What are Gerber Files and Why Panelize Them?
Gerber files are the standard file format used to describe the printed circuit board (PCB) layers and drilling information needed for manufacturing. A separate Gerber file is generated for each layer of the PCB, including the copper traces, solder mask, silkscreen, and drill holes.
Panelizing Gerber files refers to the process of arranging multiple copies of a PCB design into an array or “panel” for more efficient mass production. The main reasons to Panelize gerber files before manufacturing include:
- Reducing production costs by fabricating multiple PCBs per panel
- Enabling the use of automated assembly equipment that requires panels
- Providing tabs to hold the individual boards in place during the depaneling process
Key Considerations Before Panelizing
There are several important factors to consider prior to panelizing your Gerber files:
Board Spacing and Depaneling Method
Adequate spacing must be left between the individual boards on the panel to account for the depaneling process, where the final boards are singulated from the larger panel. Common depaneling methods and their associated minimum board spacing include:
Depaneling Method | Min. Board Spacing |
---|---|
V-Scoring | 0.6 mm – 0.8 mm |
Tab Routing | 1.5 mm – 2.0 mm |
Routing | 2.0 mm – 2.5 mm |
Punching | 3.0 mm – 4.0 mm |
Panelization Borders and Tooling
Additional space is needed around the perimeter of the panel for tooling features used in the fabrication and assembly processes. A typical panel border dimension is 5-10 mm.
Fiducial marks, pin holes, and tooling strips may also need to be added for automated assembly equipment to accurately place and process the panel. Check with your PCB manufacturer and assembly partner for their specific requirements.
Panel Size and Aspect Ratio
The overall panel size and aspect ratio (length to width) should be considered to optimize material usage and comply with any manufacturing constraints. Standard panel sizes offered by PCB fabricators usually include:
- 18″ x 24″ (457 mm x 610 mm)
- 21″ x 24″ (533 mm x 610 mm)
- 16″ x 18″ (406 mm x 457 mm)
- 12″ x 18″ (305 mm x 457 mm)
Rectangular panels with an aspect ratio of 1:1 to 2:1 are most common. Avoid extreme aspect ratios greater than 4:1.
Panelization Methods and Tools
There are several methods and software tools available for panelizing Gerber files:
PCB Design Software
Most PCB design software packages have built-in functionality for panelizing. This is often the easiest method if you have access to the original PCB design files.
To panelize in PCB design software:
- Open the PCB layout file
- Create a new document with the desired panel size
- Import multiple copies of the PCB into the panel document
- Arrange the boards in a grid, leaving appropriate spacing
- Add tooling features like borders, fiducials, etc.
- Export Gerber files for the completed panel
Popular PCB design software with panelization capabilities include:
- Altium Designer
- Autodesk Eagle
- KiCad
- Cadence Allegro
- Mentor Graphics PADS
Gerber Editing Software
Dedicated Gerber file editing software allows you to import and panelize existing Gerber files without needing the original PCB design files. These programs offer powerful features for viewing, modifying, and arranging Gerber data.
Steps to panelize in Gerber editing software:
- Import the individual board Gerber files
- Create a new panel document and set the desired panel size
- Place multiple copies of the imported board files into the panel
- Arrange and space the boards appropriately
- Add any necessary panel tooling features
- Export the final panelized Gerber files
Some popular Gerber editing software includes:
- GerbView (free viewer included with KiCad)
- GC-Prevue
- CAM350
- ViewMate
Panelization Services
If you don’t have access to panelization software or want to avoid the complexity, many PCB manufacturers and service bureaus offer panelization as a paid service.
You simply provide them your individual board Gerber files and inform them of any special panelization requirements. They will then panelize the files for you and return the panel Gerber files ready for fabrication.
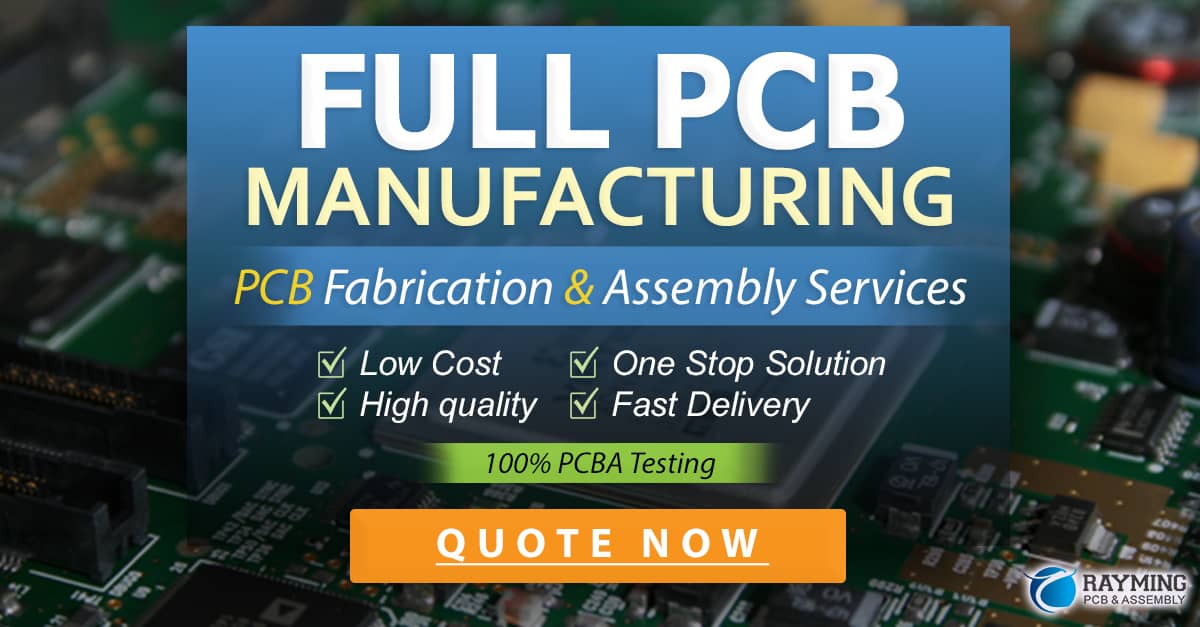
Step-by-Step Panelization Process
Here is a detailed step-by-step guide to panelizing Gerber files using PCB design software:
-
Open your PCB design software and load the original PCB layout file that you want to panelize.
