Introduction to PCB Cleaning and Flux Removal
Printed Circuit Boards (PCBs) are essential components in modern electronics, providing a platform for electrical components to be mounted and interconnected. During the soldering process, flux is used to facilitate the bonding of components to the PCB. However, after soldering, residual flux can remain on the board, potentially leading to corrosion, decreased performance, and reduced lifespan of the PCB. Therefore, it is crucial to clean flux from PCBs to ensure optimal functionality and longevity.
In this comprehensive guide, we will explore various methods and techniques for effectively cleaning flux from PCBs. We will discuss the importance of PCB cleaning, the different types of flux, and the most suitable cleaning solutions for each flux type. Additionally, we will provide step-by-step instructions for manual and automated cleaning processes, as well as tips for maintaining a clean PCB and preventing future flux buildup.
Understanding Flux and Its Role in PCB Assembly
What is Flux?
Flux is a chemical compound used in the soldering process to remove oxidation from metal surfaces, promote wetting of the solder, and facilitate the formation of a strong bond between the solder and the components. Flux is applied to the PCB before soldering to ensure that the solder adheres properly to the pads and component leads.
Types of Flux
There are three main types of flux used in PCB assembly:
- Rosin Flux
- Rosin flux is the most commonly used type of flux in electronics manufacturing.
- It is available in various activator levels, such as no-clean, RMA (Rosin Mildly Activated), and RA (Rosin Activated).
-
Rosin flux leaves a residue that may require cleaning, depending on the activator level and the specific application.
-
Water-Soluble Flux
- Water-soluble flux is designed to be easily removed with water or aqueous cleaning solutions.
- It is more active than rosin flux and provides excellent wetting properties.
-
Water-soluble flux requires thorough cleaning after soldering to prevent corrosion and ensure long-term reliability.
-
No-Clean Flux
- No-clean flux is formulated to leave minimal residue after soldering, eliminating the need for post-soldering cleaning in most cases.
- It is ideal for applications where cleaning is not feasible or desirable, such as in high-volume production or when the PCB is not easily accessible for cleaning.
- However, even no-clean flux may require cleaning in critical applications or when the residue level is too high.
The Importance of Cleaning Flux from PCBs
Cleaning flux from PCBs is essential for several reasons:
- Corrosion Prevention
- Flux residues can be corrosive, especially when exposed to moisture and humidity.
-
Over time, corrosion can lead to degradation of the PCB and its components, causing failures and reduced lifespan.
-
Improved Electrical Performance
- Flux residues can be conductive, leading to current leakage and short circuits.
-
Cleaning flux ensures optimal electrical performance by removing any conductive contaminants.
-
Enhanced Appearance
- Flux residues can give the PCB an unsightly appearance, which may be undesirable for certain applications.
-
Cleaning flux results in a cleaner, more professional-looking PCB.
-
Compliance with Industry Standards
- Many industries have specific cleanliness requirements for PCBs, such as IPC-610 and IPC-A-610.
- Cleaning flux is necessary to meet these standards and ensure the reliability and quality of the final product.
Choosing the Right Cleaning Solution for Your Flux Type
Selecting the appropriate cleaning solution is crucial for effectively removing flux residues from PCBs. The choice of cleaning solution depends on the type of flux used during the soldering process.
Cleaning Solutions for Rosin Flux
For rosin flux, the following cleaning solutions are commonly used:
- Isopropyl Alcohol (IPA)
- IPA is a popular choice for cleaning rosin flux due to its effectiveness and relatively low cost.
- It dissolves rosin flux residues and evaporates quickly, leaving minimal residue behind.
-
IPA is suitable for manual cleaning and can also be used in ultrasonic cleaners.
-
Deionized (DI) Water
- DI water can be used to clean rosin flux, particularly for RMA and RA flux types.
- It is often used in combination with other cleaning agents, such as surfactants or saponifiers, to enhance its cleaning efficacy.
-
DI water is an environmentally friendly option and is suitable for use in automated cleaning systems.
-
Commercial Flux Removers
- There are numerous commercial flux removers specifically designed for cleaning rosin flux.
- These products often contain a blend of solvents and surfactants that effectively dissolve and remove flux residues.
- Commercial flux removers are available in both liquid and aerosol forms and can be used for manual or automated cleaning.
