In the realm of electronics and industrial applications, protecting sensitive components and assemblies from environmental factors such as moisture, vibration, and physical impact is crucial. Two common techniques used for this purpose are potting and coating. While both processes serve to provide protection, they differ in their methods, materials, and applications. In this article, we will explore the distinctions between potting and coating, their respective advantages, and the factors that influence the choice between these two processes.
Introduction
Electronic devices and components are often exposed to various environmental challenges that can compromise their functionality and lifespan. These challenges may include moisture, temperature fluctuations, vibrations, and physical impacts. To mitigate these risks, manufacturers employ protective measures such as potting and coating. Understanding the differences between these two techniques is essential for selecting the most suitable approach based on the specific requirements of the application.
What is Potting?
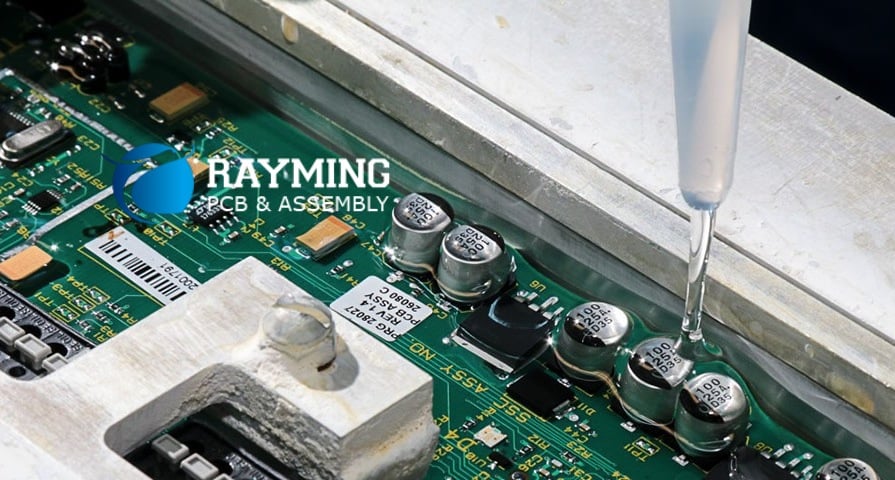
Potting is a process in which a liquid, thermo-setting compound, typically a polymer resin, is poured or injected into a housing or enclosure containing electronic components or assemblies. The resin is then cured, typically through heat or a chemical reaction, forming a solid, protective encapsulation around the components.
Potting Materials
Various potting materials are available, each with its own unique properties and characteristics. Some common potting compounds include:
- Epoxy Resins: Widely used potting materials known for their excellent adhesion, chemical resistance, and mechanical strength. Epoxy resins can be tailored to meet specific requirements, such as thermal conductivity or electrical insulation.
- Silicone Resins: Flexible and resistant to moisture, silicone resins offer good thermal stability and electrical insulation properties. They are often used in applications requiring flexibility or vibration damping.
- Polyurethane Resins: Known for their toughness and resistance to impact, polyurethane resins are suitable for applications requiring high mechanical strength and protection from physical shock.
- Acrylic Resins: Offering good optical clarity and resistance to UV radiation, acrylic resins are often used in applications where transparency or light transmission is required.
Advantages of Potting
Potting offers several advantages for protecting electronic components and assemblies:
- Environmental Protection: The solid encapsulation provided by potting effectively shields components from moisture, dust, chemicals, and other environmental contaminants.
- Mechanical Protection: The rigid or semi-rigid potting compound helps absorb vibrations and physical impacts, preventing damage to the enclosed components.
- Thermal Management: Some potting materials possess good thermal conductivity, aiding in heat dissipation and improving the overall thermal management of the assembly.
- Electrical Insulation: Potting compounds can provide electrical insulation, preventing short circuits and ensuring the safe operation of electronic components.
- Tamper Resistance: The solid encapsulation created by potting can deter unauthorized access or tampering with sensitive components or assemblies.
What is Coating?
Coating, also known as conformal coating, is a process in which a thin, protective layer of material is applied over the surface of an electronic assembly or component. This layer acts as a barrier against environmental factors such as moisture, dust, and chemicals, while still allowing access to the components for inspection or repair.