-
Create a new PCB document. Set the board dimensions to your desired panel size. A common panel size is 16″ x 18″ (406 x 457 mm).
-
Import your original PCB layout into the new panel document. Most software will have an “Import” or “Place” command to bring in an existing PCB file.
-
Arrange multiple copies of the imported PCB into a grid pattern on the panel. Leave adequate spacing between the boards based on your planned depaneling method (see table above).
- For V-score depaneling, space boards at least 0.7 mm apart
- For tab routing, 1.8 mm spacing is typical
- Routed boards need a minimum of 2.2 mm spacing
- Punched boards require 3-4 mm spacing
-
Add a panel border around the perimeter of the arranged PCB array. A typical border width is 7-10 mm. Use the software’s line or rectangle drawing tools.
-
Include any necessary tooling features on the panel:
- Place fiducial marks in the corners and center of the panel border for automated assembly
- Add tooling strips for panel handling if required
- Include an identification label with the part number, revision, etc.
-
Double check the spacing, arrangement, and tooling features on your completed panel. Ensure there are no overlapping or off-grid elements.
-
Export a new set of Gerber files for your completed PCB panel. Be sure to export all layers, including the top and bottom copper, solder mask, silk screen, and drill files.
-
Perform a final check of your exported panel Gerber files using a Gerber viewer. Verify that all layers align correctly and no errors are present.
-
Send your final panelized Gerber files to your PCB manufacturer for fabrication.
Tips for Successful Panelization
-
Always verify that your panel fits within your manufacturer’s standard or maximum allowed panel sizes. Larger panels may incur higher costs.
-
If using an irregular panel size, confirm it is acceptable with your manufacturer before proceeding.
-
Clearly communicate your depaneling method to the fabricator to ensure they leave adequate spacing between boards.
-
Consider the grain direction of the panel material when laying out your boards. Aligning the board lengthwise with the grain can make depaneling easier.
-
If feasible, use the same board orientation for all boards on the panel to simplify assembly.
-
Include a 1-2 mm “squeeze” around the perimeter of routed or punched designs to account for cutting tolerances.
-
For designs sensitive to EMI, maximize the board-to-board spacing to reduce crosstalk.
-
On mixed-technology panels (SMT and through-hole), place SMT boards together and through-hole boards together to optimize assembly.
-
If using V-score or punch depaneling, avoid placing components or traces under the depaneling paths.
-
When in doubt, consult with your manufacturer early in the design process to avoid problems later.
Panelization FAQs
Q1: What is the minimum spacing between boards on a panel?
A1: The minimum board-to-board spacing depends on the depaneling method:
– V-Scoring: 0.6 – 0.8 mm
– Tab Routing: 1.5 – 2.0 mm
– Routing: 2.0 – 2.5 mm
– Punching: 3.0 – 4.0 mm
Q2: How big should I make the border around my panel?
A2: A border of 5-10 mm around the perimeter of the panel is typical. This leaves room for tooling features, labels, and handling during manufacturing.
Q3: What are fiducial marks and why are they needed?
A3: Fiducial marks are small circular pads added to the panel that serve as reference points for automated assembly equipment. They allow the machinery to accurately locate and place components on the boards. Usually 3 fiducials are placed in a non-linear pattern on the panel.
Q4: Can I panelize boards of different designs together?
A4: Yes, boards of different shapes and designs can be combined onto one panel as long as they use the same fabrication process and materials. This is often done to make the best use of the available panel area. However, it can complicate the assembly process since the different designs may require separate component setups.
Q5: Do I need to panelize my design if I’m only making a few prototype boards?
A5: For small prototype runs, panelization is usually not necessary. You can have your PCB manufacturer fabricate the individual boards as-is. Panelization is more important for volume production where the efficiency advantages outweigh the added effort.
By following this panelization guide and tips, you’ll be well prepared to create efficient panels of your PCB designs that are optimized for manufacturing. Good luck with your projects!
0 Comments