Introduction to Programmable IC Marking
Programmable Integrated Circuits (ICs) are essential components in modern electronics, offering flexibility and customization for various applications. To ensure proper identification and traceability, these ICs require clear and standardized marking procedures. This article delves into the process of defining programmable IC marking, covering essential aspects such as marking methods, information to be included, and industry standards.
What is Programmable IC Marking?
Programmable IC marking refers to the process of applying identifiable information onto the surface of a programmable integrated circuit. This marking serves multiple purposes, including:
- Identification of the IC manufacturer and part number
- Indication of the IC’s programming status
- Traceability for quality control and inventory management
- Compliance with industry standards and regulations
Importance of Proper IC Marking
Proper marking of programmable ICs is crucial for several reasons:
-
Quality Assurance: Clear and accurate marking allows for easy identification of ICs during the manufacturing process, ensuring the correct components are used in the intended applications.
-
Traceability: In case of any issues or failures, marked ICs can be traced back to their manufacturing batch, enabling efficient problem-solving and root cause analysis.
-
Counterfeit Prevention: Standardized marking helps combat counterfeit ICs by providing a means to authenticate genuine components.
-
Regulatory Compliance: Many industries have specific marking requirements to ensure compliance with safety and quality standards.
Marking Methods for Programmable ICs
Several methods are commonly used for marking programmable ICs, each with its own advantages and considerations.
Laser Marking
Laser marking is a precise and permanent method that uses a focused laser beam to create marks on the IC surface. It offers several benefits:
- High precision and clarity
- Durability and resistance to wear and environmental factors
- Non-contact process, minimizing the risk of damage to the IC
- Flexibility in terms of mark size, location, and content
However, laser marking requires specialized equipment and may have higher initial costs compared to other methods.
Ink Marking
Ink marking involves applying ink directly onto the IC surface using techniques such as pad printing or inkjet printing. This method is known for:
- Lower equipment costs compared to laser marking
- Ability to mark on various surfaces and materials
- Faster marking process for high-volume production
Considerations for ink marking include ensuring the compatibility of the ink with the IC surface and the potential for smudging or fading over time.
Label Marking
Label marking involves attaching a pre-printed label or sticker onto the IC package. While this method is simple and cost-effective, it has some limitations:
- Potential for labels to peel off or become damaged
- Limited space for detailed information
- May not be suitable for high-temperature or harsh environments
Label marking is often used for temporary identification or in conjunction with other marking methods.
Information to be Included in IC Marking
The information included in programmable IC marking varies depending on the specific application, industry standards, and manufacturer preferences. However, some common elements are:
-
Manufacturer Logo or Name: Identifies the company that produced the IC.
-
Part Number: Unique identifier for the specific IC model or family.
-
Date Code: Indicates the manufacturing date, usually in a coded format (e.g., YYWW for year and week).
-
Lot Code: Identifies the manufacturing batch or lot for traceability purposes.
-
Programming Status: Indicates whether the IC has been programmed or is blank.
-
Pin 1 Indicator: Helps orient the IC correctly during assembly.
-
**Revision or Version
Number**: Specifies the version or revision of the IC design.
-
Country of Origin: May be required for compliance with trade regulations.
-
Certification Marks: Indicates compliance with industry standards or certifications (e.g., RoHS, UL).
The specific content and format of the marking may vary based on the available space on the IC package and the requirements of the end application.
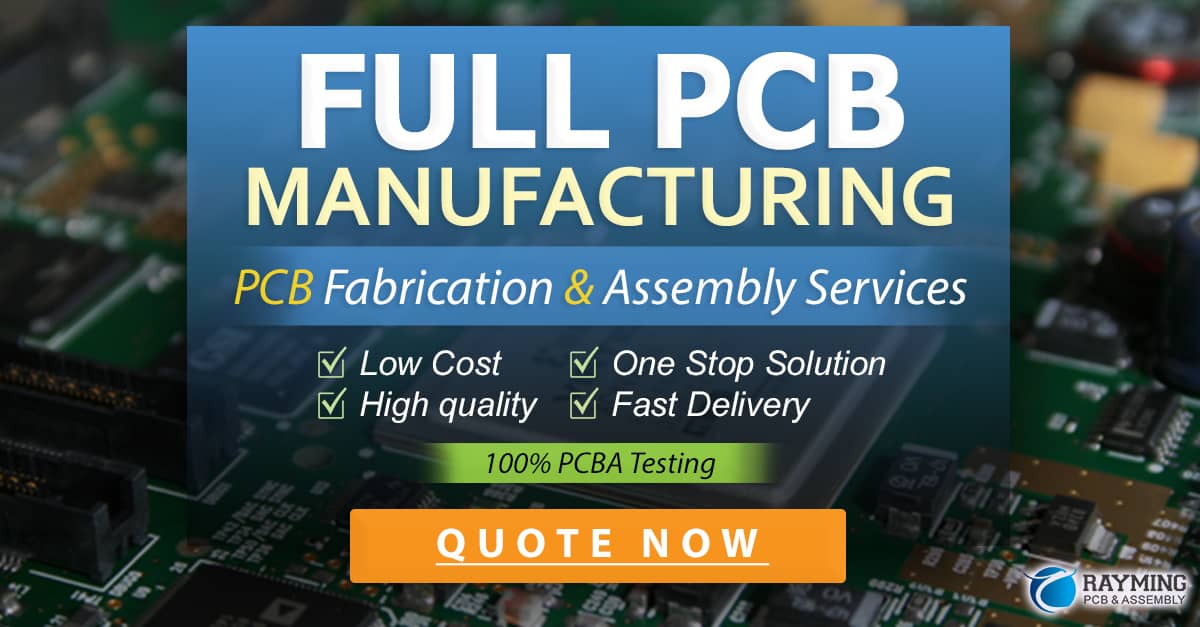
Industry Standards for IC Marking
Several industry standards provide guidelines and requirements for programmable IC marking to ensure consistency and reliability across manufacturers and applications.
