What is PCB Edge Clearance and Why is it Important?
PCB edge clearance, also known as PCBEdgeClearance, refers to the minimum distance between the edge of a printed circuit board (PCB) and any copper traces, components, or other conductive elements on the board. This clearance is crucial for ensuring the proper functioning, reliability, and manufacturability of the PCB.
Maintaining adequate PCB edge clearance is important for several reasons:
-
Manufacturing processes: During the manufacturing process, PCBs are often panelized, meaning multiple boards are fabricated together on a single panel and then separated using methods such as routing, scoring, or V-cutting. Proper edge clearance prevents damage to components or traces during the separation process.
-
Mechanical stability: Components or traces too close to the edge of the board are more susceptible to damage from handling, vibration, or mechanical stress. Adequate edge clearance helps protect these elements and enhances the overall durability of the PCB.
-
Electrical integrity: Insufficient edge clearance can lead to short circuits or signal integrity issues, especially if conductive elements are exposed at the edge of the board. Maintaining proper clearance helps prevent these problems and ensures reliable electrical performance.
-
Safety and regulatory compliance: Many industry standards and regulations, such as the IPC (Institute of Printed Circuits) standards, specify minimum edge clearance requirements to ensure the safety and reliability of electronic devices. Adhering to these guidelines is essential for compliance and customer satisfaction.
Factors Affecting PCB Edge Clearance
Several factors influence the determination of appropriate PCB edge clearance, including:
-
Board thickness: Thicker boards generally require larger edge clearances to accommodate manufacturing processes and ensure mechanical stability.
-
Copper weight: The thickness of the copper traces on the PCB, often referred to as copper weight, can impact the required edge clearance. Thicker copper traces may necessitate larger clearances to prevent damage during manufacturing or handling.
-
Component placement: The location and orientation of components on the PCB can affect edge clearance requirements. Components placed near the edge of the board may need additional clearance to prevent damage or interference with the board’s outline.
-
Manufacturing capabilities: The specific manufacturing processes and equipment used by the PCB fabricator can influence the minimum achievable edge clearance. It is important to consult with the manufacturer to determine their capabilities and limitations.
-
Industry standards and regulations: Depending on the application and industry, various standards and regulations may dictate specific edge clearance requirements. For example, the IPC-2221 standard provides guidelines for edge clearance based on board thickness and copper weight.
Calculating and Implementing PCB Edge Clearance
To determine the appropriate PCB edge clearance for a given design, engineers can follow these steps:
-
Consult industry standards: Review relevant industry standards, such as IPC-2221, to identify the recommended minimum edge clearance based on board thickness and copper weight.
-
Consider manufacturing capabilities: Discuss edge clearance requirements with the PCB fabricator to ensure that the proposed design is compatible with their manufacturing processes and equipment.
-
Evaluate component placement: Assess the placement of components near the edge of the board and adjust the clearance as needed to accommodate their dimensions and orientation.
-
Use CAD tools: Utilize computer-aided design (CAD) software to define and visualize edge clearance requirements. Many PCB Design tools include features for setting and checking edge clearance rules.
-
Conduct design reviews: Perform thorough design reviews to ensure that edge clearance requirements are consistently met throughout the PCB Layout. Engage with colleagues and stakeholders to gather feedback and identify potential issues.
Once the appropriate edge clearance has been determined, it is important to consistently apply these requirements throughout the PCB design process. This can be achieved by:
-
Defining design rules: Establish clear design rules within the CAD software to enforce edge clearance requirements automatically. This helps prevent accidental violations and streamlines the design process.
-
Conducting design rule checks (DRC): Regularly perform DRCs to verify that the PCB layout adheres to the defined edge clearance rules. Address any violations or discrepancies promptly to maintain design integrity.
-
Communicating with stakeholders: Clearly communicate edge clearance requirements to all relevant stakeholders, including designers, manufacturers, and assembly partners. This ensures that everyone involved in the PCB Development process is aware of and follows the established guidelines.
