing Considerations
When designing your PCBA enclosure, it is important to consider the manufacturing process to ensure feasibility and cost-effectiveness. Some key manufacturing considerations include:
Design for Manufacturing (DFM)
- Minimize complex geometries and undercuts to facilitate molding or machining
- Ensure proper draft angles for easy ejection from molds
- Avoid thin walls or sharp corners that may cause manufacturing issues
Tolerances and Fit
- Specify appropriate tolerances for mating parts and interfaces
- Consider the assembly process and ensure easy alignment and fitting of components
- Allow for sufficient clearance between the PCBA and enclosure to avoid interference
Fastening Methods
- Choose appropriate fastening methods (e.g., screws, snap-fits, or adhesives) based on the enclosure material and assembly requirements
- Consider the serviceability and disassembly of the enclosure for maintenance or repairs
- Minimize the number of fasteners to reduce assembly time and cost
Prototyping and Testing
Before finalizing your PCBA enclosure design, it is crucial to create prototypes and conduct thorough testing to validate the design and ensure it meets all requirements. Consider the following prototyping and testing methods:
3D Printing
- Create rapid prototypes using 3D printing techniques (e.g., FDM, SLA, or SLS)
- Evaluate the form, fit, and function of the enclosure
- Identify any design issues or manufacturing challenges
Functional Testing
- Conduct environmental testing (e.g., temperature cycling, humidity, or vibration) to validate the enclosure’s performance
- Perform EMI testing to ensure compliance with regulatory standards
- Test the mechanical strength and durability of the enclosure
User Testing
- Conduct user trials to gather feedback on the ergonomics and usability of the enclosure
- Assess the visual appeal and aesthetics of the design
- Identify any potential improvements or modifications based on user feedback
Frequently Asked Questions (FAQ)
1. What is the best material for a PCBA enclosure?
The best material for a PCBA enclosure depends on the specific requirements of your application. Factors such as operating environment, mechanical requirements, and cost considerations should be taken into account. Common materials include plastics (e.g., ABS or polycarbonate), metals (e.g., aluminum or steel), and composite materials (e.g., carbon fiber or glass-reinforced plastics).
2. How do I ensure proper thermal management in my PCBA enclosure?
To ensure proper thermal management, consider incorporating passive or active cooling techniques in your enclosure design. Passive cooling methods include natural convection (using vents or openings), heat sinks, and thermal interface materials. Active cooling methods involve the use of fans, thermoelectric coolers, or liquid cooling systems. The choice of cooling technique depends on the heat generation of your PCBA and the operating environment.
3. What are the key considerations for EMI shielding in a PCBA enclosure?
EMI shielding is crucial to prevent electromagnetic interference from disrupting the functioning of your PCBA. Key considerations include selecting appropriate shielding materials (e.g., conductive coatings, metal shielding, or conductive plastics) and implementing proper grounding techniques. Ensure that your enclosure design provides sufficient shielding coverage and includes grounding points, shielding gaskets, and cable shielding as necessary.
4. How can I optimize my enclosure design for manufacturing?
To optimize your enclosure design for manufacturing, follow Design for Manufacturing (DFM) principles. Minimize complex geometries and undercuts, ensure proper draft angles for molding, and avoid thin walls or sharp corners. Consider the tolerances and fit of mating parts, and choose appropriate fastening methods based on the material and assembly requirements. Aim to simplify the design and reduce the number of components to minimize manufacturing costs.
5. What types of prototyping and testing should I conduct for my PCBA enclosure?
Prototyping and testing are essential to validate your PCBA enclosure design. Use 3D printing techniques to create rapid prototypes and evaluate the form, fit, and function of the enclosure. Conduct functional testing to assess the environmental performance, EMI compliance, and mechanical strength of the enclosure. Additionally, perform user testing to gather feedback on ergonomics, usability, and aesthetics. Based on the test results, make necessary improvements or modifications to optimize your enclosure design.
Conclusion
Designing an enclosure for a Printed Circuit board assembly (PCBA) requires careful consideration of various factors, including environmental conditions, mechanical requirements, thermal management, EMI shielding, and manufacturing considerations. By understanding these requirements and following the guidelines outlined in this article, you can create a well-designed PCBA enclosure that protects your electronic components, ensures reliable performance, and enhances the overall user experience of your product.
Remember to select the appropriate material based on your specific needs, incorporate effective thermal management techniques, and implement proper EMI shielding and grounding. Consider the manufacturing process and follow Design for Manufacturing (DFM) principles to optimize your enclosure design for cost-effectiveness and ease of production.
Prototyping and testing are crucial steps in validating your PCBA enclosure design. Utilize 3D printing for rapid prototyping, conduct functional testing to assess performance and compliance, and gather user feedback through user testing. Based on the test results, iterate and refine your design to ensure it meets all the necessary requirements.
By following the guidelines and best practices outlined in this article, you can successfully design a high-quality PCBA enclosure that meets the specific needs of your application, ensuring the reliability, durability, and aesthetics of your electronic product.
0 Comments