What is UV Soldermask and Why Use It?
UV soldermask, also known as solder resist or solder mask, is a thin lacquer-like layer of polymer that is applied to the copper traces of a printed circuit board (PCB). Its main purposes are to prevent solder bridges from forming between closely spaced solder pads, protect the copper traces from oxidation and corrosion, provide electrical insulation, and act as a barrier against contaminants like dust and chemicals.
Applying UV soldermask to your PCB offers several key benefits:
– Prevents solder bridges and short circuits
– Protects copper traces from the environment
– Insulates and prevents current leakage between conductors
– Makes the PCB easier to clean by creating a smooth surface
– Gives the PCB a professional, finished appearance, especially if using colored mask
– Allows for higher density designs by acting as a barrier between small traces and pads
Types of UV Soldermask
UV soldermasks come in three main varieties:
Type | Description |
---|---|
Liquid Photoimageable | Applied as a liquid and then exposed to UV light through a photomask to cure it. Allows for high resolution and fine pitch designs. |
Dry Film Photoimageable | Comes as a thin dry film that is vacuum laminated onto the PCB before being exposed with UV light through a photomask. Faster application than liquid. |
Liquid Non-Photoimageable | Applied as a liquid but does not require photomasking and UV curing. Simply screen printed and then oven cured. Lower resolution and best for simple PCB designs. |
For at-home PCB fabrication, liquid photoimageable soldermask is usually the best choice. It provides good resolution and can be applied with simple tools. The UV exposure can be done with a DIY exposure box.
Tools and Materials Needed
To apply UV soldermask to a PCB at home, you will need:
- Cleaned and etched PCB board
- Liquid photoimageable soldermask
- Foam brush or squeegee applicator
- Transparency film and printer
- UV exposure unit (can be homemade)
- Soldermask developer chemical
- Chemical safe gloves and goggles
- Well ventilated work area
Homemade UV Exposure Box
A UV exposure box is necessary to cure the photoimageable soldermask. A simple one can be made at home with the following components:
- UV fluorescent or LED black light bulbs
- Reflective interior (aluminum foil works)
- Timer switch
- Aavailable power supply
- Enclosure to contain the UV lights
The key is to have even illumination across the PCB surface at the appropriate wavelength (usually 365 – 410nm) and intensity to fully cure the resist. Exposure time will vary based on the type and thickness of the soldermask.
Step by Step Process
1. Prepare the PCB
The PCB should be completely fabricated with the copper traces etched and cleaned of any oxide layer. If any holes need to be protected from the soldermask (like vias or component pins), use a small dot of enamel paint to cover them temporarily.
2. Print the Photomask
The photomask is a negative image of where you want the soldermask to remain after developing. Use PCB design software to create the mask by selecting the copper areas and exporting them as a filled black image. Print this onto a transparency film using a laser printer or photoplotter. Make sure the printout is very opaque.
3. Apply the Soldermask
Working in a low UV environment, carefully apply a thin, even coat of the liquid photoimageable soldermask to the PCB using the foam brush or squeegee. A thickness of around 0.001″ or 1 mil is typical. Inspect it carefully to make sure there are no bubbles or missed areas. Allow it to settle flat for a few minutes.
4. Expose the Soldermask
Carefully place the photomask transparency onto the still wet soldermask layer, ink side down. Then put the PCB into the UV exposure unit and turn on the lights for the recommended time (usually a few minutes). This will harden the soldermask that is not covered by the dark areas of the photomask.
5. Develop the Soldermask
Put on the gloves and goggles. Immerse the PCB into the soldermask developer chemical and gently agitate until all the unexposed areas of soldermask have dissolved away. This usually takes a few minutes.
6. Final Curing
Rinse the PCB thoroughly with water and allow it to dry. Then place it back into the UV unit for a longer final curing exposure, around 10-15 minutes. This will make the remaining soldermask hard and durable. The mask may not reach its full color until after curing.
7. Finish Up
If any holes were covered in step 1, use a solvent to remove the enamel dots. The PCB is now ready for final assembly. If any touchup is needed, use soldermask repair pens to cover exposed areas.