Cleaning Solutions for Water-Soluble Flux
Water-soluble flux is designed to be easily removed with water or aqueous cleaning solutions. The following cleaning solutions are commonly used:
- Deionized (DI) Water
- DI water is the primary cleaning solution for water-soluble flux.
- It effectively dissolves and removes flux residues without leaving any additional contaminants behind.
-
DI water can be used in manual cleaning processes or automated cleaning systems.
-
Saponifiers
- Saponifiers are alkaline cleaning agents that convert flux residues into water-soluble compounds.
- They are often used in combination with DI water to enhance the cleaning efficiency and reduce the cleaning time.
- Saponifiers are suitable for use in automated cleaning systems, such as inline or batch cleaners.
Cleaning Solutions for No-Clean Flux
No-clean flux is designed to leave minimal residue after soldering, and in most cases, cleaning is not required. However, if cleaning is necessary, the following solutions can be used:
- Isopropyl Alcohol (IPA)
- IPA can be used to remove any remaining no-clean flux residues, although it may not be as effective as with rosin flux.
-
It is suitable for manual cleaning and can also be used in ultrasonic cleaners.
-
Specialized No-Clean Flux Removers
- Some manufacturers offer specialized cleaning solutions designed specifically for removing no-clean flux residues.
- These products are formulated to dissolve and remove the minimal residues left behind by no-clean flux.
Flux Type | Cleaning Solutions |
---|---|
Rosin Flux | IPA, DI Water, Commercial Flux Removers |
Water-Soluble Flux | DI Water, Saponifiers |
No-Clean Flux | IPA, Specialized No-Clean Flux Removers |
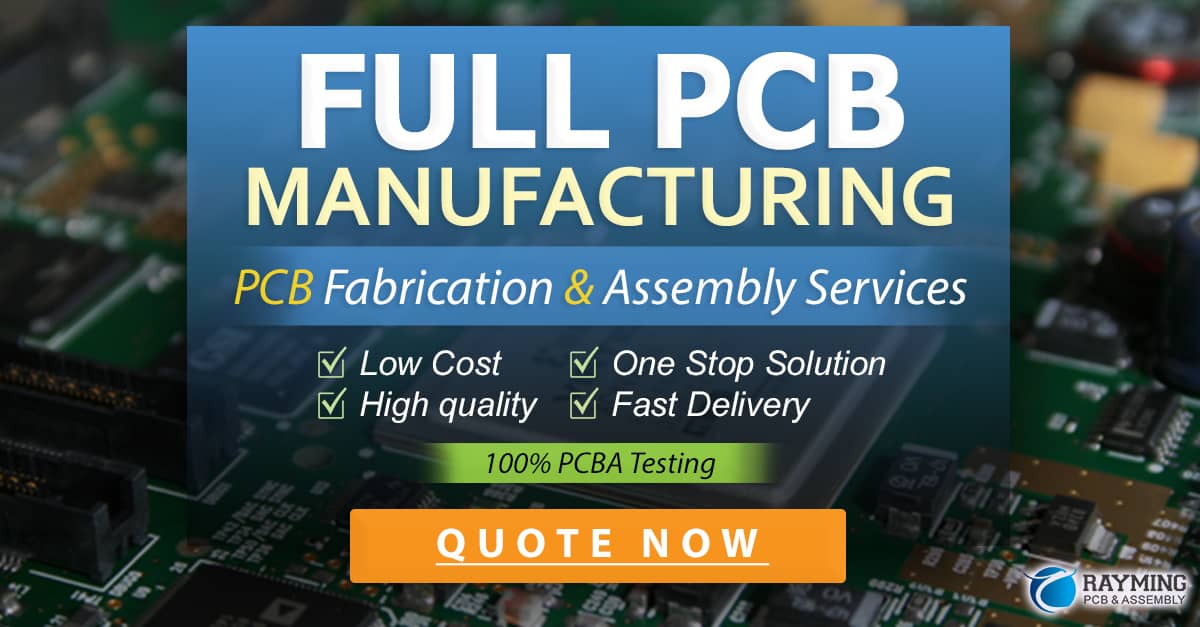
Manual Cleaning Techniques for Removing Flux from PCBs
Manual cleaning techniques are suitable for small-scale PCB cleaning, prototyping, or when automated cleaning equipment is not available. The following steps outline the manual cleaning process for removing flux from PCBs:
Step 1: Preparation
- Wear appropriate personal protective equipment (PPE), such as gloves and eye protection.