JEDEC Standards
The Joint Electron Device Engineering Council (JEDEC) is a global standardization body for the microelectronics industry. JEDEC has established several standards related to IC marking, including:
- JESD30: Descriptive Designation System for Semiconductor-Device Packages
- JESD609: Marking, Symbols, and Labels for Identification of Lead (Pb) Free Assemblies, Components, and Devices
These standards provide a framework for consistent marking practices and help ensure interoperability between different manufacturers.
IPC Standards
IPC, formerly known as the Institute for Printed Circuits, is a global trade association that develops standards for the electronic interconnection industry. Relevant IPC standards for IC marking include:
- IPC-7710: Marking, Symbols, and Labels for Identification of Lead-Free and Other Reportable Materials in Lead-Free Assemblies, Components, and Devices
- IPC-SM-782: Surface Mount Design and Land Pattern Standard
These standards offer guidance on marking requirements for lead-free components and provide recommendations for land patterns and packaging dimensions.
Military and Aerospace Standards
For applications in military and aerospace industries, additional marking standards may apply to ensure the reliability and traceability of programmable ICs. Examples include:
- MIL-STD-130: Department of Defense Standard Practice for Identification Marking of U.S. Military Property
- SAE AS5553: Counterfeit Electronic Parts; Avoidance, Detection, Mitigation, and Disposition
These standards impose stricter requirements for marking, documentation, and traceability to mitigate the risks associated with counterfeit parts in critical systems.
Marking Procedures and Best Practices
To ensure consistent and reliable marking of programmable ICs, manufacturers should establish well-defined procedures and adhere to best practices.
Develop a Marking Specification
Create a detailed marking specification that outlines the required information, format, and location of the marks on the IC package. This specification should consider:
- Readability and legibility of the marks
- Compatibility with the IC package material and surface finish
- Compliance with relevant industry standards and customer requirements
The marking specification should be communicated to all relevant stakeholders, including design, manufacturing, and quality control teams.
Implement Quality Control Measures
Establish quality control measures to ensure the accuracy and consistency of IC marking. This may include:
- Regular calibration and maintenance of marking equipment
- Visual inspection of marked ICs using magnification or automated vision systems
- Verification of marking content against the marking specification and customer requirements
- Traceability of marked ICs throughout the manufacturing process
Implement statistical process control methods to monitor the marking process and identify any deviations or abnormalities.
Train Personnel
Provide adequate training to personnel involved in the IC marking process. This training should cover:
- Operation and maintenance of marking equipment
- Understanding of the marking specification and industry standards
- Quality control procedures and inspection criteria
- Handling and storage of marked ICs
Regular refresher training and updates should be conducted to ensure personnel remain proficient and aware of any changes in marking requirements.
Continuous Improvement
Continuously monitor and improve the IC marking process based on feedback from customers, internal quality metrics, and industry developments. This may involve:
- Regularly reviewing and updating the marking specification
- Investigating and addressing any marking-related issues or customer complaints
- Adopting new marking technologies or methods as they become available
- Participating in industry forums and standardization efforts to stay informed of best practices and emerging trends
By fostering a culture of continuous improvement, manufacturers can ensure their IC marking procedures remain effective and aligned with evolving industry requirements.
Frequently Asked Questions (FAQ)
-
What is the purpose of marking programmable ICs?
Marking programmable ICs serves multiple purposes, including identification of the manufacturer and part number, indication of programming status, traceability for quality control and inventory management, and compliance with industry standards and regulations. -
What are the most common methods for marking programmable ICs?
The most common methods for marking programmable ICs are laser marking, ink marking, and label marking. Laser marking offers high precision and durability, while ink marking is cost-effective for high-volume production. Label marking is simple but may have limitations in harsh environments. -
What information is typically included in programmable IC marking?
Programmable IC marking typically includes the manufacturer logo or name, part number, date code, lot code, programming status, pin 1 indicator, revision or version number, country of origin, and any relevant certification marks. -
Are there industry standards that govern programmable IC marking?
Yes, several industry standards provide guidelines and requirements for programmable IC marking, including JEDEC standards (e.g., JESD30, JESD609), IPC standards (e.g., IPC-7710, IPC-SM-782), and military and aerospace standards (e.g., MIL-STD-130, SAE AS5553). -
How can manufacturers ensure the quality and consistency of programmable IC marking?
Manufacturers can ensure the quality and consistency of programmable IC marking by developing a detailed marking specification, implementing quality control measures, providing adequate training to personnel, and continuously monitoring and improving the marking process based on feedback and industry developments.
Conclusion
Programmable IC marking is a critical aspect of the electronics manufacturing process, ensuring proper identification, traceability, and compliance with industry standards. By understanding the various marking methods, required information, and relevant industry standards, manufacturers can establish robust marking procedures that meet the needs of their customers and end applications.
Implementing best practices such as developing a comprehensive marking specification, implementing quality control measures, training personnel, and continuously improving the process, manufacturers can ensure the consistency, reliability, and effectiveness of their programmable IC marking.
As the electronics industry continues to evolve, staying informed of the latest marking technologies, standards, and requirements will be essential for manufacturers to remain competitive and meet the ever-increasing demands for quality and reliability in programmable ICs.
0 Comments