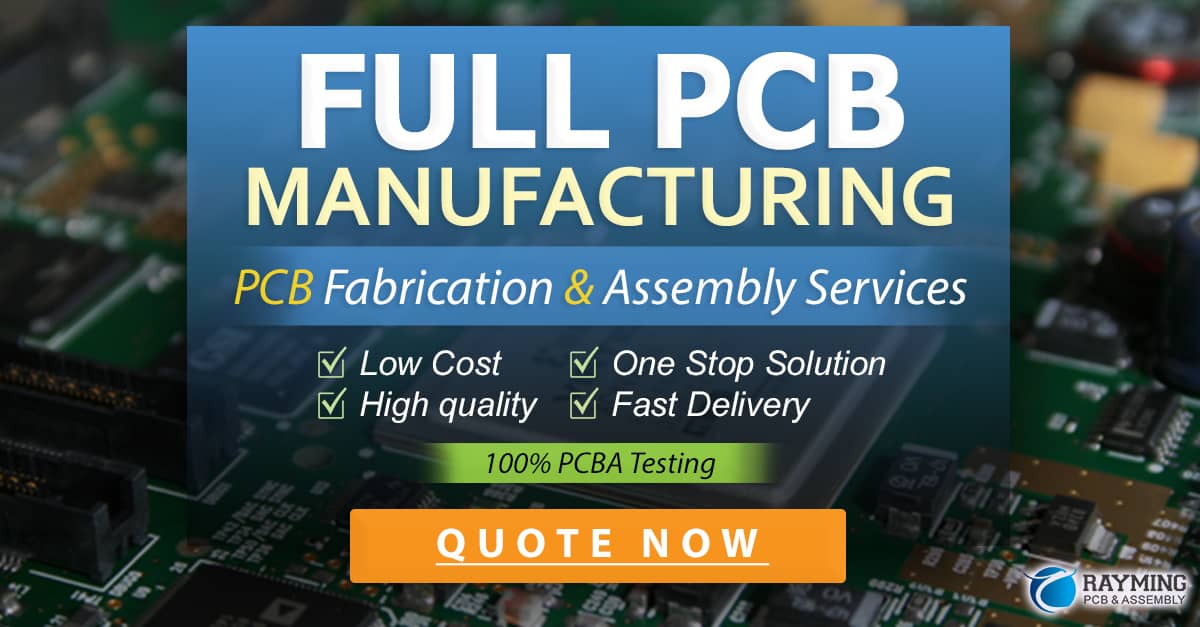
FAQ
What color options are available for UV soldermask?
UV soldermasks are commonly available in green, blue, red, yellow, black, white, and purple. Green is the most common color, followed by blue and red. Some vendors also offer clear masks for a more natural look.
How does UV soldermask compare to epoxy liquid or dry film masks?
UV curable masks offer some advantages over non-UV masks:
- Faster curing with no oven needed
- Higher resolution for finer pitched designs
- More professional appearance
- Better chemical and heat resistance
However, UV masks do require the extra equipment and steps for masking and exposing. Non-photoimageable masks may be preferable for very simple PCB designs.
Can UV soldermask be removed if needed?
Yes, cured UV soldermask can be chemically stripped using specialty removers based on methylene chloride or alkaline solutions. It can also be abraded off with scrubbing or sandblasting if the underlying copper is not critical. However, it is very durable once fully cured and can be difficult to remove, so make sure the PCB design is final before application.
How long does UV soldermask last?
When properly applied and cured, UV soldermask is very long lasting. It is chemically inert, waterproof, and resistant to corrosion and abrasion. A PCB protected by soldermask can easily last for many years, even decades, in normal environments. Only in harsh, corrosive conditions would the mask degrade prematurely.
Are there any safety concerns with UV soldermask?
The main safety concern is with the uncured material and developer chemicals, which can be skin and eye irritants. Always wear gloves and goggles when handling, work in a ventilated area, and avoid any skin contact. Once fully cured, however, the soldermask is considered to be non-toxic and safe to handle. As with any UV light source, avoid looking directly at bright UV exposure units.
In summary, applying UV soldermask is an excellent way to protect and enhance your homemade PCBs. With a bit of practice and the right tools, professional looking solder mask application is achievable in the home workshop. The key steps are creating the photomask, properly applying the liquid soldermask, exposing it under UV light with the mask, and then developing away the uncured areas. By following this guide and observing the proper safety precautions, you’ll be able to give your DIY PCBs a durable, great looking soldermask finish.
0 Comments