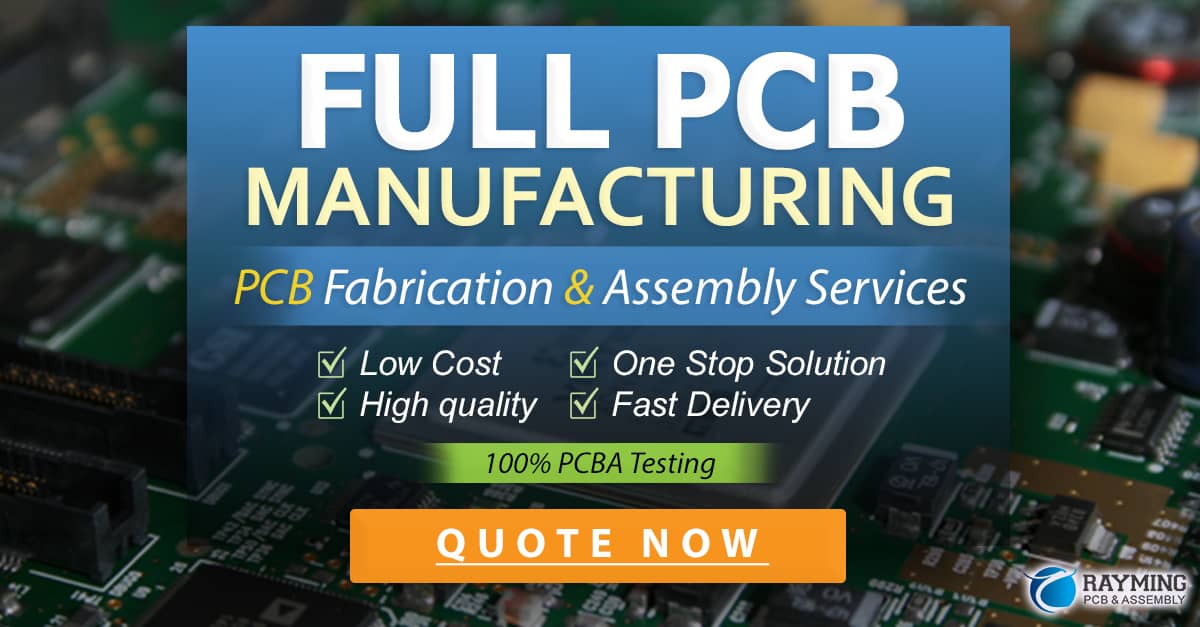
Common PCB Edge Clearance Issues and Solutions
Despite careful planning and design, PCB edge clearance issues can still arise. Some common problems and their potential solutions include:
- Insufficient clearance: If the edge clearance is found to be insufficient during manufacturing or testing, possible solutions include:
- Adjusting the PCB layout to increase the clearance between components or traces and the board edge.
- Modifying the board outline to provide additional space for clearance.
-
Considering alternative manufacturing processes or equipment that can accommodate tighter clearances.
-
Inconsistent clearance: Inconsistencies in edge clearance across the PCB can lead to manufacturing difficulties and potential reliability issues. To address this, designers should:
- Review the PCB layout to identify and correct any areas with inconsistent clearance.
- Ensure that design rules are properly defined and enforced throughout the layout process.
-
Conduct thorough DRCs to catch and resolve any clearance discrepancies.
-
Component interference: If components placed near the edge of the board interfere with the required clearance, solutions may include:
- Repositioning the affected components to provide adequate clearance.
- Selecting alternative components with smaller footprints or different orientations.
-
Adjusting the board outline to accommodate the component placement while maintaining proper clearance.
-
Manufacturing limitations: In some cases, the desired edge clearance may exceed the capabilities of the chosen manufacturing process or equipment. To overcome this, designers can:
- Consult with the PCB fabricator to identify alternative manufacturing options that can achieve the required clearance.