Coating Materials
Various coating materials are available, each with its own unique properties and characteristics. Some common coating materials include:
- Acrylic Coatings: Known for their excellent moisture resistance, acrylic coatings offer good adhesion and flexibility. They are often used in applications where humidity and condensation are concerns.
- Silicone Coatings: Providing excellent moisture and chemical resistance, silicone coatings are flexible and can withstand temperature extremes. They are commonly used in harsh environments or applications requiring flexibility.
- Polyurethane Coatings: Offering good abrasion resistance and toughness, polyurethane coatings are suitable for applications requiring mechanical protection or resistance to wear.
- Parylene Coatings: Applied through a vapor deposition process, parylene coatings form a thin, conformal layer with excellent moisture and chemical resistance. They are often used in medical or high-reliability applications.
Advantages of Coating
Coating offers several advantages for protecting electronic components and assemblies:
- Environmental Protection: The thin, conformal coating acts as a barrier against moisture, dust, chemicals, and other environmental contaminants, extending the lifespan of the components.
- Reworkability: Unlike potting, conformal coatings can be selectively removed or repaired, allowing access to the components for inspection, testing, or rework.
- Flexibility: Many coating materials offer flexibility, allowing them to conform to the shape of the components and withstand vibrations or flexing without cracking or peeling.
- Thickness Control: Conformal coatings can be applied in very thin layers, minimizing the impact on component dimensions and weight.
- Selective Application: Coatings can be selectively applied to specific areas or components, providing localized protection while leaving other areas accessible.
Factors Influencing the Choice between Potting and Coating
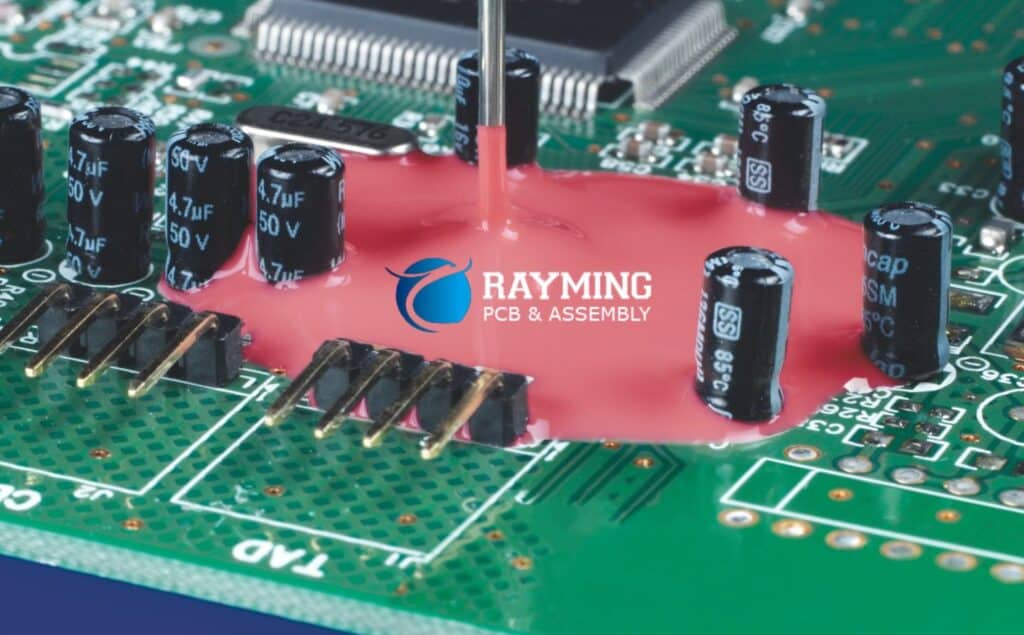
When deciding between potting and coating, several factors should be considered:
- Application Requirements: The specific operating environment, performance requirements, and design constraints of the application will influence the choice between potting and coating. For example, applications requiring high mechanical protection or tamper resistance may benefit from potting, while applications with frequent rework or inspection needs may be better suited for coating.