- Ensure that the PCB is powered off and disconnected from any power sources.
- Remove any components that may be sensitive to the cleaning process, if possible.
- Place the PCB on a clean, lint-free surface or in a suitable cleaning tray.
Step 2: Applying the Cleaning Solution
- Select the appropriate cleaning solution based on the type of flux used (refer to the previous section).
- Apply the cleaning solution to the PCB using a soft brush, lint-free swab, or spray bottle.
- Gently agitate the cleaning solution on the PCB surface to help dissolve the flux residues.
- Allow the cleaning solution to work on the flux residues for the recommended time, as specified by the manufacturer.
Step 3: Rinsing and Drying
- Rinse the PCB thoroughly with deionized (DI) water to remove the cleaning solution and dissolved flux residues.
- Use a gentle stream of compressed air or a lint-free cloth to remove excess water from the PCB.
- Allow the PCB to air dry completely, or use a low-temperature oven or hot air gun to accelerate the drying process.
Step 4: Inspection and Rework
- Visually inspect the PCB under magnification to ensure that all flux residues have been removed.
- If any residues remain, repeat the cleaning process focusing on the affected areas.
- Once the PCB is clean and dry, reinstall any components that were removed during the cleaning process.
Automated Cleaning Methods for PCB Flux Removal
Automated cleaning methods are ideal for high-volume PCB production or when consistent and efficient cleaning results are required. The following automated cleaning methods are commonly used in the electronics manufacturing industry:
Inline Cleaning Systems
Inline cleaning systems are integrated into the PCB assembly line and clean the PCBs immediately after the soldering process. These systems typically consist of a conveyor belt that transports the PCBs through various cleaning stages, such as:
- Pre-wash: The PCBs are sprayed with a cleaning solution to soften and dissolve the flux residues.
- Wash: The PCBs are subjected to a high-pressure spray of cleaning solution to remove the dissolved flux residues.
- Rinse: The PCBs are rinsed with DI water to remove any remaining cleaning solution and flux residues.
- Drying: The PCBs are dried using hot air knives or a combination of air and vacuum drying.
Inline cleaning systems are highly efficient and can process a large number of PCBs quickly and consistently.
Batch Cleaning Systems
Batch cleaning systems are standalone units that clean PCBs in batches, rather than continuously like inline systems. These systems are suitable for low to medium-volume production or when the PCBs are not part of an automated assembly line. Batch cleaning systems typically consist of a cleaning chamber, a reservoir for the cleaning solution, and a filtration system. The cleaning process involves:
- Loading: The PCBs are loaded into a cleaning basket or fixture and placed in the cleaning chamber.
- Cleaning: The cleaning chamber is filled with the cleaning solution, and the PCBs are cleaned using agitation, ultrasonic energy, or spray jets.
- Rinsing: The PCBs are rinsed with DI water to remove the cleaning solution and dissolved flux residues.
- Drying: The PCBs are dried using hot air or a combination of air and vacuum drying.
Batch cleaning systems offer flexibility in terms of the cleaning process and can accommodate PCBs of various sizes and shapes.
Ultrasonic Cleaning
Ultrasonic cleaning is a highly effective method for removing flux residues from PCBs. This method uses high-frequency sound waves to create microscopic cavitation bubbles in the cleaning solution. As these bubbles collapse, they release energy that helps to dislodge and remove flux residues from the PCB surface. Ultrasonic cleaning can be used in both manual and automated cleaning processes:
- Manual Ultrasonic Cleaning
- The PCB is placed in a beaker or tray filled with the cleaning solution.
- The beaker or tray is then placed in an ultrasonic cleaning tank.
- The ultrasonic energy is applied for a specific duration, depending on the level of contamination and the type of flux.
-
After cleaning, the PCB is rinsed with DI water and dried.
-
Automated Ultrasonic Cleaning
- Ultrasonic cleaning can be integrated into inline or batch cleaning systems.
- The PCBs are transported through an ultrasonic cleaning chamber filled with the cleaning solution.
- The ultrasonic energy is applied as the PCBs pass through the chamber.
- The PCBs are then rinsed and dried in subsequent stages of the automated cleaning process.
Ultrasonic cleaning is particularly effective for removing flux residues from hard-to-reach areas, such as under components or in tight spaces between components.
