What is Solder Paste?
Solder paste is a key material used in surface mount technology (SMT) for assembling electronic components onto printed circuit boards (PCBs). It is a homogeneous mixture of tiny solder particles suspended in a flux medium. The solder particles are typically made of a tin-lead (SnPb) alloy or lead-free alloys such as tin-silver-copper (SAC).
Composition of Solder Paste
Solder paste consists of two main components:
- Solder alloy particles (90% by weight)
- Flux medium (10% by weight)
The solder alloy particles provide the necessary metallic content for forming reliable electrical and mechanical connections between components and the PCB. The flux medium serves multiple purposes, including:
- Protecting the solder particles from oxidation
- Improving the wetting and spreading of the molten solder during reflow
- Removing oxides and contaminants from the surfaces to be soldered
- Providing a suitable rheology for printing and placement of components
Types of Solder Paste
Solder pastes can be classified based on various factors, such as alloy composition, particle size, and flux type.
Alloy Composition
- Tin-Lead (SnPb): Traditionally used, but being phased out due to environmental and health concerns
- Lead-Free: Common alloys include SAC (Tin-Silver-Copper), SnAg (Tin-Silver), and SnCu (Tin-Copper)
Particle Size
Solder paste particle size is typically classified by mesh size, which refers to the number of openings per linear inch in the screen used to sieve the particles. Common particle sizes include:
Mesh Size | Particle Size Range (µm) |
---|---|
Type 3 | 25-45 |
Type 4 | 20-38 |
Type 5 | 15-25 |
Type 6 | 5-15 |
Smaller particle sizes are used for fine-pitch components and high-density assemblies.
Flux Type
Solder paste flux can be categorized by its activity level and residue characteristics:
- Rosin (R): Mildly activated, non-corrosive, non-conductive residues
- Resin (RMA): Rosin-based, higher activity, non-corrosive, non-conductive residues
- No-Clean (NC): Low residue, designed to be left on the board after soldering
- Water-Soluble (WS): Highly activated, corrosive, conductive residues, requires cleaning
Solder Paste Properties
To ensure optimal performance in the SMT process, solder paste must possess several key properties:
Printability
Solder paste should have a consistent viscosity and rheology that allows for accurate and repeatable deposition through stencil openings onto the PCB pads. Factors affecting printability include:
- Particle size distribution
- Flux formulation
- Printing parameters (speed, pressure, separation distance)
Tackiness
Tackiness refers to the ability of the solder paste to hold components in place after placement and before reflow. Adequate tackiness prevents component movement during handling and ensures accurate alignment.
Slump Resistance
Slump is the tendency of solder paste to spread or flow beyond the intended area after printing. Slump resistance is essential for maintaining the integrity of the printed deposit and preventing bridging between adjacent pads.
Wetting and Spreading
During reflow, the molten solder should readily wet and spread on the PCB pads and component terminations to form a strong metallurgical bond. The flux medium plays a critical role in promoting wetting by removing oxides and contaminants from the surfaces.
Shelf Life and Storage
Solder paste has a limited shelf life, typically ranging from 3 to 6 months when stored at refrigerated temperatures (2-10°C). Proper storage and handling are crucial for maintaining the paste’s performance characteristics.
Solder Paste Application Process
The SMT assembly process involves several steps in which solder paste is applied and processed:
-
Stencil Printing: Solder paste is deposited onto the PCB pads through a stencil using a squeegee blade. The stencil thickness and aperture dimensions determine the volume and geometry of the printed solder paste.
-
Component Placement: Surface mount components are placed onto the printed solder paste deposits using automated pick-and-place machines or manual methods.
-
Reflow Soldering: The assembled PCB is subjected to a controlled heating process in a reflow oven. The solder paste melts, wets the surfaces, and forms a metallurgical bond between the components and PCB pads upon cooling.
-
Inspection and Rework: After reflow, the soldered assembly is inspected for defects such as bridging, insufficient solder, or misaligned components. Any defects are reworked using appropriate techniques.