- Modify the PCB design to work within the limitations of the available manufacturing processes.
- Consider using specialized techniques, such as laser cutting or milling, to achieve tighter clearances in specific areas of the board.
Best Practices for Ensuring Proper PCB Edge Clearance
To minimize the risk of edge clearance issues and ensure the successful manufacturing and performance of PCBs, designers should follow these best practices:
-
Stay informed: Keep up to date with the latest industry standards, guidelines, and best practices related to PCB edge clearance. Regularly review and incorporate this information into the design process.
-
Collaborate with manufacturers: Establish strong communication channels with PCB Fabricators and assembly partners. Seek their input and guidance on edge clearance requirements and limitations early in the design process.
-
Use appropriate design tools: Invest in high-quality CAD software that offers robust features for defining, checking, and enforcing edge clearance rules. Regularly update and calibrate these tools to ensure accuracy and reliability.
-
Conduct thorough reviews and testing: Perform comprehensive design reviews and DRCs at multiple stages of the PCB development process. Conduct physical inspections and testing to verify that edge clearance requirements are met in the manufactured product.
-
Document and communicate: Clearly document edge clearance requirements and design decisions. Share this information with all relevant stakeholders to ensure consistency and adherence to the established guidelines.
-
Continuously improve: Monitor the performance and reliability of manufactured PCBs and gather feedback from customers and end-users. Use this information to identify areas for improvement and refine edge clearance practices over time.
Frequently Asked Questions (FAQ)
1. What is the recommended minimum edge clearance for a standard 1.6mm thick PCB?
According to IPC-2221, the recommended minimum edge clearance for a 1.6mm thick PCB is 0.3mm (0.012 inches) for copper weights up to 2 ounces per square foot (oz/ft²).
2. Can edge clearance requirements vary depending on the specific application or industry?
Yes, edge clearance requirements can vary based on the specific application or industry. Some industries, such as aerospace or medical devices, may have more stringent requirements due to the critical nature of the devices and the harsh environments they may be subjected to.
3. What should I do if my PCB design violates the recommended edge clearance guidelines?
If your PCB design violates edge clearance guidelines, you should first consult with your PCB fabricator to determine if they can accommodate the reduced clearance. If not, you may need to adjust your design by moving components or traces further from the board edge or by modifying the board outline to provide additional clearance.
4. How can I ensure that my PCB design maintains consistent edge clearance throughout the layout?
To ensure consistent edge clearance, define clear design rules within your CAD software that specify the required clearance. Regularly run design rule checks (DRCs) to verify that the layout adheres to these rules and address any violations promptly.
5. Are there any specialized manufacturing processes that can help achieve tighter edge clearances?
Yes, some specialized manufacturing processes, such as laser cutting or milling, can help achieve tighter edge clearances in specific areas of the board. However, these processes may increase manufacturing costs and lead times, so it is important to consult with your PCB fabricator to determine the most appropriate solution for your specific design and requirements.
PCB Thickness | Copper Weight | Minimum Edge Clearance |
---|---|---|
0.8mm | 1 oz/ft² | 0.2mm (0.008 inches) |
1.6mm | 1 oz/ft² | 0.3mm (0.012 inches) |
1.6mm | 2 oz/ft² | 0.3mm (0.012 inches) |
2.4mm | 1 oz/ft² | 0.4mm (0.016 inches) |
2.4mm | 2 oz/ft² | 0.4mm (0.016 inches) |
Table 1: Minimum edge clearance recommendations based on PCB thickness and copper weight (Source: IPC-2221)
In conclusion, maintaining proper PCB edge clearance is essential for ensuring the manufacturability, reliability, and performance of printed circuit boards. By understanding the factors that influence edge clearance, following industry guidelines and best practices, and collaborating closely with manufacturing partners, designers can effectively navigate the challenges associated with edge clearance and produce high-quality PCBs that meet the demands of their intended applications.
0 Comments