- Component Accessibility: If access to individual components for testing, repair, or replacement is required, coating may be the preferred option, as potting typically encapsulates the entire assembly, making component access difficult.
- Thermal Management: Applications with high heat dissipation requirements may benefit from potting materials with good thermal conductivity, while coating may be more suitable for applications with lower thermal demands.
- Cost and Production Volume: Potting can be more labor-intensive and time-consuming compared to coating, making it more expensive for high-volume production. Coating, on the other hand, can be more cost-effective for large-scale applications.
- Design Constraints: The physical dimensions, shape, and layout of the components or assembly may influence the choice between potting and coating. Potting may be more suitable for complex shapes or densely packed components, while coating can be applied to a wider range of geometries.
- Regulatory Compliance: Certain industries or applications may have specific regulatory requirements or standards that favor one method over the other, such as medical devices or aerospace applications.
It is important to carefully evaluate these factors and consult with experienced professionals to determine the most suitable protection method for a given application.
Comparison Table
To summarize the key differences between potting and coating, the following table provides a side-by-side comparison:
Aspect | Potting | Coating |
---|---|---|
Protection Method | Encapsulation with a solid compound | Thin protective layer applied to the surface |
Materials | Epoxy, silicone, polyurethane, acrylic resins | Acrylic, silicone, polyurethane, parylene |
Environmental Protection | High protection against moisture, dust, chemicals | Good protection against moisture, dust, chemicals |
Mechanical Protection | Excellent protection against vibration and physical impacts | Moderate protection against vibration and impacts |
Thermal Management | Can provide good thermal conductivity (material dependent) | Generally limited thermal management capabilities |
Component Accessibility | Limited access to individual components after potting | Components remain accessible for rework or repair |
Reworkability | Difficult to rework or repair potted assemblies | Selective removal or repair of coating is possible |
Flexibility | Limited flexibility (rigid or semi-rigid encapsulation) | Many coating materials offer flexibility |
Thickness | Thick encapsulation | Thin conformal layer |
Cost and Production Volume | Higher cost, more labor-intensive for large volumes | More cost-effective for high-volume production |
Typical Applications | Harsh environments, tamper resistance, high mechanical protection | Moderate environments, frequent rework or inspection needs |
Frequently Asked Questions (FAQs)
- Q: Can potting and coating be used together? A: Yes, in some cases, potting and coating can be used in combination to provide enhanced protection. For example, a conformal coating can be applied first to protect against moisture and chemicals, followed by potting for additional mechanical protection and tamper resistance.
- Q: How long does it take for potting or coating materials to cure? A: The curing time varies depending on the specific material and curing method used. Potting compounds typically require longer curing times, ranging from hours to days, while conformal coatings can cure within minutes or hours, depending on the material and curing process (e.g., air drying, UV curing, or heat curing).
- Q: Can potting or coating materials be removed or repaired? A: Potting compounds are generally difficult to remove or repair once cured, as they encapsulate the entire assembly. Conformal coatings, on the other hand, can be selectively removed or repaired using specialized solvents or techniques, allowing access to the underlying components.
- Q: What are the environmental considerations for potting and coating materials? A: Both potting and coating materials may have environmental concerns related to their manufacturing, application, and disposal processes. Many modern materials are designed to be more environmentally friendly, with reduced volatile organic compounds (VOCs) and improved recyclability. It is important to follow proper handling and disposal guidelines for each material.
- Q: Can potting or coating materials affect the electrical or thermal performance of the components? A: Potting and coating materials can potentially impact the electrical or thermal performance of components if not selected and applied properly. For example, some potting compounds may have high thermal resistance, hindering heat dissipation, while certain coating materials can affect electrical characteristics if applied too thickly. Careful material selection and application techniques are crucial to minimize any adverse effects.
Potting and coating are essential techniques for protecting electronic components and assemblies from environmental factors and ensuring reliable operation. While both methods serve a similar purpose, their distinct characteristics and advantages make them suitable for different applications and requirements. By understanding the differences between potting and coating, manufacturers can make informed decisions and select the most appropriate protection method based on their specific needs, ensuring the longevity and optimal performance of their electronic devices.
0 Comments