Automated Cleaning Method | Advantages | Disadvantages |
---|---|---|
Inline Cleaning Systems | – High throughput – Consistent cleaning results – Integrated into the assembly line |
– High initial investment – Limited flexibility in terms of PCB size and shape |
Batch Cleaning Systems | – Flexibility in cleaning process – Accommodates various PCB sizes and shapes – Lower initial investment compared to inline systems |
– Lower throughput compared to inline systems – Manual loading and unloading of PCBs |
Ultrasonic Cleaning | – Highly effective for removing flux residues – Cleans hard-to-reach areas – Can be used in both manual and automated processes |
– May damage sensitive components if not used properly – Requires optimization of cleaning parameters (frequency, power, duration) |
Tips for Maintaining a Clean PCB and Preventing Flux Buildup
Maintaining a clean PCB and preventing flux buildup is essential for ensuring the long-term reliability and performance of electronic devices. The following tips can help you keep your PCBs clean and minimize the need for extensive cleaning:
- Use No-Clean Flux When Possible
- No-clean flux leaves minimal residue after soldering, reducing the need for post-soldering cleaning.
-
Consider using no-clean flux for applications where cleaning is not critical or when the PCB is not easily accessible for cleaning.
-
Optimize Soldering Process Parameters
- Adjust soldering temperature, time, and iron tip size to minimize flux splatter and excess flux deposition.
-
Use the minimum amount of flux necessary to achieve good solder joints.
-
Implement Proper Handling and Storage Procedures
- Handle PCBs with gloves to prevent contamination from skin oils and other contaminants.
-
Store PCBs in clean, dry, and dust-free environments to minimize the accumulation of contaminants.
-
Perform Regular Inspections
- Regularly inspect PCBs for signs of flux buildup, corrosion, or other contamination.
-
Address any issues promptly to prevent further degradation of the PCB.
-
Clean PCBs Before Conformal Coating
- If conformal coating is required, ensure that the PCB is thoroughly cleaned before applying the coating.
-
Flux residues trapped beneath the conformal coating can lead to corrosion and other reliability issues.
-
Follow Industry Standards and Guidelines
- Adhere to industry standards, such as IPC-610 and IPC-A-610, for PCB Cleanliness and acceptance criteria.
- Stay updated with the latest guidelines and best practices for PCB cleaning and flux removal.
By implementing these tips and maintaining a proactive approach to PCB cleanliness, you can extend the lifespan of your PCBs and ensure optimal performance of your electronic devices.
Frequently Asked Questions (FAQ)
-
Q: Can I use rubbing alcohol to clean flux from my PCB?
A: While rubbing alcohol (isopropyl alcohol) can be used to clean flux from PCBs, it is important to ensure that the alcohol has a high purity level (90% or higher). Lower purity rubbing alcohol may contain impurities that can leave residues on the PCB or damage sensitive components. It is always best to use electronics-grade isopropyl alcohol for PCB cleaning. -
Q: How often should I clean my PCBs?
A: The frequency of PCB cleaning depends on various factors, such as the type of flux used, the operating environment, and the specific application. In general, it is recommended to clean PCBs after the soldering process to remove any flux residues. If the PCB is exposed to harsh environments or if flux buildup is observed during regular inspections, additional cleaning may be necessary. -
Q: Can I use a toothbrush to clean my PCB?
A: While a toothbrush can be used to agitate the cleaning solution and remove flux residues, it is important to choose a soft-bristled brush to avoid damaging delicate components on the PCB. A dedicated PCB cleaning brush or a soft-bristled paintbrush is a safer alternative. Always be gentle when brushing the PCB surface to prevent any damage. -
Q: How do I know if my PCB is clean enough?
A: Visual inspection is the most common method for assessing PCB cleanliness. Use a magnifying glass or microscope to examine the PCB surface for any visible flux residues, discoloration, or corrosion. Industry standards, such as IPC-610 and IPC-A-610, provide guidance on acceptable cleanliness levels for PCBs. In critical applications, more advanced cleanliness testing methods, such as ionic contamination testing or surface insulation resistance (SIR) testing, may be required. -
Q: Can I use a dishwasher to clean my PCBs?
A: Using a dishwasher to clean PCBs is not recommended. Dishwashers are designed for cleaning dishes and utensils, not delicate electronic components. The high water pressure, harsh detergents, and extreme temperatures in a dishwasher can damage PCBs and their components. Always use dedicated PCB cleaning solutions and methods to ensure the safety and integrity of your PCBs.
0 Comments