What is a soldermask and why is it important in PCB manufacturing?
A soldermask, also known as a solder resist or solder stop mask, is a thin layer of polymer applied to the copper traces of a printed circuit board (PCB). Its primary function is to prevent solder from bridging between conductors during the soldering process, which could lead to short circuits and other issues. The soldermask also protects the copper traces from oxidation and provides electrical insulation.
In addition to its functional benefits, the soldermask also serves an aesthetic purpose by giving the PCB its distinctive color. The most common soldermask colors are green and blue, but other colors like red, yellow, black, and white are also available.
The role of soldermask in PCB assembly
During the PCB assembly process, the soldermask plays a crucial role in ensuring the proper placement and adhesion of components. The soldermask is applied to the PCB after the copper traces have been etched but before the components are soldered onto the board. Openings in the soldermask, called solder pads or vias, expose the underlying copper and allow for the attachment of components.
The soldermask helps to define the boundaries of these solder pads, preventing solder from spreading beyond the intended area. This is particularly important for surface mount components, which have small, closely spaced leads that can easily short circuit if too much solder is applied.
The advantages of using a black soldermask
While green and blue are the most popular soldermask colors, black soldermasks have gained popularity in recent years due to their unique properties and advantages. One of the main reasons for choosing a black soldermask is its anti-reflective properties.
Reducing light reflection
In applications where light reflection from the PCB surface is undesirable, such as in optical devices or high-end audio equipment, a black soldermask can help minimize reflections. The matte finish of the black soldermask absorbs more light compared to glossy finishes, reducing glare and improving the overall performance of the device.
Some examples of applications where a black soldermask is preferred include:
- Camera modules and optical sensors
- Automotive displays and instrument clusters
- High-end audio equipment
- Medical devices and imaging systems
Enhanced aesthetics
In addition to its functional benefits, a black soldermask can also enhance the visual appeal of a PCB. The sleek, modern look of a black PCB can be particularly attractive for consumer electronics and other products where aesthetics are important.
Black soldermasks can also make it easier to read text and markings on the PCB surface, as the contrast between the white silkscreen and the black background is higher compared to other soldermask colors.
Improved heat dissipation
Another advantage of using a black soldermask is its ability to dissipate heat more effectively than lighter-colored soldermasks. The dark color of the black soldermask allows it to absorb more heat from the components on the PCB and radiate it away from the board.
This can be particularly beneficial in high-power applications or devices that generate significant amounts of heat, as it can help prevent components from overheating and extend the overall lifespan of the PCB.
The science behind anti-reflective coatings
To understand how black soldermasks reduce light reflection, it’s helpful to have a basic understanding of the science behind anti-reflective coatings.
The principles of light reflection and absorption
When light strikes a surface, some of the light is reflected while the rest is absorbed. The amount of light reflected depends on the material’s refractive index, which is a measure of how much the light’s speed changes as it passes through the material.
Materials with a high refractive index, such as metals, tend to reflect more light, while materials with a low refractive index, such as air, reflect less light. The greater the difference in refractive indices between two materials, the more light will be reflected at their interface.
Interference-based anti-reflective coatings
One way to reduce light reflection is by using interference-based anti-reflective coatings. These coatings consist of one or more thin layers of material with carefully chosen thicknesses and refractive indices.
The layers are designed so that the light reflected from the top of the coating is out of phase with the light reflected from the bottom of the coating. When these two reflected waves meet, they destructively interfere with each other, effectively canceling out the reflection.
Absorptive anti-reflective coatings
Another approach to reducing light reflection is by using absorptive anti-reflective coatings, which is the principle behind black soldermasks. These coatings are made from materials that absorb a significant portion of the incident light, minimizing the amount of light that is reflected.
Black soldermasks typically use carbon black pigments or other dark-colored pigments to achieve their light-absorbing properties. The pigment particles are dispersed throughout the soldermask material, creating a matte finish that scatters and absorbs light more effectively than a glossy surface.
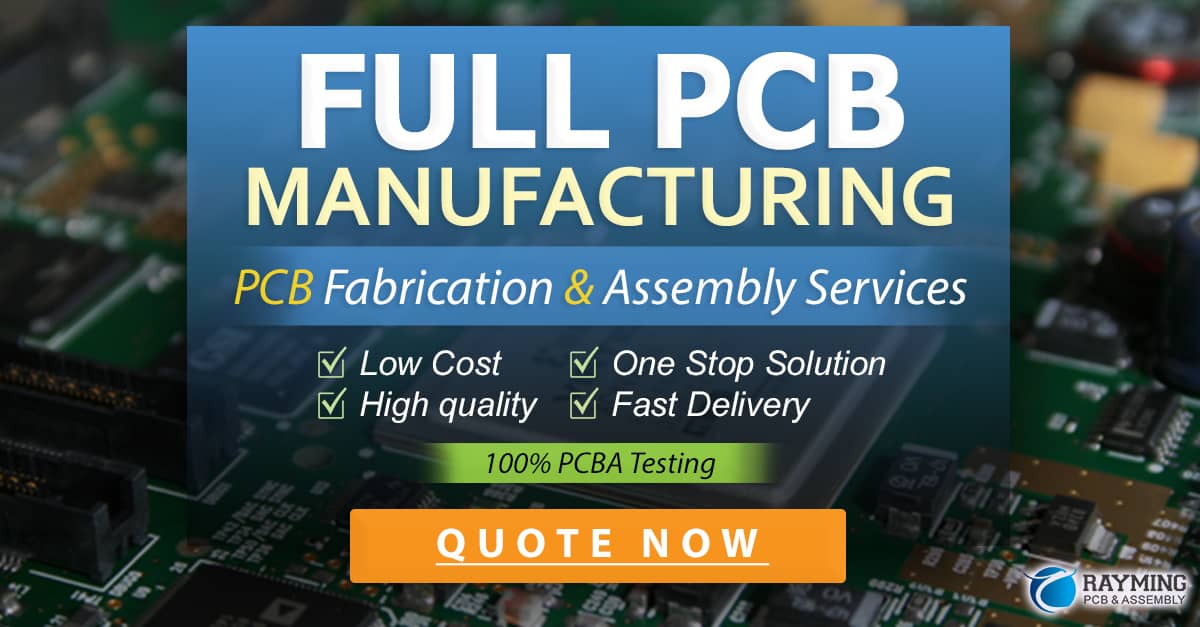
Choosing the right soldermask for your PCB
When selecting a soldermask for your PCB, there are several factors to consider, including the intended application, the desired aesthetic, and the manufacturing process.