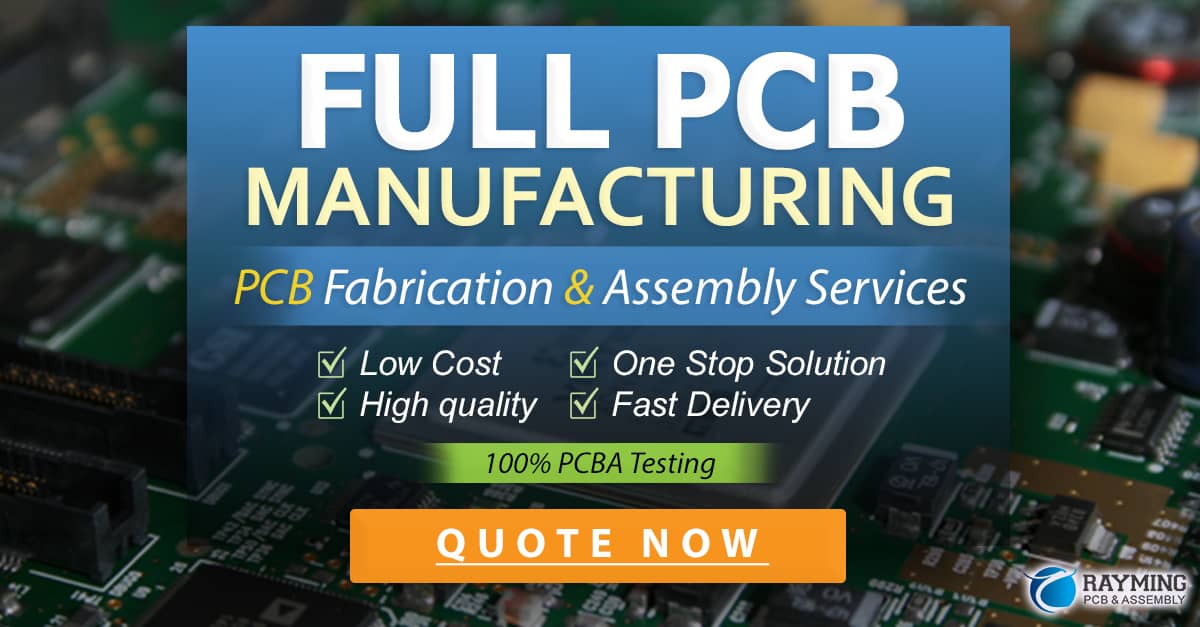
Solder Paste Defects and Troubleshooting
Several defects can occur during the solder paste application and reflow process, leading to assembly quality issues. Common defects include:
- Insufficient Solder: Inadequate solder volume, resulting in weak or open connections
- Solder Bridging: Excess solder causing short circuits between adjacent pads or pins
- Solder Balls: Tiny spheres of solder that can cause short circuits or reliability issues
- Poor Wetting: Incomplete solder coverage or dewetting, leading to weak or unreliable connections
- Component Misalignment: Shifting or rotation of components during placement or reflow
Troubleshooting solder paste defects involves identifying the root cause and implementing appropriate corrective actions, such as:
- Adjusting stencil design or printing parameters
- Optimizing reflow profile and temperature settings
- Improving component placement accuracy and machine maintenance
- Selecting suitable solder paste formulations and storage conditions
Frequently Asked Questions (FAQ)
- What is the difference between solder paste and solder wire?
-
Solder paste is a mixture of solder particles suspended in a flux medium, used for SMT assembly. Solder wire is a solid wire of solder alloy, typically used for hand soldering or through-hole assembly.
-
Can solder paste be reused after printing?
-
It is generally not recommended to reuse solder paste after printing, as it may have been exposed to air and contaminants, leading to changes in its rheology and performance.
-
How should solder paste be stored?
-
Solder paste should be stored at refrigerated temperatures (2-10°C) in airtight containers to prevent moisture absorption and oxidation. Before use, the paste should be allowed to reach room temperature and mixed thoroughly.
-
What factors influence the selection of solder paste for a specific application?
-
Factors to consider when selecting solder paste include the alloy composition, particle size, flux type, printing requirements, component pitch, reflow profile, and environmental considerations.
-
How can solder paste performance be optimized?
- Solder paste performance can be optimized by proper storage and handling, regular stencil cleaning, optimizing printing parameters, maintaining consistent reflow profiles, and implementing a robust process control and quality assurance system.
Conclusion
Solder paste is a critical material in SMT assembly, enabling the reliable and efficient connection of surface mount components to PCBs. Understanding the composition, properties, and application process of solder paste is essential for achieving high-quality and defect-free assemblies.
By selecting the appropriate solder paste formulation, optimizing the printing and reflow parameters, and implementing effective process controls, manufacturers can ensure the consistent production of reliable electronic assemblies.
As technology advances and miniaturization continues, the development of advanced solder paste materials and processes will remain a key focus in the SMT industry to meet the evolving demands of electronic packaging.
0 Comments