Evaluating your application requirements
The first step in choosing a soldermask is to evaluate the specific requirements of your application. Consider questions such as:
- Is light reflection a concern for your device?
- Will the PCB be exposed to harsh environmental conditions?
- Are there any specific color or aesthetic requirements?
- What are the electrical and thermal demands of the application?
Answering these questions will help you narrow down your soldermask options and choose the one that best meets your needs.
Comparing soldermask materials and properties
There are several types of soldermask materials available, each with its own set of properties and advantages. Some common soldermask materials include:
- Liquid photoimageable (LPI) soldermasks
- Dry film soldermasks
- Epoxy liquid soldermasks
- Urethane liquid soldermasks
LPI soldermasks are the most widely used type and offer excellent resolution, adhesion, and durability. They are applied as a liquid and then exposed to UV light through a photomask to create the desired pattern.
Dry film soldermasks are applied as a solid film and are typically used for high-volume production due to their faster processing times. Epoxy and urethane liquid soldermasks offer improved chemical and thermal resistance compared to LPI soldermasks.
When comparing soldermask materials, consider factors such as:
- Adhesion to the PCB substrate
- Resistance to chemicals, solvents, and moisture
- Thermal and electrical properties
- Ease of processing and compatibility with your manufacturing equipment
Working with your PCB manufacturer
Once you’ve chosen a soldermask material and color, it’s essential to work closely with your PCB manufacturer to ensure that your design can be successfully fabricated. Your manufacturer can provide guidance on design rules, such as minimum soldermask clearances and webbing, to help you optimize your PCB layout for manufacturability.
Be sure to communicate your soldermask requirements clearly and provide your manufacturer with any necessary documentation, such as Gerber files and assembly drawings. Working collaboratively with your manufacturer can help you achieve the best possible results for your PCB project.
FAQ
-
Q: Can black soldermasks be used for all types of PCBs?
A: Black soldermasks can be used for most types of PCBs, but they may not be suitable for every application. It’s essential to evaluate your specific requirements and consult with your PCB manufacturer to determine if a black soldermask is the best choice for your project. -
Q: Are black soldermasks more expensive than other colors?
A: In general, black soldermasks are slightly more expensive than standard green or blue soldermasks due to the additional pigments and processing required. However, the cost difference is usually minimal and may be offset by the performance and aesthetic benefits of using a black soldermask. -
Q: How does the durability of black soldermasks compare to other colors?
A: The durability of a soldermask depends more on the material and processing than the color itself. High-quality black soldermasks can offer the same level of durability and protection as other colors, provided they are applied and cured correctly. -
Q: Can black soldermasks be combined with other colors or finishes?
A: Yes, black soldermasks can be used in combination with other colors or finishes, such as white silkscreen or selective gold plating, to create unique and eye-catching PCB designs. However, it’s important to ensure that the different materials and processes are compatible and will not adversely affect the performance or reliability of the PCB. -
Q: Are there any special considerations when designing a PCB with a black soldermask?
A: When designing a PCB with a black soldermask, it’s important to pay attention to the contrast between the soldermask and any text or markings on the board. White silkscreen is typically used for maximum visibility against a black background. Additionally, ensure that your design adheres to your manufacturer’s guidelines for soldermask clearances and other design rules to avoid any issues during fabrication.
Soldermask Color | Reflectivity | Heat Dissipation | Aesthetics |
---|---|---|---|
Black | Low | High | Sleek, modern look |
Green | Medium | Medium | Traditional, widely used |
Blue | Medium | Medium | Popular, vibrant |
Red | High | Low | Eye-catching, specialty applications |
Yellow | High | Low | Attention-grabbing, safety applications |
White | Very High | Low | Clean, minimalist look |
In conclusion, black soldermasks offer unique advantages in applications where light reflection is not wanted, such as in optical devices and high-end audio equipment. The anti-reflective properties of black soldermasks are achieved through absorptive coatings that minimize the amount of light reflected from the PCB surface.
In addition to their functional benefits, black soldermasks can also enhance the visual appeal of a PCB and improve heat dissipation, making them an attractive choice for a wide range of applications.
When selecting a soldermask for your PCB, it’s essential to evaluate your specific requirements and work closely with your PCB manufacturer to ensure that your design can be successfully fabricated. By understanding the science behind anti-reflective coatings and the properties of different soldermask materials, you can make an informed decision and achieve the best possible results for your PCB project.
0 Comments